ARGOLF uses NX & Teamcenter Manufacturing to digitalize production processes
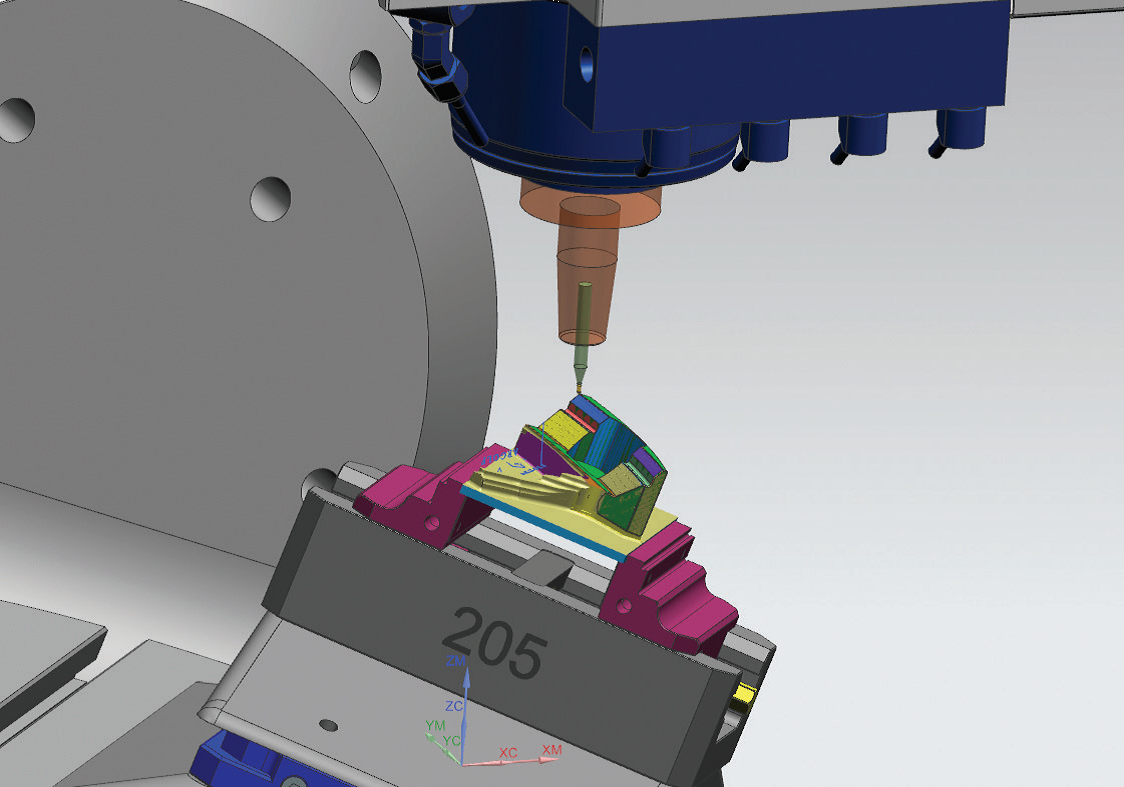
Siemens’ solutions enable ARGOLF to reduce reprogramming time for design modifications
Delivering French-made putters
ARGOLF was founded in 2010 following a meeting between two aeronautical industrialists, brothers Olivier and Sébastien Colas, both executives with Armor Meca (a company that offers high-precision machining services and manufactures machinery components for aeronautics, defense, food and medical industry), and golf professional Emmanuel Carlier.
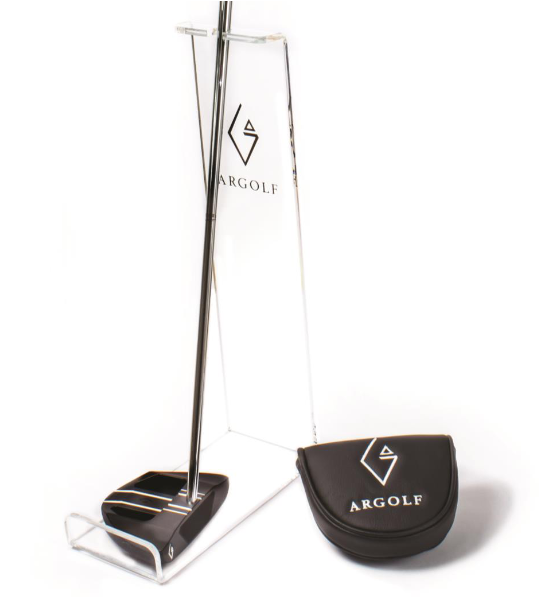
ARGOLF is the name behind an all-new range of golf putters that combine finesse, technological precision, balance and performance. Representing a high-tech approach to developing golf clubs, ARGOLF putters meet the requirements of every type of player, from beginners and confirmed amateurs to professionals. The putters’ aesthetics and ergonomics are suitable for all golfers, providing maximum comfort and efficacy on the greens.
Right from the outset, the company opted for the Made in France tag; its putters are designed and produced on the Armor Meca production site in Brittany’s Côtes d’Armor department. In fact, the names given to the various putters pay tribute to the region’s strong sense of identity with, and its ties to, the legend of King Arthur: Morgane, Uther, Pendragon, Graal for mallet putters, and Lancelot, Arthur and Merlin for blade putters.
Applying aeronautical know-how
“As golf enthusiasts, we originally sought to create two putters to cater to our own personal needs,” explains Olivier Colas, the director of ARGOLF. “We benefited from long-standing expertise in the machining of aeronautical components, modern production techniques and a research department that used Siemens’ integrated, high-performance CAD and CAM software solutions. “We thus designed and manufactured these first putters by drawing on our working methods and tools, both in terms of design and production. It proved to be an immediate success. That’s how the idea of creating our own brand came about, one that would combine design and high technology with an ongoing concern for precision and quality.”
To set itself apart from its competitors in a sector that is already largely populated by the major brands, the company opted for a strong differentiation strategy by leveraging its expertise in the machining of complex aeronautical parts. It also differentiated itself by using materials and processes such as titanium, integral machining and anodic oxidation in sulfuric acid, a technique used in the aerospace industry, to diffuse the reflection of light that would otherwise disturb the golfer about to putt. These innovations are backed up by ARGOLF patents, such as for its C-claws grooves, which offer players great precision and stability when putting.
“Basically, we drew on our aeronautical know-how for the benefit of golf,” says Olivier Colas.
The upshot is a range of putters combining performance, precision and visual aesthetics that have already won over plenty of professional golfers from around the world.
Using NX and Teamcenter to develop putters
To design and manufacture its putters, ARGOLF turned to its research and development (R&D) department, which uses an integrated NX software solution from product lifecycle management (PLM) specialist Siemens PLM Software that includes NX CAD for design, NX CAM software for manufacturing, and Teamcenter software for managing manufacturing data.
From draft sketch to production
The overall process is as follows:
The design office uses hand-drawn sketches drawn by Olivier Colas to create 3D models in NX. The teams involved collaborate to optimize the design while observing the technical specifications imposed by the regulatory authorities, the United States Golf Association (USGA) and the Royal and Ancient Golf Club of St Andrews (R&A) in St Andrews, Fife, Scotland.
Once the final design has been resolved, the computer-aided design (CAD) models are prepared for machining using NX CAM software. Four or five prototypes are then produced in a series of two. These prototypes are passed on to golfers so that they can assess their feel and performance. Based on their feedback, the design office carries out adjustments to finalize the end product.
The final model is then submitted to the federation for approval. Only then can the putters be mass produced on the Armor Meca production site’s dedicated machining centers. They are controlled using a 3D measuring machine calibrated to the nearest micron.
Innovating while adhering to strict regulations
Putting is the most precise part of the game of golf. The putter’s design must bring the golfer all the requisite technical benefits: clean strike, smooth glide, even impact and a ball propelled without any bounce.
All things considered, the putter head’s design is a complex affair: it requires innovation, while adhering to strict design rules. For example, the distance from heel to toe must be less than or equal to 7 inches or 177.8 millimeters (mm). The distance from the sole to the uppermost portion of the club head, including authorized details, must be less than or equal to 2.5 inches (63.5 mm), etc. All these guidelines are applied and integrated in the 3D design process as parametric rules.
Furthermore, ARGOLF has developed a patented groove system, dubbed C-claws, which improves top spin; for example, the ball’s capacity to spin forwards and go further once struck. This system also underwent 3D CAD studies in NX.
“NX offers a comprehensive modeling system, making it possible to interchangeably use more productive modeling methods, from solids and surfaces to parametric modeling,” says Cédric Gautier, head of R&D. “NX also includes advanced features for creating, handling and analyzing complex shapes that can be quickly and easily modified.”
Machining to the nearest micron
As with aeronautical parts, putters are machined using the company’s ultra-modern machining centers controlled by the NX software: Mallet putters are machined in two 5-axis operations and blade putters are machined in three 4-axis operations with a 5-axis finishing. The multi-axis machining helps the company reduce the number of setups and improve accuracy. All machining operations are based on the International Organization of Standardization (ISO) code generated by NX to the nearest micron.
We particularly appreciate the highly visual machining simulation features in NX that are a great help in our daily work. NX CAM software offers an integrated postprocessing system that directly generates the machine’s ISO code without having to use a third-party postprocessor; this is an important advantage.
Cédric Gautier, head of R&D, ARGOLF
Janus Engineering, Siemens’ partner and leading reseller of NX CAD/CAM solutions in France, provided support by choosing, installing and deploying Siemens PLM Software.
“NX CAD is an integrated design solution that helps to rationalize and speed up the process for developing innovative products,” says Nicolas Simon, director of Janus Engineering. “NX CAM offers tools for machine tool programming, postprocessing and machining simulation, which serves to reduce the NC programming and machining times, produce top-quality parts, and optimize the use of manufacturing resources.”
Leveraging agility
ARGOLF has successfully digitalized its design and manufacturing processes in order to be agile: “Herein lies the key to our success,” points out Olivier Colas. “By opting for Siemens’ integrated solutions, we now benefit from very fast design modifications and machine cycles. Reprogramming times are reduced whenever we modify the design.”
Moreover, since the company manufactures its putters in France on automated, robotized production lines, it can adjust its production runs in line with demand.
Exploring the international markets
ARGOLF is now established in the United States, South Korea, Japan and Australia. It intends to further develop the Asian and the American markets, and is looking to set up a distribution network in Europe. By building on its aeronautical expertise, the company’s objective is to become one of the market’s major players in the coming three-to-four years. This market is estimated to represent approximately 100 million amateur and professional golfers worldwide.
Thanks to Siemens’ software, ARGOLF has successfully digitalized its design and manufacturing processes. With the support of Janus Engineering, it will continue to deploy Teamcenter Manufacturing and SIMATIC IT Preactor (manufacturing operations management) to optimize its production flows. Additionally, it plans to deploy Siemens’ coordinate measuring machine (CMM) solutions.