Manufacturing PCB and Box Together

Creating end-to-end digital transformation
In electronics manufacturing, there are several manufacturing processes that may be accomplished by different manufacturing suppliers within the value chain. There is often a customer that commissions the product, such as brand owner like Apple, designs the product, and transfers the PCB design to a manufacturer that produces the board. That board, together with the design of the end product, are transferred to another manufacturer that produces the final product (box-build).
Some manufacturers do both the PCB and the box-build manufacturing. These companies are the subject of this blog. They are responsible for the end-to-end manufacturing of the finished product. Instead of having a digital infrastructure that supports the product end to end, however, they often have different solutions for the two segments of the process – one for PCB manufacturing and one for box-build. While there is significant potential synergy across production areas for these manufacturers, their siloed systems are preventing them from realizing that efficiency.
We at Siemens, having worked in all segments of the electronics industry, saw this challenge in the market. We invested specifically to solve this problem. We built on our strong foundation in electronics manufacturing execution with the Camstar MES platform, which creates efficiency in the box-build process. We acquired Mentor Graphics four years ago to extend the platform’s capabilities in PCB manufacturing with their Valor solution. Mentor’s Valor solution was the PCB industry’s first true end-to end software solution, covering all phases of PCB manufacturing from new product introduction to assembly and test. We combined those best-of-breed solutions to create quality, efficiency, flexibility, safety and speed optimized across technical domains. The result was Opcenter Execution Electronics.
The Opcenter Execution Electronics solution delivers a holistic system, uniquely capable of unifying product design through process planning through service – end to end.
Let’s look at the requirements the manufacturer of the end-to-end process faces. The PCB process is an automated one, relying heavily on machines and automation. The process is well standardized, with variation in board shape and component placement. The process is always the same – apply the screen printing, position the components, do the cooking in the oven, perhaps some manual placing, then inspection.
The box-build is more challenging. It is not as standardized as PCB production and requires the ability to remodel the process often. More powerful assistance to the human operator is needed in box-build. The types of manufacturing steps are more varied. For example, mobility requirements of the end product drives product dimensions, wearability requirements, pocket fit, and an exact matching of electronic with mechanical functionality.
Now, let’s consider the main trends in the electronics industry that are intensifying the need for efficiency, specifically for the manufacturer that handles both the PCB and the box-build processes.
- Mixed product life-cycle. For our PCB/box-build manufacturer, we have mixed product life-cycles, with more complex product assembly. While the industry as a whole is struggling with shorter product life-cycles overall, our manufacturer experiences differences from the PCB life-cycle to its box-build life-cycle. PCBs may have revision cycles, but they are going into the same cases.
- High customization. Consumers today are loyal to particular brands. Product models must respond to changing preferences and expectations. As the product evolves, every release has the risk to disappoint or the opportunity to gain wider market demand. New features from version to version, representing functionality improvements, must be brought to market quickly and with high quality to address the significant competition. Agility in the manufacturing process, and control over manufacturing change, are critical.
- New technologies and regulations. Products may have variability depending on markets, with different languages, climates, and unique regulations. The manufacturer must comply with different regulations for the EU, Africa and US, for example, which adds complexity to their compliance system requirements. Those regulations need to be met for the PCB as well as the final product.
With all of this complexity, and the pressure of speed, margin, and quality, manufacturers must apply a progressive product improvement paradigm. The growing of a product – based on previous revisions – requires efficient change management, and the intelligent analysis of those changes to understand the implications on the specifications of the rest of the product. They must work in delta, with revisions, adding features and removing obsolete ones. With each change brings an impact to all the other components of the product. The PCB/box-build manufacturer’s change management approach is used across design, process planning and production. The changes have to consider the interdependence of the electronic parts with the mechanical parts.
Throughout the process, the human to machine connectivity and collaboration includes automated data collection and work instruction progress in step-by-step activities. An operator may receive a label, scan that label, and then the system must use that context for the operator to perform something specifically. The result of that operation may trigger a unique next step.
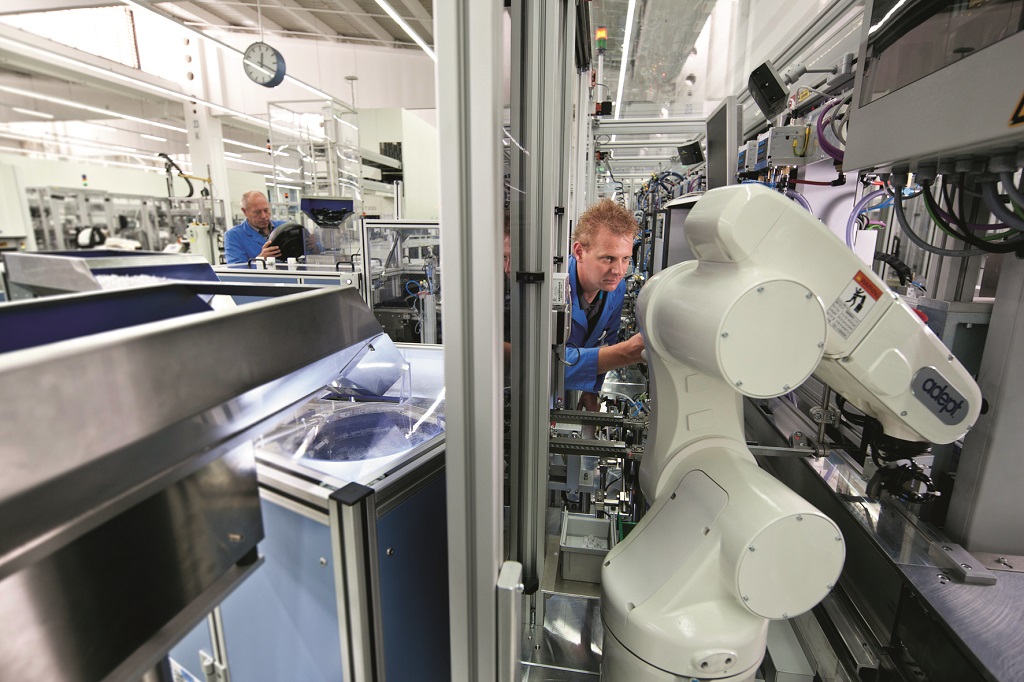
Operators in this environment are not artisan, who are very skilled, but very expensive. Today, the operator may be in a single area of the build process. They may not do the same job every time, but perhaps 10 different jobs. They move from one station to another, they are allowed doing operations where they are properly skilled, and identify themselves with the value of the single step rather than the final product. In this case, we can’t count on the operator for the final quality of the end product. The sum of all the steps is the quality of the product.
The importance here is that these operators are in a mixed environment. They handle different tools and different components, but don’t collect the experience of doing just one job. There may be a mix of assembly, test and repair. There may be automated context-driven label printing, safety and error proof concepts like poka yoke, automated robot cells for safety, robot cells for heavy duty functions. Assembly and quality requirements may be in the same operation. These steps tighten the interdependence, the complexity of certifications, training, and augmented reality.
There may be programmed devices to set corresponding parameters, understand human positions, trigger the parameter reading, collect parameters – and all this must consider the previous operations context and parameters. These things require information flow across the production environment.
These operational realities require an MES system, a system that is able to connect an end-to-end process from design to automation to human operations. Product variability requires progressive operator learning and skill acquisition.
The intelligence gleaned from a single system that orchestrates the PCB and the box-build processes, with a complete digital twin in terms of quality and process, detects root causes between box and PCB. This is a unique capability with a holistic system, enabling improvements across product revisions. If you have an MES system assisting the operator, and in the same facility you are acquiring data from PCB manufacturing, you can implement more advanced analysis for quality improvement.
Here we come to the smart factory example – if you have more information, you are able to find root causes that may be related to the skill of the operator, plus the parameters of the PCB process, plus a mechanical characteristic of the box.
That’s what Opcenter Execution Electronics delivers. It provides collaboration across planning, execution, assembly and quality, harmonizing human operations with automation and electronic PCB manufacturing with box-build.