EV component manufacturing – Part 2
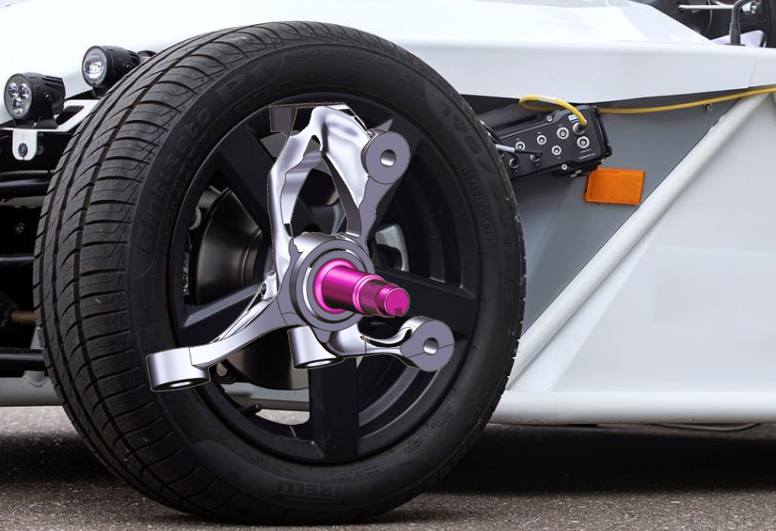
The digital thread – data management for seamless digital manufacturing
In the first blog in this series, we presented the manufacturing challenge before us: the redesign and manufacturing of the steering knuckle for an electric sports car with the goals of achieving lighter weight, higher durability, and faster turnaround time. Meeting these stringent requirements within a tight deadline necessitates a highly automated manufacturing process that leverages the latest technologies in 3D printing, CNC machining, and CMM inspection for crafting the knuckle.
As we tackle what is essentially an optimization process, we will be going in circles – by design. This highly iterative process involves a team of engineers distributed globally, where a change in one step impacts all others. The question arises: how will we manage all of these cycles?”
First, let’s take a look at our team spanning two continents:
- Our CAD engineer, Joe, is working from Manchester, UK
- Mike is in New York and is responsible for CAM and is managing the manufacturing data
- Carson is doing additional CAM programming in Charlotte
- Our additive engineer, Adam, is in Indiana
- CNC Machining and 3D Printing is done in Hoffman Estates outside of Chicago
- The job-shop machining expert is Chris, who uses Sinumerik CNC technology. He’s located in New York state.
- CMM inspection programming is done by Joe in Orlando.
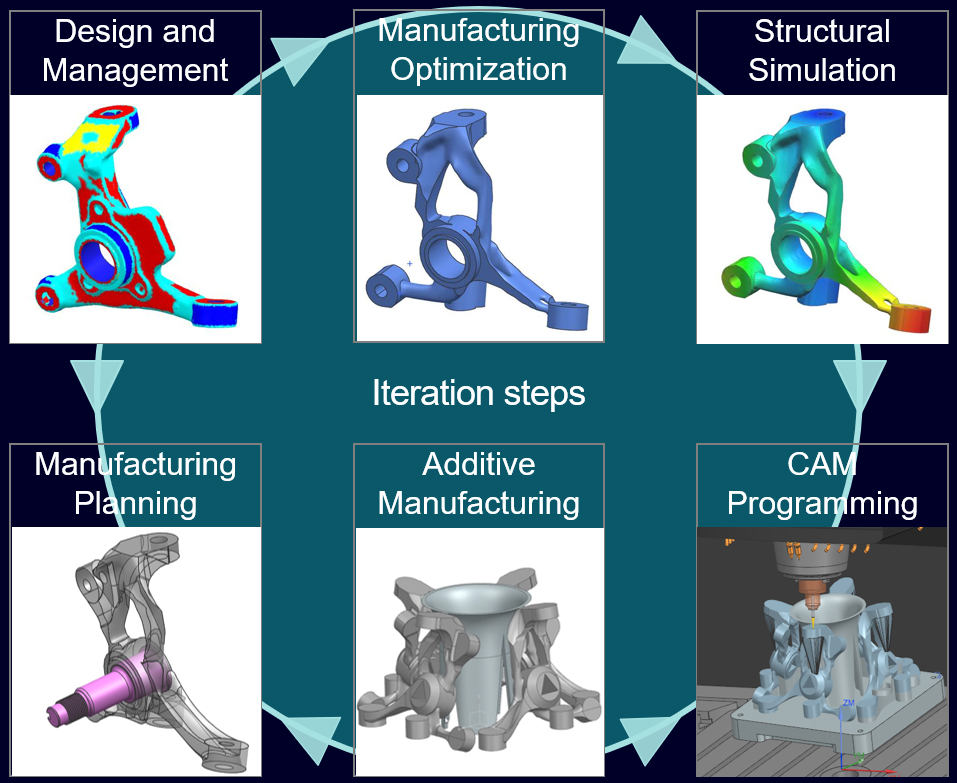
In a traditional production process, without a digital manufacturing infrastructure, this work would typically be carried out in isolated silos by respective experts. In our example, our engineering experts would have generated more than 20 versions in a single week that were not aligned with one another. The conventional process is painstakingly slow, involving numerous interface discussions, emails, no real concurrent work, and numerous variants that are incompatible with each other. The most significant concern with the conventional approach is that the manufacturing teams on the shop floor can never be certain if they are using the latest revision to produce the part. This is a critical issue, impacting the quality of the part, the safety of the consumer, and the reputation of the company.
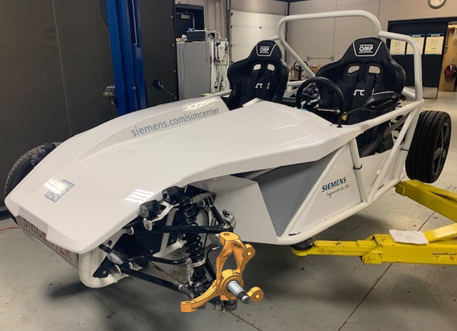
How can we expedite this collaborative and iterative process? We must systematically manage these iterations across our team in a comprehensive and disciplined manner; otherwise, chaos may ensue. Thankfully, our digital manufacturing infrastructure provides a well-managed environment with immediate access to all pertinent data, design iterations, and real-time changes. It is the sole means by which we can achieve efficiency, prevent errors, and operate a more agile process.
Our optimization process becomes remarkably seamless, enabling us to address the following fundamental questions that demand cross-functional collaboration:
- What is the required function of the part, and what are the initial design requirements?
- Can the part be 3D printed in this design?
- If the additive manufacturing engineer makes changes, is it still structurally sound?
- Are the ‘fixtures’ printed with the part?
- Can all dimensional features be accessed on the machine with standard tools and without collision?
- Can all support structures be removed on the CNC machine to avoid dust exposure?
In this blog series, we will describe how we successfully addressed all these questions before creating a single physical part using the digital twin technology.
A single digital environment for design and manufacturing optimization
Performing these optimization cycles in a single environment not only accelerates time to market, but also improves quality. We eliminate the potential for miscommunication, human error, or data transfer mistakes. Design changes can be easily implemented by the 3D printing engineer and validated for structural integrity within minutes. Simultaneously, the manufacturing engineer can adopt these changes for the manufacturing setup and validate the operations with the digital twin of the machine tool. With the addition of Product and Manufacturing Information (PMI) to the model, this process seamlessly progresses, allowing the CMM program to be developed based on the same source of truth. This highlights the power of the digital machine shop, connecting design, engineering, and manufacturing processes with the digital thread
Teamcenter is the digital backbone that enables us to increase planning efficiency and maximize resource utilization
Teamcenter is a part of Siemens Xcelerator, an open digital business platform that includes a curated portfolio of IoT-enabled hardware and software, a powerful ecosystem of partners, and a marketplace for learning, exchanging ideas, and accessing the growing portfolio.
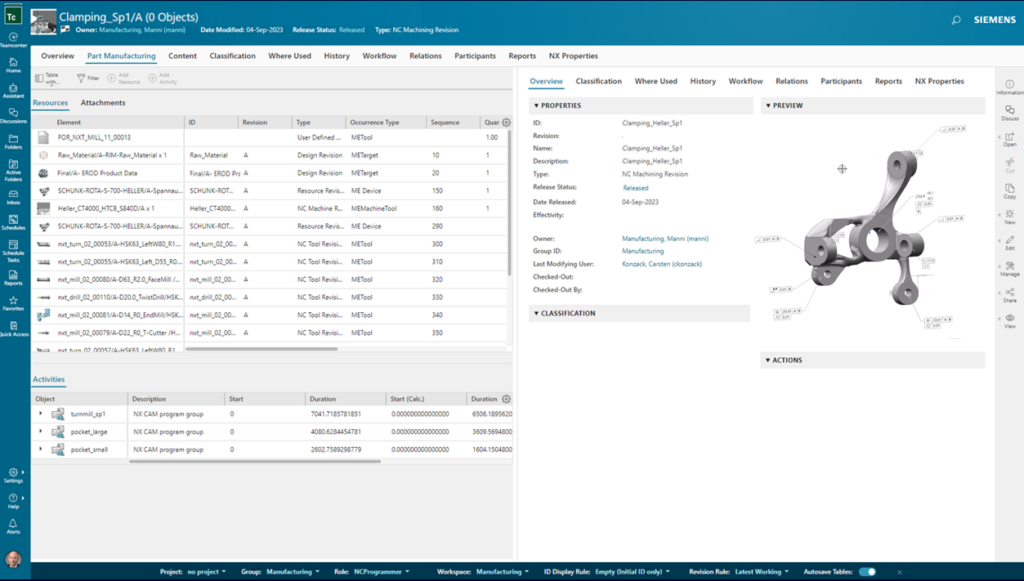
Teamcenter delivers efficient digital manufacturing collaboration
Teamcenter connects Siemens PLM Software’s comprehensive ecosystem, managing product lifecycle management (PLM) data and processes from design and engineering through production
We used Teamcenter as our environment to manage product and process definitions, data files, and resources throughout our project. Teamcenter assisted us in defining the manufacturing process for the wheel knuckle, while also handling all the associated data, including the 3D model, CNC programs, and shop docs. All steps were meticulously aligned with the correct order, and time and resource information was added to optimize the production process.
We maintained workflows and user roles for our dispersed team, while also tracking capabilities to monitor document revisions and release status. Within the same Teamcenter environment, we managed data for tools, fixtures, and machines, including versions of CNC programs. The manufacturing plan covered the entire process, starting with part preparation, CAM programming, and concluding with inspection on the CMM machine.
Connecting the shop floor digitally
To deliver the CNC programs directly from Teamcenter to the machine controller, we utilized Shop Floor Connect. This Teamcenter application, more than just a traditional DNC system, connects to the centralized Teamcenter database, helping us avoid data duplication to ensure the correct manufacturing data is used on the shop floor. It also enables production staff to access current and released CNC programs, drawings, 3D models, and other data sources through a web-based user interface that runs on any browser-enabled device or controller
Because we used the Siemens Xcelerator portfolio for the digital machine shop to design and produce our new steering knuckle, we achieved complete collaboration across all functions. We will explore how this impacted efficiency as we step through each phase of the project in the next blogs in this series.”
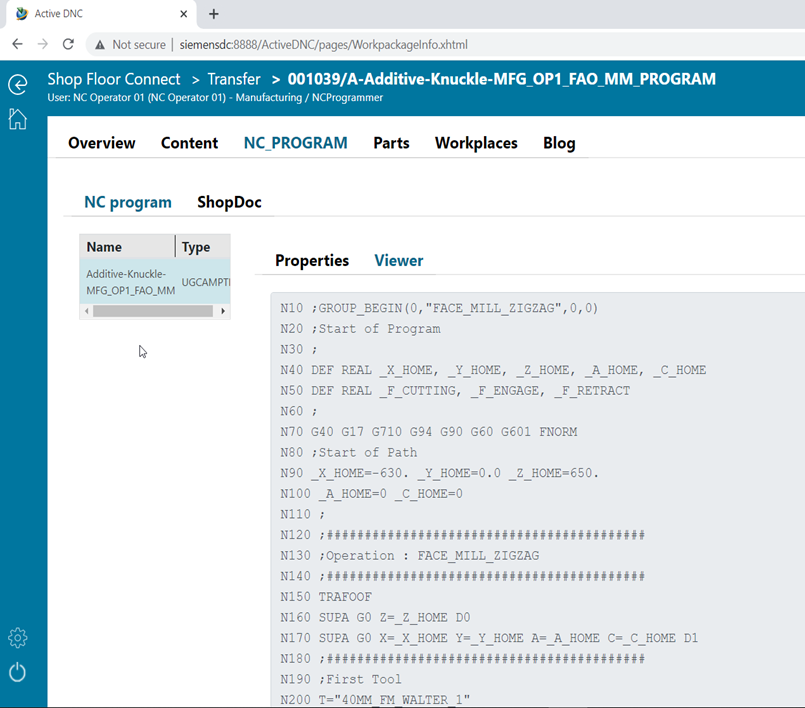
The next blog will delve into the generative design and 3D printing tasks required for our new part.