The importance of quality management in the automotive industry

Volker Schwickert, Vice President for QMS Software, Global Portfolio Development, Siemens Digital Industries Software explains the challenges that the automotive industry faces and why quality management is so crucial for success.
What are the major trends in automotive manufacturing?
The car has become a complex, sustainable system that drives autonomously, entertains the passengers, and connects with online traffic services. While globalization has been a trend for decades, supply chain disruptions, especially in electronics and semiconductors, have increased bottlenecks. When manufacturers try to solve these problems, they are going back to local sourcing, changing their suppliers, and ramping up inventories. So, automotive manufacturing demands that the digital infrastructure by which vehicles are designed, produced, delivered, experienced, and serviced must innovate just as fast as the vehicles themselves. Quality management is a crucial process for the digital transformation, and imperative for meeting today’s challenges.
Digital transformation of quality management
Why do we need to consider quality management as crucial?
As new innovators have entered the market, a dichotomy has emerged with traditional OEMs. While they are facing the same challenges, they are competing with different strengths. The OEMs have been part of an industry that pioneered quality practices.
Across the industry, however, the quality challenges are the same. With supply chain insecurity, alternative suppliers must be identified and validated more quickly. When you look at quality projects, like Advanced Product Quality Planning (APQP) or Production Part Approval Process (PPAP), which are defined in automotive norms, you have enormous pressure on timing and deadlines.
The personnel shortages and travel restrictions are also impacting quality. For example, supplier and customer audits need to be done remotely or in a hybrid approach. This is creating the need for better collaboration solutions, so participants can mitigate quality issues with proven methods.
For example, considering a global company that makes auto parts and has numerous plants around the world. If each plant has several departments with a vast number of resources, constraints, and quality approaches, the only way to manage them is with a collaborative environment that houses relevant data, quality standards and best practices. This comprehensive system needs to work towards fast and effective issue resolution, while informing all functions of required changes and actions.
Meeting guidelines and standards requirements
How are quality management solutions addressing these challenges?
Quality management systems must be able to adapt to changes in global standards and industry-specific supplements or guidelines. Whether it is a new form or procedural improvements that include new templates and methodologies – the quality management solution must keep pace.
However, in the conventional quality cycle, a gap has persisted between engineering and manufacturing. This is a key area in which building quality management on top of a smart manufacturing architecture transforms the value chain.

A closed-loop approach completes the cycle from engineering to manufacturing to supply chain, and down to field services. This is only possible with a comprehensive digital twin – where the quality information is connected across the product lifecycle.
At Siemens Digital Industries Software, we aim to help manufacturers to accelerate digital transformation. As part of these solutions, it is fundamental to support a holistic quality management strategy across the extended value chain. A digital twin enables a feedback loop back to the lifecycle for continuous improvement.
We have focused on creating this comprehensive foundation within our Siemens Xcelerator portfolio, which is a comprehensive portfolio of software, hardware and services. We see the digital twin not only connecting quality to manufacturing operations, but also connecting the entire lifecycle from product design, engineering, simulation, test and production to field performance.
Increase product quality and improve customer satisfaction
How is it possible to increase product quality and improve customer satisfaction?
Leveraging such a portfolio, the manufacturer should be able to start with design for quality, leverage 3D models and the BOM and BOP structures that are already there to improve quality process interactions.
Simulation and variation analysis are important functions that are enabled by the digital twin. In the digital realm, manufacturers can simulate design to production, do product planning and production process planning virtually, and the digital backbone can be used to sort out quality problems before the real production, where the cost of a problem is much higher.
The APQP project management, the checklists of PPAP going down the product and parts approval process – quality monitoring is available to all functions. Failure mode and effects analysis (FMEA) is fed back to the control plans and failure catalogs that need to be monitored across the lifecycle. The manufacturer must move beyond just finding problems – their systems should be preventing problems before they occur. Compliance is a byproduct of the system – it must be built in. Companies can increase product quality and improve customer satisfaction with APQP.
The continuous improvement process can also be enhanced to have minimize of failures, reducing costs in time and materials, and attaining target quality in product launches. For example, methods like cause-and-effect diagrams or 5Whys, which are used to analyze root cause, would previously be incorporated into the quality process as an attachment, where the system would document what people did on paper. People in the company must collaborate across department borders, but also with suppliers and customers.
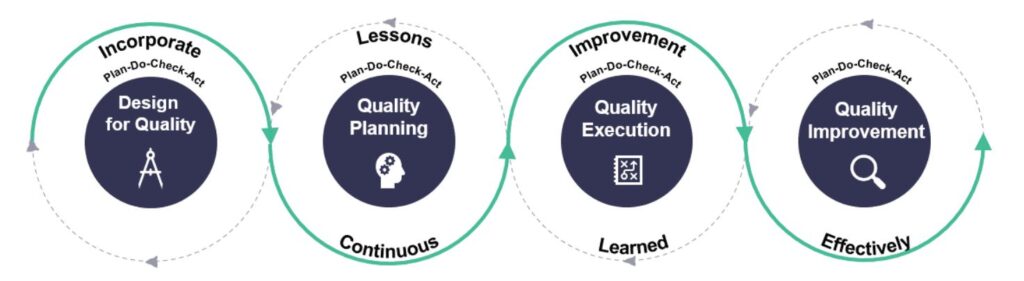
What about the next steps for digitalizing quality management
A capability of modern digital manufacturing tools is the ability to quickly adapt to the changing needs of the business and extend core solutions farther into the value chain. Integrating a low-code platform allows users to create easy-to-use interfaces and workflows for every participant in the value chain.
Cloud accessibility is another key requirement for the future of quality management.
The bottom line is that there is a strong business case for digital transformation and quality management. When both OEMs and suppliers implement a comprehensive quality management solution, many benefits come up:
- harmonized processes;
- strengthened security;
- rationalized resources;
- reduced scraps and reworks;
- improved warranties and goodwill;
- more rapid and effective corrective and preventive actions;
- higher customer satisfaction and loyalty.
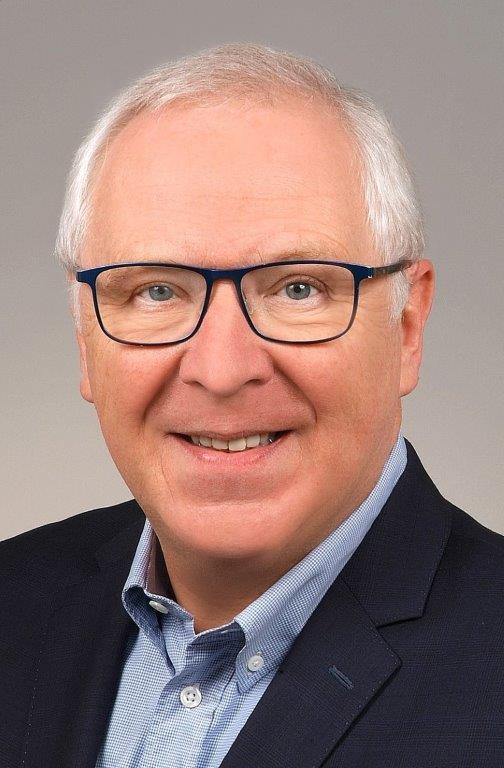
Volker Schwickert, Vice President for QMS Software, Global Portfolio Development, Siemens Digital Industries Software.
(For more information about Volker Schwickert: LinkedIn)