How much time do you spend searching for parts?
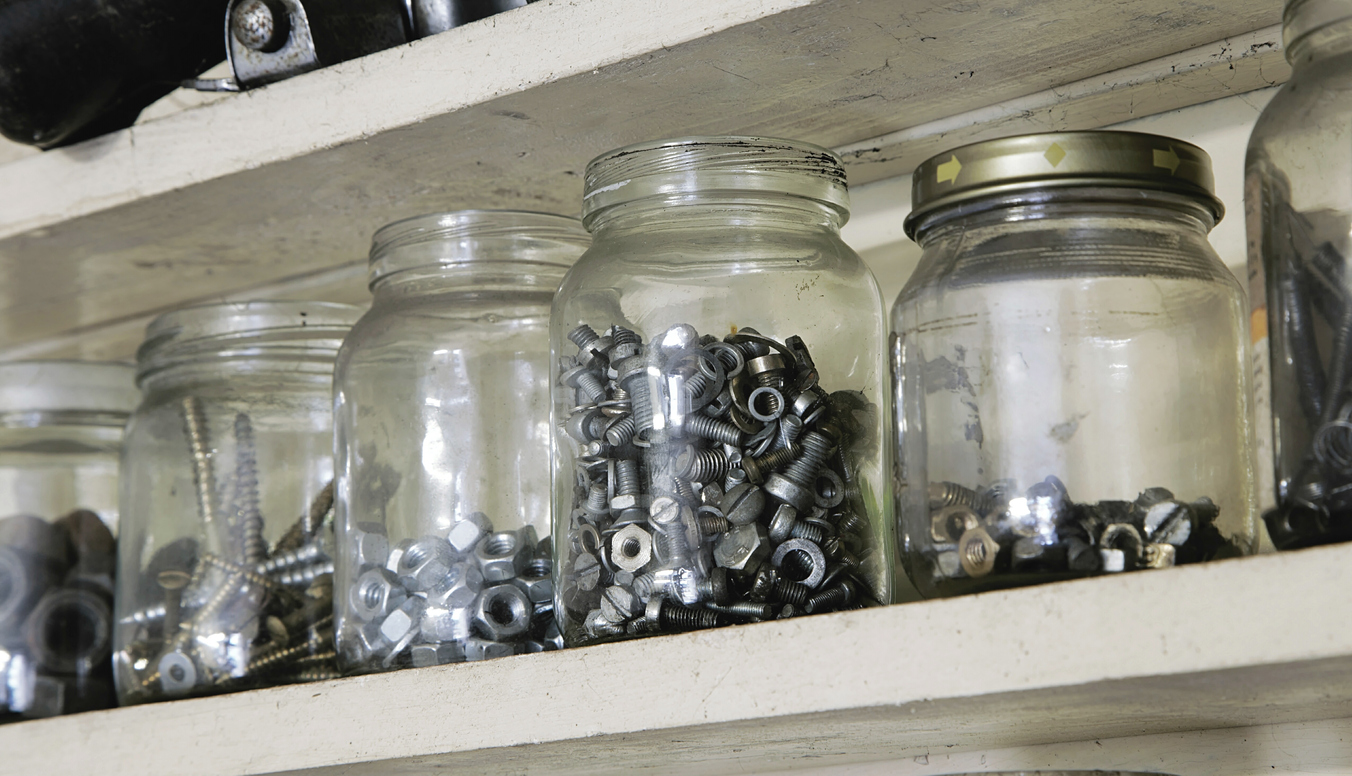
Imagine repairing your lawn mower’s Briggs & Stratton engine and discovering a cracked 1/4-20 bolt. You dump out the old nut and bolt jar on your workbench, start sifting through and find what looks to be a match. But it’s metric M6x1. It seems to fit, so problem solved. You get through a couple of weeks of mowing the lawn, and then the engine starts to rattle.
Engineers are often faced with the same dilemma. They dig through internal databases, which are virtual nut and bolt jars. Yet, they often can’t find the parts they need and, out of frustration, end up painstakingly searching for parts online to download or recreate the parts that already exist somewhere in their system. In this simple example, how much time does a design engineer waste looking for a bolt? Now, imagine the search is for a more complex part or component.
Lean engineering and procurement teams in nearly every industry face the same challenges in designing and sourcing parts. They must navigate numerous systems, such as multiple CAD, PLM and ERP platforms. Many of the world’s leading OEMs and tier manufacturers often have these software systems siloed, with little or no integration.
Data residing in isolation causes significant challenges in accessing information that should otherwise be intuitive. In today’s IIoT-Industry 4.0 world, any manufacturer wishing to remain competitive must manage time, costs and efficiencies. However, 48% of engineers still spend at least one hour per day searching for parts because the quality of the company’s parts master data is insufficient and unclassified.
In this environment, searching for parts and information becomes increasingly difficult and time-consuming for engineers and purchasers. Poor internal component search engine tools and a lack of access to high-quality supplier catalogs lead to wasted engineering effort.
Couple this with multiple facilities working together with master parts data created in different languages, and it becomes daunting to search for, design and procure parts. Too often, this leads to inaccurate information and cost overruns.
Searching for parts leads to wasted time and money
Without the right strategic parts management, software engineers waste an average of 68% of their time searching for parts, or configuring and unnecessarily recreating new components. This equates to thousands of work hours yearly wasted on non-constructive activities without monetary value. On top of that, each newly created component carries an expense of its own. A Survey among 128,000 engineers and designers revealed that a single design engineer may waste over 1,250 hours per year, costing the company over $100,000.
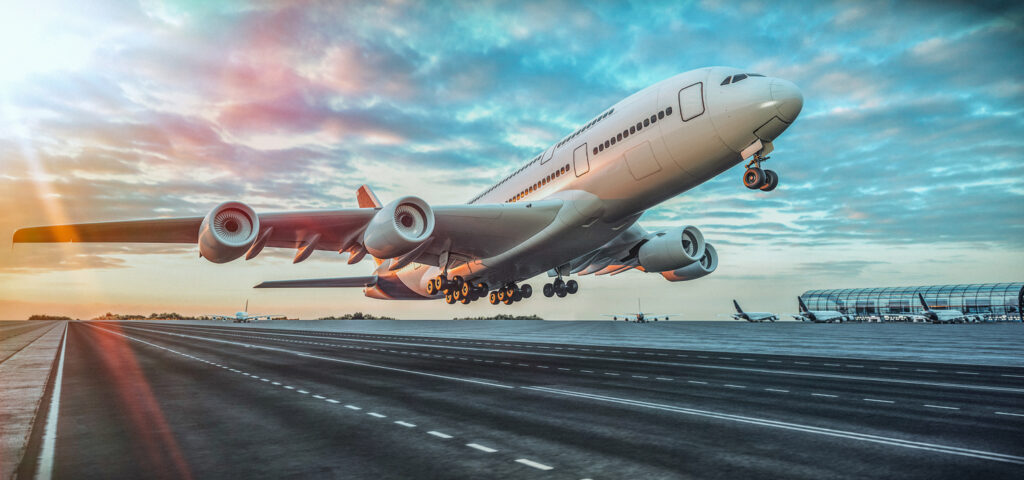
Under these conditions, a newly created single part that is self-designed can be costly. According to Rolls-Royce, every self-designed part by their engineers requires 400 additional data elements, processes and parts. The expense for every new component is accordingly high.
The following shows the average development cost per part in different industries reported by leading manufacturers:
- Company making clamping devices for machine tool equipment: $225
- Organization manufacturing machinery that produces woven plastic packaging, plastic recycling and refinement equipment: $800, plus an additional $100 per year
- Global leader in driveline and chassis: $1,100
- Global leader in compaction technology and equipment: $1,400
- Major truck and bus manufacturer: $3,400 to $4,500
Finding the CAD within PDM
Product Data Management (PDM) is intended to help companies improve their control, access and share critical product-related files and information in a central system. Within this information is CAD data, which includes manufacturing instructions, models, parts information, requirements, notes and associated documents. However, studies have shown companies have an average of three different CAD systems. To further complicate matters, external partners’ tools often do not communicate with the company’s platforms, which frustrates engineers and procurement and impedes them from efficiently doing their jobs.
Attempting a specific part number lookup within a conglomeration of CAD files can be like that proverbial “jar of nuts and bolts” or searching for a single 1/4-20 bolt in the local junkyard. Engineers and procurement specialists waste costly time searching, sometimes only to find out too late it was the wrong component. It is a thankless job, but one that can be easily corrected.
Survey on the design of products using CAD files
Tech-Clarity conducted an international survey on software-intensive product design, including CAD files. The study of 2,500 companies included a combination of organizations including:
- 39% from companies of less than $50 million (USD) in revenue
- 16% ranged from $50 million and $100 million
- 12% from $100 million to $250 million
- 16% between $250 million and $1 billion
- 17% were greater than $1 billion
Survey respondents were a mix of engineers and designers representing manufacturing and design industries, including:
- 34% Industrial Equipment/Machinery
- 22% Automotive and Transportation
- 17% Building Products/Fabrication
- 15% High-tech and Electronics
- Others included Consumer Packaged Goods, Energy/Utilities, Chemicals, Life Sciences/Medical Devices, and more.
According to the Tech-Clarity survey, 49% of companies report sharing information with other departments is a top design efficiency challenge. And 46% report simply trying to find the correct information hampers their design work, with 35% saying they often work on wrong or outdated data. These are significant roadblocks to efficiency, costing companies millions in lost productivity.
Even when an engineer locates the correct version of a file, they may still need to manipulate the data so it can be used in a partner’s CAD system. It’s been reported that nearly half of all organizations find it cumbersome to import files from other CAD platforms and discover they are tough to modify.
These semi-automated or completely manual operations cause unnecessary loss of time and money, not to mention burnout.
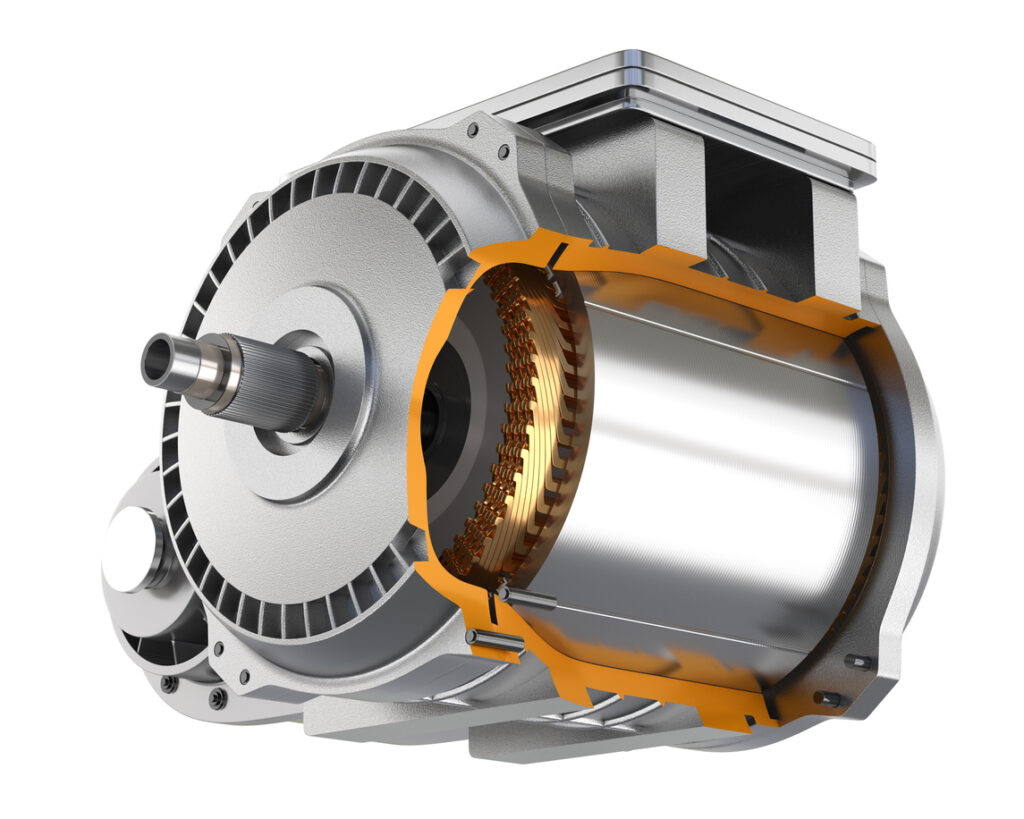
Lean engineering, procurement and Industry 4.0
As mentioned above, in today’s IIoT-Industry 4.0 world, manufacturers must manage time, costs and efficiencies to remain competitive. Every facet of communication in lean engineering technology, CAD, CAM, PLM, ERP and supply chain software must be unified. Each plays a critical role in streamlining processes to improve design efficiency and critical manufacturing procedures. And in the collective of it all, the Industrial Internet of Things (IIoT) demands a massive influx of data from these platforms. Yet, with these challenges come opportunities to improve operational excellence and workflow automation.
In practice, the Industrial IoT helps configure, manage and monitor devices used in manufacturing operations. And up the food chain are the design, selection and procurement of parts and components needed for IIoT practitioners to do their jobs efficiently. Smart technology begins at the source of the design, and supply chain management software assists in product development, sourcing, production and logistics by automating operations. This helps factory operators optimize resources and improve product quality by automating tasks and generating valuable data. All of which relies on the initial design phase to create efficiencies and profitable outcomes.
Conclusion
There are many challenges in searching for parts, designing components and maintaining procurement efficiencies when working with disparate software. Often, out of frustration, a design engineer or buyer may succumb to maverick buying. Maverick buying is when an employee purchases goods, parts or materials for a project, going outside of the accepted buying channels of their organization, potentially ending up with duplicate parts and cost overruns. In addition, ignoring proper CAD standards and software classifications will impede engineering efficiency and parts management.
But it’s not all gloom and doom. There are solutions that can alleviate the challenges and difficulties in engineering and procurement. Highly innovative 3D shape and attribute search tools can enable users to find internal CAD data from multiple business systems and navigate trillions of supplier parts from digital libraries in the CAD software.
Many mobile tools also help design engineers, product managers and procurement navigate software from anywhere. These include mobile product catalogs, product configurator mobile apps, and 3D CAD models mobile apps, all allowing for powerful search and social sharing.
About the author
Adam Beck is the Director of Marketing at CADENAS PARTsolutions. He is a marketing graduate from the Miami University, Farmer School of Business in Oxford Ohio. Adam has years of experience in marketing and design for various industries.
About CADENAS PARTsolutions
CADENAS PARTsolutions is a Siemens Digital Industries Software Software and Technology Partner. Software and Technology partners are leaders in their domain and leverage the open Xcelerator portfolio to provide customers with a comprehensive set of integrated solutions.