Siemens NX CAM software powers precision in electric vehicle part manufacturing [article]
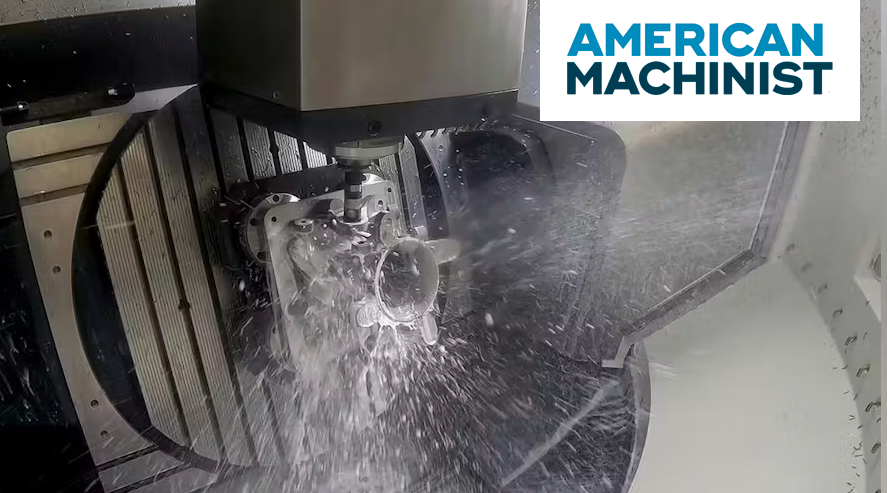
In the automotive industry, the emergence of electric vehicles (EVs) has initiated a wave of manufacturing innovation, prompting manufacturers to reassess traditional production methodologies and adopt new technologies. Specifically, how can manufacturers achieve less material waste and optimize cost savings for real production?
In a recent article published by the American Machinist, a trade magazine of the international machinery industries and their machining aspects, features how Siemens redesigned and manufactured the steering knuckle for Siemens EV eRod. The goal was to achieve a lighter-weight part with higher durability in a faster turnaround time. Explore the article that explains how Siemens and its technology partners met these stringent requirements within a tight deadline using a highly automated manufacturing process that leverages the latest technologies in 3D printing, CNC machining, and CMM inspection for manufacturing the knuckle.
The American Machinist article features how automotive manufacturers can achieve these results by integrating optimization into the design and engineering workflow, particularly through combining additive manufacturing with established manufacturing technologies. Siemens NX software, part of the Siemens Xcelerator portfolio, played a central role in generating initial designs, optimizing component development, and streamlining the manufacturing process. For example, the simulation-driven design phase ensured that the steering knuckle was produced using a minimum amount of material, resulting in a part that is 45% lighter than the standard, with improved stress-handling capability. Comprehensive manufacturing plans were also developed using Siemens Teamcenter and Opcenter software platforms, automating programming tasks and ensuring precision throughout the manufacturing process.
Driving efficiency and precision in EV part manufacturing with NX CAM software
American Machinist features how Siemens NX CAM software, with its advanced features like five-axis programming and integrated simulation, played a key role. Utilizing digital twin technology, with NC programming and advanced CAM features in NX, streamlined the design and manufacturing processes, simplifying programming and reducing machining time.

During the manufacturing stage, the American Machinist article highlights how this project leveraged the perfect combination of additive and advanced manufacturing methods to achieve a 60% less programming time thanks to task automation.
Enhanced quality and productivity through integrated CMM inspection programming

After designing the steering knuckle, optimizing it for weight, durability and manufacturability, American Machinist explains how Siemens addresses quality control for the industrialized process.
Using Product Manufacturing Information (PMI) capabilities in NX helped validate tolerance and dimensional information, ensuring adherence to industry standards. This information was seamlessly integrated into the digital twin of the part model, eliminating the need for paper drawings, and automating the inspection process.
Closing the part’s development loop, NX CMM Inspection Programming automated the creation of inspection features, tolerances, and paths using PMI data, reducing programming time and minimizing errors. It could easily define inspection processes and validate them with machine code simulation, ensuring accuracy and preventing collisions on the shop floor. Upon inspection, any out-of-tolerance situations were quickly addressed using NX CMM’s data analysis capabilities.

At the conclusion of the manufacturing process, the CMM quality control and production preparation phases are crucial steps to ensure the part’s readiness for assembly. This automated approach ensures that the part meets the expected tolerances, guaranteeing its quality and readiness for integration into the final assembly.
As the project approaches its end, American Machinist highlights the impressive EV part manufacturing collaboration among Siemens and its technology partners to produce an optimized knuckle that was eventually installed on the Siemens eRod EV. Siemens believes that digital manufacturing is at a turning point with these technologies, and it is only through projects like this that realizes and validates that outcome. Whether it is from the the perspective of reducing waste and maximizing resource utilization during design or to reduce mass and energy consumption during use, the future of digital manufacturing continues to transform the everyday.
If you missed the series on EV component manufacturing, please find them here:
EV component manufacturing – part 1
EV component manufacturing – part 2
EV component manufacturing – part 3