NX CAM helps Hendrick Motorsports accelerate racecar component manufacturing
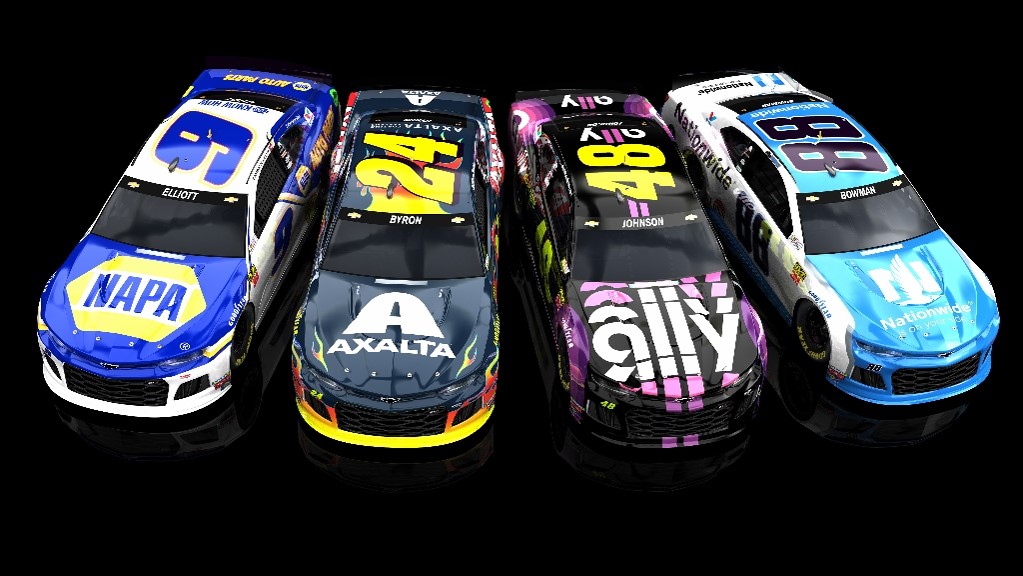
Fewer setups and faster machining processes result from improved manufacturing engineering
Since its founding in 1984, Hendrick Motorsports (HMS) has earned a record 13 car owner championships in NASCAR’s premier division. From its headquarters in Charlotte, North Carolina, USA, the company currently fields four full-time Chevrolet race teams on the NASCAR Cup Series circuit. Hendrick has partnered with Siemens since 1998 to build its impressive race cars.
At Realize LIVE 2020, Siemens’ global customer event, HMS design engineer David Kapp explains how Hendrick Motorsports is using Siemens NX CAM to accelerate the manufacture of racecar components. Kapp provides manufacturing support for Hendrick’s CNC Operations Group. “My job is to help the people who take our parts from concept to reality,” he notes.
Manufacturing challenges
Making parts for NASCAR racecars is challenging. Part quality is paramount in these vehicles, which feature engine power in excess of 700 hp and speeds in excess of 200 mph. Parts must perform effectively for hours at a time under these extreme conditions.
“We deal with complex geometries, multiple materials, and all the while we have to make sure that our products meet the strict NASCAR regulations,” Kapp points out. “We also have to race against the clock and the calendar every week to meet our deadlines. New design ideas will help us only if they make it to the track.”
To meet these challenges and make their delivery deadlines, HMS has invested in multifunction computer numerical control (CNC) machines with multi-axis positioning, along with conventional machining equipment. This production environment enables HMS to reduce the number of setups needed for each component. The approach speeds the manufacturing cycle and eliminates some of the tolerance stackup that occurs each time a new setup is employed. Manufacturing components on this advanced shop floor requires the support of CAM software that efficiently orchestrates end-to-end part manufacturing and delivers high-precision parts.
The solution
Hendrick Motorsports accelerates part production by using comprehensive CAD/CAM software that connects the entire team. Their Siemens system features NX™ software for design and manufacturing, and Teamcenter® software. The system standardizes part development and production, which has enabled HMS to improve part tolerances while minimizing the number of machining setups.
To engineer each manufacturing process, HMS captures all the machining entities (such as the table and rotor) in a digital twin that enables them to accurately design fixtures in NX CAM. HMS manufacturing engineers then collaborate with their machinists to come up with the machining approach that allows them to complete as much of the part as possible in each setup. “Once we have these assemblies in place, we can use them over and over again in future manufacturing jobs,” Kapp adds.
Kapp’s Realize LIVE presentation showcases the manufacturing approach the company has developed for three representative components: a steel rear spindle for the wheel hub, an aluminum cooling system expansion tank, and an aluminum engine oil pan.
Wheel hub spindle
The spindle component is part of the rear axle housing; the wheel hub rides on the spindle and the rear axle passes through it. NASCAR rules stipulate that the part must be made in one piece from magnetic steel. NASCAR also dictates the size and minimum wall thicknesses of the spindle, so the HMS engineering team is tasked with meeting these requirements while making the component as light as possible. Both inside and outside surfaces are sculpted where possible to minimize weight. Specific spindle configurations are tailored to the particular track on which the car will race.
To manufacture the spindle, HMS machinists start with a blank that has a completed “snout” where the rear axle will ride. The blank is secured with custom jaws and finished in one setup using cavity milling and variable streamlining of the inner (ID) and outer diameter (OD) surfaces. Machining the complex inner diameter is especially challenging, Kapp notes. “Tool choice and setup rigidity, feeds and speeds can yield a really nice surface finish,” he says.
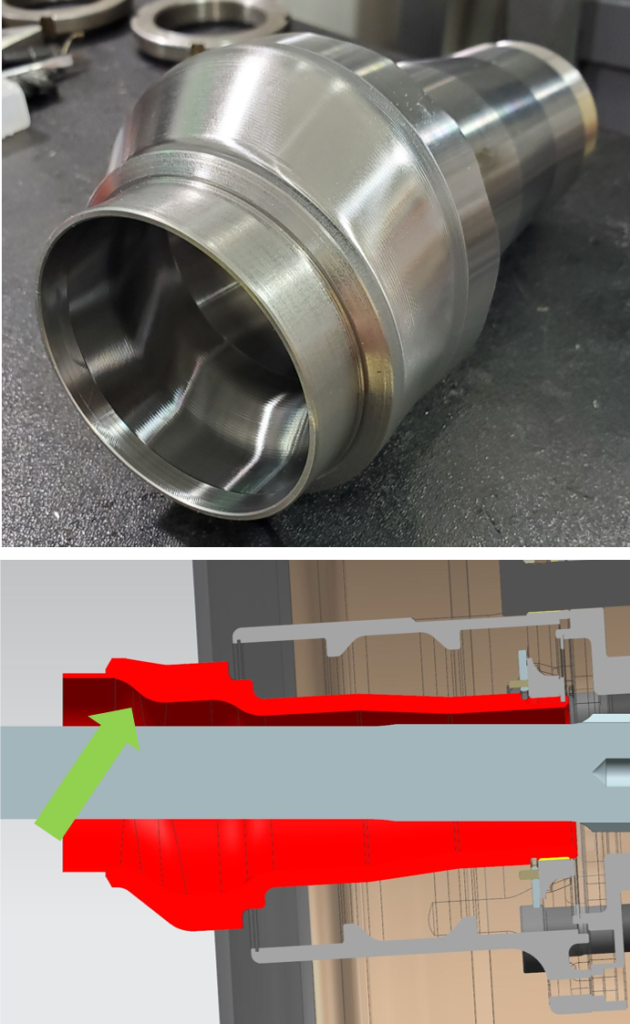
Cooling system tank component
The cooling system tank component is machined from aluminum stock in two setups. About 70 percent of the component’s outside is created, as well as the entire ID surface and flange profile, by a mill-turn operation in the first setup. HMS has chosen this first setup with a live tooling option knowing that actual machining may take longer than it would with conventional milling. The live tooling setup makes up the difference by eliminating additional setup time and fixturing.
The rest of the OD and plumbing ports are machined in a conventional mill during the second setup. A custom fixture positions and holds the work in progress (WIP). “Our programmers are the same people who operate the CNC machines,” Kapp says. “They understand best how they want to hold the part and machine the surfaces. They frequently model their own fixtures in NX for the specific jobs.”
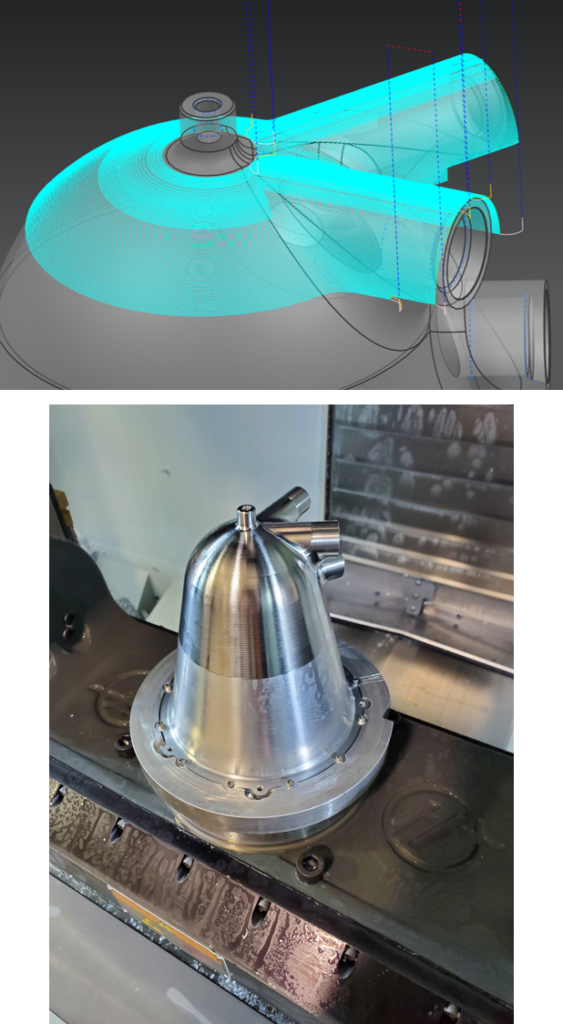
Oil pan
The engine oil pan is made from aluminum billet in two machining setups. Machining from a billet, of course, involves removal and recycling of a lot of material – 90 percent of the material in the case of this oil pan. But the advantages make this the right choice for HMS. “We choose to machine this part 100 percent,” Kapp explains, “because we don’t have to worry about porosity issues, we don’t have to invest in tooling for castings, we have no finish machine work of castings to deal with (and fixturing for that), and we can change the design anytime we want and machine the parts accordingly.”
For the first setup, HMS has developed a configuration that includes a custom rotary adapter plate and riser for the vice that holds the billet. “It’s critical that we maintain tolerances on feature size as well as feature-to-feature relationships, so that the rotating parts do not contact the oil pan,” Kapp notes. Using cavity milling and finishing operations, the operator machines everything that interfaces with the internals of the engine in this setup. The configuration and fixturing allows machining to be performed on five of the six billet faces. The second setup completes machining on the sixth face.
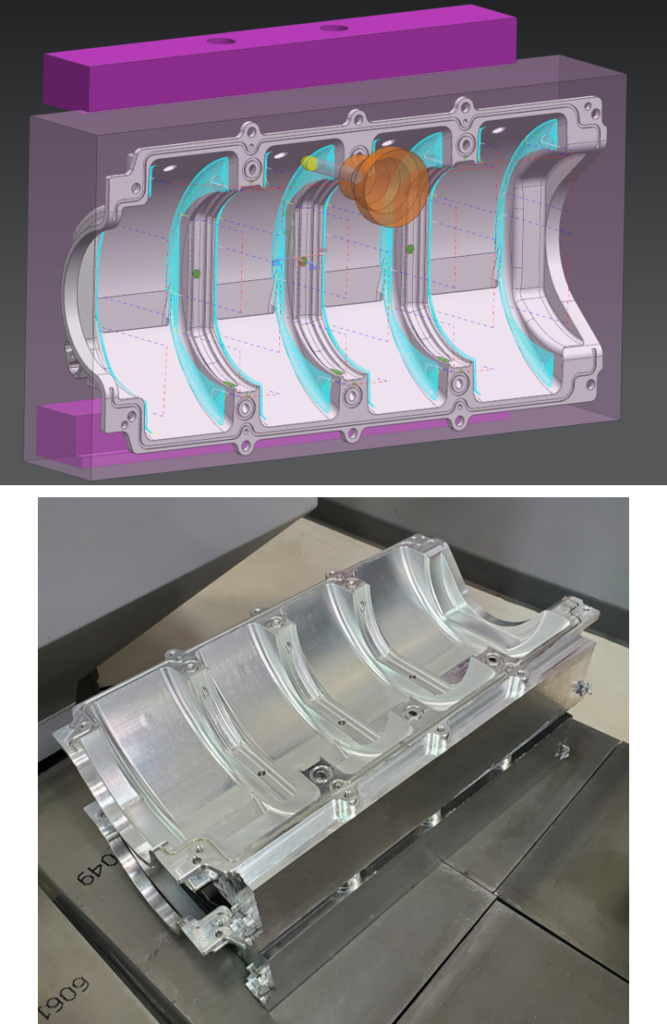
Racing performance
The proving ground for Hendrick Motorsports’ manufacturing efforts is one of the harshest of any industry. The company’s partnership with Siemens is a contributing factor to its continuing success: The thirteenth championship occurred between Kapp’s 2020 presentation and the drafting of this blog.
“Our industry thrives on speed, whether it’s on the shop floor or the racetrack,” Kapp concludes.
Siemens continues to partner with leaders across manufacturing industries to build products and systems that improve sustainability, safety, quality, and compliance, allowing them to better serve their customers, and contribute to a more prosperous world.
—–