How to conduct off-line programming for event-based simulation
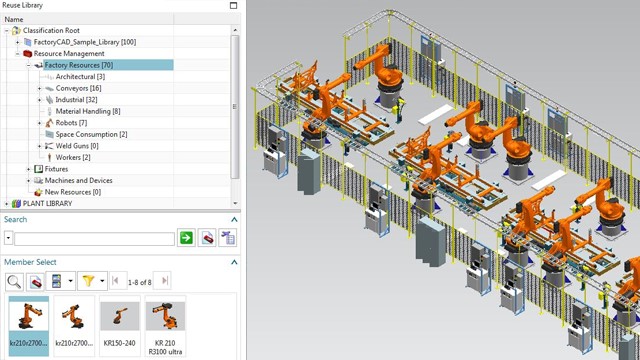
Whenever a manufacturer makes changes on the production line for current or upcoming products, all production must stop so the technicians and engineers can make changes to the industrial equipment and robotic operations for the new requirements. This has been the way from the beginning of the automated industry and amplified in today’s fast-paced production environment. Every couple of years, we experience a new model or a facelift that must be implemented on the same line. It’s not an easy process.
Of course, there have always been solutions to aid this engineering endeavor from computer-aided design (CAD) software that evolved into specialized tools such as Robcad and, lately Process Simulate. And for the past 10-15 years, there was a lot of progress made to validate robotic operations digitally. More and more integrators have seen the benefits of using tools such as Process Simulate rather than program the robot trajectory directly on-site, point-by-point, using the teach pendant. The new method has introduced time savings for on-site operations, better optimized robotic paths, and a much safer overall production environment.
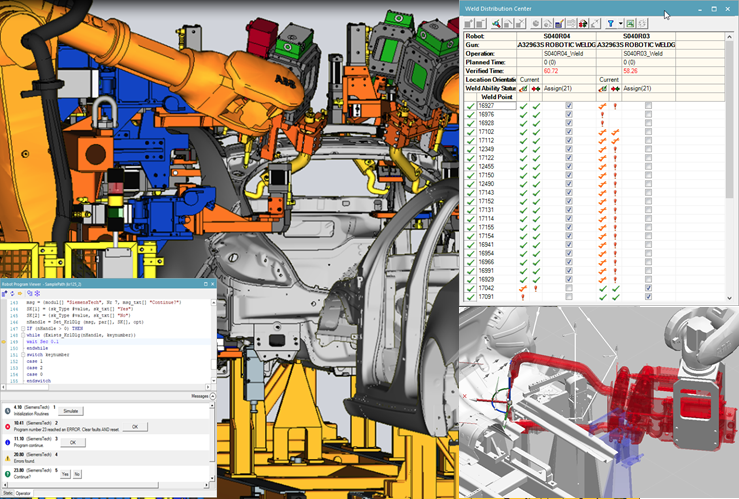
What is the next step?
From the collective experience of our engineers, we noticed that a lot of integrators value the idea of the digital twin and understand the benefits of digital validation. Interestingly, they rarely validate the simulation in an event-based manner.
Using Process Simulate, we can run the study in the Line Simulation mode that enables us to use signals in the exact way we would use them on-site. It also includes robot modules, parallel tasks and custom commands. We can not only recreate the precise motion of the robot, but also implement, test and validate the logic side of the robotic operation.
These are some of the following scenarios where an event-based simulation is useful:
- Robots interference – This is maybe the most common scenario that must be validated before the on-site installation. In Process Simulate, we can easily see the interference zone, so we have a very educated understating of what the best solution is to avoid collisions
- Area request when working with other equipment
- Communication with toolings and PLC
- Safety scenarios, especially in areas where human operators are involved
- Implement, test and validate complex programming structures
- Significantly reduce the time spent on-site for robot setup and programming
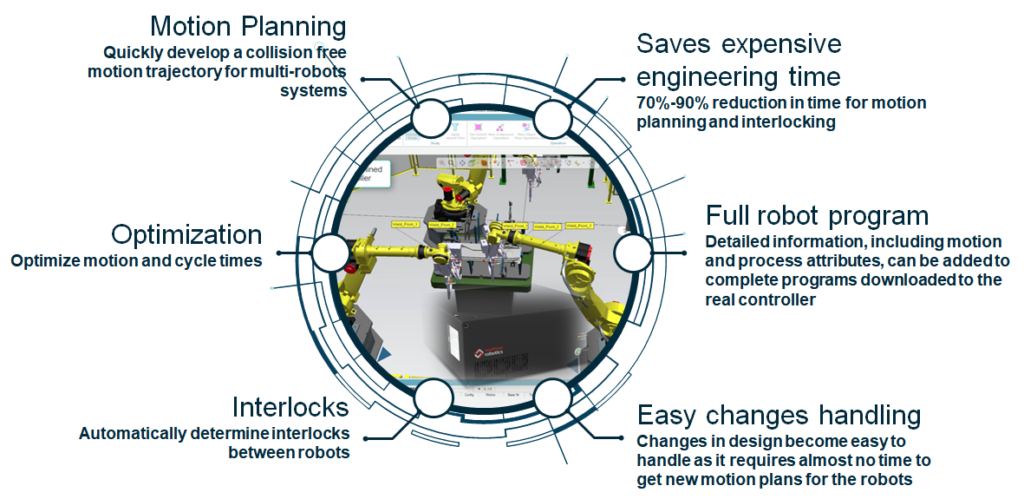
As part of our efforts to bring new light to the event-based simulation, we prepared a video to better present the ease of use and benefits of an event-based workflow.
Want to know how Process Simulate can integrate better with other engineering departments? Check out our article on Teamcenter Manufacturing
Contributors: Alex Dinca, Alex Ioanitescu, and Endre Szucs are digitalization specialists at ADA Computers, a Siemens Digital Industries Software Smart Expert partner in Romania specializing in NX for Manufacturing and NX for Design.