The Advanced Production of an EV Component at IMTS 2022
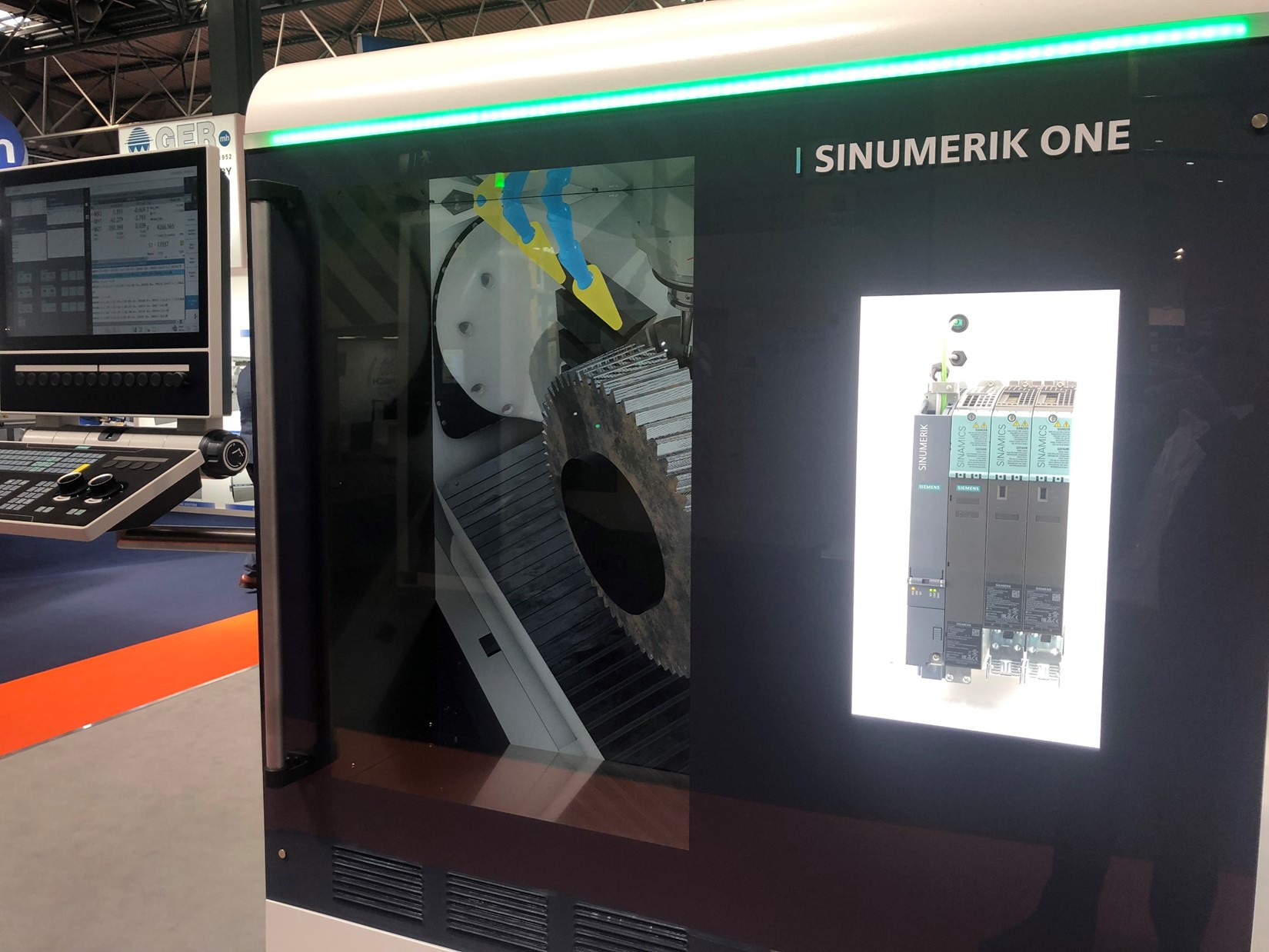
IMTS 2022 is almost here! Don’t miss North America’s leading manufacturing technology show September 12-17 in Chicago. Siemens showcases how manufacturers can boost productivity with digital twin technology. The digital-to-real demonstration follows the manufacturing process of a next-generation lightweight component for an electric vehicle (EV) displayed at the booth. Discover why manufacturers of all sizes choose to partner with Siemens to accelerate their digital transformation with solutions ranging from topology optimization to additive manufacturing, and CNC programming and machining – all topics that will be discussed in detail at Siemens booth #133346.
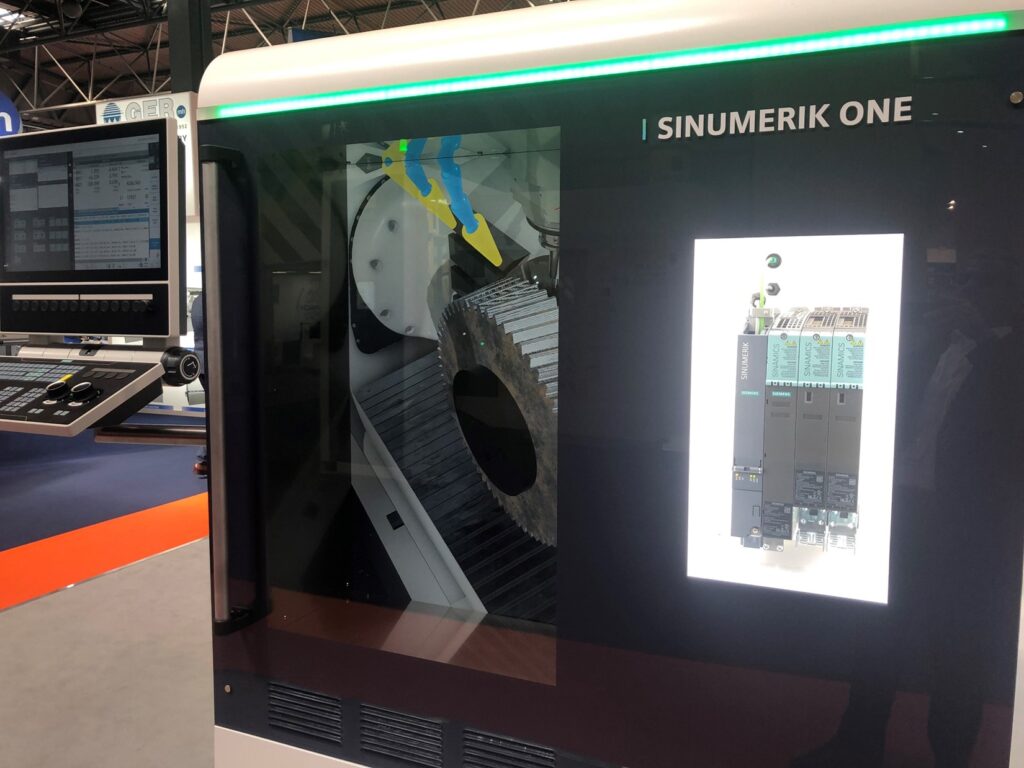
In the last article of the IMTS 2022 blog series, we discussed how NX for Manufacturing allows manufacturers to prepare and program new generations of components by seamlessly connecting the additive and subtractive manufacturing steps, making the process associative and flexible. Using the NX for Manufacturing solution set (CAM, Additive Manufacturing and CMM), we can digitally transform the part production. Now we transition to the next stage of optimizing production by transferring the verified NC programs directly to the IoT-enabled SINUMERIK ONE to feature how the entire steering knuckle is produced.
To start, the EV part is separated into two fragments — the steering knuckle and the spindle. The steering knuckle is produced in a two-step process of 3D printing and advanced CNC machining, while the spindle is machined by using conventional CNC methods. The steering knuckle is designed in NX using the latest topology optimization methods. Using NX, the components are then prepared for additive manufacturing using an industrial 3D printer. This steel-made component is produced additively by means of powder bed fusion technology. Next, the newly printed part is transferred to the SINUMILL machining center equipped with the new SINUMERIK ONE CNC to be finished in a two-step machining process, which was programmed with NX CAM. To make certain the workpiece has the perfect surface finish, the part program is monitored by machine tool digitalization software, Analyze MyWorkpiece /Toolpath, where it searches for any possible defects and guarantees the overall part quality of the finished product.
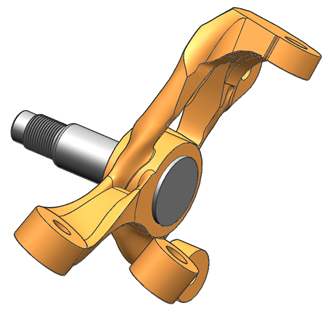
in Siemens NX Software
To conclude the production stage of the EV component, the spindle is programmed in Siemens ShopTurn software and produced on a TRAK TC820sl turning center equipped with the new SINUMERIK ONE control platform. Before the spindles are manufactured, the part program will be brought into the Run MyVirtual Machine environment, the digital twin technology of the machining application. This allows machine tool programmers and operators to verify the part program in the digital world before the first cut is made in the real world. Once the part program is validated and free of errors, it is transferred to the CNC machine for production.
Interested in experiencing the immersive digitalization demonstration of the EV component? Visit Siemens at IMTS 2022 to witness the digital manufacturing process of this next generation part, which is lighter and better-performing resulting in significant strength-to-weight ratio and fundamental design changes to deliver more extensive performance gains. Learn how manufacturers, like you, can combine the real and digital worlds to boost productivity and achieve new levels of flexibility using interoperable software and IoT-enabled machine tool technologies. You will find Siemens in booth #133346 located in the Controls-CAD-CAM pavilion and booth #433028 in the Additive Manufacturing pavilion. We hope to see you there.