What’s new in NX for manufacturing (June 2024)
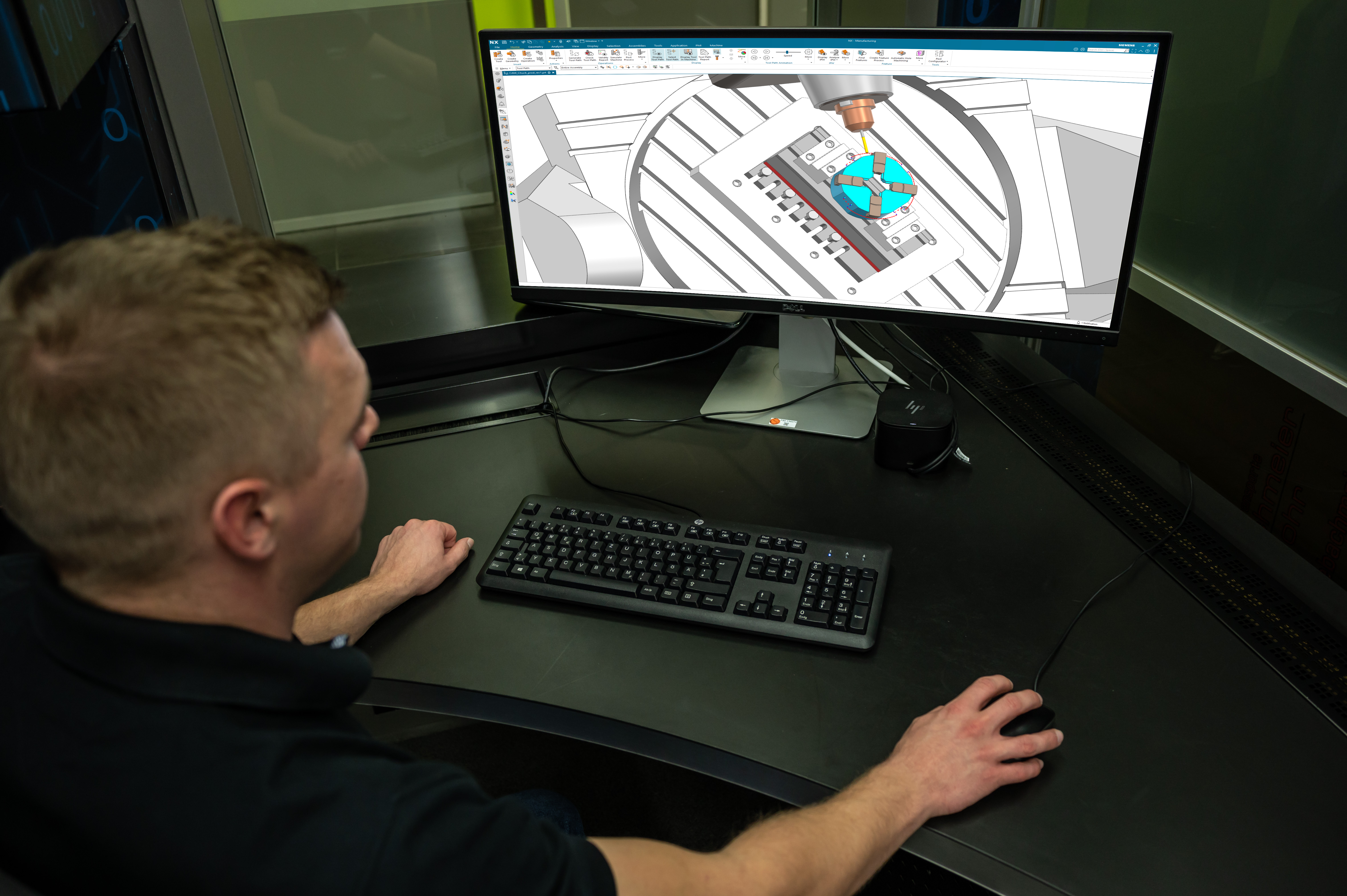
As summer approaches, we’re excited to unveil the newest NX 2406 software update! Packed with new features and enhancements, this release can boost your part manufacturing productivity. Get ready to dive into the enhanced capabilities of our integrated solutions for part manufacturing, including:
- NX CAM
- NX Additive Manufacturing
- NX CAM On-Machine Probing
- Part Manufacturing Data Management
- NX Assembly Line Planner
- NX Line Designer
Every NX update is designed to improve your efficiency and productivity, and NX 2406 is no exception. Discover all the exciting new part manufacturing features available in this latest version. Check out the video featuring innovative enhancements that will improve your NX software experience.
What’s new in NX CAM
NX CAM software features important enhancements based on the feedback from our users. Below we are highlighting the new capabilities that can help you be more efficient.
3D adaptive roughing, the high-speed machining strategy in NX CAM is now even more flexible, allowing programmers to determine the tool path start location to predrilled locations for safe tool engagement at high speeds.

With the new Start Drill Point feature, you can easily specify the area for the start point and the system automatically determines the exact start point based on the operation parameters. When specifying pre-drill points, you can now pre-drill a pocket to its floor. This allows the tool to plunge directly to the cutting level without a helical entry move, saving tool life and reducing overall machining time.
The Holemaking operation now offers improved control of non-cutting moves (both within and between features), more robust local gouge checking, and quicker tool path calculation time.

The Transfer using Engage and Retract option enhances control over toolpaths between cutting levels by replacing rapid motion with step-over types, ensuring controlled feedrates and safe transitions. Using the Relative Plane option, you can optimize transfer motions between hole features in a pocket, prioritizing safety. Additionally, you can adjust distances using the Lowest Rotary feature to minimize gaps between hole features and nearby collision geometries.
Extend tool life, improve surface quality, and ensure effective chip evacuation by enabling the Chip Removal Option.
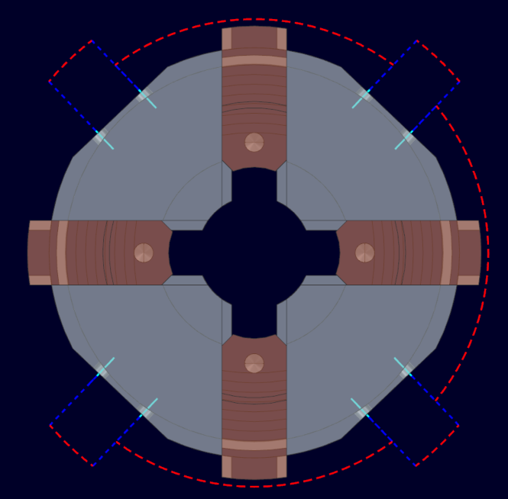
The new none-cutting moves options for Hole/Boss Mill provide greater control over the toolpath within a machined feature. This results in better tool life, improved swarf evacuation, and enhanced part quality. These options are available for Hole Milling, Boss Milling, Thread Milling, Thread Boss Milling, and Groove Milling.
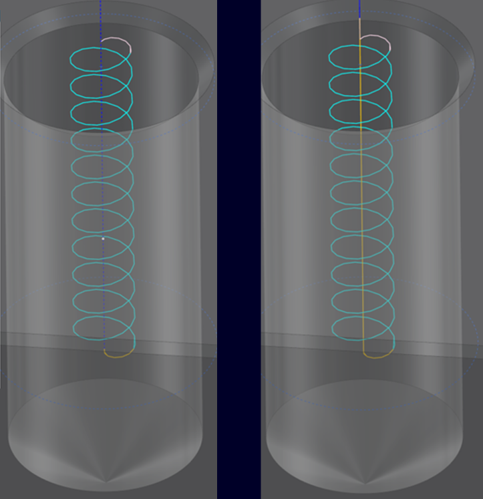
The Cloud Connect Tool Manager, a capability for efficient management of tools and machining data, has been significantly improved. It now offers enhanced data management, simplified tool holder creation, and direct access to multiple tool vendor catalogs within the application.
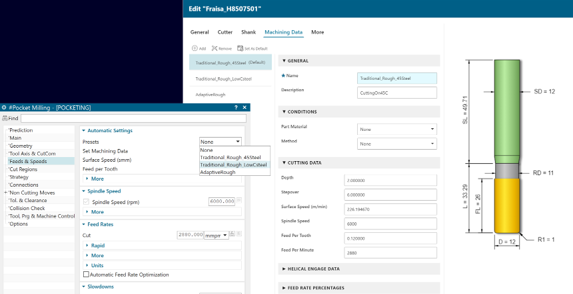
Improvements to the Cloud Connect Tool Manager include an intuitive interface for managing multiple sets of machining data associated with the tools. For instance, you can easily specify the part material, cutting parameters, helical engagement settings, and feedrates. The predefined tool machining data streamlines the CNC programming.

Machining data is now directly linked to each tool, allowing easy management of machining setting. Cloud Connect Tool Manager, which previously supported only a single set of machining data per tool, now allows multiple sets for greater flexibility. The new preset option enables you to automatically retrieve cutting parameters based on criteria like part material and cutting method settings.
The holder creation process has been streamlined using modern interface and fast import of data from cutting tool catalogues. Using the enhanced import functionality you can now read holders, enabling a seamless and intuitive import process from various tool vendor catalogues, including SECO and Walter Tools.
Machine Powered Programming is an innovative feature that transforms CNC programming. You can program while using a digital replica of the machine tool and its kinematics. This method offers a fresh and more efficient programming experience.
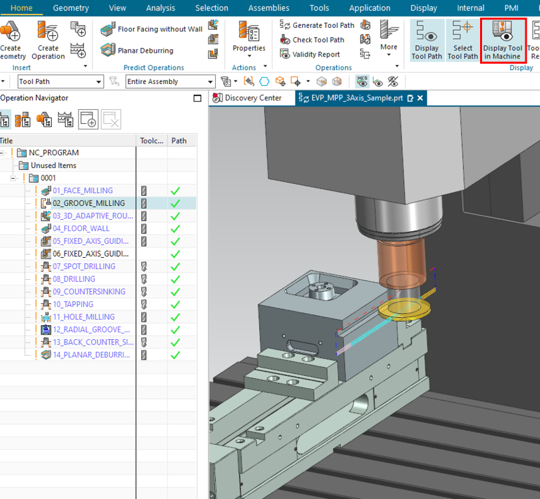
Programming complex jobs has never been simpler. You can gain constant access to the machine’s capabilities, which are now integrated into the programming process, making it more intuitive. This technology not only guides programmers to make the right decisions but also reduces the need for repeated simulation. This new programming method allows faster programming and improved toolpath quality.
Real Part Cut off After IPW transfer: The latest enhancement significantly improves the simulation accuracy for certain operations. Before, when the in-process workpiece (IPW) was divided into multiple parts during operations like turning cut off, the disconnected segments would remain in place in the simulation. This often led to false collision warnings.
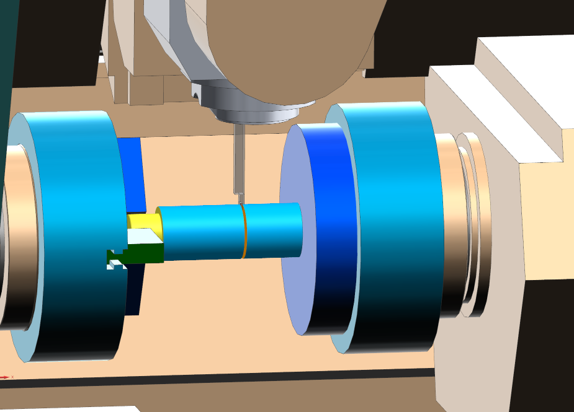
Now, segments that would fall away in a real-world scenario are simulated to do so in the simulation, reducing unnecessary collision alerts and providing a more accurate depiction of what to expect during actual production, enhancing overall efficiency and safety.
What’s new in Additive Manufacturing
The upcoming version of NX Additive Manufacturing provides new enhancements to the users in multi-axis and fixed plane capabilities.
A sub-nester has been added to group and nest small fragile parts as a pre-nester before creating sinterboxes. Additionally, brush facet selection makes it easier to define support regions on faceless convergent bodies, and there are multi-laser path preview enhancements for the Build Processor on EOS machines.
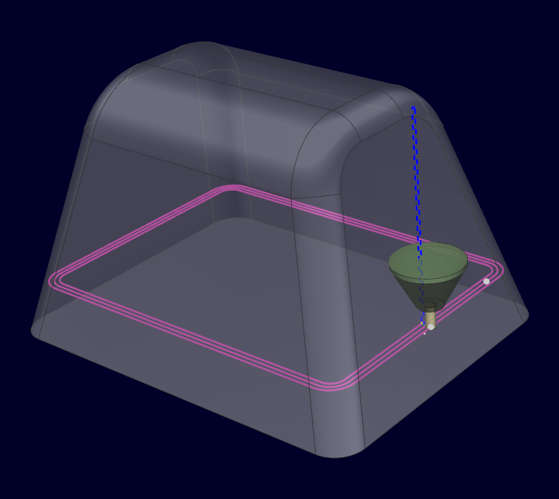
Flexibility in build widths has improved with the option to create multiple beads in planar thinwall, as opposed to previous versions that deposited a single bead per layer. Users can now create parts with thicker walls using a user-specified offset value.
Additionally, users can use a ramping strategy between layers and an inside-out to outside-in cut pattern, allowing for a continuous bead. This is compatible with the profile slicing option but not with the Helix option.
Build styles have been revamped with enhanced database access, enabling customization of individual operation components for user-specified Process Parameters. Creating basic build rules is now simpler, and applying custom process parameters to them is more streamlined.
Users can achieve successful builds on the first attempt by employing varied parameters for different operation sections, such as Finish Passes, Infill Passes, and Spring Passes, based on the output type.

This update offers increased flexibility in controlling process parameters across all operation aspects.
NX now allows you to use multiple offset beads in planar additive thin-wall operations, which reduces the need to model auxiliary manufacturing geometry and new build styles and build rules. In addition, NX gives you a way to capture and control machine and material specific process parameters, known as the “secret sauce,” for portions of a multi-axis additive operation.
Custom process parameters can be assigned to special attributes of output types, such as Helix Top/Bottom and Stepovers, for specific cases or unique requirements. You can now have the flexibility to dive deeper into assigning these parameters, when necessary, although it is not mandatory for general use.

The latest enhancements introduce improved visual representation of angled supports relative to the build platform or part geometry through color coding. This feature helps users quickly identify and manage supports positioned at angles, which require specific considerations for ensuring proper support and structural integrity during additive manufacturing.

This enhancement allows users to promptly identify printability issues and make immediate adjustments to support structures, ensuring all supports meet necessary criteria for successful printing. By providing color-coded feedback, the software enhances precision and efficiency in support generation, giving users greater control over creating and adjusting supports for reliable printing outcomes.
NX offers enhanced control over mesh quality for parts on the build tray, providing a variety of Print Resolutions to suit different levels of detail and processing needs. The available options include Coarse, Standard, Fine, Extra Fine, Ultra Fine, and User Defined, with Fine set as the default resolution.
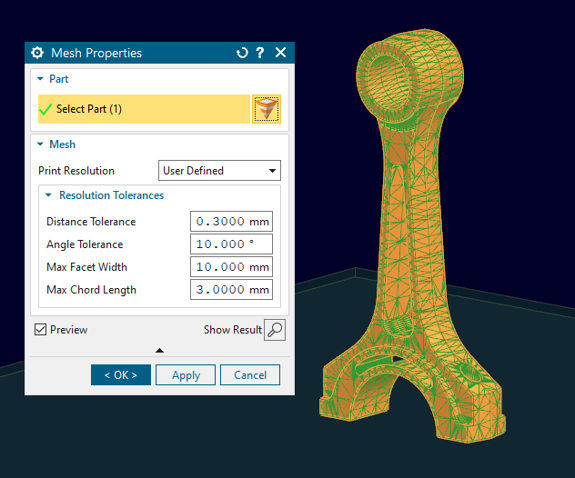
The latest update enhances control over mesh quality for parts on the build tray, offering various Print Resolutions to meet different levels of detail and processing needs. This improves the accuracy of printed parts by allowing users to define and adjust mesh properties through the Mesh Properties dialog. You can specify facet quality using options such as Distance Tolerance, Angle Tolerance, Max Facet Width, and Max Chord Length.
What’s new in NX CAM On-Machine Probing
NX CAM On-Machine Probing now has advanced capabilities that allow programmers to configure and capture parameters for streamlined process optimization and reuse of best practices.
The latest enhancements improve user workflow and increase programming speed. On-machine probing now automatically generates the toolpath each time a probing cycle is selected, or parameters are modified, eliminating the need for manual efforts. Toolpath animation is also continuously accessible now.

Considering the growing number of cycles and supported controls, the latest version introduces continuous improvements and optimizations to enhance manufacturing accuracy and efficiency. Updates include various features, adjustments, and fixes specifically designed for Sinumerik and Heidenhain controls. Initial implementations are focused on Renishaw I+ cycles for Sinumerik, but look out for future integrations with Fanuc, Okuma, and Haas controls through PostHub.

Presetting capabilities are also available ensuring that all parameter options can now be preset in a central setting file. Settings can be customized based on defined conditions, streamlining setup and optimization. Users can filter and sort measurement cycles to match specific machine/controller configurations or a generic machine setup, ensuring precise adaptation to various operating environments. A significant enhancement is the new control of tracking points for toolpath calculation, offering flexibility through machine-side calibration. This allows users to select either the probe tip or probe center for calculation purposes.

A new Post Processor add-on has been developed for both Post Builder and TCL-based solutions, serving as a bridge. This allows users to continue using their familiar environment while gradually transitioning to the upgraded Post Configurator. It ensures compatibility with legacy post-processing solutions and guarantees long-term support and compatibility with future versions of NX CAM.

What’s new in Part manufacturing Data management
NX’s part manufacturing data management has seen significant improvements, enhancing the organization and control of manufacturing process data within the software. These updates streamline workflows, improve efficiency, and uphold data integrity throughout the manufacturing process.
New enhancements have been added to the Manufacturing Resource Library (MRL) in Teamcenter, enabling easy management of manufacturing resources such as machines, fixtures, and cutting tools.
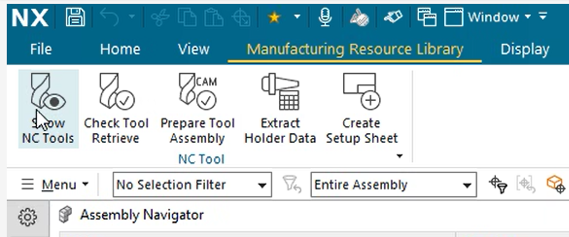
With direct access from NX through a dedicated Ribbon tab for MRL, you can now prepare manufacturing resources in Teamcenter, whether through Teamcenter RAC or the new web-based interface in Active Workspace.
Latest updates include access to functions such as checking NX CAM Tool Retrieve for tool compatibility with NX CAM, preparing tool assembly to create NX assembly part files integrated with NX Assembly/MTB, extracting holder data for analyzing tool holder geometry integrated with MX CAD/NX CAM, and generating setup sheets directly within NX using integration with NX Drafting.
With Machining Data Library in the MRL module, managing technology data like Feeds & Speeds data tables is now enhanced through the Teamcenter web user interface. This provides a streamlined method to look up machining details, search for technology data, reference properties, and assign resources to attributes.
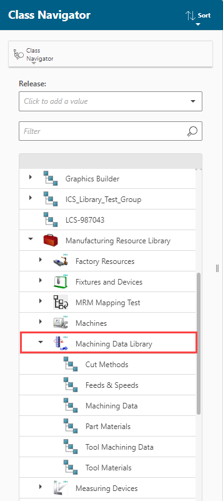
The intuitive interface facilitates quick access and assignment of accurate data. The Machining Data Library includes three main classes for managing technology records:
- Feeds & Speeds data tables
- Machining Data linked to specific machines
- Tool Machining Data for additional cutting tool references.
CMM resource management has been enhanced in the latest version, making it easier to manage probing tools, coordinate-measuring machines, and related devices. This includes operations such as classifying and preparing inspection machines, devices, accessories, probing assemblies, and measuring systems and components.

Detailed instructional videos are available in the Manufacturing Resource Library, offering background information and technical tips on defining and preparing these resources, helping users effectively manage CMM resources.
What’s new in NX Assembly Line Planner
The new reporting view in NX Assembly Line Planner enables users to create reports featuring visual representations of crucial line data. This includes visualizations of the product at various stages of assembly and the resources employed throughout the production process. Users can incorporate additional details, such as tables listing resource types and their power usage. Administrators can effortlessly generate report templates in .pdf, .html, or .pptx formats based on the application’s data, and manage them centrally in Teamcenter without requiring NX customization or programming expertise. This feature empowers users to generate reports to track planning milestones effectively.

With the introduction of the new high-level Gantt view and enhanced ability to manage flows between operations across different stations, cross-station process planning in Assembly Line Planner has been streamlined.

This allows planners to create detailed process definitions for manufacturing lines more effectively, particularly when planning operations that utilize shared resources across stations. You can now easily create, update, and delete flows between operations in different stations, while also accessing current and target takt times in the PERT view.

For better representation of product build-up, enhancements to the PERT view in Assembly Line Planner improve clarity. Incoming products are color-coded differently with added transparency to emphasize newly assigned items. Additionally, images now capture entire line nodes, including sublines within the loaded scope.
What’s new in NX Line Designer
NX Line Designer’s load performance has seen a significant improvement, with load speeds now 87% faster compared to previous NX versions. This enhancement addresses the primary user requirement for efficient load times, optimizing performance in both native and managed modes. You can now seamlessly load additional data as needed during their interactions.
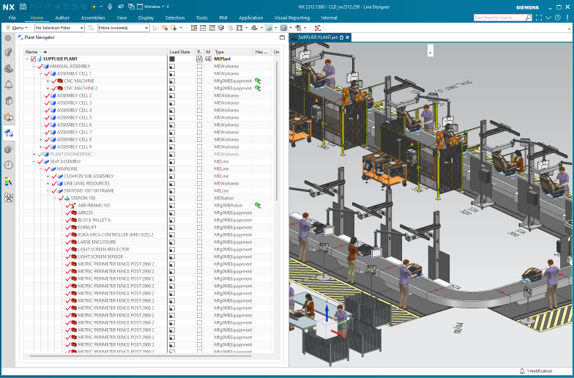
With enhanced support for minimal load now available in both native and managed modes, the loading process has been optimized. In native mode, only parts with connectors and their immediate parent nodes are loaded minimally. In managed mode, parts with kinematics are partially loaded, while part family members are fully loaded.
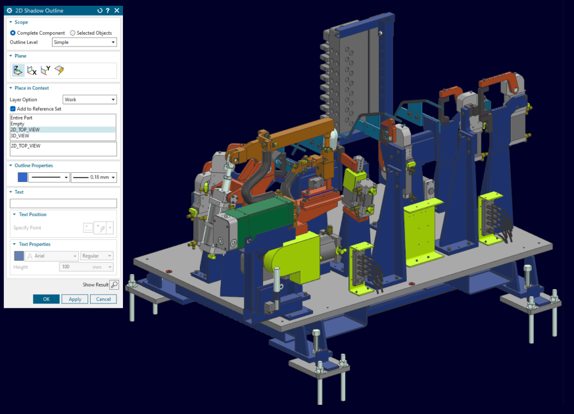
The user experience has been enhanced with the new 2D shadow outline feature in NX Line Designer, which refines the visual representation of objects through improved outlines and shadows. This increases visibility during the design of production lines or layouts. You can now quickly generate 2D representations of entire equipment or sub-assemblies by selecting content from either the Navigator or directly from the Graphic Window. The latest 2D shadow outline command streamlines the process of creating outlines, allowing users to generate them for entire assemblies or selected content designated as a Reference Set.
Advanced options such as adding and customizing text properties—including color, font style and height—have also been added, to efficiently complete the authoring process in a single session.
Additional resources have been integrated into the Line Designer library. The new Factory Resource Library is available on the Support Center under NX additional downloads. It includes resources from categories like Architectural, CNC Machines, Industrial, Material Handling, Robots, Vehicles, and Workers for both Inch and Metric units.
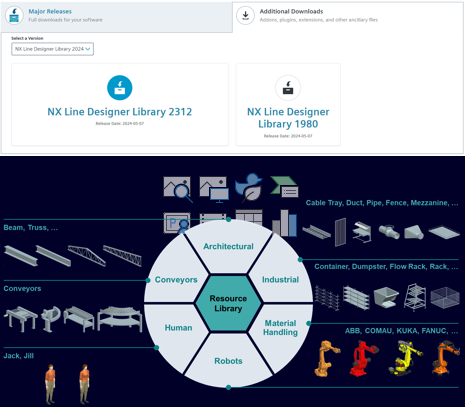
Learn more
Watch the release day premiere video featuring innovative new features and enhancements that will level up your NX software experience.
Eager to learn more about the NX for manufacturing features? Check out the step-by-step tutorial videos on our online community.
Explore more about the new design capabilities in the latest NX -> here.
Looking to gain more insights into programming prismatic components, complex parts and high-quality molds? Sign up for a guided 30-days free trial now.