How virtual commissioning has redefined automation’s customer/supplier relationship
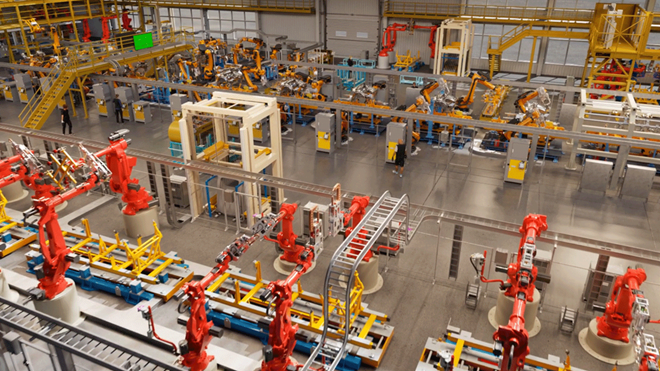
“We assume that when we go on-site to commission a new production system, we’ll need to spend weeks tinkering with it.” These are the words of many machine builders and systems integrators today, even if they aren’t always said out loud. The industry simply assumes that automation systems are too complex to nail on the first try, and a certain level of tweaking post-install will always be necessary.
But this tinkering stage represents a major inefficiency to OEMs who want true turnkey systems from the moment of installation. And this is exactly why over the past year, our team of experts at Longterm Technology Services has seen an explosion in OEMs mandating virtual factory acceptance testing (FAT) and virtual commissioning to their suppliers, specifically by using Tecnomatix Process Simulate from Siemens Digital Industries Software.
What is virtual factory acceptance testing?
Virtual FAT is exactly what the name implies. It comprises the activities normally associated with on-site factory acceptance testing, but these activities are performed on a digital twin of the planned production system.
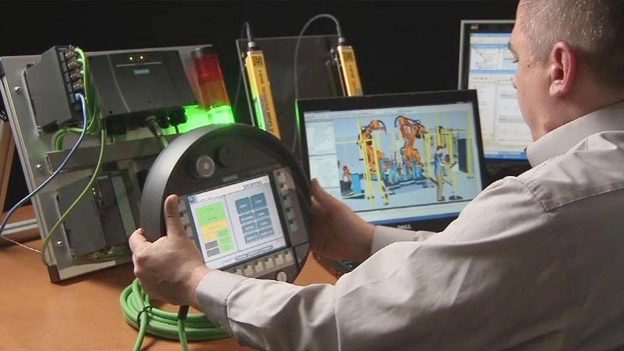
In essence, OEMs want their suppliers to create full simulations of their automation systems in a 3D environment. These twins not only need to simulate the mechanical and electrical behavior of real systems but also need to be driven using the true production-ready robot programs and control logic, complete with finalized hardware configuration. This digital twin or “virtual commissioning study” is delivered to the OEM before the real system is built and installed. This allows the customer to have their internal team run the simulated production system through all its production variants to simulate real-world behavior using finished robot programs, control logic, hardware configurations, and mechanical/electrical behavior. In other words, the supplier is no longer delivering a simulation, but a simulator for the planned system.
Why Tecnomatix Process Simulate?
So why are OEMs asking suppliers to use Tecnomatix Process Simulate specifically? Because this software can do far more than any other solution on the market, which is essential for OEMs looking to future-proof their investment in this new technology. Some solutions can provide robotic OLP, while others can provide virtual commissioning. But these solutions can’t also provide full digital human modeling for ergonomics studies. They can’t use virtual commissioning to control fleets of AGVs. They can’t use AI to automatically generate collision-free robot paths on the fly. They can’t simulate paint thickness and coverage areas for industrial painting applications. They can’t import point cloud data for brownfield applications. The list goes on…
Immediate Benefits
One can see right away how virtual commissioning would benefit the customer with additional layers of control and transparency in all their automation projects. During project design reviews, the customer can ask to see their supplier’s progress on the digital twin and can watch this system being driven by true robot programs, control logic, safety tags, and hardware configurations. In an age of emulated hardware through solutions like Siemens TIA Portal and PLCSim Advanced, suppliers can complete full projects without ever laying hands on real controls or robotics hardware until the moment of on-site installation.
Once the project enters virtual FAT, the customer can use the digital twins to spot any mechanical, electrical, or controls issues in their system and report these issues back to the supplier. In a traditional approach, the system would already be installed on the factory floor before these types of problems would be caught. The image below provides an idea of how the virtual commissioning approach eliminates risks to the project’s timeline and capital expenses by introducing added layers of control and predictability.
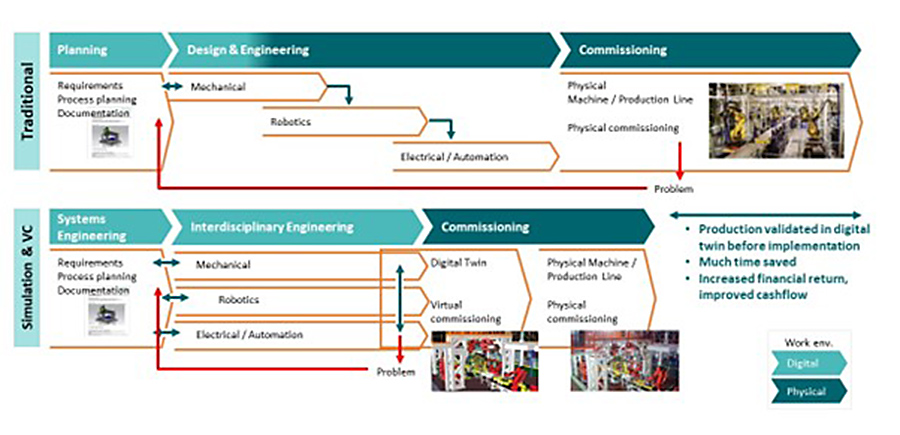
Long-term Benefits
As appealing as the immediate benefits of virtual FAT might be, it’s the long-term benefits that are attracting OEMs to this approach at a growing rate.
Let’s say you’re an OEM that receives a digital twin of every new production system you implement. Over time, you build up a library of these digital twins. As part of your virtual FAT, you also ask your suppliers to calibrate these digital twins against the finished real-world automation systems. Now you’ve established a growing library of 3D automation systems that you know are perfect 1-to-1 matches with the systems installed on your factory floor. With this library in hand, you can reprogram or repurpose any of those systems (or their individual components) for future projects without going anywhere near the physical systems. You can even check the performance of these systems and debug in real-time using only the digital twin. This is where the OEMs will continue to benefit from virtual commissioning long after their supplier has delivered a machine or system. This move toward full-scale factory digital twinning is already happening. Just look at this real factory digital twin that has been created through a partnership between Siemens Digital Industries Software and Nvidia.
Where We Are Today
Digital twinning and virtual commissioning are no longer the future of industrial automation. They are already here.
While digital twinning and virtual commissioning might have been occasionally required of Tier 1 suppliers five years ago, they are now regularly required in contracts down through tier 2 and 3 suppliers. This is because the benefits to the customer have become overwhelming, and difficult lead times on hardware have made it necessary for suppliers to carry out entire automation projects without ever touching real hardware up to the point of on-site system commissioning.
Of course, this trend toward virtual commissioning has many benefits for automation suppliers as well, which is why many leading machine builders and integrators adopted virtual commissioning long before it was a customer-driven requirement. But the acceleration of this trend has undoubtedly increased as a result of OEMs mandating it. Any doubt about the inevitability of virtual commissioning in industrial automation was erased at a recent event at the LIFT Facility in downtown Detroit. Hosted in partnership between Longterm Technology Services and Siemens Digital Industries Software, this event saw representatives from dozens of automation companies from across North America visit to see virtual commissioning performed up-close using Tecnomatix Process Simulate. And the number one reason people said they were attending? Because their customers had demanded they start using Tecnomatix to perform virtual commissioning.
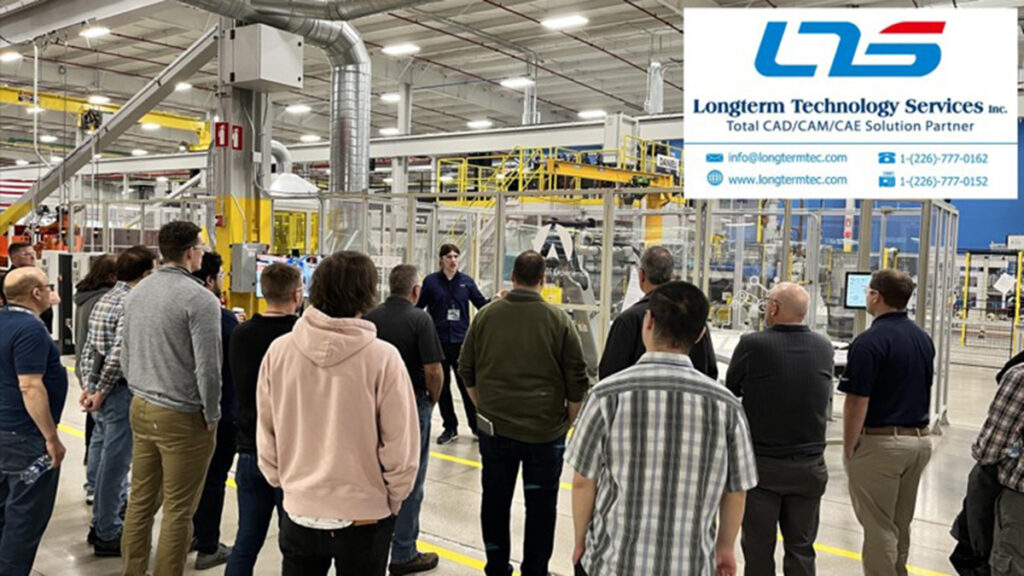
The trend toward virtual commissioning has now travelled well along the technology adoption curve, with the industry’s Innovators and Early Adopters having already used this technology for over a decade. What OEM requirements have done is rapidly push this technology through the Early Majority of suppliers and into the stages of late adoption. By now, any company adopting virtual commissioning is on the latter end of the curve.
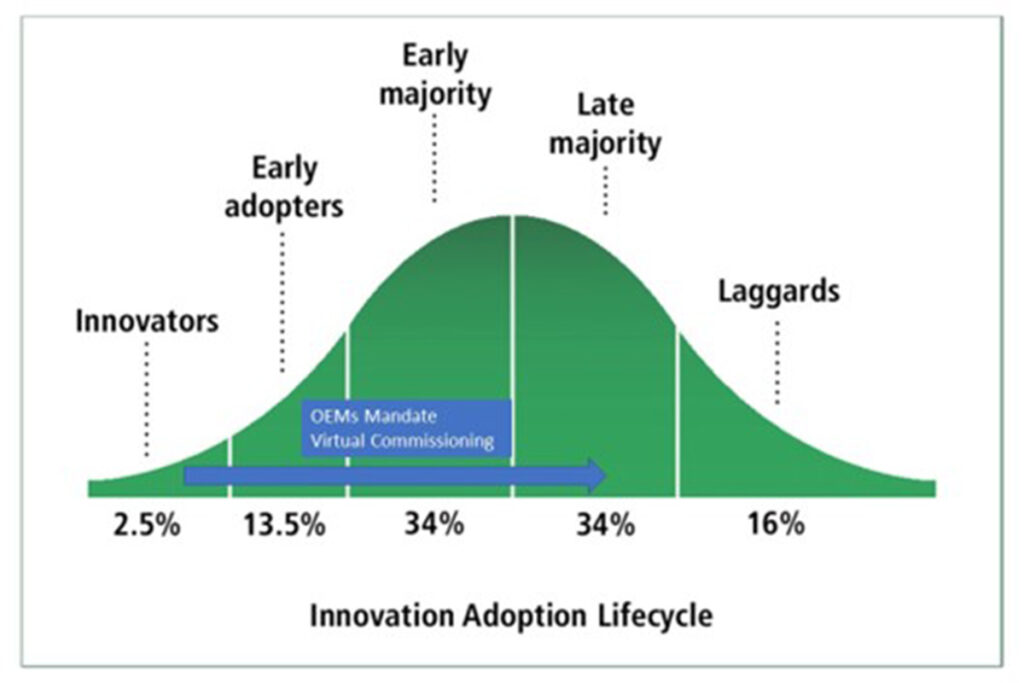
Once this stage is complete, the only group remaining will be the laggards, who will not adopt virtual commissioning until customers and market forces truly force them to.
Next Steps
If you are interested in learning more about how your team can invest in virtual commissioning using Tecnomatix Process Simulate, reach out to our team of experts at Longterm Technology Services. We are deeply experienced in helping companies purchase, implement, train on, and use this technology to its fullest potential.
About the author
Phil Glennie, Ph.D. is the Director of Marketing and Sales at Longterm Technology Services. Over his career, he has worked extensively in the world of enterprise software, including ERP, APS, and PLM solutions. He is dedicated to helping companies of all sizes take their next step forward in Industry 4.0.
About LTS
Longterm Technology Services based in London, Ontario, Canada, and Troy, Michigan, USA, is a recognized Siemens Expert Partner with over twenty years of deep experience helping companies supercharge their products and processes with Siemens Digital Industries Software.