Looking beyond home-grown production scheduling tools
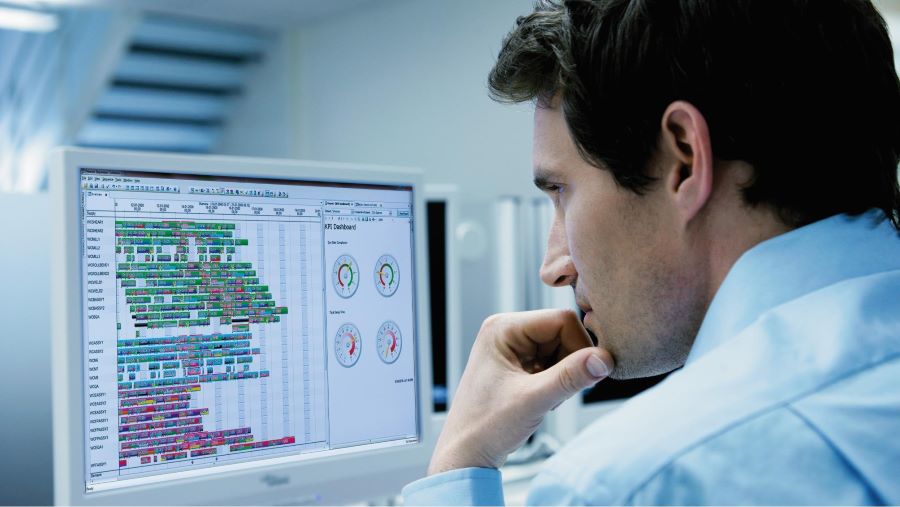
When speaking to SMBs across North America, you’ll often hear planning and scheduling professionals say that they use a “home-grown” solution to do their production scheduling. This usually refers to a customized ERP, Excel spreadsheet, third-party software, or more often than not, some mix of the three.
For anyone interested in solution-finding, this scenario poses an interesting question: why are so many companies using scheduling setups and solutions that are unique to them? Is it simply because their processes are so unique, or is there something missing in the solutions available on the market?
The current landscape for ERP-enabled scheduling
An ERP is a huge investment. That’s why it makes sense for companies to want to use this software to its fullest extent. When it comes to production scheduling, though, ERPs can’t account for the real-world constraints of your shop floor or the hard-earned knowledge your team has about how things work in the real world. For example, your ERP doesn’t know that it takes longer for a certain machine to cool down than it does to heat up, which can have major consequences for how you sequence some operations.
On top of that, an ERP typically assumes that all resources are available always, or that your shop floor basically has infinite capacity. The ERP takes some estimates about processing times, creates large buckets of time, and asks you to toss your tasks into those buckets and hope that they’ll provide enough buffer to account for any unforeseen changes. Or you just toss in so much buffer that you think it’ll be able to absorb any possible disruptions to your production schedule without impacting your OTD too much.
Home-grown scheduling solutions
So now, we can start to understand why many companies using ERPs and MRPs still supplement these tools with Excel spreadsheets or other manual processes, because scheduling always requires more knowledge than what can be loaded into a conventional ERP. This is why so many companies end up with a “home-grown” solution. And to be fair, many of the planners and schedulers we speak with do an incredible job using this method.
Still, the manually intensive “home-grown” approach is time-consuming and susceptible to errors, and it rarely captures the shop floor knowledge required to tackle the constant challenge of re-planning and re-scheduling production due to demand changes, breakdowns, quality issues, material issues, absence of employees, etc.
Enter Opcenter APS
An advanced planning and scheduling solution like Siemens Digital Industries Software’s Opcenter APS can plug easily into an existing ERP system while incorporating data about the real-world constraints of the shop floor. With this tool, a scheduling professional can regenerate their company’s entire production schedule, if necessary, every single morning (in 15 minutes) to accommodate changing conditions (late arrival of materials, sick employees, machine breakdowns, etc.). These changes are so seamless that they aren’t detectable to a shop floor worker who is receiving their work assignments each morning since the rescheduling will not interrupt any operations that have already begun.
The best path forward
A scheduling solution should only schedule work when resources and materials are available, and this is why APS scheduling is so crucial. Without one, a company’s only other options are to stay status quo with their home-grown solution or spend significant amounts of money and time on revamping their ERP and/or MRP to take on the tasks of finite capacity planning and scheduling.
With the simple integration of an APS solution into the existing ERP, the ERP system retains the BOM structures, explosion, routings and inventory control while the APS deals with the problems associated with the allocation of materials between aggregated orders and uses this as part of the scheduling function. That means the constraints include not only the machines, labor and tooling, but also the constraints associated with the availability of materials at raw, intermediate, and finished stock levels.
Best of all, synchronization is easy because all your APS data is coming from one source: your existing ERP.
Next steps
As time goes on, we see more companies moving from their home-grown solutions to adopting an APS scheduling solution like Opcenter APS. If you’d like to discuss what APS scheduling can do for your company, please contact us to learn more. Or check out our webinar on Opcenter APS and smart scheduling to learn more.
Philip Glennie, Ph.D. is the Director of Marketing and Sales at Longterm Technology Services. Over his career, he has worked extensively in the world of enterprise software, including ERP, APS, and PLM solutions. He is dedicated to helping companies of all sizes take their next step forward in Industry 4.0.
Longterm Technology Services based in London, Ontario, Canada, is a recognized Siemens Smart Expert Partner with over twenty years of deep experience helping companies supercharge their products and processes with Siemens Digital Industries Software.