How heavy equipment companies achieve zero-defect manufacturing in part production
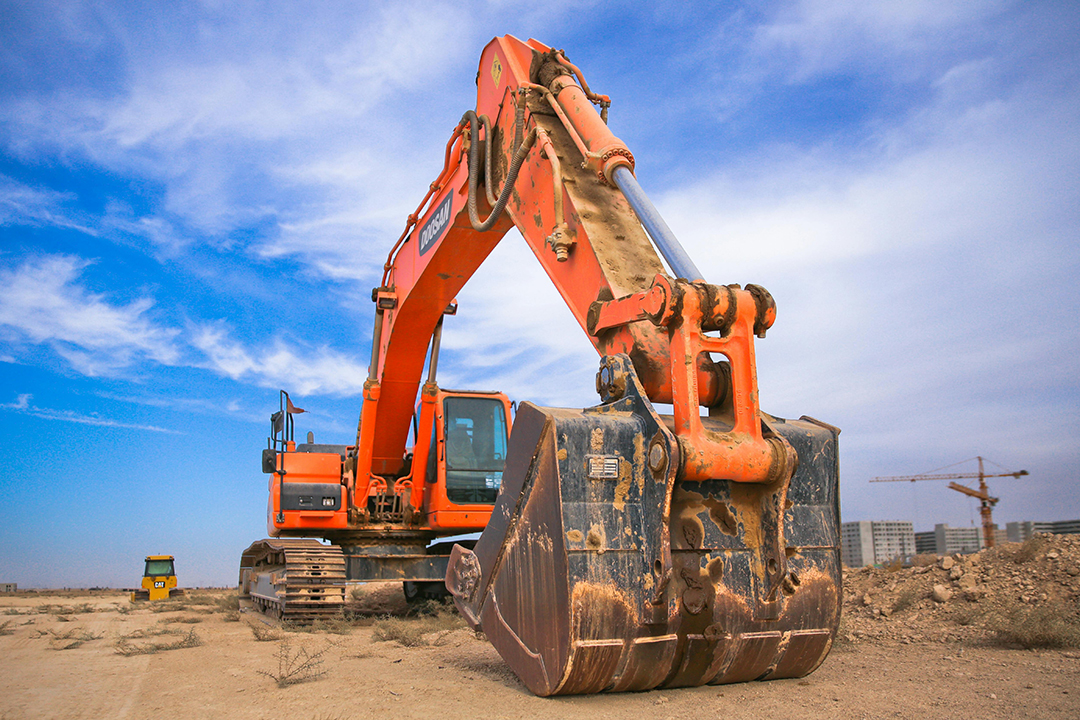
In this blog, we will navigate the landscape of heavy equipment manufacturing, highlighting the role of digital software tools in helping companies address industry challenges. We discuss how heavy equipment companies, and their suppliers can utilize integrated digital manufacturing solutions (including advanced CAD/CAM software) to make the equipment that customers demand in an efficient and sustainable way, while achieving zero-defect manufacturing in their part production process.
Drive by any construction site, and you’ll spot them: bulldozers, loaders, excavators, compactors, cranes, and more. You’ll see this heavy equipment machinery at work and think “big tools for big jobs”—and you’ll likely keep driving without a second thought. But what if you aren’t alone in the car? What if you have your curious, wide-eyed kids in the back seat, eagerly peering out the window for a better look?

To them, these aren’t just big machines, they’re metal giants! Complex, colossal beasts capable of super heroic feats.
The intricate dance of complex parts, gears, the mastery of hydraulics, the sheer power – it’s a symphony of engineering brilliance. Beyond the surface of these mechanical behemoths lies a story of precision, collaboration, and innovation. In creating these mechanical marvels, heavy equipment companies bring together thousands of meticulously manufactured components. It requires a blend of expertise, cutting-edge technology, and processes that enable zero-defect manufacturing from heavy equipment OEMs and their suppliers.
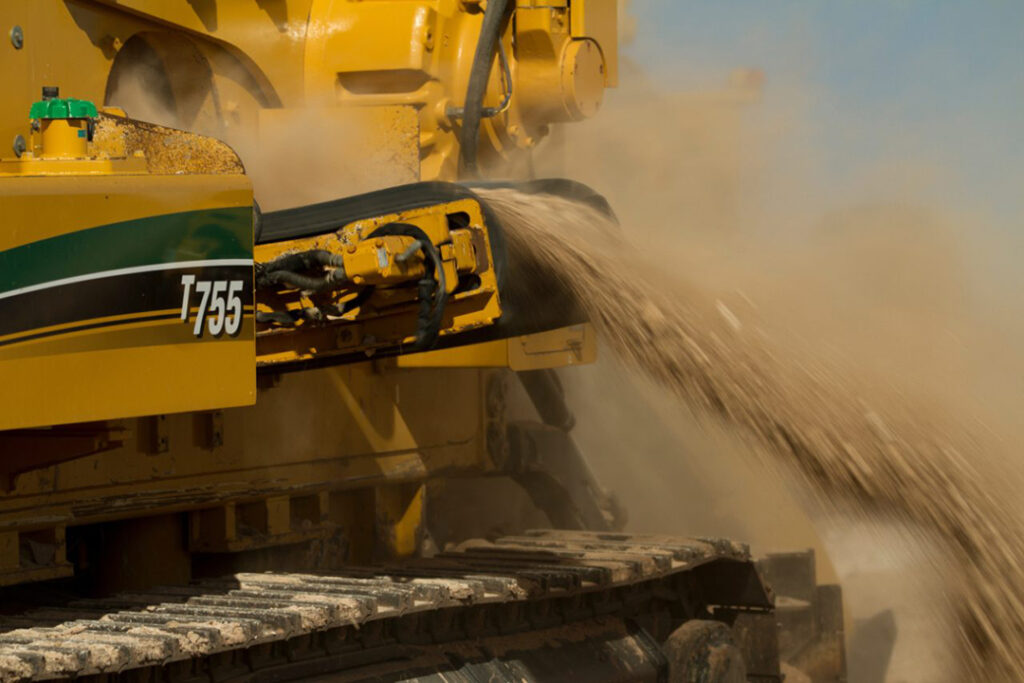
So, let’s take a closer look behind the scenes at the intricate tapestry of part manufacturing, and the precision required to ensure safety, quality, and performance in the heavy equipment industry.
Trends and challenges facing heavy equipment machinery manufacturers
Heavy equipment manufacturing is characterized by highly configurable products, made in limited production volumes, with very tight margins. OEMs and their component suppliers must take advantage of every cost saving opportunity. Manufacturing efficiency can make a significant difference in impacting profit margins.
Adding to the challenge, industry trends in heavy equipment, including electrification, more digital capabilities, sustainability, and specialization, require a new generation of machines. This means that manufacturers must be able to manage additional complexity, including more components from more diverse suppliers and a greater degree of customization. To ensure safe margins, manufacturers need to continue to focus on ways to increase efficiency and flexibility. Achieving zero-defect manufacturing is a difference maker.
Digital tools for zero-defect manufacturing
To meet these challenges, heavy equipment manufacturers are looking to digital tools to optimize their part manufacturing and drive zero-defect manufacturing. By automating part production and leveraging the comprehensive digital twin that includes product and production, companies can virtually plan and simulate the most demanding manufacturing processes, minimizing real-world errors and enhancing quality.
Today, Computer-Aided Manufacturing (CAM) is at the heart of the part manufacturing processes. Using CAM software, engineers create programs to run the Computer-Numerical Control (CNC) machine tools on the shop floor. The most advanced CAM software systems enable programmers to use the virtual replica of the entire machine so they can program, validate, and then output the optimal machining process.
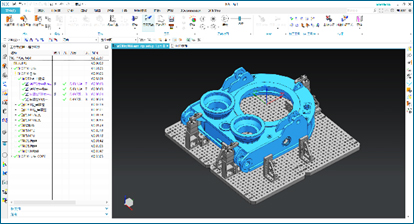
NC programming automation is an important time saver. Using highly automated CAM software simplifies programming of the most challenging components. CAM systems can help companies improve overall productivity by generating optimized machining processes, ensuring consistent outcomes, and eliminating waste. Utilizing advanced cutting techniques, modern CAM software can significantly reduce cycle times. Through automation and the reuse of company best practices, the entire process is streamlined and accelerated, offering companies substantial efficiency gains. CAM software is critical for increasing manufacturing efficiency, improving part quality and helping manufacturers achieve the goal of zero-defect manufacturing.
Watch automated NC programming in action on a heavy equipment component
Let’s look at the NC programming of a heavy equipment component using the industry-leading CAM software – NX CAM. In the example below, we will demonstrate how to create the operations to efficiently machine a hitch bracket.
The hitch bracket provides a secure and stable connection between the machine and various accessories, such as trailers, plows, or other agricultural and construction implements. The hitch bracket allows the machine to exert its power and traction to tow, pull, or operate these attachments efficiently. Hitch brackets facilitate the quick and easy interchangeability of attachments to enhance a machine’s functionality and overall effectiveness.
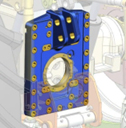
To program this prismatic part, we’ll use the advanced 2.5-axis capabilities of NX CAM that enable you to quickly program a large number of features, while generating toolpaths that can reduce machining time. Watch the video to learn more about some of the advanced programming capabilities aiding in zero-defect manufacturing including:
- Feature-based machining helps you automate programming using proven processes. The system analyzes the part, recognizes its features, and creates all of the necessary machining operations to make this part.
- Post Hub, NX CAM’s cloud-based solution for postprocessing, provides an extensive library of post kits for a wide range of machine tools allowing you to quickly output production-ready NC programs.
- Integrated G-code-driven simulation is a key NX CAM advantage that facilitates integrated simulation and verification. Programmers can check tool paths within the NC programming session, verify material removal to optimize machining, and simulate multi-axis operations for error-free manufacturing.
- Output production-ready NC programs for your machine tools. The validated programs can be easily transferred to the shop floor.
- Complete shop documentation can be generated and transferred to production. This enables you to leverage a modern, highly automated CAM system (such as NX CAM) to quickly program any heavy equipment component, while ensuring that you use the latest manufacturing technologies in production.
How SANY reduced production costs by 15%
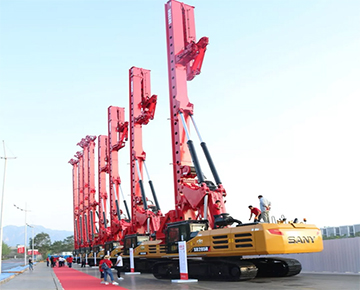
SANY, one of the largest heavy equipment manufacturers, makes machinery for some of the most demanding applications such as earth-moving, road building, and other construction projects. Their extensive product line includes excavators, pile drivers, wheel loaders along with many other products.
Their reputation for toughness is built on their equipment’s durability, which directly depends on the quality of the components used to build SANY’s equipment.
Until recently, the use of multiple software systems for design and manufacturing prevented SANY from standardizing their complex part manufacturing processes. This disconnected, and inflexible process required a lot of manual input impacting the overall efficiency and the quality of the critical components.
To address these challenges, SANY has deployed NX software to program their CNC machines and make the components needed for their equipment.
As mentioned above, NX CAM helps engineers automate NC programming by using feature-based machining technology. SANY engineers use this capability to recognize the features on a part and create a complete machining process for manufacturing the part on their CNC machines. It provides consistent results and use of proven methods, which helps standardize the process.
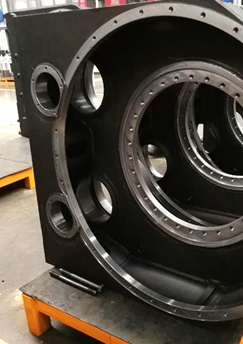
The integrated machining simulation enables SANY’s programmers to use one software system for NC programming and validation, eliminating the need for a separate system for simulation. Using the accurate digital twin of the part, machine setup and machining process, the engineers can ensure that the generated operations are optimized and error-free. This can eliminate costly errors on the production floor and maximize machine uptime.
NX enables the engineers to create complete shop documentation (such as setup sheets, tooling lists) tailored to the company’s needs. This complete manufacturing data, including the production-ready NC programs, is transferred to production to drive their advanced CNC machines.
This end-to-end digital process (powered by NX CAM) enables a high level of automation and connectivity. As a result, SANY’s manufacturing team achieves virtually perfect first acceptance rate, while reducing production costs and increasing the productivity, helping them maintain their reputation for quality and durability.
Digital manufacturing solutions for heavy equipment companies
As heavy equipment manufacturers embrace digital part manufacturing to meet challenges in an evolving industry landscape, the role of digital manufacturing software solutions becomes increasingly clear. Digital solutions including CAD and CAM enable heavy equipment companies to increase efficiency, ensure precision, and facilitate standardization in the production of heavy equipment parts – leading to the ultimate goal of zero-defect manufacturing.
Learn more about Siemens NX digital manufacturing solutions and check out a free trial of NX CAM to see how these solutions can help you embark on your digital transformation journey.