Additive Manufacturing + Aerospace Industry = Efficiency
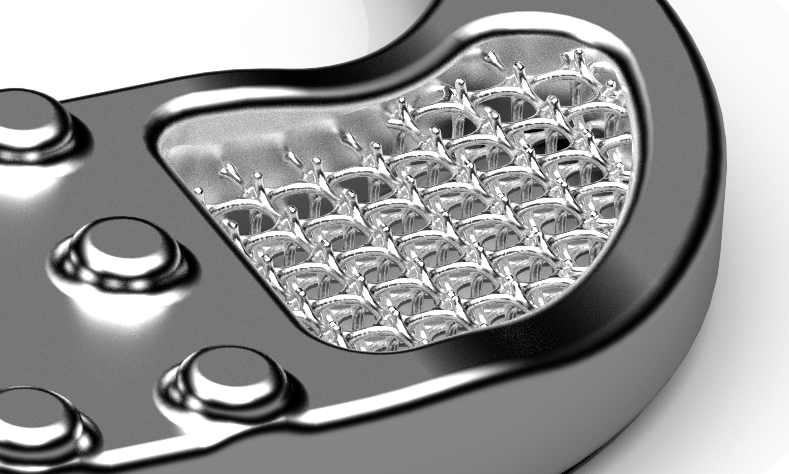
Time for a diet…
I am one of those people who really loves to travel. Even though my enjoyment of flying has lessened along with the decline in the convenience of the endeavor, it still amazes me. It simply blows my mind that it is an everyday occurrence for humans to board an aluminum tube to fire ourselves into the stratosphere, only to arrive on the other side of the planet hours later. It is hands-down a super-feat of engineering and mathematics. Therefore, while it is not as fun as it used to be, I still get a charge of excitement when my plane takes off and I leave terra firma behind, even after hundreds of flights.
However, did you ever wonder why airlines seem intent on trying to get you to travel without carry-on luggage? The answer is weight. Shaving only 20 pounds off the weight of an airliner can save as much as $2 million dollars per year in fuel savings. Speaking honestly, if losing 20 pounds made me $2 million per year richer, I would be living at the local diet center, so I cannot fault them.
However, what if aerospace companies could have their cake and eat it too? Getting passengers to lighten their load is not the only way to reduce the flying weight of an airliner. This is why aerospace companies continually look to reduce the weight of the aircraft itself. In the past, this has meant adopting new technologies like the composite materials used in Boeing’s Dreamliner aircraft. Today, this need for lighter weight aircraft has translated into aerospace being one of the most active industries for additive manufacturing.
Optimization FTW!
At Siemens, we have been talking about the potential for reducing weight via topology optimization for some time now. Whenever we talk about additive manufacturing and aerospace, topology optimization for weight reduction is always a topic of that Topology optimization can be used to reduce the weight of individual partsconversation, and this is for good reason. The potential for optimized parts to reduce weight of aircraft is immense. Now admittedly, there are economic and scale factors that keep 3D printed parts from being used widely on aircraft today. However, we firmly believe that these are issues that will fall away in the future, making additive manufacturing and topology optimization much more feasible in the aerospace world. This is why last year we introduced a topology optimization package for designers in Siemens NX. This is an important part of our end-to-end solution for additive, and our hope is that by bringing this technology out of the analysis realm and into the design world, we can widen the availability of the technology and drive higher levels of adoption for this exciting technology.
On a side note, MIT Sloan Management Review and our partner Deloitte have produced a very nice video series entitled Following the Digital Thread that includes an examination of topology optimization in an aviation context. Siemens and NX is well represented, so we encourage you to have a look.
Climbing the Lattice…
Aerospace companies are also investigating lattice structures for weight reductionOf course, optimization is not the only way to make a part lighter. We have also seen interest in lattice structures in the aerospace industry. Lattice structures allow you tofill the areas of a part thatwould normally be solid material with a grid-like structure instead. The very nature of these structures means that they are very difficult to manufacture using any methodother than additive manufacturing.
Now lattice structures can be used solely for weight reduction, but this is not the only use for them. Lattice structures can also be tuned to distribute forces in desired directions depending on the structure of the lattice. The structure of a lattice can also be tuned to dampen vibrations caused by resonance. Furthermore, they can be used to mitigate the propagation of cracks in a part because of the air gaps between the areas of material.All of these are potential use cases for lattices beyond standard lightweighting and as these structures become more commonplace, and as people experiment more with their behavior, we expect this list of use cases to grow and we often see aerospace companies at the forefront of the experimentation with these unique structures.
Defying Gravity
When it comes to cutting-edge technology, materials, and processes, the aerospace industry is always at the forefront. Additive manufacturing, topology optimization, and lattice structures are all part of this constantly evolving story. At Siemens, we expect the importance of these technologies in to continue to increase as aerospace companies constantly push the boundaries of nature to defy gravity on a daily basis.
If you’re in the aerospace industry and you’re using or looking at additive manufacturing, I’d love to hear about your experience in the comments below.
This is part three of a five-part series on additive manufacturing technology innovation in various industries.
Ashley Eckhoff has a background in engineering and has been with Siemens for over 20 years in various capacities. He has spent the last few years deep-diving into additive manufacturing in both product design and marketing roles.