Disrupt and Lead by Transforming Part Manufacturing
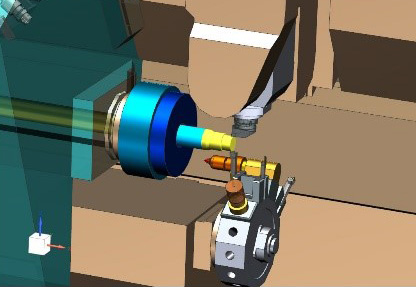
Being profitable in part manufacturing is never easy, and over the past few years has become even harder. Many companies in this industry sector continue to ignore the importance of digitalization relying on traditional ways of production. Manufacturers, irrespective of their size, often fail to understand the exponential escalation of costs caused by productivity inefficiencies and continue operating using “islands of automation”. The digital process gets abruptly broken when the part manufacturing hits the planning and production stages. Sounds familiar?
Digitalization of the part manufacturing sector can no longer be overlooked, and this article aims to touch on the key foundations to transform the sector so the various market challenges can be efficiently addressed, with increased level of competitiveness, and most importantly profitability.
Increasing challenges for European high value manufacturing sector
Gardner Intelligence World Machine Tool Survey indicates that nine out of the twenty top countries, when it comes to machine tool consumption, are in Europe. There is a clear trend within the European zone in utilizing multi-axis, multi-function, multi-channel machines driven by both the re-shoring of manufacturing and high labor costs.
This type of machine considerably streamlines part manufacturing processes; however they present substantial challenges. Cutting tool breakage, part scrapping, or machine crashes, lead to downtime, productivity losses, and ultimately operational costs.
When you then add the increased pressure of shortened delivery times, competitive pricing, and expected quality the profitability boundaries get narrowed to a point where there is no margin for error.
The way forward
To remain competitive, part manufacturers must transform their operations through digitalization. A proven concept to achieve this is the implementation of a highly accurate digital twin. The potential value of the digital twin lies within its ability to represent the physical in the digital world.
Realizing an accurate virtual representation can only be achieved through continuously enriching the various components of the digital twin. An on-going activity to digitally capture all phases of the part manufacturing processes as well as the required production resources (i.e. machine tools, cutting tools, fixtures, part process planning, etc.), and its in-use monitoring.
The true digital twin of the Machine Tool
With the most accurate digital twin of the machining process, companies can dramatically improve their programming efficiency and eliminate multiple iterations with external NC Code simulation systems. This is particularly relevant for the most advanced and therefore most complex machines to program, as it removes the “islands of automation”.
With a true digital twin of the machine tool, fully operative in the context of the part programming we are seeing:
- NC programming productivity doubled.
- Reliable and safe toolpaths delivered, with significant part quality improvements, as well as shorter delivery times.
- Production resources maximized, leading to productivity gains of 70%, resulting in both business expansion, and profitability.
Digitalization of part manufacturing is a must do!
Ignoring digitalization of the part manufacturing space seriously undermines the ability to remain competitive and ultimately stay in business.
Many of our customers, from small business to large enterprises, have been digitalizing their manufacturing operations using Siemens’ software for part manufacturing. Its comprehensive capabilities provide significant process improvements contributing to the companies’ sustainability and commercial success.
Please contact me directly should you be interested in gaining further insights on how the most accurate digital twin can support your company in transforming part manufacturing operations.
Where manufacturing meets tomorrow.
Written by Pedro Leon (pedro.leon@siemens.com), EMEA Portfolio Development Team – Digital Manufacturing