Simplify Machining Complexity using Integrated Toolpath Analysis
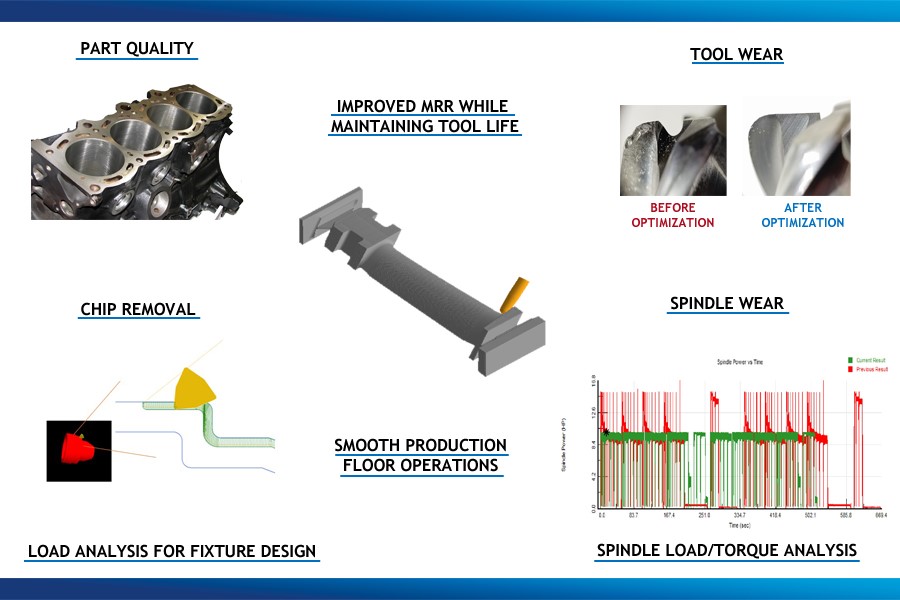
This article was written by Nishant Saini at Third Wave Systems.
CNC machining is a highly competitive field. Companies compete on razor-thin margins to deliver the most optimal quality products to customers. In this competitive environment, it is critical to ensure that you use the most efficient toolpath. An efficient toolpath needs to strike a balance between part quality, tool life and cycle time. The ability to analyze and optimize your toolpath, as part of your workflow, using the integration between Siemens’ NX CAM software and Third Wave Systems’ Production Module software, will ensure that you always deliver the most efficient toolpaths possible. The integration also ensures that the modifications to the toolpaths are traceable and reproducible for future use.
Toolpath Analysis
Understanding your toolpath can take many forms. It ultimately depends on the kind of problem a user is looking to solve. There are multiple factors that need to be taken into account, including, but not limited to, cycle time, tool wear, machine spindle wear, chip removal and part flatness. The integration between NX CAM and Production Module allows the users to conduct engineering analysis at the time of toolpath creation to ensure that the NC program created is the most efficient one, given the constraints the machine tool, the cutting tool and the part geometry present (Fig. 1).

For example, the NC programmer can identify potential tool deflection problems at the time of toolpath creation (Fig. 2). Tool deflection is a function of the cutter geometry and the rough stock being machined at any given instance.

Such kinds of problems are difficult to anticipate without the detailed toolpath analysis. For the detailed toolpath analysis, it is essential to understand the tool and workpiece engagement for every rotation of the tool. For certain part quality problems, the user may need data at every degree of rotation. The integration between NX CAM and Production Module makes this analysis possible. NX CAM dynamically calculates the work In-Process Workpiece (IPW) using the toolpath, tool geometry and the process conditions for every operation. Production Module takes these inputs and provides information about directional force components, temperature, linear pressure, engagement angle and more.
The Science Behind the Analysis
To effectively make the trade-off between cycle time and tool life while maintaining part quality, understanding of the material being machined is critical. The pressure on the tool when turning Inconel at 300 SFM or milling at 3000 SFM is a result of a complex interaction of thermal-softening and strain-hardening as the material is sheared. Material behavior under machining conditions is an inherently non-linear problem. To capture the non-linear response, Third Wave Systems (TWS) uses the first-principles-based material modeling approach (Fig. 3). TWS combines material modeling expertise with its finite-element analysis (FEA) technology, AdvantEdge, to create a material database for a wide variety of cutting conditions.

From a user standpoint, all this complexity is under-the-hood. The user just needs to select the material from one of the 140+ experimentally validated material models. These material models are essential for the toolpath analysis software, Production Module, to provide outputs including forces, linear pressure and temperature to analyze the toolpaths comprehensively (Fig. 4).

Making Toolpath Analysis Part of the Workflow
While the analysis is sophisticated, it has to be made available to users in a manner that generating efficient toolpaths is simple. To enable this, NX CAM provides some of the most robust toolpath strategies right out of the box. The user needs to select the optimal strategy for a given application, considering the part geometry, machine tool and cutting tools combination. Production Module can help make such decisions.
For example, the table below compares three different types of roughing strategies using two different types of cutting tools. The charts below each of the toolpath strategies show the spindle power consumption and the chip load variation as a function of time. Users will notice that the High Efficiency Toolpath, based on the Adaptive Milling strategy in NX CAM, shows a smoother spindle power consumption profile than the other two strategies. Interestingly, while the chip load is relatively constant for the conventional toolpath, the variation in the engagement with the workpiece results in an inconsistent power consumption pattern. This indicates a highly variable cutting force throughout the toolpath, resulting in shock on the tool that would lead to lower tool life. The table (Table 1) highlights the differences for each strategy along with the potential for further improvements possible in terms of cycle time savings for the particular roughing operation.

Based on the analysis, the user can choose to optimize the toolpath and these changes are stored in the NX part file. It is critically important that these changes are traceable and reproducible.
Given the closed-loop nature of the integration between NX CAM and Production Module, the updates to the toolpaths are part of the revision-controlled part files (Fig. 5). The seamless integration allows the user to easily exchange the project data between NX CAM and Production Module. The optimized toolpath, along with the optimization parameters, is used in NX CAM for post processing and verification. The validated CNC programs are then transferred and used in production.
The users can reproduce, review and edit the toolpath as needed, whether it’s the next day or month or years in the future. The changes to the toolpath can also be reverted easily with the toolpath regeneration feature in NX CAM, providing the necessary flexibility to NC programmers.
This high level of integration, enabled by the NX’s open architecture and advanced APIs, allows a highly efficient workflow. It helps manufacturers to run optimized CAD-CAM-CNC processes tailored for their applications by integrating NX CAM with specialized solutions, such as TWS’ Production Module.

Use Cases
The integration between NX CAM and Production Module enables users to take advantage of the advanced technologies. Some of these experiences are summarized below –
Femoral Machining – Spiral Toolpath for better surface finish and reduced cycle time
In the case of femoral machining, NX CAM’s helical machining toolpath provided an average 24% cycle time reduction for the stem machining across parts of different sizes in a part family (Fig. 6). In addition, the optimized toolpath showed an improved surface finish from an Ra of 0.66 microns to an Ra of 0.56 microns.

The primary determinant to select this toolpath strategy was the observed reduction in the tangential force (in blue in Fig. 7) for the helical toolpath as opposed to the original toolpath that used the Z-Level Profile toolpath strategy. The resultant cycle time savings helped achieve cost savings of over half a million dollars.

Rotating Air Seals – Reduced pressure on the tool for improved diameter runout
For the rotating air seals made from nickel-based alloy components, a bottleneck operation was targeted for analysis to reduce Work-in-Process and improve inventory turns.
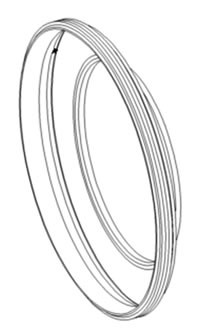
The rotating air seal is a large thin-walled component. The load per unit length (or linear pressure in Fig. 8) was the key parameter for the analysis to make sure that there is no sudden change in pressure on the tool, even though the total forces may be low. In addition, the reduced radial forces helped in improving adherence to diameter runout specification.

Engine Block Machining – Improving Part Flatness
For an engine block machining case, the user was looking to reduce cycle time and improve tool life. CMM reports identified a consistently low spot when analyzing the surface flatness on the bottom of the block. Upon reviewing the number of teeth in cut and Z force in Production Module at the low spot identified in the CMM report, it was found that there was a significant fluctuation in Z force (Fig. 9). Using the results in Production Module, the user offset the toolpath in NX CAM to balance the cutter to limit the side-to-side deflection of the cutter. Through adjusting the cutter path and load leveling the forces, the user achieved a 26% improvement on surface flatness after optimization. The improvement in surface flatness allowed for extended tool life while still achieving a 10 second cycle time reduction.

Blisk Milling – Studying chip load to improve tool life
For the titanium blisk machining, the application required an inserted milling blade for the rough milling process. Unscheduled tool changes were causing severe disruption in the production schedule. Production Module analysis revealed a significant fluctuation in the cutting forces. Based on this analysis, a conservative approach was chosen with a focus on improving tool life. The tangential force constraint value was chosen such that the peak cutting force value was reduced by more than 30% without increasing the overall cycle time. The changes made resulted in improved tool life of 2 times.

Conclusion
These examples illustrate the importance of analyzing toolpaths to identify problems that can disrupt manufacturing processes even before a part is introduced in the production environment. NX CAM is a powerful solution for CNC programming, providing flexibility and a multitude of options to create efficient toolpaths. Production Module offers a detailed analysis of specific choices the users make for their toolpath strategies, cutting tools and machine tool combinations based on its deep understanding of material behavior under machining conditions. The closed-loop integration between NX CAM and Production Module allows manufacturers to seamlessly perform analysis and achieve an optimal balance between cycle time, tool life and part quality.
Workshop Demo
The integration with NX CAM makes the toolpath analysis part of the production process. To learn more, register and attend the web-based workshop that will highlight the importance of this integration to analyze toolpaths and identify problems and fix them before they become an issue in production. Toolpath analysis using Production Module can be a vital tool in your toolkit to uncover and address problems to ensure a smooth production restart. The integration of Production Module and NX CAM helps our users in getting the first part right when production comes back online, reduces costs and provides ROI with first implementations.
About the Author
Nishant Saini is a Product Manager at Third Wave Systems, overseeing the commercial products roadmap and marketing at the company. He has been passionately involved in machining technology deployment on production floors in automotive, aerospace and cutting tool industries for over 15 years. He has an undergraduate degree in Mechanical Engineering, an M.S. in Manufacturing Systems Engineering from University of Wisconsin-Madison in addition to his MBA in General Management.