The Digital Machine Shop: Making an Idea Go Airborne
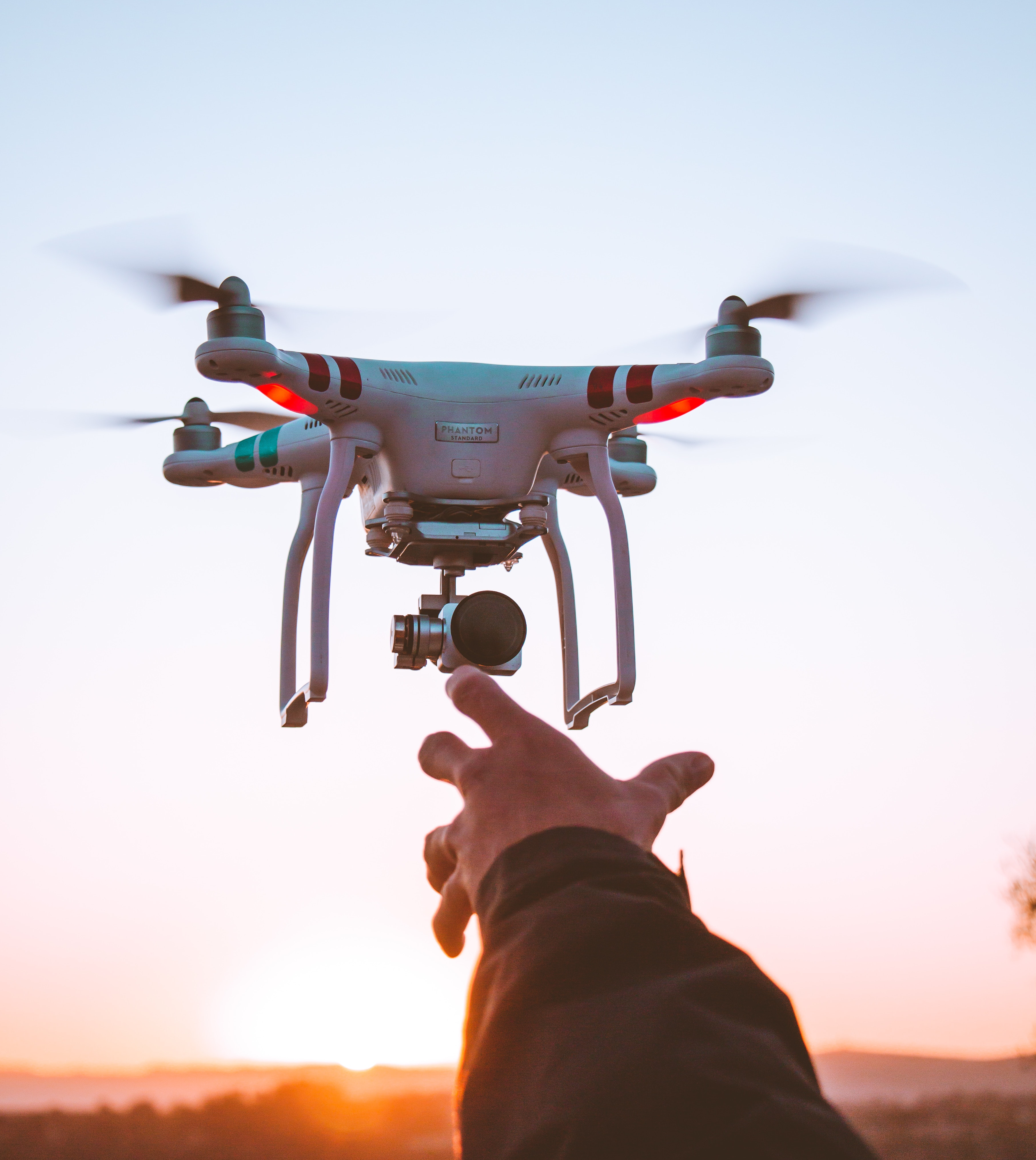
Welcome to a new weekly blog series designed to show you how the concept of a Digital Machine Shop plays out in real life.
I’m Armin Gruenewald, Vice President of Strategy & Portfolio Management at Siemens Digital Industries Software, and I’m here to kick off this series, which follows the creation of a quadcopter mold set as a way of illustrating how a Digital Machine Shop works and why it’s superior to other product development approaches. The following blog posts will be written by Siemens domain experts, starting with mold design and ending up at the shop floor.
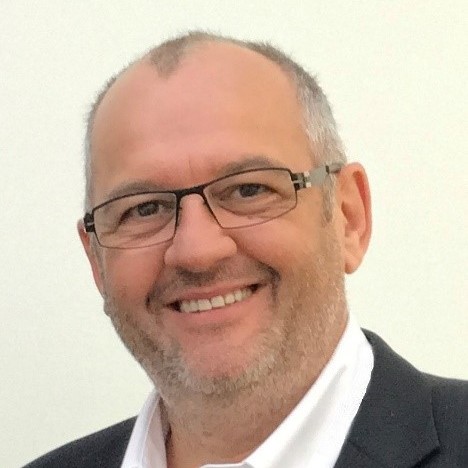
The foundation of a Digital Machine Shop rests on Siemens software technologies that automate every step of the product development process. While these technologies are all powerful in their own right, the beauty of the Digital Machine Shop approach lies in their seamless integration.
Specifically, we’ll be looking at the top cover of a quadcopter. This is a lightweight plastic part with a somewhat complex shape. It will be mass produced using injection molding, a process by which a liquid material – a polymer in this case but it could be something else like metal or glass – is injected into a hollow metal block (the mold), allowed to cool and harden, and then ejected from the mold. The process can take seconds to minutes, depending on the cooling properties of the polymer.
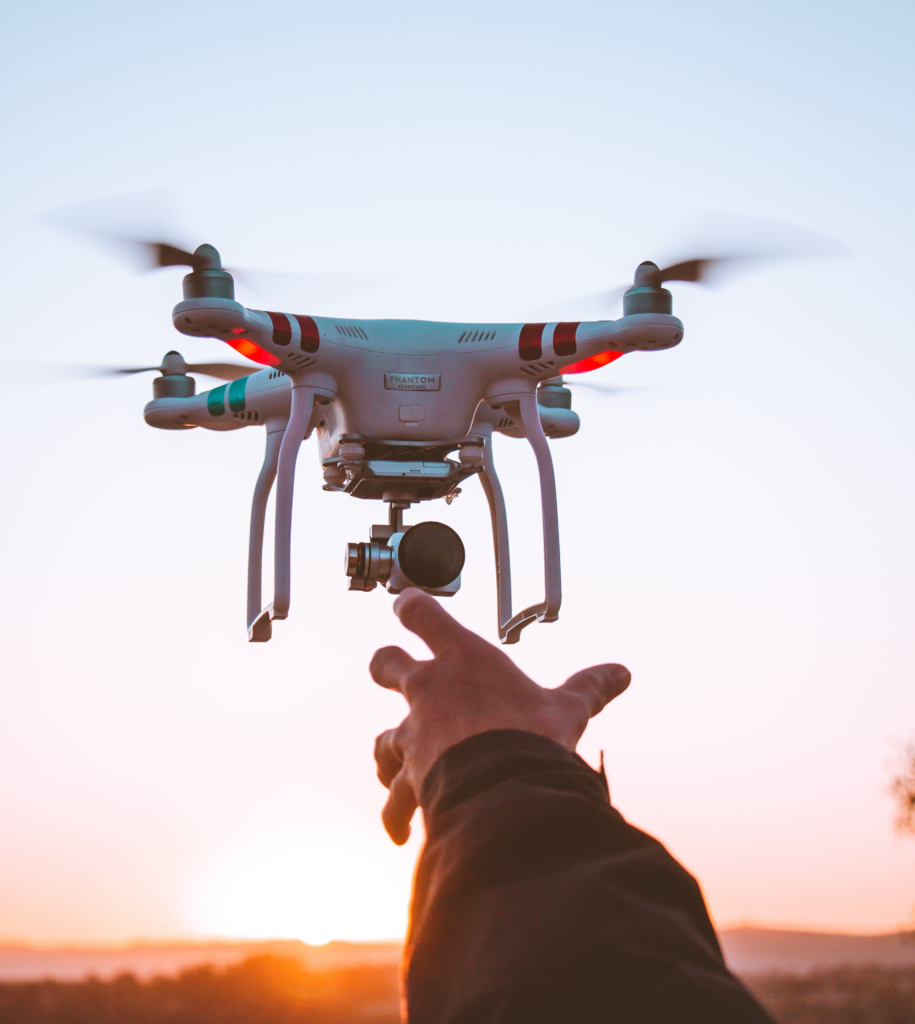
A lot goes into the making of a plastic part such as the quadcopter cover. Crucial decisions and trade-offs must be made at each step of the process, from the design of the part itself, to the design of the mold, to CNC programming, machining, additive manufacturing, and quality inspection. We’ll go through that process end-to-end, and along the way, I’ll point out the benefits of this level of integration, which include:
- Shorter product development times/shorter time-to-market
- Increased flexibility that permits cost-effective product individualization
- A higher level of quality
- Improvements in efficiency that conserve resources and help protect the environment
Anyone involved in product development knows about the decisions and trade-offs that get made along the way. Ideally, at each decision point, you chose the best option, with the end result being an optimized product and production process. To put it most simply, that is what Siemens technologies allow you to do.
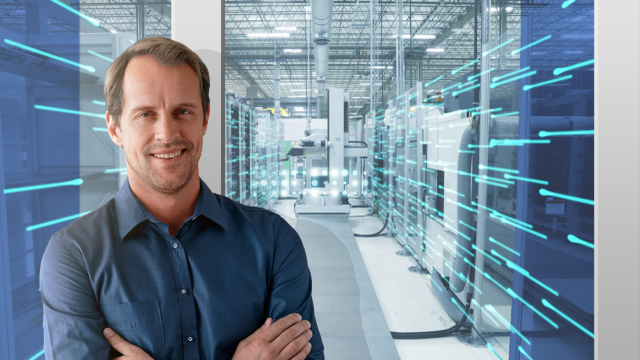
The executive’s guide to digital manufacturing
Check out our free digital machine shop eBook to learn how you can transform your business with digital manufacturing and help your machine shop thrive!
The key is the creation of digital replicas – virtual doubles of products, machines, processes, and even complete production facilities. We call these digital replicas: Digital Twins. The beauty of Digital Twins is that they can be optimized in software where you can try out multiple options quickly. You’ll see examples of this kind of optimization in the upcoming posts, in both the design and manufacturing of the quadcopter mold.
I like using a quadcopter as my example because it illustrates another point I want to make about today’s Digital Machine Shop – that it is accessible to manufacturers of all sizes. As the cost of these powerful solutions has come down, the maker of a relatively niche product like a quadcopter can implement a Digital Machine Shop as effectively as any larger manufacturer can.
In this weekly blog series, we’ll include videos of the quadcopter mold design, manufacturing, and quality inspection process, along with links to a wealth of other content that you may find helpful. By the end, I hope you will have a good understanding of modern solutions for part manufacturing, and more importantly, you’ll be excited about the enormous benefits made possible by a Digital Machine Shop.
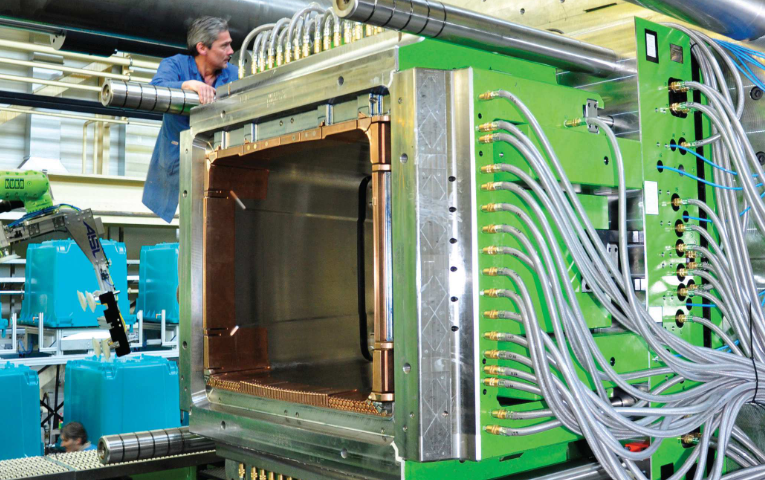
Haidlmair – Digitalized mold making fuels growth
Read the customer success story on Haidlmair, an injection molding tool maker who is saving time, enhancing quality and eliminating errors with Siemens software.
Digital Machine Shop Blog Series
Check out all the blogs in our digital machine shop series featuring the creation of a quadcopter and published weekly!
Comments
Leave a Reply
You must be logged in to post a comment.
Closing the loop between the virtual and real worlds of production.
Proud to be part of this process 🙂