Production-level 3D printing gains momentum
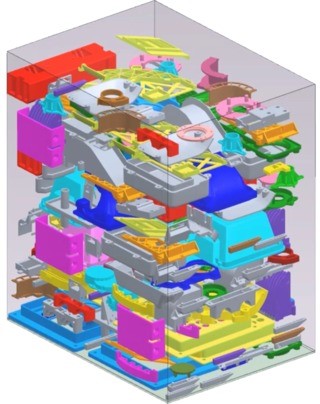
A recent article in OEM Off Highway magazine explores how the feasibility of 3D printing end-use parts has grown in recent years and how the growth presents the challenge of making additive manufacturing a “normal part of the production process.” Sarah Jensen, Managing Editor, interviewed Aaron Frankel, Senior Director of Marketing for Siemens PLM Software, to get his take on the challenge and how Siemens is addressing it with new solutions and collaboration with industry partners. The following are Aaron’s quotes from the article. You can read the complete story, “Production-Level 3D Printing Gains Momentum,” on OEM Off Highway.com
Aaron Frankel says there are a number of barriers in the AM process which need to be overcome in order for it to keep growing, particularly in the process of going from product development to the shop floor. This is due in part to the fact that multiple disconnected software applications are used by engineers and designers, and the manufacturing planners. “Typically we see companies stitching together a number of disconnected software applications in order to design and make parts with additive manufacturing,” Frankel explains. “This way of working requires numerous file conversions, and tends to result in an uncontrolled workflow since the data and process cannot be effectively managed across the different systems.”
Siemens will often see 3D printers in a corner, or disconnected from the mainstream production environment. “To drive the economic justification, we need to be able to incorporate the printing technology directly into our mainstream production, automation environment,” says Frankel.
Like Renishaw, Siemens wants to help companies take full advantage of the potential of AM. Over the past year, Siemens has announced a number of partnerships with additive manufacturing software vendors including Materialise, as well as 3D printer manufacturers such as Stratasys Ltd. to industrialize AM. “Our vision is to create an integrated end-to-end system for additive manufacturing where a company can fulfill the entire product development and manufacturing planning and execution process all in one system,” says Frankel. “We eliminate the data conversion, manage the data between every step of the process, as well as the work flows and collaboration between everyone and the equipment needed to fulfill the process.”
Siemens’ NX can maximize the number of prints to be executed within the HP Multi Jet Fusion 3D printer build volume by loading multiple 3D part models into NX, and then auto nesting and submitting them (powered by integrated Materialise capabilities) directly to the HP 3D printer.
As an example of the end-to-end solutions Siemens is providing for 3D printing, in May of this year it announced it will be introducing a new online collaborative platform for on-demand product design and 3D printing production. The platform will provide an environment capable of connecting all members of the global manufacturing community to maximize resource utilization and access additive manufacturing expertise.
The company also recently announced the creation of a new HP Inc. certified AM software module. It allows customers to develop and manage parts in a single software environment for their HP 3D Printing projects to avoid needing to use third-party tools or spend time converting data.
Siemens is building an ecosystem of partners and bringing together expertise to enable not only end-to-end AM solutions, but also explore new opportunities for more advanced types of 3D printing to create more sophisticated parts in a reliable fashion, and do it repeatedly at greater scale.
“We believe that in order to achieve the industrialization of additive, it requires an ecosystem of partners working together, each bringing their unique technologies and strengths to the table, and figuring out how to combine them to achieve something bigger,” says Frankel. “I think it would be very difficult to develop a solution in isolation. No one company at this point seems to have all the technologies together, and the foresight to be able to scale up and push the boundaries of what’s possible with additive. I think there’s still a lot of room for additive manufacturing technology to grow—in applications and in its maturity.”