Must See NX Manufacturing Sessions @ Realize LIVE
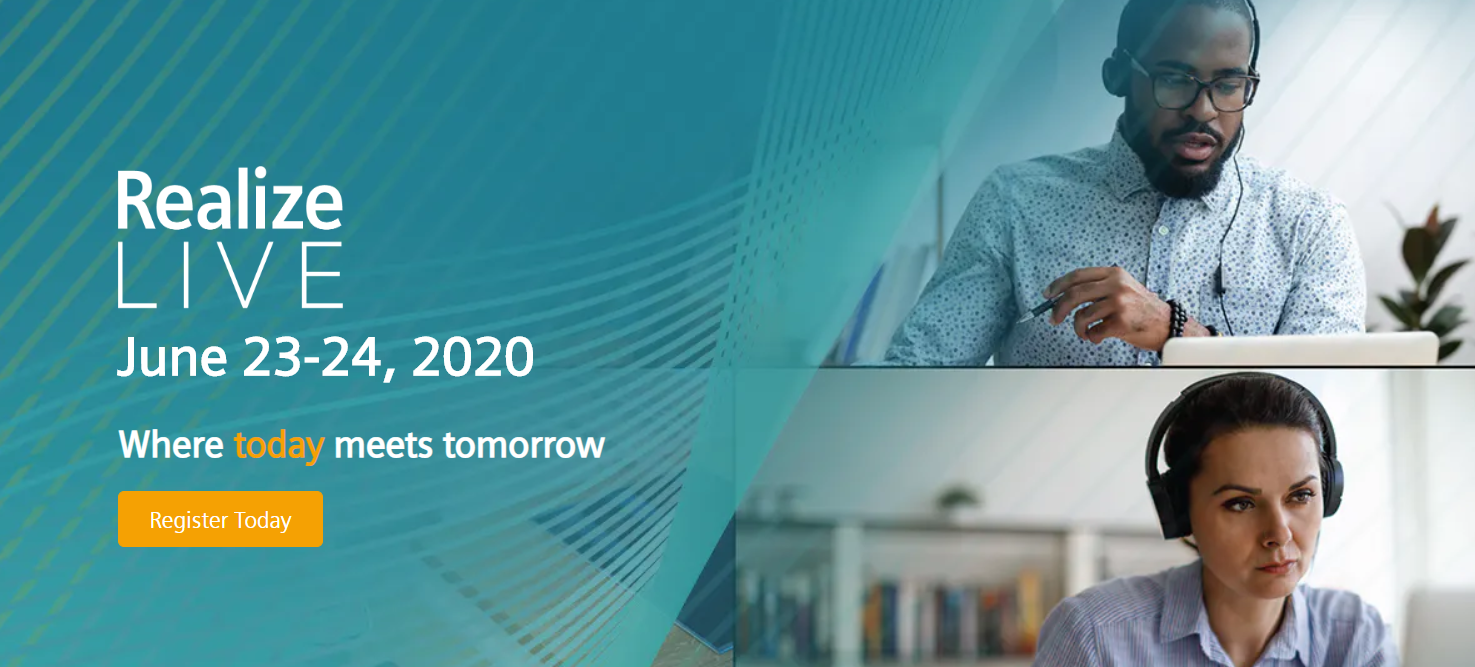
Looking for mind-expanding presentations by industry leaders and hands-on training? NX Manufacturing @Realize LIVE featured sessions bring together some of the biggest and brightest names of our time and offer live product training experiences. Spanning various themes and trends, view a snapshot of the most transformative ideas shaping our future.
Tuesday, June 23
12:30 PM – 1:10 PM EDT / 9:30 AM – 10:10 AM PDT (40 Min)
Xcelerator Portfolio Update

Rapid-Response Innovation in Manufacturing
Manufacturing is critical now more than ever. Rapid-response innovation is needed to address the complexity that industry faces today. And, by addressing this complexity, you gain a competitive advantage. You will hear from Zvi Feuer and his colleagues how Siemens software helps manufacturers effectively respond to today’s challenges and build innovative products using a comprehensive Digital Twin.
To properly maintain these innovative products, manufacturers must also integrate service operations into their processes using the comprehensive Digital Twin. This will provide the required asset-specific configuration and service requirements of the physical assets directly linked to all available engineering and manufacturing data. You will hear from Olav Hjermann how service in product and production life cycles benefits manufacturing and maintenance operations at OneSubsea.
—–
1:10 PM – 1:30 PM EDT / 10:10 AM – 10:30 AM PDT (20 Min)
Q&A for Xcelerator Portfolio Update Sessions
—–
1:50 PM – 2:10 PM EDT / 10:50 AM – 11:10 AM PDT (20 Min)
Breakout #1

Hendrick Motorsports: Manufacturing Race Car Components with NX CAM
Learn how Hendrick Motorsports uses NX CAM to machine powertrain and vehicle components for high-performance vehicles. Winner of multiple NASCAR championships, Hendrick Motorsports uses NX software to program machining operations for a wide range of components of various complexity, materials, and tolerance requirements.
This session will provide real-world part examples that are manufactured using different CNC operations, such as 3-axis machining, 3+2 positioning and 5-axis simultaneous milling. Using NX CAM’s comprehensive CNC programming functions enables the programmers and machinists to quickly make any part, turning the engineers’ ideas into reality.
—–
2:10 PM – 2:30 PM EDT / 11:10 AM – 11:30 AM PDT (20 Min)
Training Session #2
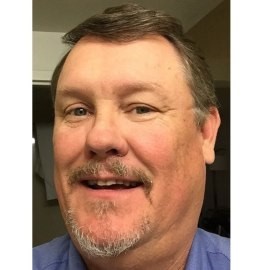
NX CAM Integrated CNC Simulation
In this session, you will select a machine tool from the provided library of machine tools, and then simulate a machining operation to discover problems before you run the code on a real machine.
—–
2:30 PM – 2:50 PM EDT / 11:30 AM – 11:50 AM PDT (20 Min)
Wednesday, June 24
12:30 PM – 12:50 PM EDT / 9:30 AM – 9:50 AM PDT (20 Min)
Breakout #3

Streamline your CAM and CMM Processes Using PMI
The successful launch of an automated CNC machining line involves a large team working concurrently. Competitive pressures require a lean manufacturing planning process so that time is not wasted by manual re-entry of data at every stage.
The PTME team at Ford is implementing a MBD Strategy in the design of high volume machining lines for automotive powertrain components. The emergence of PMI as an industry standard means that the manufacturing and inspection engineering workflow can be streamlined for higher efficiency and lower cost. This presentation will highlight the benefits of this strategy including higher quality information and the ability to automate repetitive engineering tasks through the reuse of PMI information.
Part 1 of this session will show how PMI information is used to make faster and more consistent CAM decisions.

- Creation of optimized toolpaths using the Machining Knowledge Editor that reflects information embedded in the 3D model.
- Generation of 3D in-process models that represent the as-cut condition using the capabilities of NX MLP to validate the entire line.
- Customization using the NX Open API to fill in the gaps so that in-process PMI tolerances can be created using mathematical stack-ups.
Part 2 of this session will show how the same PMI information is reused to create CMM programs integrated on the machining line.
- Significant reduction of CMM programming time over interactive input of tolerances.
- Programming of In-process inspection on shop hardened CMMs or On-Machine Probing using the In-Process PMI output from the individual operations.
- End of Line inspection using the finished part PMI.
—–
1:10 PM – 1:30 PM EDT / 11:10 AM – 11:30 AM PDT
2:10 PM – 2:30 PM EDT / 11:10 AM – 11:30 AM (20 Min)
Industrial Production of Big Metal Additive Structures

Breakout #6
The power of large-scale industrial hybrid metal additive manufacturing is the rapid production of design candidates for practical evaluation in real world environments. Generative and optimized designs are powerful capabilities to create efficient structures that express a new level of performance. Optimized designs are often 3D printed at small scale, however large-scale hybrid metal additive manufacturing provides opportunity to produce these designs for industrial applications such as automotive chassis, aerospace prototypes and even Naval vessels. The Big Metal Additive process has been developed specifically to produce these types of large complex optimized structures. NX Hybrid Additive CAM is used to program additive and subtractive operations to produce these complex geometries.
This presentation will present a case study of benefits, applied generative optimization, and design rules for producing large scale hybrid metal additive manufactured optimized structures applicable in many industries. The value of full process simulation and visualization will be illustrated. The process of creating multi-axis hybrid additive CAM codes will be explained. Several optimized and produced parts will illustrate the case study.
—–
2:30 PM – 2:50 PM EDT / 11:30 AM – 11:50 AM PDT (20 Min)
Register Now
Learn more about our presence at Realize LIVE on the Digital Manufacturing Experience page.