The Misnomer of Feature-Based Machining
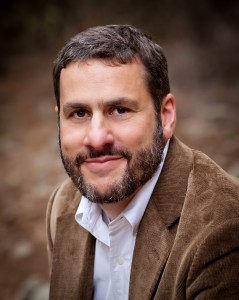
This blog post has been licensed for hosting by Siemens PLM. The concepts, ideas and positions of this post have been developed independently by Industry Analyst Chad Jackson of Lifecycle Insights. © LC Insights LLC
Ever heard of COFES, which stands for Congress on the Future of Engineering Software? Its an event out in Phoenix AZ held by Cyon Research that aims to bring together folks that are media, industry analyst, software provider and users to talk about where computer aided technology is heading.
This last year, I led a session that discussed what implications, if any, came out of the recent rash of acquisitions in the CAM space. But interestingly enough, we instead got into a discussion that focused instead on what innovations have occurred, if any at all, in the CAM industry recent years.
Coming out of that meeting, i have to admit that one of the most impressive advances in CAM in recent history is something called feature-based machining, although it isn’t exactly what it sounds like.
The Misnomer: What Its Not…
In the CAD industry, we all know what features are, right? They are specific tips of additive or subtractive operations that create geometry in 3D models. There are extrusions and protrusions, cuts and holes as well as rounds and chamfers. Furthermore, traditionally CAD software has sequenced these options into a history that is remembered. Parametric changes made through dimensions that control these features ripple through that history to drive intelligent change.
So is feature-based machining related to that? Well, not really. And that’s unfortunate, because so many of the words we use in our industry, like features for example, are loaded terms. They give people the wrong idea. So let me explain what this technology does in this case.
It’s Really Geometry-Based Machining
Basically, the technology works like this. A user designates a certain area of a part or component needs to be machined. The CAM application then analyzes the geometry in the designated region and sequences together a series of NC tool paths that are optimized to produce that result.
What’s interesting here is how this optimizations works. If you’ve ever used CAM software before, I’m sure you’re familiar with the progression of NC sequences to machine a part. You start with roughing tool paths, then you progress to finishing tool paths. Why? Well, that’s actually how you progress in cutting the metal in the real world. We’re wired that way.
This optimization, however, actually works in reverse. It extracts information from the 3D model and figures out the right finishing tool paths first. Then it actually determines what roughing passes are required to get the rest of the material out of the way.
So really, its more like geometry-based machining. But maybe I’m nitpicking.
Why is it important?
OK. So why is this a big deal? Well, there’s two reasons.
The first reason is all about the best use of a machinist’s time. Let’s be honest, there are some terribly mundane machine programming tasks out there. Mind-numbingly mundane. Drilling, tapping and threading a hundred holes in a plate isn’t mentally demanding, career fulfilling or terribly complex. Yet it has to be done. This technology can knock out such a job very quickly and let machinists focus on the jobs that demand their full attention, which are more enjoyable and challenging anyway.
The second reason is about machine utilization. Organizations nowadays are always trying to maximize the utilization rates of their machines, which represent a huge capital investment for most companies. The more parts that are machined equates to more products that can be assembled and sold or delivered to customers. Both equate to revenue that is realized. And that in turn accelerates the return on investment for the capital expense for the machine. Feature-based machining produces good NC code quickly and accurately. And as a result, its a faster way to get tool paths to those machines on the shop floor.
Summary and Questions
Let’s recap.
- Feature-based machining is somewhat of a misnomer. It has nothing to do with the features created in the sequenced used to generate the geometry of a 3D model.
- It should be described as geometry-based machining because it automatically creates a series of NC tool paths to machine out a region of a 3D model by assessing the included geometry.
- This is a good technology for automatically creating NC tool paths for mundane and highly repetitive work, freeing up machinists for more complex tasks.
- This is also good for maximizing machine utilization, because it offers a way to get good NC tool paths to the machines very quickly.
- What are your thoughts? Have you leveraged feature-based machining as of yet? What have your experiences been?
Take care. Talk soon. And thanks for reading.
About the Author
Chad Jackson is the President and Principal Analyst of Lifecycle Insights, a research and advisory firm that assesses the business impact of software applications and systems on engineering organizations. Chad has more than 15 years of experience with CAD, CAE, PDM, PLM and related technologies as part of the analyst community and software industry. Due to his industry knowledge and thought leadership, Chad is a sought-after expert, author and speaker that has advised, published and presented dozens of times domestically and internationally.