Parasolid Data Exchange
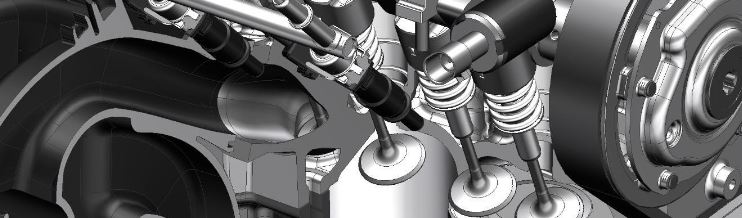
Designers, engineers and manufacturers deploy a wide range of different systems for product modeling, simulation and manufacture, often using different 3D data formats. Application developers need to ensure that users can exchange and re-use data from their applications throughout the product lifecycle and across the supply chain.
Parasolid customers enjoy interoperability with both Parasolid-based and non-Parasolid-based applications. This is due to the widespread adoption of Parasolid as a result of our open business model, together with a wide range of solutions for data import, export and optimization.
Translation-free interoperability using the widespread Parasolid XT format
Parasolid models use the open, published Parasolid XT data format. Parasolid is integrated into more than 350 applications, spanning the CAD, CAM, CAE and AEC domains. As a result, Parasolid XT is a dominant format for representing, storing and sharing 3D digital products.
The Parasolid XT format provides translation-free interoperability between all Parasolid-based applications. Two-way Parasolid version compatibility enables exchange of data between applications based on different versions of Parasolid.
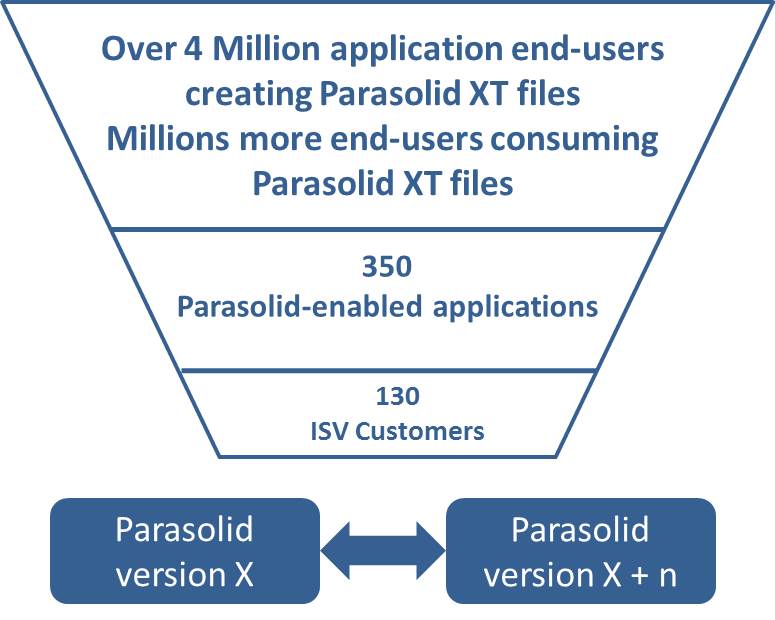
Interoperability with other data formats
To enable interoperability with applications that aren’t based on Parasolid, Siemens PLM Software and its partner, Tech Soft 3D, offer Parasolid customers a range of solutions for importing and exporting other data formats.
HOOPS Exchange
HOOPS Exchange provides a comprehensive solution for Parasolid-based applications that need to read/write a wide range of both proprietary and standard 3D data formats. A tight integration with Parasolid enables perfect import of Parasolid-based CAD formats without translation, while other CAD formats are translated into valid Parasolid models.
- Imports all major mechanical CAD formats
- Imports Parasolid-based formats from NXTM software, Solid Edge® software and SolidWorks® software without translation
- Translates non-Parasolid formats into valid Parasolid models
- Repairs invalid data such as inconsistent tolerances and geometric discontinuities
- Provides comprehensive programmatic access to data associative to Parasolid geometry: assembly/configuration, tessellated data, model structures, Product Manufacturing Information (PMI) in both visual and semantic forms, metadata and views
- Exports to standard file formats including IGES and STEP
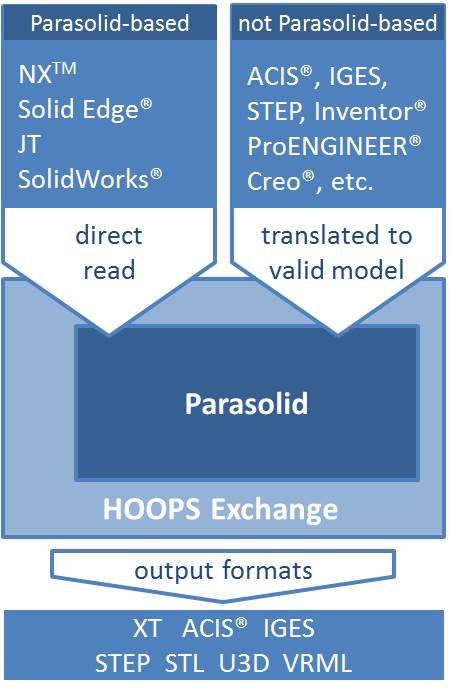
Parasolid Single Format (Point-to-Point) Translators
For more specific data exchange requirements, dedicated single format translators are available to software developers as Parasolid add-ons. These geometry-focussed translator toolkits enable high speed, end-to-end translation between Parasolid and the following industry formats:
Format | Read (to XT) | Write (from XT) |
STEP | AP203, AP214, AP242 | AP203, AP214, AP242 |
IGES | up to 5.3 | up to 5.3 |
ACIS® (SAT) | up to R24 | up to R24 |
Parasolid – intrinsically designed for interoperability
The data exchange solutions described above take advantage of intrinsic Parasolid functionality for optimizing data import and export. Parasolid customers can use this functionality to work with translated data in their CAD/CAM/CAE applications, or to develop dedicated translator solutions.
B-rep import/export | Parasolid provides functions for creating valid models from import data that has boundary-representation data structures – topological and geometric data, typically associated with solids-based modelers. |
Trimmed surface import/export | Parasolid accepts and exports geometric data in trimmed B-spline form. This supports representations from surfaces-based modelers. |
Tolerant modeling | Models imported from other applications may be less accurate (use lower precision) compared with the high-accuracy models created in Parasolid. As a result, errors may become apparent in the imported model, for example, gaps arising between edges that would be considered coincident in the lower accuracy modeler. Parasolid uses Tolerant Modeling to accommodate low resolution data by applying local tolerance information. This enables downstream modeling operations to proceed without errors arising due to the inaccuracy of the imported data. |
Unsupported geometry types | Third-party applications may create geometric data that is not supported in Parasolid, for example, proprietary surface types. In such cases, Parasolid maps the unsupported geometry to a corresponding B-surface or B-curve to support downstream modeling operations. |
Geometry repair | Parasolid includes functions for finding and repairing problems, such as self-intersecting curves and surfaces. |
Parasolid Communicator
Some applications need to consume precise Parasolid model data, without requiring sophisticated model creation and editing capabilities. In such cases, Parasolid Communicator provides a foundation level capability for Parasolid XT interoperability, visualization and interrogation. The following tools are available:
- Read/write of native Parasolid XT files.
- B-rep import and trimmed surface import/export
- Geometry repair tools for imported data
- Geometry creation – for 3D primitives, B-splines, …
- Topological and geometric evaluations and inquiries
- Calculation of mass properties, minimum and maximum distance and collision detection
- Non-destructive sectioning, graphical output and faceting/meshing
Parasolid Bodyshop – advanced data repair and optimization
However you decide to import geometry into Parasolid, there is the possibility that the model data is problematic due to low quality source data, for example. Parasolid Bodyshopis an optional add-on for Parasolid. This toolkit provides software developers with advanced tools for repairing and optimizing more problematic import data. HOOPS Exchange includes and automatically takes advantage of the Parasolid Bodyshop library to heal imported data.
Tools | Function |
Pre-processing | Geometry clean-up , e.g. removing coincident curves , closing gaps, … |
Model healing | Model healing , e.g. dealing with missing edges, aligning edges to faces, … |
Post-processing | Model optimization , e.g. simplifying complex surface types to analytic equivalents, restoring accuracy to tolerant edges , etc. |