What’s New in NX for Manufacturing software (June 2019)
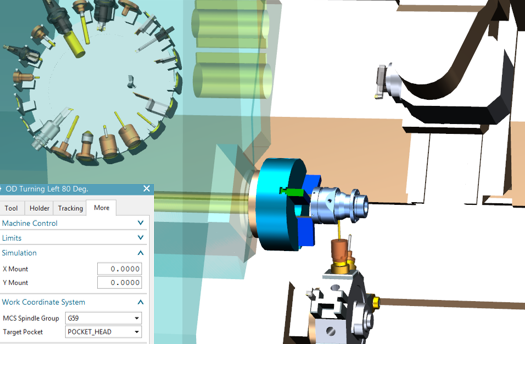
What’s New in NX for Manufacturing?
Powerful new enhancements are now available in the latest release of NX for manufacturing, our comprehensive solution for CAD, CAM, CMM, robotics and additive manufacturing.
The new capabilities will help you be more productive, including:
- Create multi-step drilling tools automatically
- Leverage barrel tools for more efficient machining
- Regenerate 5-axis toolpaths almost instantaneously
- Validate robotic operation with G-code-driven simulation

Read more about these and other enhancements in NX below. You will also find a link to videos that demonstrate the new capabilities.
For the wider part manufacturing community, we now offer a free NX CAM software trial in the cloud. Just sign up and start using NX CAM in your browser in minutes.
Prismatic parts machining
Automatic tool creation using part feature
This new, automated process in NX CAM can dramatically speed up the NC programming of parts with multi-step holes that can be found on many different parts, such as machinery components. These holes with complex geometry require special tools, called “step drills.” Creating and applying step drills using conventional methods can be a time-consuming process.
With NX, you can now automate the process. Based on the recognized hole geometry, NX will quickly search your tool library to find and select the best tool to machine the hole.
NX can also automatically create a new step drill based on the geometry of the hole. In the process, it also gives you flexibility to define the sections of the multi-step hole feature that need to be machined. Additionally, you can specify material stock for further machining.
These automated process in NX CAM reduce tool creation time by up to 6 times.

Tool magazine visualization
Programming CNC machine tools with automated tool magazines can be challenging, particularly if your CAM system lacks visualization capabilities. NX CAM lets you accurately display the machines’ tool magazines, along with all the stored tools, creating a digital twin of the entire machine.
During NC programming and when you define your tools, you can easily assign or change the target pockets.
This new capability helps you program CNC machine tools with tool magazines faster. The accurate digital display of the tool magazine and the tools helps you avoid any possible collisions between the tools.

Machining Line Planner (Multiple products and exporting solid In-Process Workpiece (IPW)
NX Machining Line Planner is used for high-volume production of complicated parts with many features. It enables distribution, balancing, programming and simulation of operations over multiple setups and machines.The new enhancements let you plan manufacturing of more than one product on a machining line. This is often the case in an automotive environment, like in the shown transmission-case example.
In this example, Product A, the upper-part of the transmission-case, is machined in Setup 1; Product B, the lower-part in Setup 2 and the two parts are assembled and machined together in Setup 3. The programming is very simple – you can select the product or combination of products to be machined in each setup and the system takes care of the rest.
Also, you can now export a solid IPW for each setup. IPW tracks the state of the machined part by using the blank or the IPW of the previous setup, as an input. This not only allows you to visualize the machined part at each stage of the multi-step process, but it also lets you create drawings for each using the IPW. These drawings, which are associative to the IPW, automatically update due to design or process change, ensuring that the latest version of the shop documentation is used in production.

Mold and die machining
Adaptive Milling for high-speed machining
Adaptive Milling is a high-speed machining method in NX CAM software that can reduce roughing machining time by up to 60 percent.
In the latest version, NX provides a new function to generate toolpaths with smooth engage and retract moves. Additionally, you can smoothen the transfer moves improving the overall machine performance.
These new controls can help you further reduce machining time, minimize machine wear and extend tool life.

Finishing using guiding curves
The Fixed Axis Guiding Curves finishing operation generates toolpath patterns using one or two sets of guiding curves.
Often, when you import CAD part models that you need to program, the geometry can be imperfect. For example, the part edges can be disjointed, having small gaps in them. Previously, if you used these disconnected curves to create your guiding curves finish operation, you’d have to first manually repair the curves, which can be very time consuming.
With the new Guiding Curve Bridge Curve option, NX automatically identifies and bridges the gaps, creating continuous curves.
This new functionality saves programming time and it enables creation of smooth finishing toolpath. The generated operation follows the natural geometry shapes, resulting in excellent surface finish that eliminates additional rework.

Complex parts machining
Smart toolpath regeneration
In the new version of NX CAM, the toolpath re-calculation time of 5-axis toolpaths has been minimized.
In many cases, especially when programming parts with complex geometries, NC programmers need to fine-tune the tool axis to achieve better machining processes. In those situations, NX can almost instantaneously calculate the updated toolpath, while maintaining all the previous toolpath adjustments, such as smoothing and trimming.
According to Siemens’ product testing, the new capability helps you calculate toolpaths with adjusted tool axis, on average, 10 times faster than before. For larger toolpaths, the time savings can be even more significant.
This not only reduces your overall programming time, but it gives you more flexibility to create optimized operations for your parts, which can improve the machine behavior and machining results.

Taper barrel tools
Machine shops are increasingly using barrel-shaped tools for 5-axis machining. These tools provide powerful advantages, such as large cutting contact with the workpiece, enabling you to machine higher surface quality with fewer passes. NX CAM has been supporting the use of these tools.
In the latest release, the support for these innovative tools has been expanded with a new class of tools – taper barrel tools. The large barrel radius (>1 meter) make the shape of these tools almost conical. The taper angle (A/2) enables you to position the barrel tool against a flat wall and yet avoid holder collisions. Using the tip radius (R1) you can perform tip machining as a separate operation.
With the new class of tools in NX CAM, you can quickly create barrel-shaped tools. You can also use parameters from tooling vendors catalog to create these tools.
When creating 5-axis operations, you can apply taper barrel tools to improve the surface finish and reduce your machining time.

G-code driven robot simulation
You can program robots to perform machining tasks as well as material handling operations using NX CAM.
The new G-code-driven simulation allows you to accurately validate the processes prior to production by using a digital twin of your robot. In this release, NX CAM provides digital robotic kits for two KUKA robots.
With the new simulation capabilities, you can emulate fly-by motions using the zone values, simulate external NC programs and sub-programs. The parser uses the Python programming language.
Note that the new release of NX supports a cell with a single robot and linear moves. Positioners (1-2 axes) and rail with mounted tool are the currently supported configurations, while mounted workpiece is planned for future releases.
By using the G-code driven simulation you can validate the robotics operations in NX CAM, helping you eliminate errors in production, while reducing setup times.

Simulation and Verification
Multiple in-process workpiece (IPW) sources
Often complex castings are pre-machined in multiple setups and then assembled together for final machining in a subsequent setup.
In the past, it was only possible to transfer a single IPW source to another setup, which could be a limitation for certain applications.
With this new function, you can use multiple IPW sources to build a composite IPW, which can be used as input blank for subsequent machining of the entire assembly.

Additive manufacturing
Print CSYS
In previous versions of NX, the designer has been able to specify a Print CSYS that relayed information about the preferred print orientation to the printer operator. The Print CSYS information is saved with the part, and with the latest release of NX, the printer operator now has the option to add parts to the build tray using the Print CSYS to define the initial orientation. The operator may adjust the orientation from there using the normal build tray setup tools in NX. As print orientation can influence part function and finish, this functionality facilitates communication about the print orientation between the designer and the machine operator.
2D Nesting
3D nesting has been part of the NX functionality for quite some time, but 3D nesting of parts in a build tray is mostly used for plastic printing. For metal printing, parts are almost always arrayed in a single layer on the build tray. 2D nesting is now an option that may be selected when nesting parts in the build tray in NX Additive Manufacturing. This option will automatically place as many loaded parts onto the build tray as possible. When parts are loaded using an existing Print CSYS for orientation, those orientations can be honored using the constraints in the Automatic Nesting dialog.

Join the NX for manufacturing conversation with other users on our manufacturing discussion forum.
Try NX CAM software free for 30 days by signing up for a trial in the cloud. Get more information here.
