Adapt to Design – Design for manufacturing
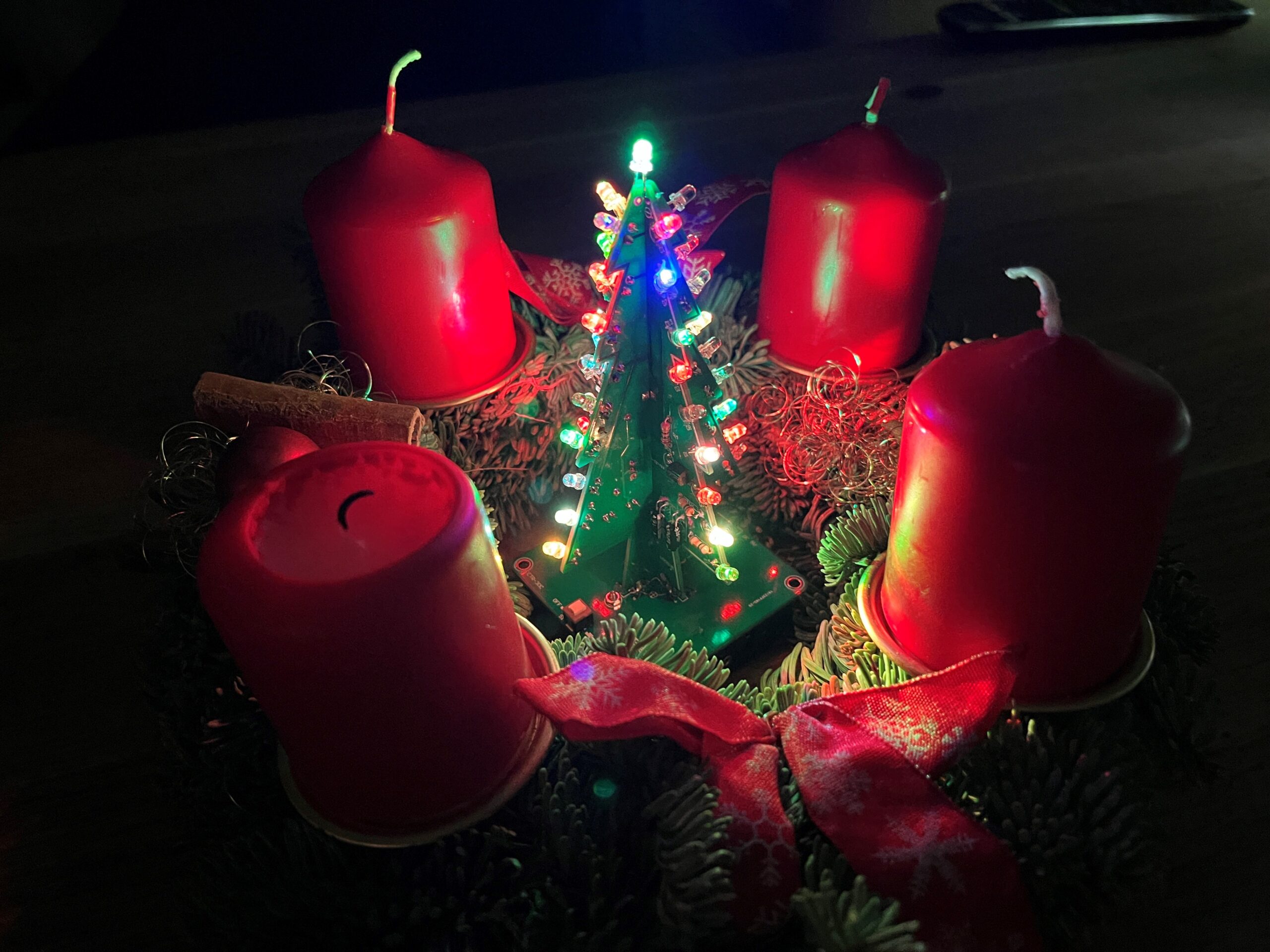
Design for manufacturing, or DFM, is a crucial aspect of electronics manufacturing best practices. It emphasizes that each printed circuit board assembly (PCBA) should be designed to facilitate optimal production. Manufacturers often favor rectangle boards, standard surface-mount device (SMD) components, and single-sided assembly. Essentially, while the external appearance of the final product may be impressive, the internal PCBA might seem less glamorous.
As Christmas approaches, I opted to engage in a project with my son. I acquired a DIY Christmas Tree Kit and commenced the manual assembly. This endeavor triggered a nostalgic leap of over 20 years to when I undertook a similar project. At that time, my soldering instructor, Mr. Alexandru Lesnic, although unaware of IPC standards, imparted a memorable lesson: “Fill the hole with solder and make sure I spot the reflection of my haircut!” (a challenging task given his baldness). I now grasp the criteria for approving electronics assemblies and the significance behind that directive, along with several other valuable pieces of advice he shared.

Although my son’s interest waned within minutes of our project, it was reignited when the Christmas tree was completed, and the LEDs began to illuminate. While engaged alone in the manual assembly, I contemplated the potential for mass production of this project. The current PCB outline poses inefficiencies for panel utilization in large-scale manufacturing, resulting in considerable waste. Although transitioning to surface-mounted devices (SMDs) would be an improvement, the SMT assembly line’s efficiency is hindered by low component density. This implies the necessity of fabricating large panels while ensuring that the bottleneck in the process lies in the pick-and-place step. To address this, enhancing panel stability through additional connection joints between PCBs is necessary, albeit at the cost of a longer cycle time for the separation process.
Can be a more efficient solution redesigning the PCB into a rectangle and arranging the LEDs in the shape of a Christmas tree? Doing this, the beauty of this design will be compromised.


Occasionally, prioritizing product design takes precedence over manufacturing efficiency. Let’s assist creators in introducing aesthetically pleasing products to the market by maintaining the original design during production. Even when striving to replicate the boards precisely as designed, conducting a Design for Manufacturing (DFM) analysis remains essential. This involves identifying layout mistakes and making informed decisions about acceptance, as unforeseen issues can have repercussions later.
We aid you in crafting effective DFM profiles using PCBflow, ensuring a smooth fabrication process without compromising the integrity of the design.