Parasolid enables SimScale to integrate geometric modeling with cloud-based engineering simulation
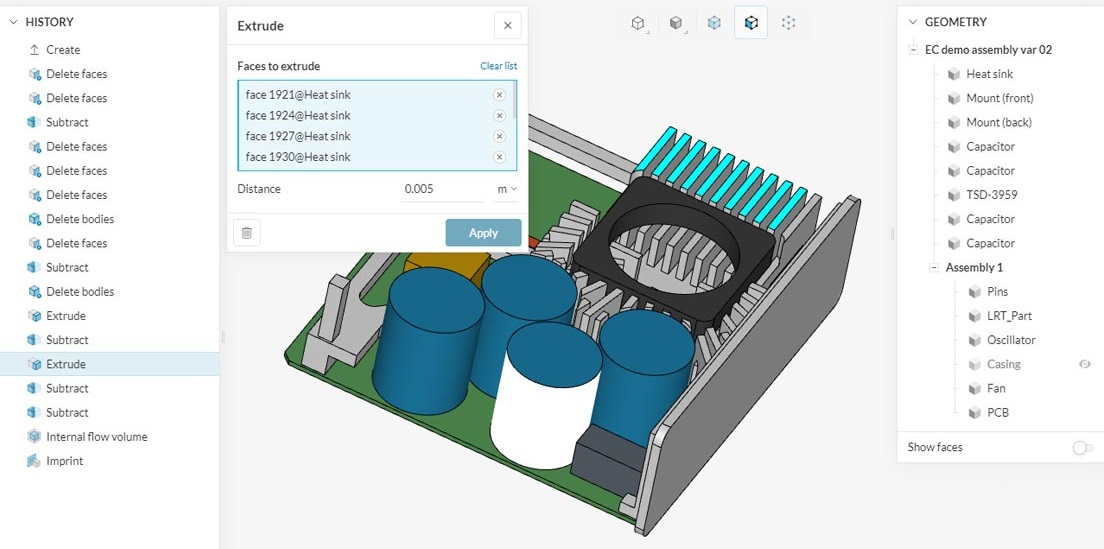
Companies need to validate their product designs early and often in the design and manufacturing cycle as they seek to mitigate the risk of delivering products that are unfit for purpose. Traditionally, this has meant the use of Computer Aided Engineering (CAE) simulation tools with high compute power demands – often presenting a barrier to adoption by smaller businesses. With the increased use of cloud technologies, more companies can access sophisticated product simulation solutions on the desktop.
SimScale has just released CAD Mode, equipping its users with an integrated solution for geometric modeling directly within their engineering simulation platform. I’ve been in contact with Sebastian Guenther, a Product Manager at SimScale, to learn how Parasolid has helped SimScale to deploy the new capability to their users. Here’s what I learned…
Modifying imported CAD models for optimal analysis
SimScale’s CAD editing capabilities leverage Parasolid geometric modeling functions to prepare CAD models for faster and more robust simulation.
CAD models often include small features such as holes, chamfers and blends that have negligible significance for simulation and may be removed or simplified to accelerate analysis. CAD designers often lack the necessary simulation experience that guides them through model preparation. CAD Mode is designed to make that step as simple as possible by providing an intuitive set of operations, avoiding a time-consuming back and forth between different departments.
SimScale’s CAD mode offers this defeaturing capability with the help of Parasolid functions that remove or simplify geometry, while automatically preserving a valid model. CAD Mode also uses Parasolid to endow users with the means to clean up design issues that might otherwise result in simulation errors. For example, by resolving overlapping bodies with Boolean modeling operations, closing sheets to fix missing faces, or extruding parts to close small gaps in the design.
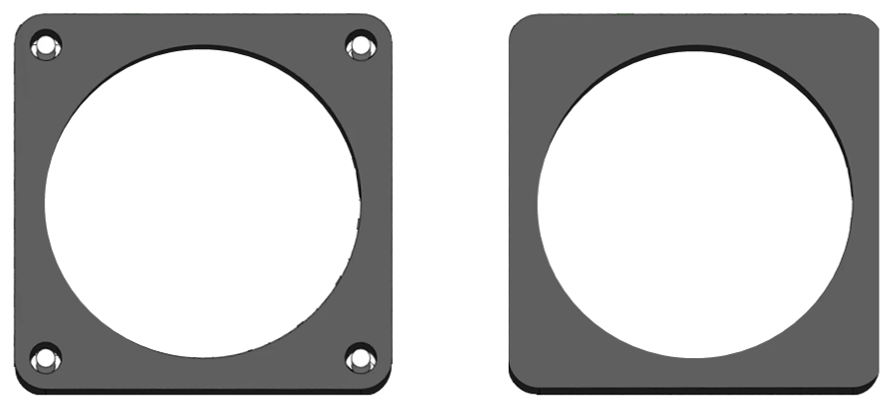
Example of part simplification in pre-processing. Holes have been removed due to their negligible effect on heat transfer through the part
The result is a 3D model that has been honed for rapid, error-free simulation. Further productivity gains are realized by eliminating the need to refer the design back to the authoring CAD system.
CAD Mode introduces additional pre-processing tools that benefit the simulation domains in which the company specializes, including solid mechanics, fluid dynamics and thermodynamics. For example, pre-processing for applications in fluid dynamics is enhanced with CAD Mode’s Flow Volume Extraction tool. You can see a neat application of CAD Mode in clean-up, simplification and flow volume extraction in this video.
CAD Mode and Parasolid Convergent Modeling
SimScale equips more than 200,000 simulation engineers with frictionless browser-based access to CAE tools running on HPC in the cloud. Engineers focus on getting results quickly and efficiently, while SimScale handles both CAE and cloud technologies automatically. One of the important factors in SimScale’s reach is simplifying the first very important simulation step – the ability to import 3D models from the user’s choice of CAD system. SimScale enables this using HOOPS Exchange from TechSoft 3D to offer SimScale users CAD-CAE interoperability via a wide range of industry standard formats like Parasolid XT, as well as proprietary CAD formats.
According to Sebastian, CAD Mode is taking interoperability a step further using Parasolid Convergent Modeling technology which unites previously incompatible facet data representations with solid B-rep models in a unified modeling environment. As a result, CAD Mode enables users to work with their choice of facet and B-rep data format.
Looking Ahead
SimScale plans to offer additional tools and automation for CAD clean-up and intelligent simplification. For the longer term, the company expects to make more extensive use of Parasolid modeling functions to offer additional design capabilities, for example, in support of design optimization studies. I’m looking forward to seeing the new developments as they roll out.