Digitalized mold making fuels growth at Haidlmair
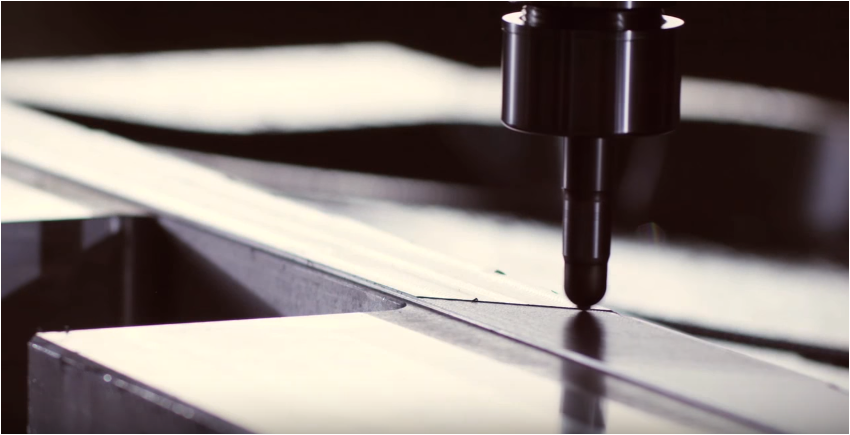
Presenting “Digitalized mold making fuels growth at Haidlmair,” a Siemens PLM Software success story.
Haidlmair is a group of companies based in mold-making. That’s what my father started thirty-five years ago. We’re working together quite closely to become the best mold maker in the world. When I started twenty years ago, I saw that we had three, four different programs in our company.
We also had the issue here that once you design it with that software, once with that software; files look nice but in the end, there were small details which were different.
And now that we focus on one system, it’s easier to bring the part from one department to the other without losing accuracy.
We’re using Siemens technology in all our areas. So we have a streamlined process from beginning to the end.
It’s especially important to have a digital twin in the virtual world because in the CAM department we’re building up the same situation we have on the machine.
We are currently driving, turning machines with the NX CAM. We’re driving 3-axis milling machines with NX CAM and 5-axis milling machines, also, with NX CAM.
It is always resulting in lower costs but also shorter delivery times to our customers.
Mold-making has a lot of different departments. And where the Siemens especially helped us, was to bring all these departments together.
The digital thread is the thing that streamlines the process.
Without the paperwork we can start parallel processing.
They are using Teamcenter to get this part out of the system. They’re using the NX CAM function to make the program for the machines. After the post processing they’re using the simulation functions to bring a safe program to the machine.
Now, even the machine operator can check the CAD model. So before the machine operator gets the physical part on the machine, he can check with the designer to get this fixed early and to get a high quality part.
The next steps in the future are standardization and automation. We are starting in the CAD, going through CAM, going through assembly, and everything is Siemens.
The entire feature based manufacturing is the basis for the automation.
I’m actually working on a project to fully automate the NC programming of electrodes using feature-based manufacturing. We want to build up about 80% of our electrodes to machine fully automatic without any human interaction.
That’s one thing that keeps us ahead of the competitors.
Mold-making is very competitive. But to be honest, we’re not focusing on our competitors, not at all. We are focusing ourselves to grow and make the steps forward.
So with the Siemens integrated system, we have one solution for everything, which is always online, always live. I would say that these are hundreds of thousands of euros every year which we are saving.
I’m very optimistic that we can achieve lower prices in the future with even higher quality than nowadays. And, I guess that’s what every customer would like to see.
Read the complete case study, Injection molding tool maker saves time, enhances quality and eliminates errors