Enabling digital collaboration through manufacturing project management software
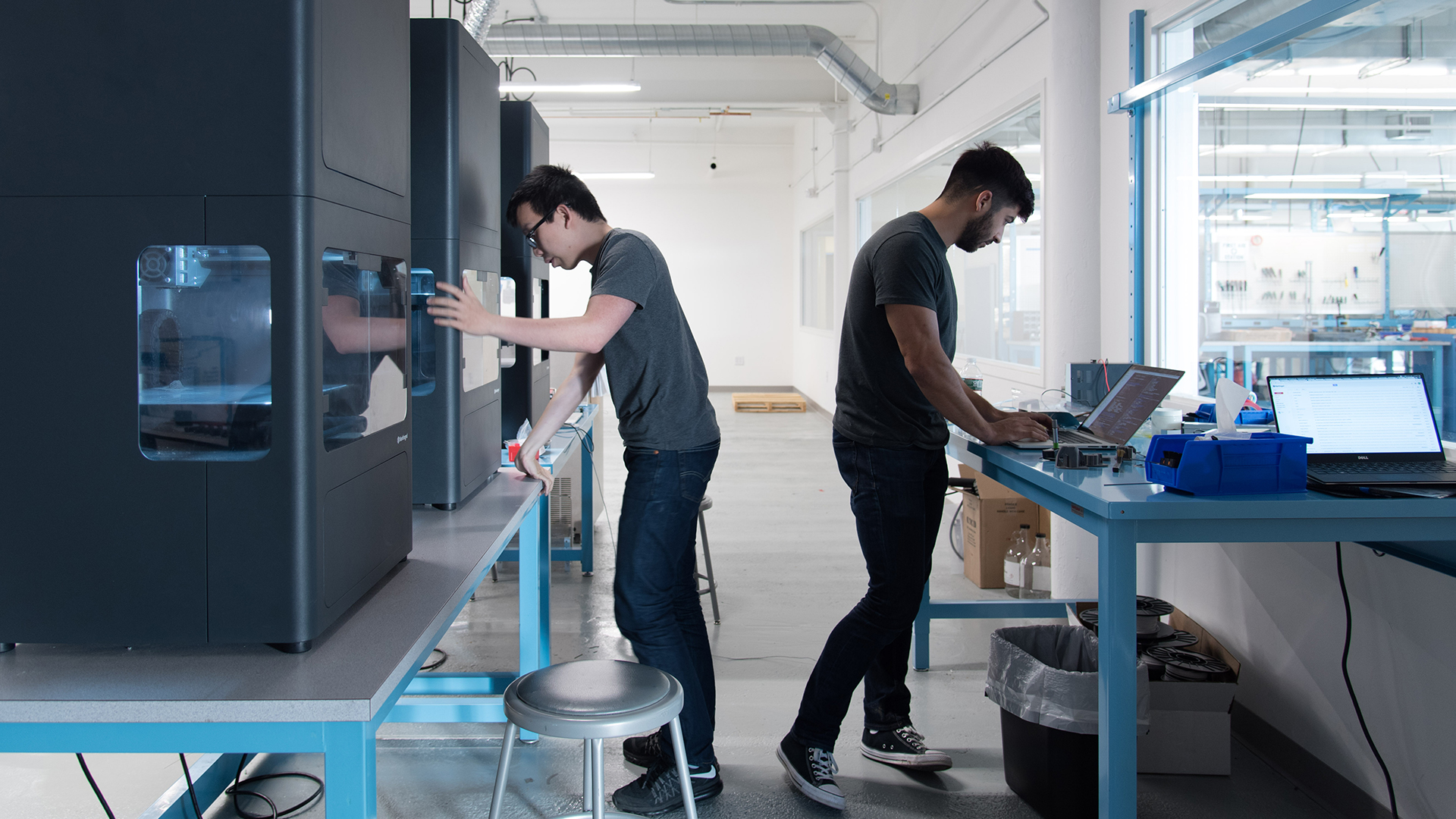
As you’ve now gathered, if you’ve been keeping up with this blog series, I’m pretty passionate about solving the problems I’ve encountered in the machine shop industry over the last 20 years. The previous blogs in this series addressed real-time visibility into job shop assignments, and the issues with chasing paper across the shop floor. In this blog, we will take a deeper dive into another issue related to the attention disorder, namely the hurdles in collaboration resulting from unlinked process and data. Using manufacturing project management software, the machine shop can streamline their work.

The reality of leadership in a machine shop
Many employees imagine that being the boss would bring prestige and leisure, delegating all work to others. For those who have moved up into these positions, especially in a job-shop environment, the reality is hugely different, to say the least. Keeping track of multiple jobs, people, tooling, machinery, and other resources in a fast-paced, low-volume, high-complexity process can be a heavy burden for those willing to lead.
I had this manager at a tooling shop I worked at years ago in Warren, Michigan, who never seemed to leave the building. Most of the employees there worked at least six or seven days a week, but he was one who outworked them all, constantly coming in earlier than others while also staying late. Sadly, this dedication came at a heavy cost in his personal life.
It makes sense when you really pay attention to what these people are responsible for daily. There are so many moving parts to the job shop, and customers want their parts yesterday. Every employee will have questions about ongoing work at some point, which prevents the manager from doing some of their own required tasks. The term “firefighting” was often used in some of the interviews we conducted with job shops, speaking about the challenges they endure constantly. For the individual manager, when the other employees have finished their shift and gone home to their families, the remainder of the day’s workload still sits piled on the desk waiting for completion.
The communication bottleneck in the machine shop
Clear and effective communication is key to getting work done on the shop floor and freeing up management’s time, but there are more often bottlenecks caused by the communication systems in place.
In one interview, an experienced machine shop manager expressed his frustration to us about verbal and email communication. As he explained it, verbal communication is a problem because the human memory is not the best storage system for information. When people walk away after speaking about project plans or problem solving, the actual words spoken seem to evaporate into thin air. What two people remember about a single conversation is often different.
This manager cited emails as another poor conduit of communication because, although the embedded text does capture the conversations, it often provides too much information rather than not enough. We are all familiar with the scenario where we are the latest recipient of a long email chain which was previously replied to and forwarded numerous times before it landed in our own inbox. Now it feels like we must read a whole unpublished article just to find a little bit of information that we need.
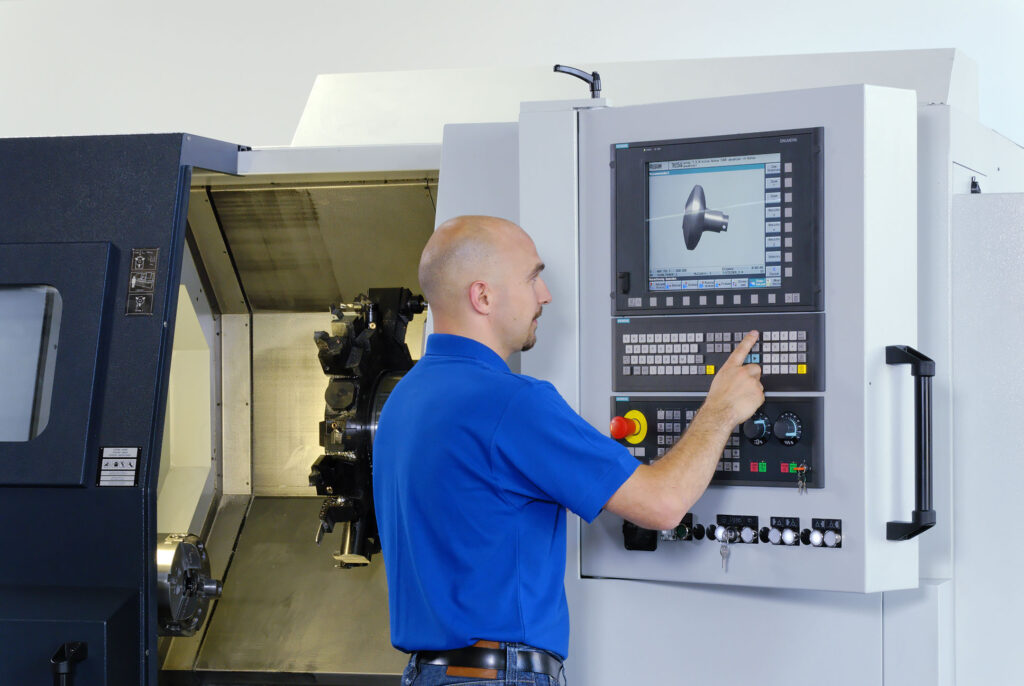
Solving the attention disorder with manufacturing project management software for machine shops
The machine shop is no different from other fast-paced environments where decisions are being made and changed constantly. Building on the digital infrastructure for common data and document repositories and digital workflows described in the previous blogs, the digital machine shop also requires a digital collaboration hub where questions can be resolved and answers approved. The resulting actions should be documented for future reference and validation.
Manufacturing project management software is the digital solution required. It should allow management to record the process plan and couple it with all the required shop documents needed for a heightened understanding of the intent. Also, collaboration should be captured on the same platform, directly in the process plans being communicated or on the documents needing further clarity.
We know the attention disorder can be frustrating for people working in the machine shop environment. Instead of getting pulled in all directions, manufacturing project management software with digital collaboration helps us reduce our search time for relevant documents and directions, and gets us working smarter and faster.
So, how do we create that type of solution? By tailoring it specifically to the needs of the small- to medium- machine shop environment. Discover more about Siemen’s solutions for today’s machine shops.