What’s new in NX for manufacturing (December 2023)
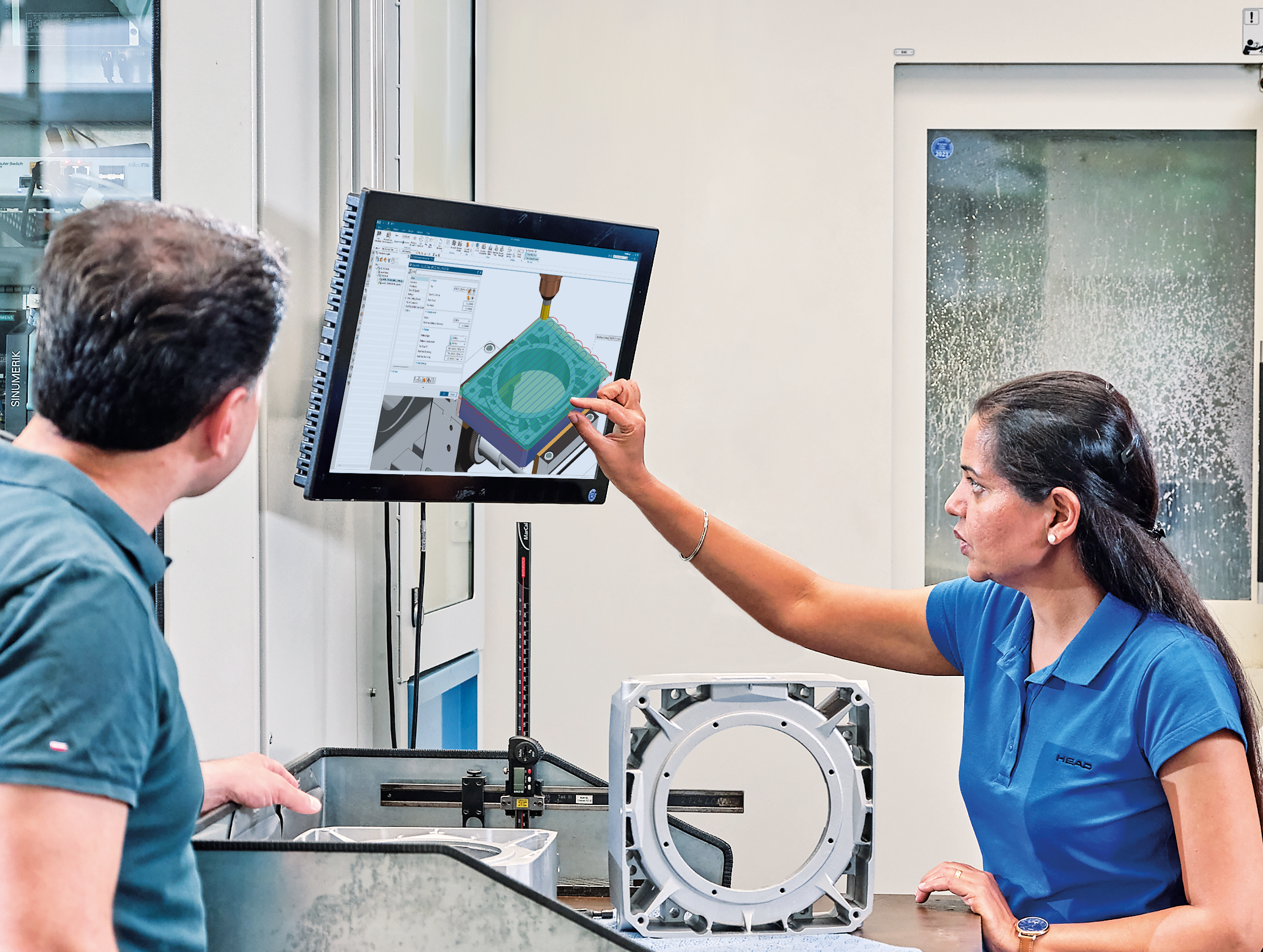
We are excited to announce the latest version of NX for manufacturing With the addition of powerful new capabilities and enhanced functionalities to your part manufacturing solutions, you can achieve higher levels of productivity using the NX software.
In this blog, you will learn about the latest features and product updates for our comprehensive software for part manufacturing including:
- NX CAM
- NX Additive Manufacturing
- NX CAM On-Machine Probing
- NX CMM Inspection Programming
- Part Manufacturing Data Management
- NX Line Designer and Fixture Planner
- NX Assembly Line Planner
What’s new in NX CAM
The new Quick Roughing operation in NX CAM software offers a swift and easy-to-program offset roughing process with a user-friendly interface and streamlines the creation of roughing operations with minimal input, saving valuable programming time. It is ideal for programming simpler components, such as prismatic parts and less complex molds, cavities, and cores, dies, castings, and forgings with contoured shapes using planar cut levels. The new roughing method automatically applies the most efficient cutting strategies to different region types, such as open and closed regions. The improved quick roughing feature ensures robust holder collision avoidance while maintaining the right holder clearance values, enhancing not only the safety and reliability of the machining process but also the overall efficiency and quality of the produced parts.

The new Face Milling operation provides modern programming techniques to interactively adjust toolpath parameters, improving your programming efficiency. Face Milling operations have been significantly improved. The new Face Milling operation, featuring zig and zig-zag patterns now makes it easier for users to program face milling toolpaths. The interactive on-screen UI allows users to effortlessly specify path parameters like Cut Angle, Run Off, First Pass Overhang, Blank Thickness, Start Point, and Floor Stock, providing them with automatic toolpath previews and ensuring faster toolpath generation.

The latest Wall Finish Barrel Swarf operation helps you reduce machining time and improve surface finish using advanced settings to generate optimized toolpaths easily. You can now use taper barrels for parts with straight walls and tangent barrels for parts with curved walls. With the newly introduced 5-axis Wall Finish Barrel Swarf operation subtype, you can also swarf deep planar or contoured walls using a 5-axis tool motion with tangent barrel, taper barrel, and standard barrel tools.

The user-friendly and enhanced Holemaking features now make it easy to manage control points during drilling and pilot drilling, especially when working with depths less than the In-Process Workpiece (IPW) stock. The new control point option called “Use initial” ensures the tool consistently positions itself above the Initial Programmed Workpiece (IPW) for each operation, preventing sudden movements into the previously drilled hole.

This results in safer toolpaths with increased control, minimizing the risk of tool breakage and better control for entry into the hole. Users can now choose the clearance depth from the bottom of a hole or boss, reducing the depth a tap or thread mill goes into a threaded feature. This solution gives users complete control over how far the threading tool stops from the bottom of the feature.
With the upgraded Cloud Connect Tool Manager, you can effortlessly generate entire tool assemblies using the dynamic assembly tool preview. With the inclusion of tool holders in the latest release, you can seamlessly create tool assemblies with tool holders and cutting tools. The module supports several search functions for added convenience.
What happens to the existing assembly tools saved in the previous version of the library ? They can be quickly and automatically converted with just a single click.

The latest Mill-Turn Workpiece feature offers a more intuitive and faster creation of advanced mill- turn CAM setups. This enhancement, available for use only when a machine tool is loaded, has reduced the need for additional setup efforts. It achieves this by combining the definitions of Milling and Turning Workpieces into a single geometry object, streamlining the programming process, and simplifying the geometry tree for more user-friendly mill-turn setups.

Your software feedback is extremely valuable to us, That is why we actively incorporate your input. to improve the overall CAM experience by turning your feedback into new features and improvements. Now within NX CAM, you can provide feedback anonymously using a simple survey submission process without difficulty. Share detailed insights, ensuring your input is delivered directly to the NX CAM Product Owner for a thorough review.

Quick Roughing in the latest version of NX CAM is extremely practical for NC programmers. First, it’s simple to use.
Andre Luis , Director, Cadcamnx Worldwide
I can create great roughing operation with just a few clicks. Plus, it’s very fast! Compared to other methods, Quick Roughing can cut the toolpath calculation time by up to 50%.
What’s new in NX Additive Manufacturing
The upcoming version of NX Additive Manufacturing introduces new enhancements in Multi-Axis and Fixed Plane capabilities.
The latest Morph Across operation is supported for back-and-forth and short zig-zag motions, particularly favored for Wire Arc Additive Manufacturing (WAAM) and ring-shaped parts compared to circular racetrack motions. This operation automatically detects a drive curve, produces output across that curve, and allows for splits to maintain the specified minimum & maximum stepover range.
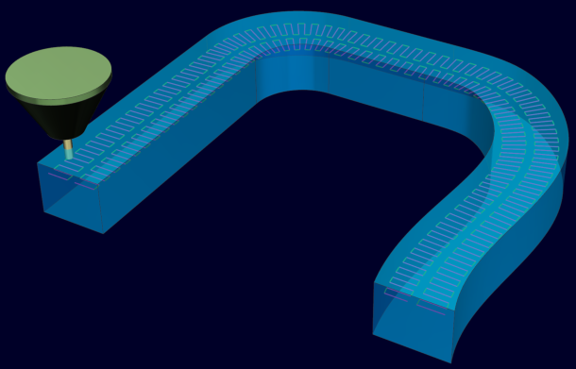
The In-Process Workpiece display per level functionality enhances the user experience in programming multi-axis additive parts. Verify a complete build or identify potential voids by visualizing their additive buildup on each level.
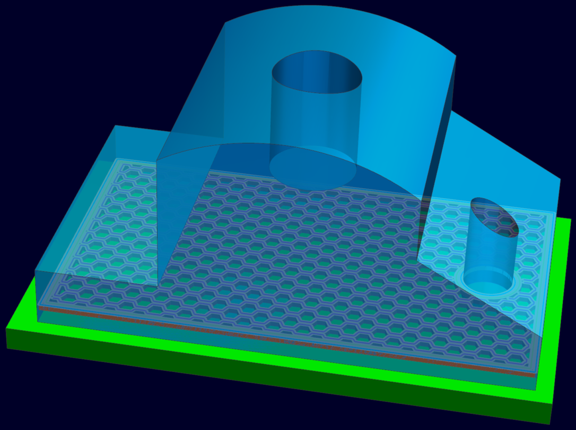
With just a click or a keyword command, users can systematically inspect, and check for voids or other issues across all levels before initiating the printing process. Perform the inspection one level at a time, contributing to an improved programming and user experience.
When it comes to making parts, sometimes a simpler solution in Additive Manufacturing gets the job done just right. For instance, take the situation where companies seek to retrofit an existing CNC machine with a print head; in such cases, a simpler and more economically viable solution becomes necessary. In response to these specific needs, we introduce Fixed-Axis Additive Manufacturing — a tailored solution designed explicitly for fixed-axis operations and smaller NC files. Notably, it now boasts a more accessible price point while retaining essential additive manufacturing capabilities. The solution offers a simplified interface, reducing tool axis options, to further streamline the programming process. Additionally, the generated NC files are shorter.
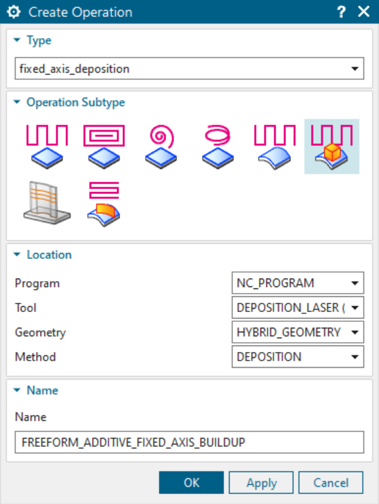
This new solution specifically caters to less intricate parts, focusing solely on the 3-axis functionality. It presents a cost-effective way to implement additive manufacturing, providing core functionalities needed to address a wide range of applications.
It is now easier to add a build tray containing a single part to another build tray. By employing part occurrences as associative references, data seamlessly transfers from the production build tray to the part data in the development build tray. This eliminates the need for duplicating initial build preparation data in the production build tray, resulting in a substantial 95% performance improvement. Additionally, any modifications made in the development tray are automatically propagated to the production build tray through the Synchronize command.
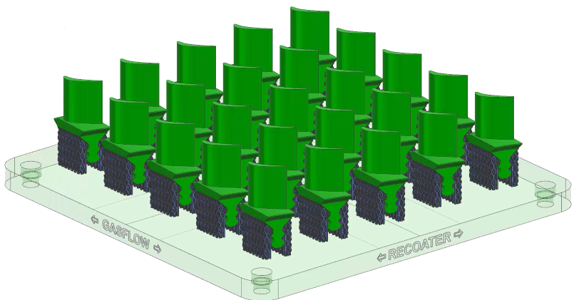
Other enhancements for fixed axis additive include in-line angled supports, repositioning parts using bounding box that contribute to a streamlined process, reducing the time needed for positioning and orienting parts.

The creation of supports becomes even more user-friendly with the help of in-line angled supports, enhancing the overall user experience.
What’s new in part manufacturing data management
Teamcenter’s manufacturing data management capabilities enable seamless connectivity between people, systems, and machines through a digital thread spanning across your organization and plants.
Users can now save time, enhance productivity and experience streamlined collaboration via Active Workspaces, gaining direct access to commands and functions essential for daily tasks.
In the Recent and Discussions tabs, explore quick access to the recently used objects and an overview of ongoing discussions with your colleagues. In the Recent tab, view objects in progress for swift access to important tasks. Meanwhile, the Discussions tab offers an overview of parts collaboratively worked on with colleagues, allowing you to share comments and suggested changes across your organization.

The Teamcenter web user interface in Active Workspace now allows you to effortlessly define multitools and prepare these tools for use in the NX CAM environment. Transfer information from related inserts to multitool cutters, streamlining the process and ensuring precise details are accurately applied.
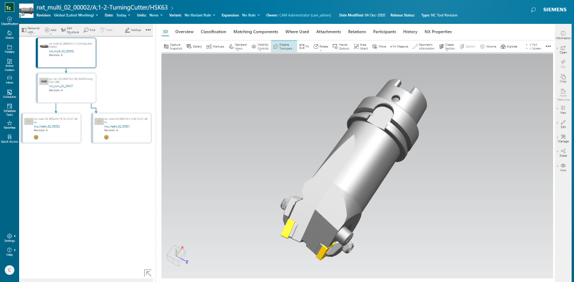
The new Shop Floor Connect (SFC) Download Counter is a security feature designed to limit the maximum downloads of NC programs. Users can set the maximum downloads of NC datasets from SFC using this feature.
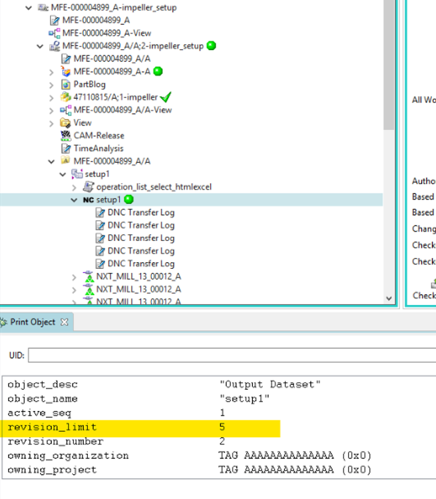
What’s new in NX CAM On-Machine Probing
NX CAM On-Machine Probing module provides comprehensive measurement technology to optimize the manufacturing process and improve workpiece quality. Measure, evaluate and compensate for process variations throughout your machining process and enhance your quality and efficiency.
The latest enhancement in NX CAM On-Machine Probing, provides an intuitive user interface, where all parameter possibilities and available cycles are visualized with a tooltip and an image.
Configurable dialogs provide flexibility and support for creating additional cycles. Users can benefit from graphical and user-friendly custom dialogs in all available languages provided by NX and the corresponding machine control, even without requiring developer expertise. Managing UI extensions is simplified with available editors, eliminating the need for manual and time-consuming source code editing.
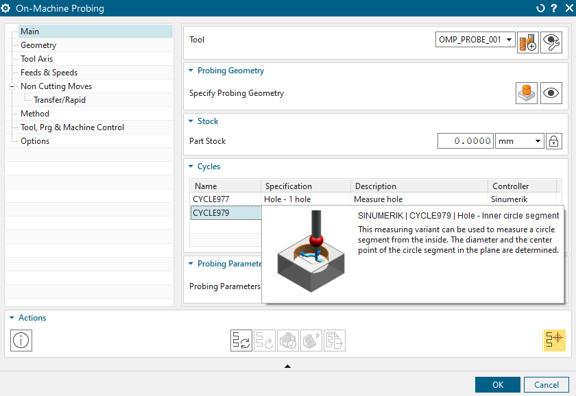
NX On-Machine Probing post-processor and simulation add-ons are available for free via Siemens NX CAM Post Hub. The latest improvements include the addition of layers for postprocessor and simulation extensions for commissioning. The free template layer enables easy integration using the post configurator in the layer manager. Even with different technology for post processors, you can still use it as a template. Additionally, a template is provided for your CSE machine simulation, simplifying integration into your simulation. If you need support to implement the extension in postprocessors and machine simulation, please reach out to your service provider.
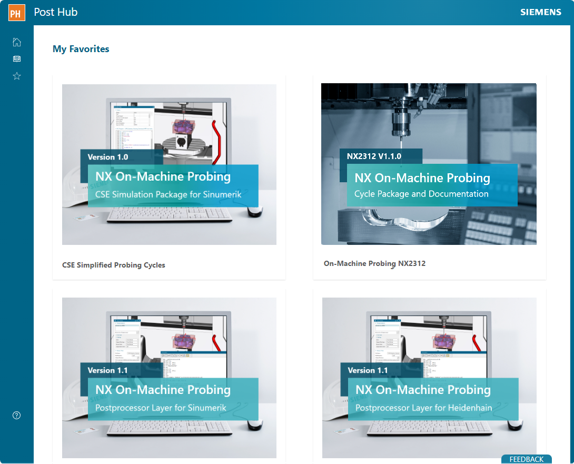
What’s new in NX CMM Inspection Programming
Generating automated and optimized inspection paths is even simpler now, especially for axis-symmetrical parts, which can be challenging to inspect with non-rotary table machine. With the automatically generated collision-free inspection path, users can efficiently inspect groove planes, cylinders, and circles with star probes. This enhancement enables a reduction in inspection programming time and an improvement in path quality.
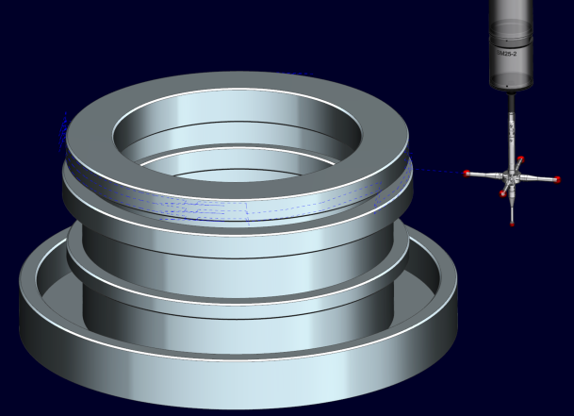
The new Split Scan Suboperation has refined how we handle scan operations, moving away from the previous approach of managing them as one large, multi-section suboperation. This new capability helps you generate an efficient inspection path with an enhanced user experience, enabling users to control, change and adjust scan operations for path geometry.

What’s new in NX Assembly Line Planner
The new tool validation feature allows you to choose the optimal joining tool for an operation, based on the geometry of the tool, product and fixture. You now can save time and efforts spent on revisions and adjustments while creating a smoother and more streamlined workflow. Planning engineers and simulation teams can collaborate on cohesive data, minimizing the need for changes during simulations and decreasing the necessary change management workflows.
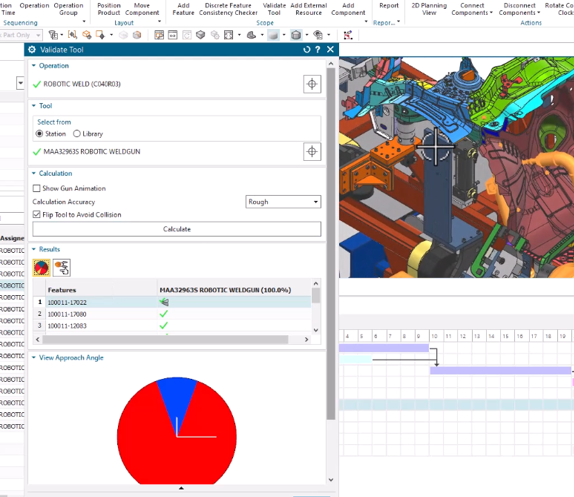
Detailed Takt time planning is now possible, allowing the planning engineer to set station-specific target Takt times, distinct from the assembly line target. This enhancement optimizes the overall production flow, ensuring smooth operation, especially for duplicated stations with longer processes. For instance, instead of the assembly line 60 second target Takt time, each duplicated station can have a 120 second target, accommodating alternating material flow while maintaining the assembly line validity.

What’s new in NX Line Designer
The latest enhancement in NX Line Designer introduces improved support for minimal load in both native and managed modes. You can leverage the minimal load option to load and display plant structures with lightweight representations, enhancing load performance. Native mode offers complete support for minimal load, including parts with connectors and kinematics. In managed mode, parts with kinematics and the immediate parent node containing resources that are interconnected, are loaded partially. The loading status of components can be seen in the Load State column of the Plant Navigator.
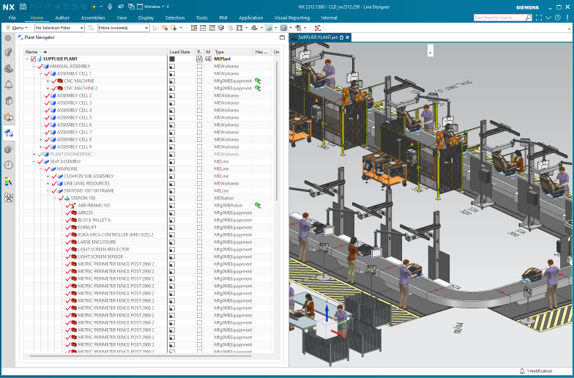
The newly enhanced 2D shadow outline feature allows you to efficiently create outlines for entire assemblies or a set of scoped selected content. By choosing simple or detailed outlines, you can employ advanced options like selecting a plane, changing colors, style and width, as well as assigning to a layer. This streamlines the authoring process, enabling completion in a single step. With this upgraded feature, you can quickly generate a 2D representation of equipment or sub-assemblies directly from the navigator or graphics window. You will receive a notification if outline creation encounters issues with bad or lightweight geometry. This alert helps identify and address potential problems in the outline creation process.

The latest enhancement to the Define Tool feature gives you the ability to define tool tips so that the tips are ignored when you do a clearance check. Save time and effort by reusing the defined tips in multiple scenarios while performing collision checks. Once configured in Line Designer, these tips can be applied in applications like Assembly Line Planner and Fixture Planner, ensuring consistency and efficiency across different tasks.

With just a few clicks, you now can enhance their experience in the Plant Navigator by adding a unit column. This column displays the units of components in the plant structure, making information easily accessible and improving user interaction.

Learn more
Eager to learn more about the NX for manufacturing features? Check out the step-by-step tutorial videos on our online community.
For more information about the new design capabilities in NX, check out this blog.
Season’s Greetings
The entire Siemens Digital Manufacturing team wishes you success in the new year!