AI-powered root cause analysis improves product quality
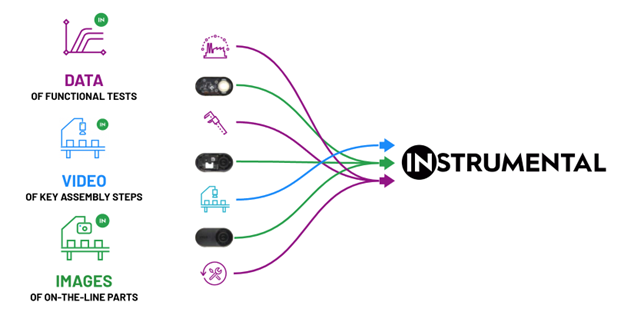
Solving quality issues remains a challenge
Manufacturers know problems can occur at any stage of production. These issues can cause delays, scrap, rework, and lost revenue if not caught and addressed quickly. Companies use Quality Management Systems (QMS) like Teamcenter Quality to avoid these negative consequences. These solutions can systematically manage quality processes, capture issues, guide users through a best practices resolution methodology, and document events for audit purposes.
However, in many cases getting the right data to determine the root cause is a difficult and often manual task resulting in delayed and sub-optimal solutions. State of the art for defect analysis is a complex undertaking involving lengthy back-and-forth communication to aggregate vast amounts of test data from multiple suppliers and physically collect and disassemble units. Additionally, engineers travel to factories around the globe to stand on production lines, hoping to be in the right place at the right time to catch defects and identify opportunities to improve the overall design or assembly.
Now, Instrumental has joined forces with Siemens to supercharge the process of remotely discovering issues, rapidly assessing impact and root-causing problems, and monitoring the efficacy of corrective and preventive actions, all in order to help minimize the impact on production lines.
Streamlining root-cause analysis in Teamcenter Quality with Instrumental
Instrumental is a cloud-based manufacturing quality and AI platform that delivers a unified, traceable record of manufacturing data and images. The platform uses proprietary computer vision algorithms to proactively identify and investigate new issues. Quality and engineering teams have immediate access to powerful data and visual correlation tools, making it easier to solve complex problems on assembly and manufacturing lines.
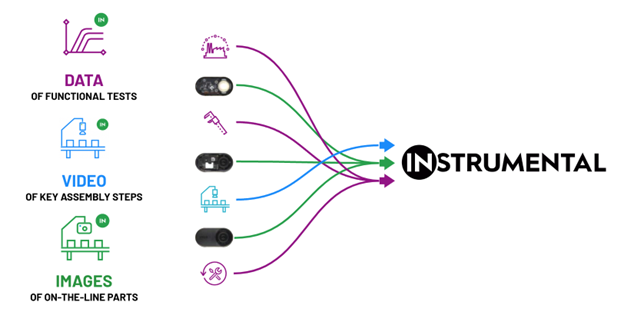
To help maximize quality and eliminate deviations, non-conformances, and issues, Instrumental’s AI-powered “Discover” feature automatically highlights visual anomalies. Engineering teams can then identify product issues, prioritize them and easily monitor them on their production line. Moving forward, units impacted will be detected in real-time and rerouted for repair or scrap.
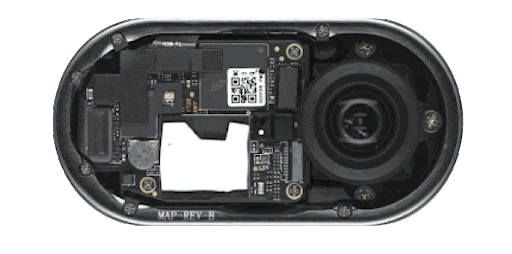
Once a defect is discovered, engineering teams can create a pass/fail model in just a few clicks to identify all past and future units impacted. New issues can then easily be exported to Teamcenter Quality with a single click.
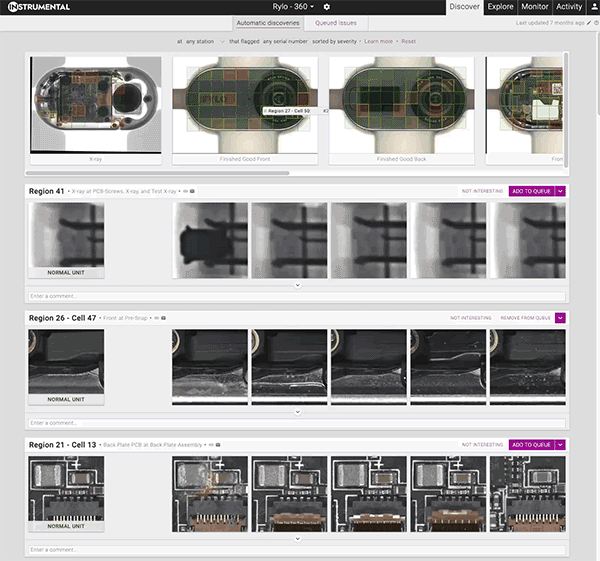
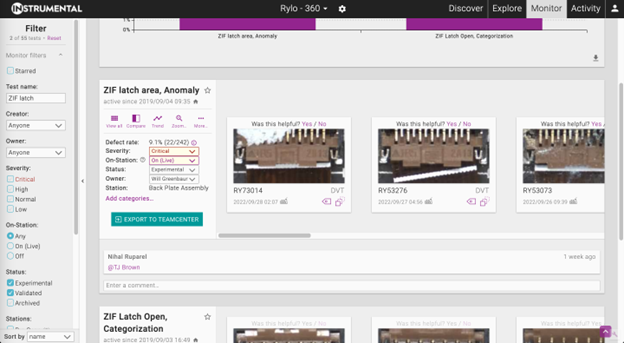
Pushing an issue from Instrumental to Teamcenter Quality automatically brings in all the related data, including defect images and serial numbers for all impacted units, allowing users to create immediate containment actions and investigate the problem while following well-established methodologies like 8 Disciplines Problem Solving.
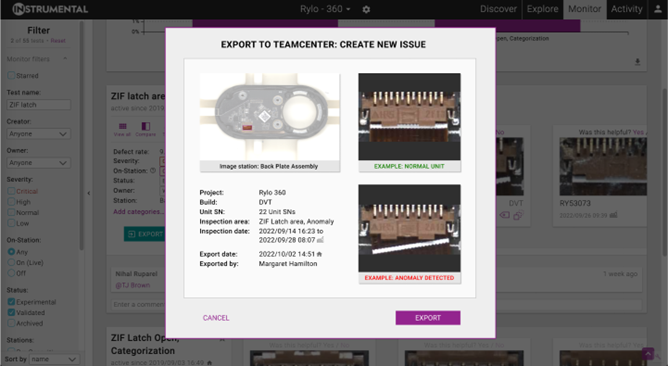
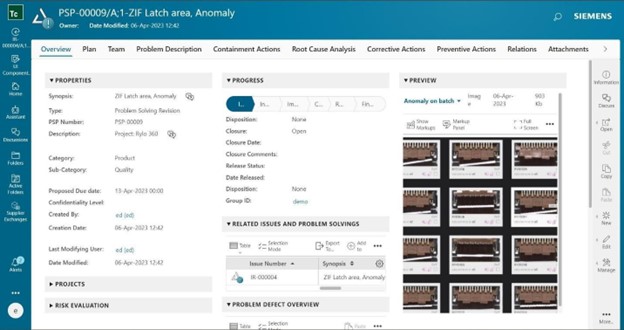
Engineering teams can use Instrumental’s AI-powered root-cause analysis to accelerate the creation of containment, corrective, and preventive actions in Teamcenter Quality.
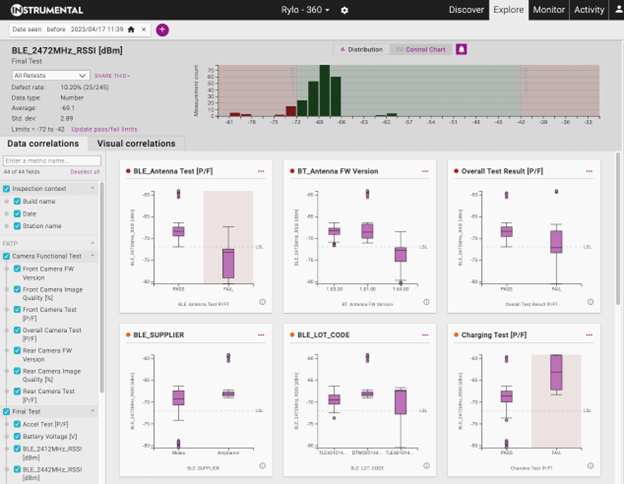
To summarize, the benefits are:
- Automated anomaly detection to proactively fix issues before they get out of control.
- Improved efficiencies by allowing engineers to easily access production data.
- Enhanced root-cause analysis activities through AI powered correlations.
- Streamlined documentation for product and process related issues.
- Tracking and measurement of the effectiveness of corrective actions over time.
- Meaningful contribution to sustainability initiatives, including carbon reduction from higher yields throughout the supply chain and reduced travel expenditure.
The combination of Siemens Teamcenter Quality with Instrumental provides a powerful solution to improve the efficiency of root cause analysis. “By leveraging machine vision, AI and data analytics, combined with time-proven methodologies, manufacturers can solve issues faster while preventing them from happening again, ultimately improving their bottom line.“ said Levent Koese, Siemens’ Quality Product and Portfolio Manager.
See what customers say about Instrumental. Schedule your demo today (link here)!
For more information, go to www.instrumental.com and watch a short video of Instrumental.
About the author:
Anna-Katrina Shedletsky, CEO and founder of Instrumental, holds dual degrees in mechanical engineering from Stanford University. She previously served as Product Design Engineering Lead for the first generation Apple Watch.
About Instrumental
Instrumental is a manufacturing quality platform based in Palo Alto. It was founded back in 2015 By Anna-Katrina Shedletsky and Sam Weiss. Instrumental has raised over $80M in venture funding and is working with the world’s leading electronics brands such as Meta, Bose and SolarEdge.
About Siemens Dynamo Program
Instrumental is a Partner Startup in the Siemens Dynamo Open Innovation Program. Dynamo identifies, nurtures and integrates disruptive technologies and business models from diverse origin to ensure Siemens’ leading position in Industry 4.0.
Comments