Kineo Flexible Cables – benefits for robotics automation
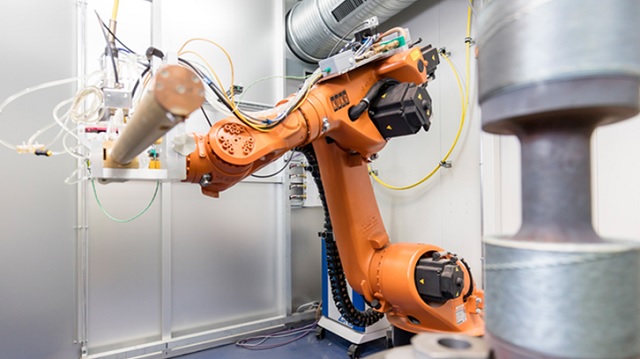
We recently announced the launch of Kineo Flexible Cables, a new software component for modeling cable routing and performance. Here we take a closer look at its target application in robotics simulation.
Pneumatic and electrical cables in robotic systems may perform millions of flexing and twisting cycles throughout their lifetime. Choosing the correct cable configurations during the design stage is critical to extending their life on the factory floor. Cables need to be long enough to connect effectively, without surplus cable causing damage in the operating environment, or being subject to damage itself. The choice of cable also needs to withstand the operating stress inherent to complex and repetitive robot motion.
Users of Kineo Flexible Cables can model the behavior of cable configurations in a virtual prototype. Users define a range of different cables parameters, such as length, radius, density, stiffness and fixing points. A fast physics-based solver computes changes in the cable configuration during motion cycles, with simulation scaling in real-time for multiple cables. Forces like inertia and gravity are taken into account so that cable oscillations can be realistically modeled. Users can also measure the internal stress that is imparted on a cable to understand the forces of flexion and torsion that the cable will need to endure in the real world. With integral collision detection, cable clashes with the working environment can be anticipated.
Some of these capabilities can be seen in the video below. This shows an implementation of Kineo Flexible Cables in Tecnomatix Process Simulate software. In this example, cable simulation is used to track potential collisions in a pick-and-place work cell.
Kineo Flexible Cables has been designed for integration by any robotics OEM or System Integrator to enhance their automation software and provide their manufacturing customers with reduced operational costs.
For more info, please message me, or visit:
Comments
Leave a Reply
You must be logged in to post a comment.
Hello, can you tell me which parameters are used in Process Simulate in the functionality?
Process Simulate’s flexible cable option will support these cable parameters: length, radius, attachment points, stiffness, density and oscillation damping. You can define additional conditions such as maximum tension, maximum twist, minimum radius of curvature and maximum permitted contact force. The software will simulate cable motion/deformation according to these parameters, while taking account of collisions in the environment (such as coiling around the robot arm).