What’s New in NX for Manufacturing (December 2021)
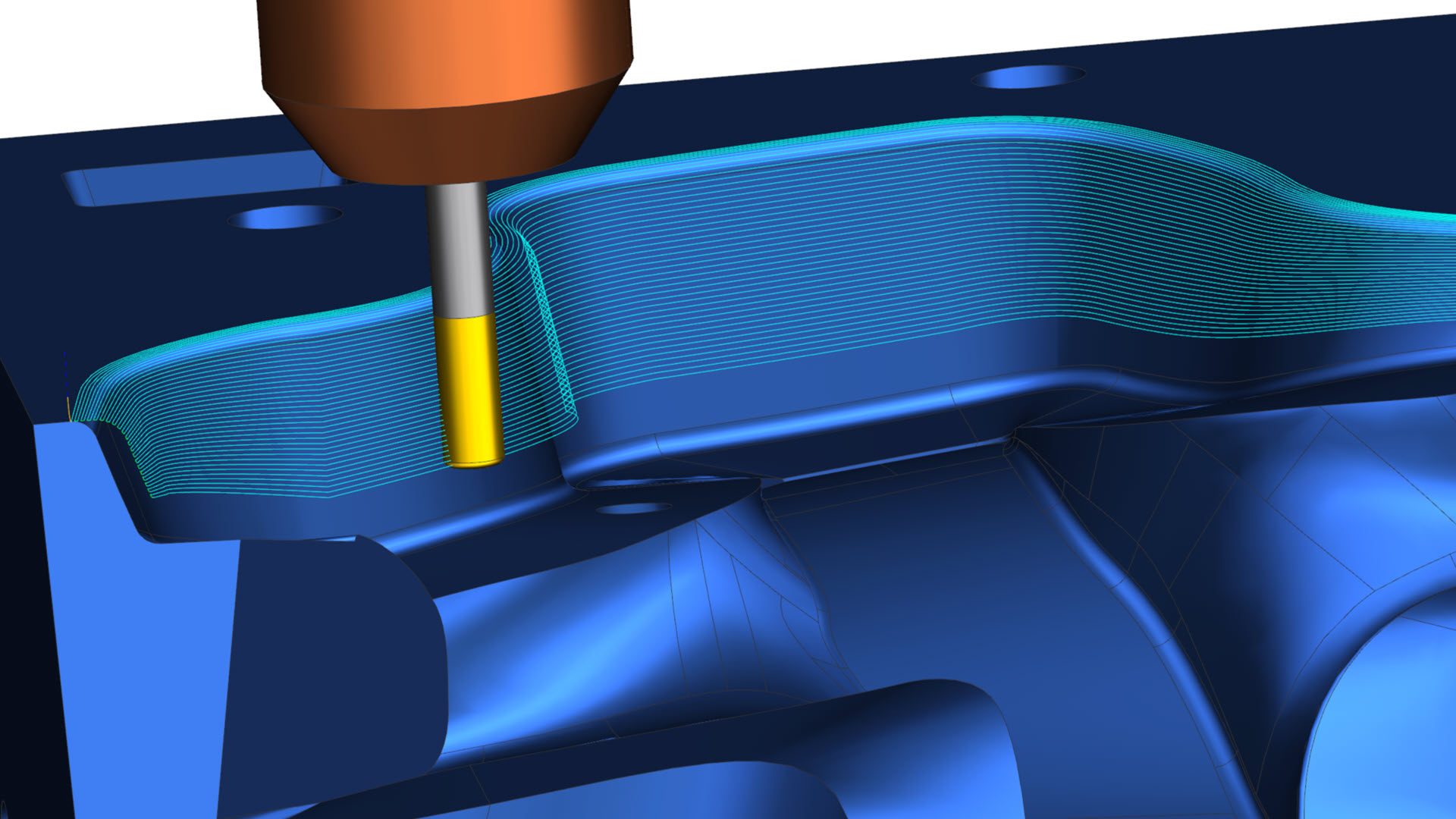
The holiday season is upon us, and this year we’re gifting a new release of NX for Manufacturing! With the newest release of NX for Manufacturing (Dec 2021) comes powerful new capabilities that enable companies to boost production efficiency, both in planning and on the shop floor.
This blog highlights the intricacies of the newest functionalities in NX for Manufacturing, including those in:
- NX CAM
- NX Additive Manufacturing
- Manufacturing Process and Data Management
- NX CMM Inspection Programming
- NX Assembly Line Planner
- NX Line Designer
- Supporting Xcelerator Share
NX CAM
The new AI-powered NC programming capability streamlines the creation of machining processes. NX CAM can now predict and suggest the next programming step based on the current machining application and your workflow patterns. This innovative AI technology helps you accelerate and standardize the programming process, reducing time to market.
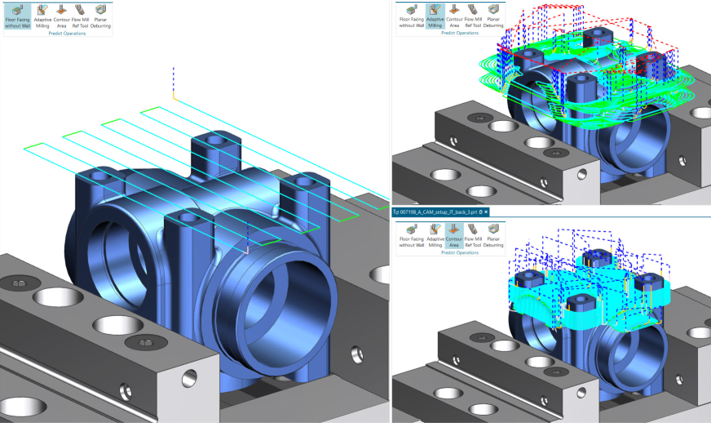
The new Z-level Undercut machining method requires minimum input to program hard-to-reach, undercut part regions. In just a few clicks, you can now create high-quality collision-free toolpaths using T-cutter, spherical or barrel tools. By eliminating manual input and the creation of additional drive geometry and projection definition, the Z-level Undercut method results in 5 times faster programming.
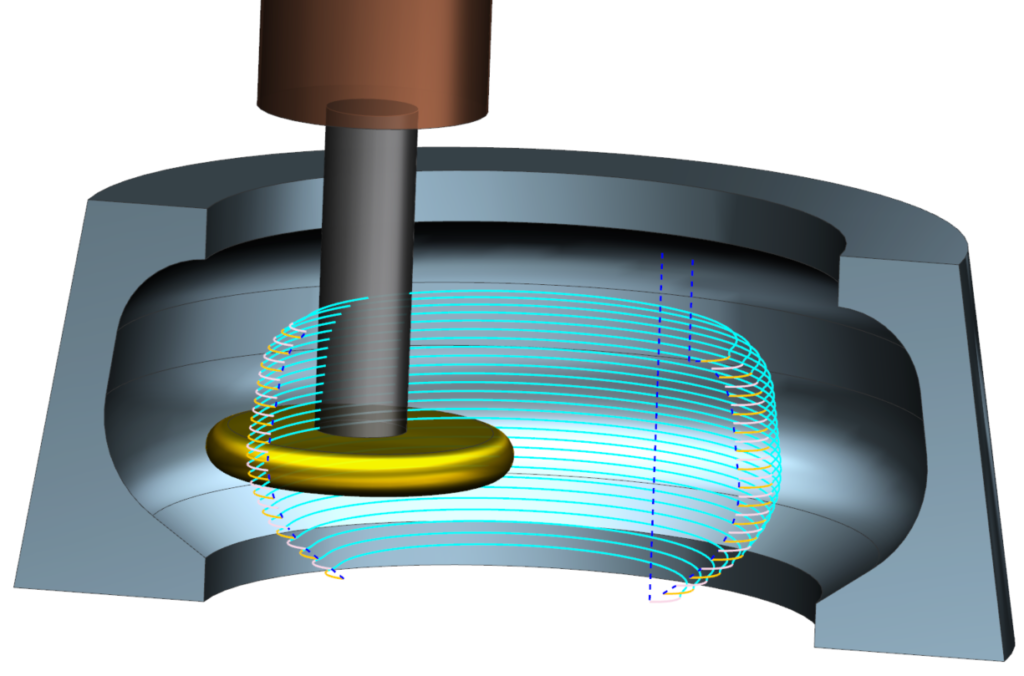
The Flow Milling operation has replaced the Flow Cut operation for a new, advanced rest machining operation. The legacy Flow Cut operations, such as Single, Multiple and Ref Tool Flow Cut, can be automatically migrated to the new Flow Milling, enabling you to immediately leverage the benefits of this new advanced operation. The new, robust operation improves toolpath’s reliability and consistency, enabling precise toolpaths to remove the uncut material.
With the improved arc fitting, cut area consistency and better uncut material finding in the Flow Milling operation, you can now create accurate and optimized toolpaths for shallow features and sharp corners, which is usually challenging to program using traditional methods.
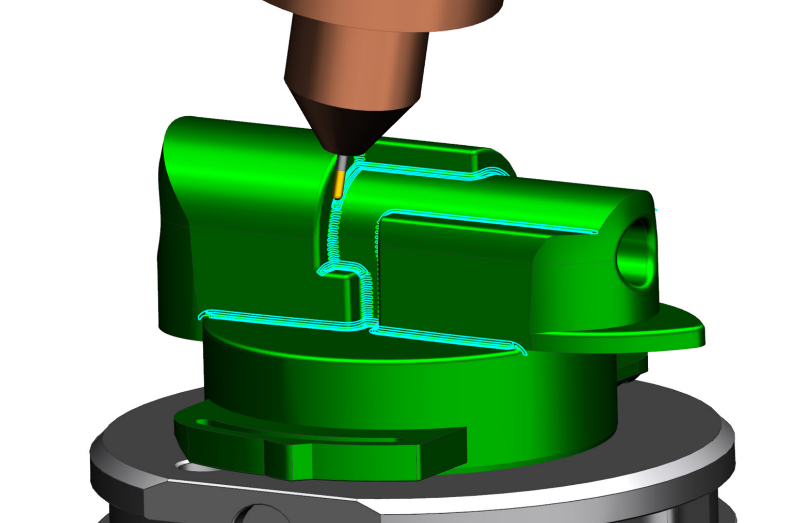
The Planar Deburring operation now allows you to specify the edges that you want to skip when deburring. When NX automatically identifies all the edges, you can easily specify the edges that don’t need to be deburred. This is useful when edges on the CAD part model have different chamfer angles. In these situations, you can select edges to ignore and debur the remaining edges. If needed, the excluded edges can be deburred with another tool in a separate operation, allowing you flexibility to quickly program deburring operations on parts of any complexity.
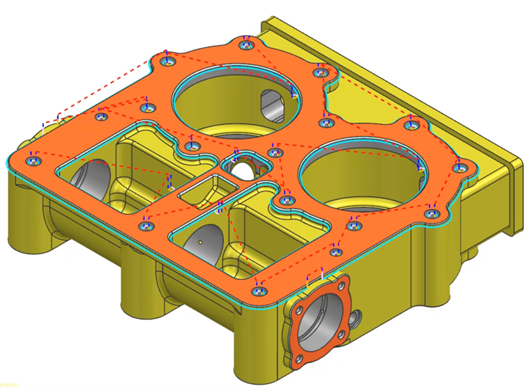
The 3-axis Guiding Curves finishing operation now supports bull nose tools, in addition to ball nose and spherical tools. A bull nose tool is ideal for finishing steep areas, resulting in better surface finish, improved part quality and minimized benchwork. You can quickly create a high-quality finishing tool path that follows the natural shape of the part. The 3-axis Guiding Curves operation can design a full tool path with guide curves with expanded support for the cutting tools.
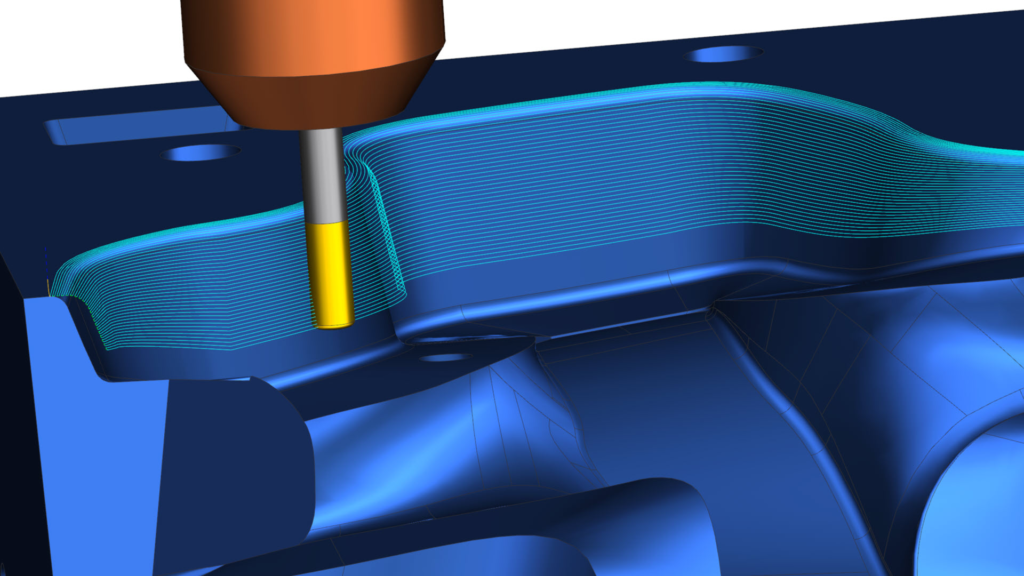
The enhanced Operation Navigator framework provides more flexibility and ease of use. For example, you can now configure the operation navigator for multi-channel machining with clear channel visibility. For each channel, you can filter the view individually, making the programming of multi-function machines much more intuitive.
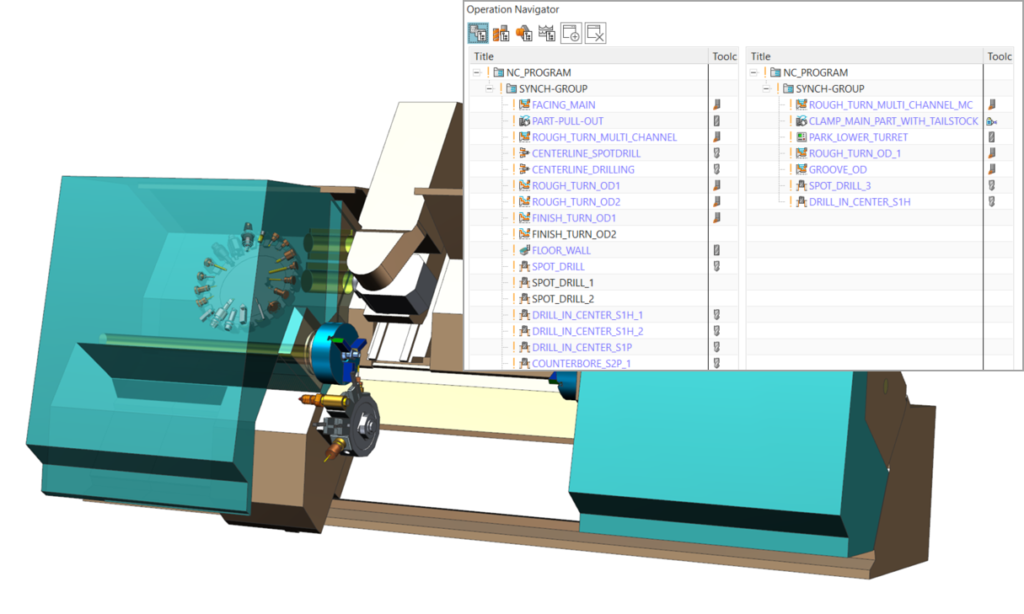
The new Parametric Triangular Thread Insert and Holder Support provides enhanced support for thread turning tools. You can utilize standard triangular and trapezoidal inserts to create thread turning operations with realistic tool representations, enabling faster programming and accurate machining simulation. The parametric definition of the insert and holder supports the user in fitting the dimensions and now follows the ISO standard. For instance, if the nose radius is greater than the Profile Depth Insert (PDPT), the system informs you the value range which can be entered. This ensures error free programming and supports you when defining realistic parameters for the insert.
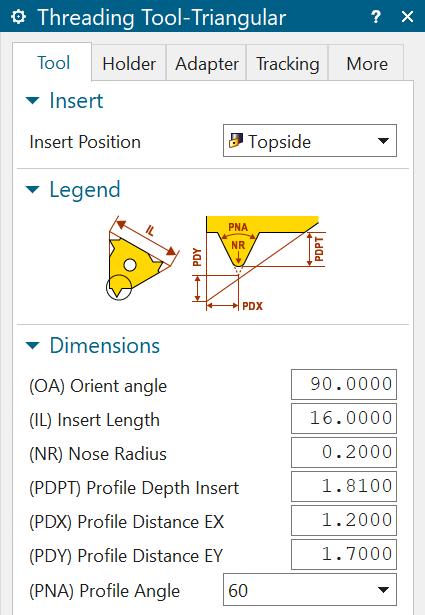
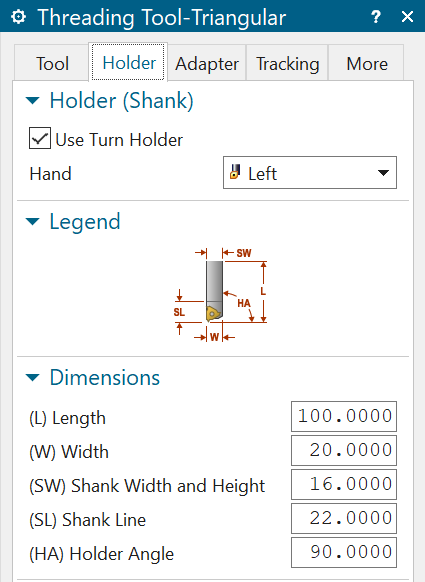
The new Parametric Triangular Thread Insert and Holder Support allows for an improved workflow using an accurate representation of thread tooling tools.
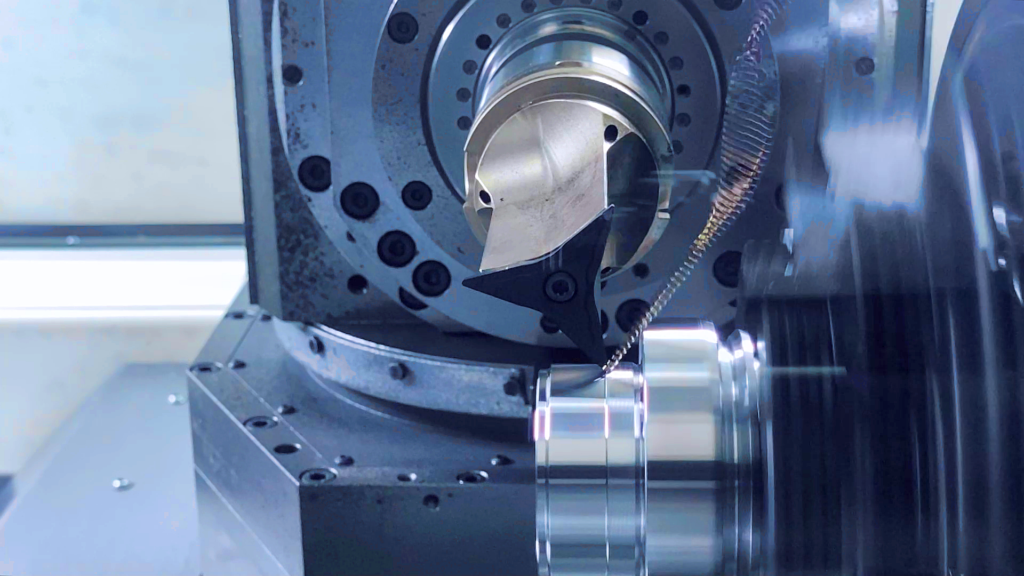
High-dynamic turning webinar
Learn how modern CAD/CAM/CNC technologies, like high-dynamic turning, can help your machine shop stay competitive.
Smart Machine Kit Solution (SMKS) is a modern approach for NX CAM users to accurately validate and generate production-ready NC programs. SMKS, also known as digital twins of the CNC machine tools, are available on Post Hub, NX CAM’s cloud-based postprocessing platform with more than 1,200 kits. Each SMKS includes the accurate model of the machine with kinematics, postprocessor, and G-code-driven simulation.
You can now purchase an SMKS license for different types of machining operations (such as 2-axis Turning and 3-axis Milling), enabling you to install the available kits from Post Hub. For example, having the SMKS 3-Axis Milling license allows you to download and install any 3-axis milling kit for different machine tools, such as HAAS, DMG MORI and Makino directly from NX CAM. In this case, you can install unlimited number of 3-axis milling SMKS from Post Hub.
As an additional benefit, you can also try any SMKS to a single operation without a license. With the new SMKS approach, NX CAM users gain additional flexibility to easily program a wide range of CNC machine tools.
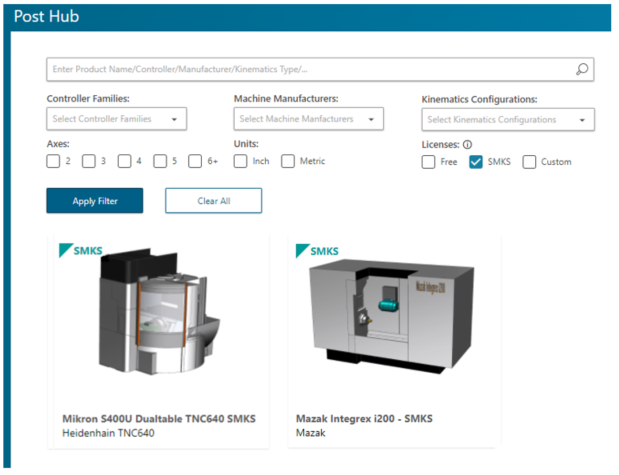
NX Additive Manufacturing
This release of NX continues the trend of applying automation to additive manufacturing. The new capabilities for automating the population of the build tray, including Part Orientation Optimization, equate to gains in efficiency when printing parts at industrial scales.
Being able to copy parts and the associated supports within the build tray and the ability to nest parts across multiple build trays streamline the build setup process. Additionally, integrated orientation optimization runs dozens of simulations simultaneously in the cloud to find the optimal build orientation for reduced distortion.
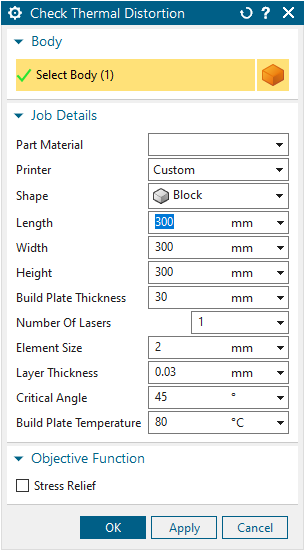
The new Morphing pattern can be used to create an interpolated infill morphing pattern between at least two objects. The Morphing of the infill pattern allows for smoother output with fewer corners, resulting in fewer voids created within the printed body. Multiple input curves or drive surfaces are supported, and both curves and drives can be used as drive objects.
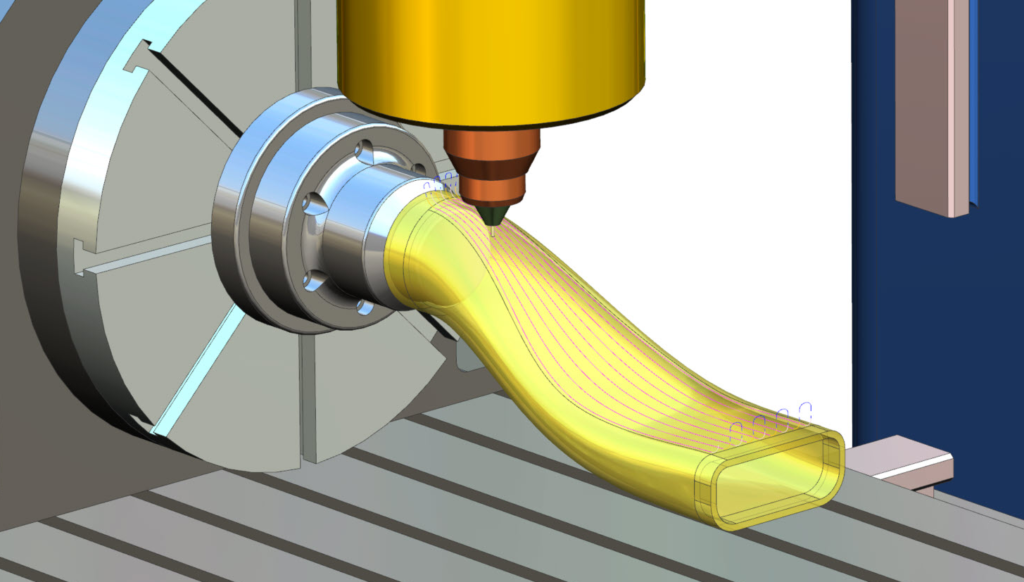
With 3D Freeform Gradient Buildup, you can mix two different metals during the build process, specifying the percentage and level for each metal. With full control of 3D Freeform toll axis, the gradient buildup allows you to have customized material properties from top to bottom of your build.
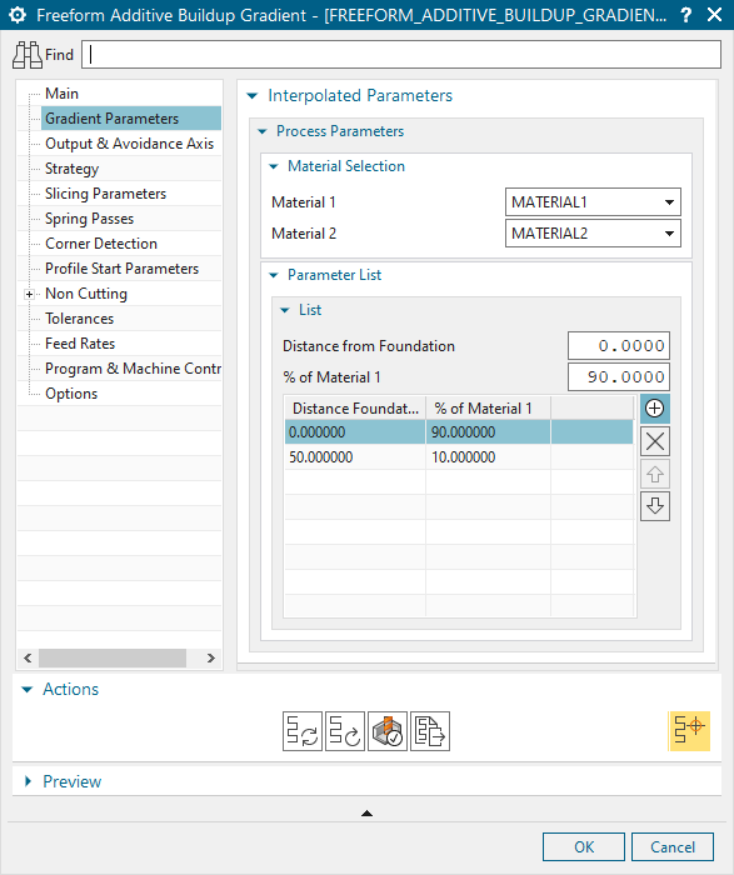
The Print Driver for EOS provides the ability to off-load print jobs to the new AM Print Server. The built-in capability is for complete layer and stack representation and allows for a selection from multiple build strategies. There are also several output formats, including *.openjz and *.task.
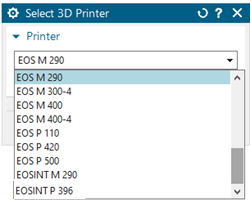
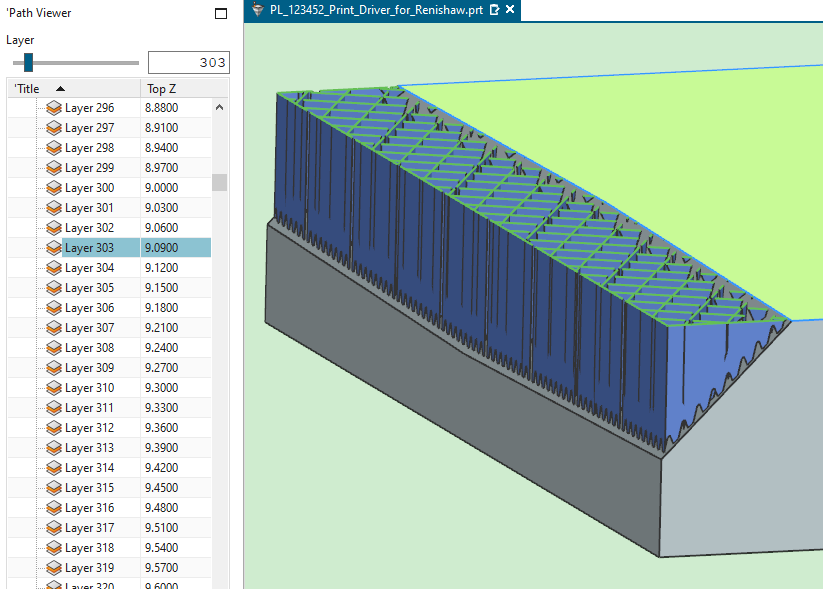
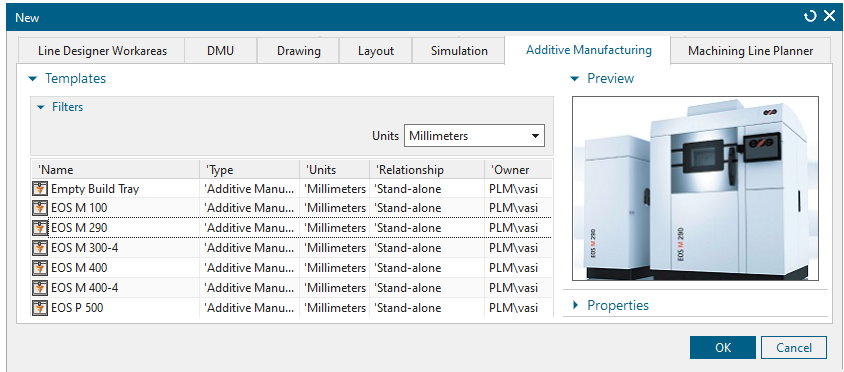
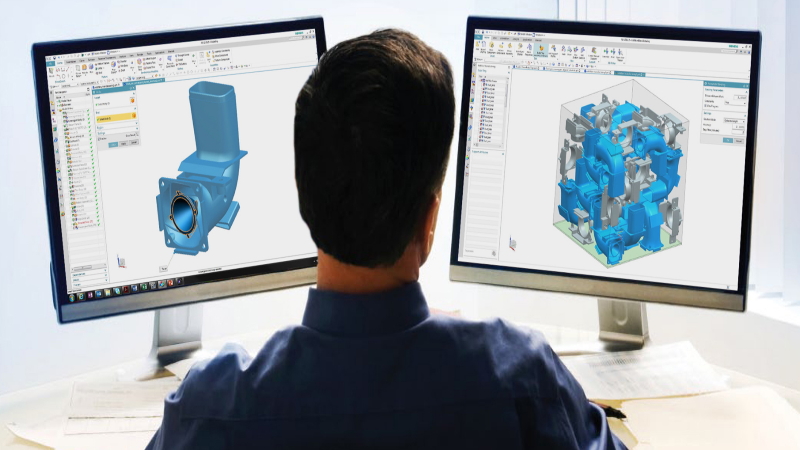
Industrial 3D printing webinar
Learn how to make your machine shop more competitive using industrial 3D printing from Siemens and HP.
Manufacturing Process and Data Management
Manually creating a tool assembly in NX CAM with the needed parameters can be a time consuming and cumbersome task. You need to design the tool and holder, set the tool mount junctions, identify cutting/non-cutting geometry, and manually create the parametric holder representation.
Using the seamless integration between NX and Teamcenter, you can quickly create the NX tool assembly part file from the tools stored in the Manufacturing Resource Library (MRL). The entire process is automated – the system analyzes the tool geometry, recognizes the tool parameters, and specifies the cutting and non-cutting geometry. All the needed parameters, such as tool and tool holder parameters, are included in the tool assembly, allowing for direct use in NX CAM without modifications.
With this new functionality, the time needed to prepare a tool assembly is significantly reduced, enabling fast and efficient programming. Additionally, you can leverage the accurate digital models of tool assemblies to perform a realistic machining simulation in NX, ensuring error-free production.
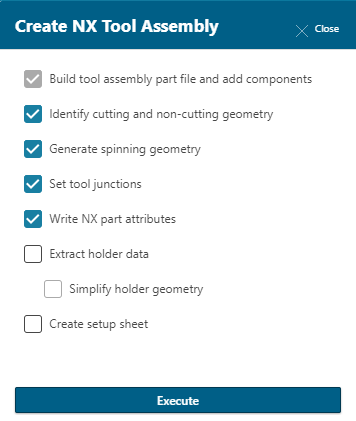
NX CMM Inspection Programming
NX CMM Inspection Programming has an improved user experience for the use of CMM in CAM. The new NX Metrology allows for the creation of full CMM programs in the machining environment. The new dialog creates one operation, combining the inspection, tolerance and path features that were previously three or more unique operations in NX CMM. In the new Metrology, the CMM Probing dialog automatically creates all the necessary CMM content, such as the selection of Product and Manufacturing Information (PMI) or a geometric element, with just one click.
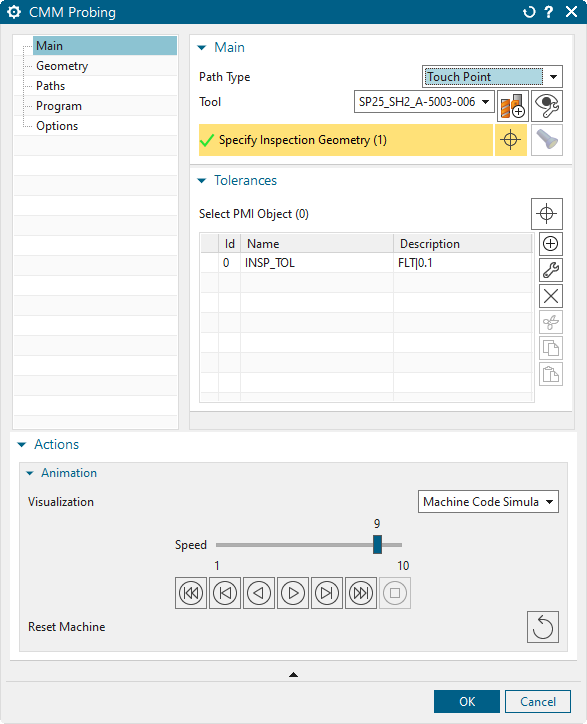
NX Assembly Line Planner
NX Assembly Line Planner now supports the use of Operation Groups. Grouping operations under a station by variants or a different logical differentiator can help define the process inside of a station, while also providing a simplified overview of the main steps. Operation Groups are a typical use case in mixed production lines and allow for the management of the process flow in the station between groups and/or operations. This support is available both for the creation of new groups within Assembly Line Planner and legacy data created in other applications, such as in the Rich Client.
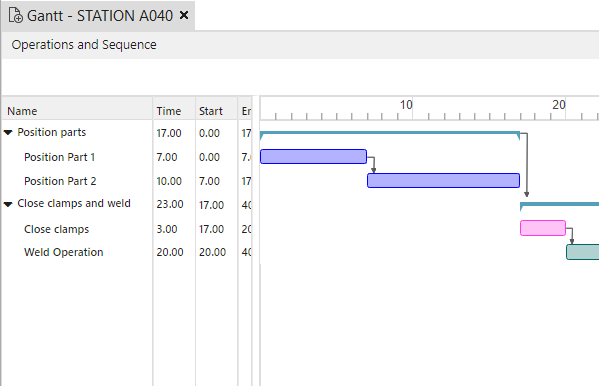
The New Workarea command in NX Assembly Line Planner allows you to create any new structure node quickly and easily in the plant. For example, this function can be used to create a new area inside of a line, which itself will contain several stations. To create several stations at once, you can keep the window open and simply provide the required names to avoid unnecessary changes of view. This simplifies the line planning scenarios by hiding the complexity of the data model while providing a quick way to perform the required planning tasks at the same time.
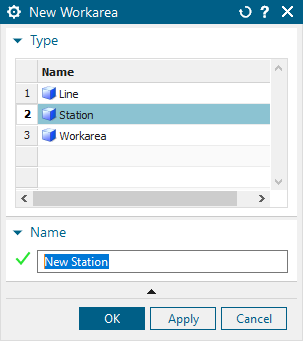
NX Line Designer
More than 150 Parametric Resources have been added to the Resource Library, resulting in over 500 resources that you can create with. For standard resources, Part Families are used over Product Template Studios (PTS) to promote reuse, also known as instancing. This prevents instances where the same resource is used multiple times in the layouts. All relevant resources are added with connectors in order to facilitate drag and drop functionalities to connect components. These resources are available in Imperial and Metrics for both Native and Managed Line Designer modes. Kinematics has been added to the relevant resources, and they contain a set of standard Reference Sets as well. Some resources also contain Plant Simulation Class to ease data exchange with Plant Simulation.
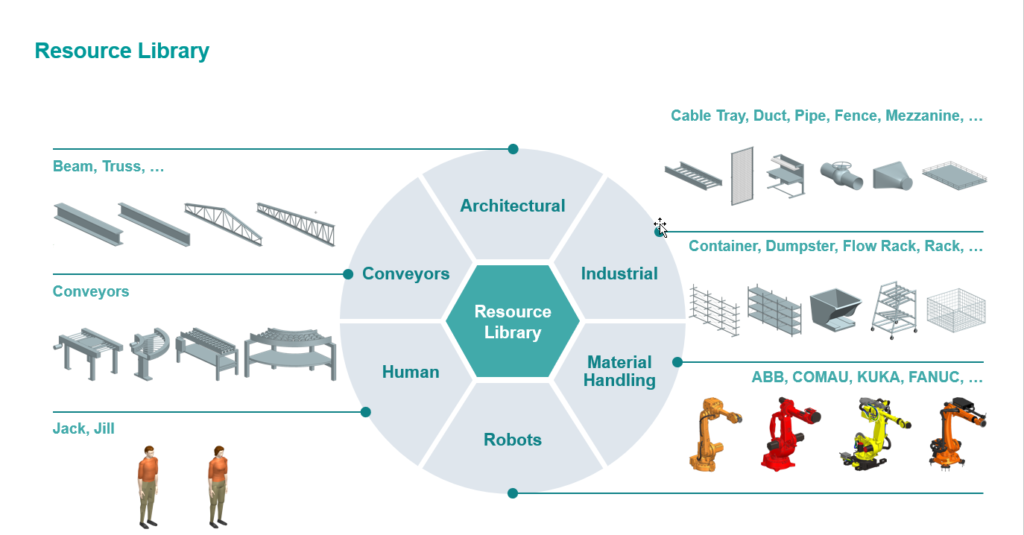
Supporting Xcelerator Share
Xcelerator Share is a cloud-based collaboration service that supports distributed working environments and is available with many Siemens software subscriptions. It is part of the Xcelerator Portfolio and provides:
- Secure cloud storage with desktop syncing
- Permission-based project sharing with task management
- Engineering-centric view & markup
- Any device, any time, browser-based access to data

NX CAM now seamlessly integrates with Xcelerator Share to provide simple, secure and effective collaboration with colleagues, partners and customers.
NX CAM now connects directly to Xcelerator Share, ensuring simple and effective collaboration with secure data access. You can collaborate on part designs and update the machining securely with those on your team as well as suppliers and other external partners.
NX CAM allows you to open necessary part files directly from the cloud. With a single click in NX CAM, you can update the part with all the necessary revisions made by others on the design. Once the part has been updated in the software, you can then generate the updated shop floor instructions including work instructions, NC operations, cutting tool lists, and more.
Learn More
Check out these step-by-step tutorial videos on the new NX for Manufacturing features on our online community.
For more NX information, check out the new release of NX for Design.
Enter our holiday giveaway for a chance to win a free copy of The CNC Handbook to ring in the new year!
Explore NX’s advanced capabilities for NC programming by signing up for the NX CAM cloud-based trial. No installation is required meaning you can run NX in your browser, in just a few minutes. Try it today!
Also make sure to check out this free eBook on how to make manufacturing lead time an asset in your digital machine shop.