KineoWorks Version 8.0 Highlights
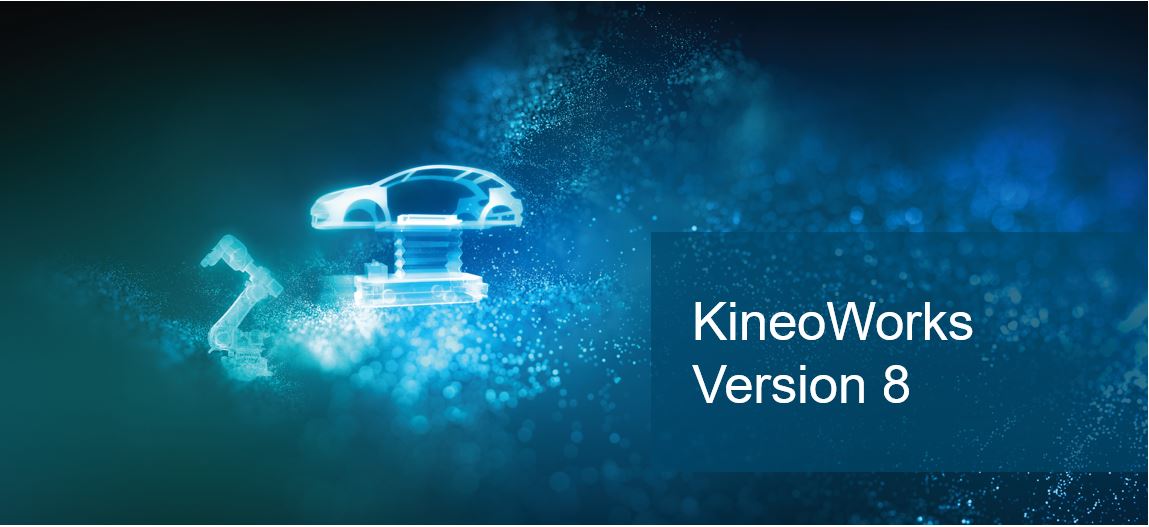
KineoWorks is a software component that automatically computes collision-free motion, solving complex path-planning problems in applications such as robot simulation/control and virtual assembly/disassembly verification. KineoWorks version 8 includes the following enhancements :
Trajectories
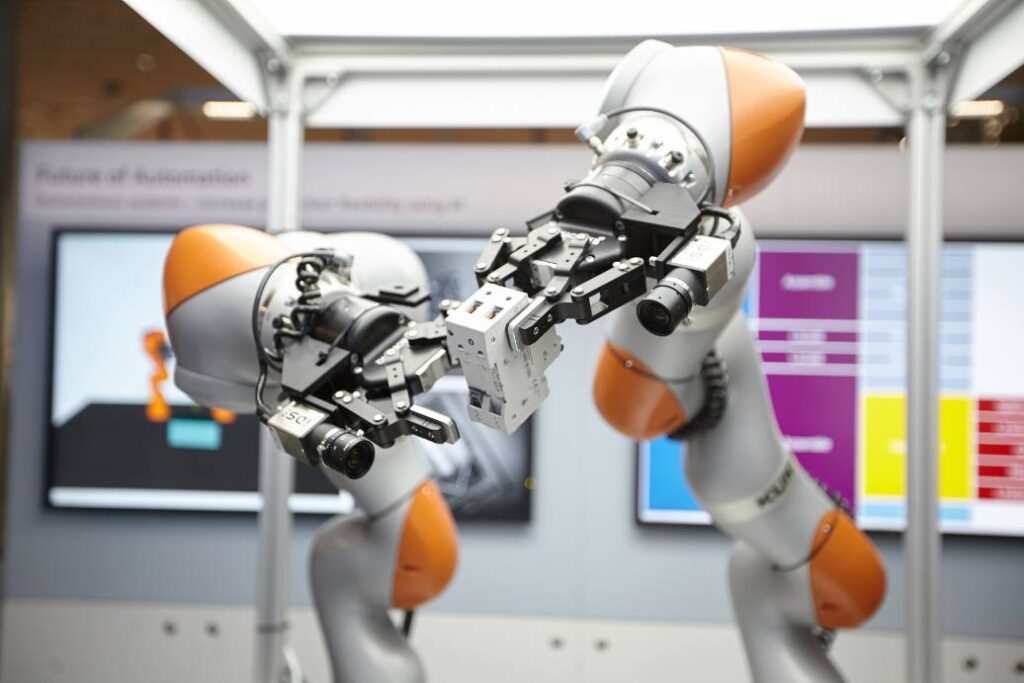
New Motion Planner :
Robot motion is described using trajectories that comprise the positions, velocities and accelerations of the moving components as a function of time.
KineoWorks’ path-planning solution generates a collision-free route between positions in space which is not a function of time, so the resulting output is not immediately suited to simulating or controlling robots.
In order to deliver effective motion planning in robotics, the collision-free path must be transformed into a suitable trajectory so that operational velocities and accelerations can be taken into account. KineoWorks version 8 now includes a new Motion Planner that automates the transformation of collision-free paths into a wide range of trajectories suitable for industrial robotics, including :
- RCS trajectories : A robot vendor’s proprietary motion control software is called a Robot Controller System (RCS). This module can be used to plan and simulate the robot’s trajectories in a virtual environment using a standard RRS (Realistic Robot Simulation) interface. KineoWorks can now interact with an RCS-RSS simulation to compute trajectories that are directly compatible with the robot.
- Cubic spline trajectories : KineoWorks can generate a cubic spline trajectory. This follows a piecewise third-order polynomial path that guarantees the continuity of speed and acceleration at each point in the path. The trajectory can be optimized to minimize cycle time.
Standard 7-DOF robot trajectories
KineoWorks includes it own RCS module which makes it possible to evaluate robot controller trajectories independently of a vendor’s RCS module. Version 8 adds support for standard 7-DOF robots. These robots typically comprise seven revolute joints in series to emulate the motion that can be achived using the shoulder, elbow and wrist in combination. Furthermore, these trajectories can be optimized for cycle-time or energy consumption criteria.
New path optimization
Version 8 introduces a new option to optimize paths by minimizing waypoints. When a collision-free path is computed for a given object or system, the path is comprised of series of intermediate configurations, or waypoints, through which the object/system moves between its initial configuration and and target configuration. In some industrial applications, it’s desirable to reduce the number of waypoints in a path, although this can come at the cost of increasing the overall path length. With KineoWorks version 8, it’s now possible to recompute paths to reduce the number of waypoints. The trade-off in path length can be capped to optimize the path according to the application’s requirements.
API enhancements
Simplified coding of complex path-planning problems :
The Application Programming Interfaces (APIs) for solving complex path-planning problems have been simplified to accelerate the implementation of this advanced functionality. An example of a complex path-planning problem is sequence optimization.
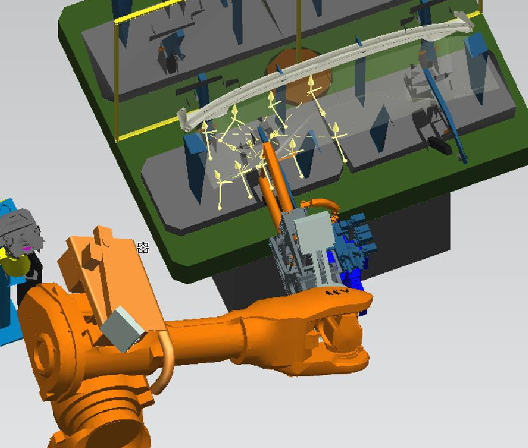
Consider a welding tool which should weld a series of unordered points in such a way that the distance traveled by the tool during the welding cycle is minimized.
KineoWorks solves this problem by computing a collison-free path that reorders the weld positions to minimize the total distance travelled, while integrating these results with the pre-defined (ordered) positions of the tool outside each weld cycle.
Complex path-planning problems such as these will now be easier for developers to code using the simplified API structures.
Robot API improvements :
The API for creating robots has been enhanced to simplify the process and deliver a better user experience through new and improved functions that enable the creation of standard 6-DOF and 7-DOF robots.
Inverse Kinematics API improvements :
Inverse kinematics (IK) may be used to compute a robot’s configuration based on a target position for the Tool Centre Point (TCP). The Inverse Kinematics API has been improved in version 8.0 making it easier to register, diagnose and apply appropriate IK algortihms.
Support for new platforms
KineoWorks is now available for Debian Linux platforms. Supported versions include Debian 10 “Buster” and Debian 9 “Stretch”.
Microsoft Visual Studio 2019 has been newly added as a supported development environment.
Further information
Please contact the author for further information about KineoWorks version 8