Electrical Systems podcast (Ep.#5): “Increasing Wire Harness Manufacturing and Profitability”
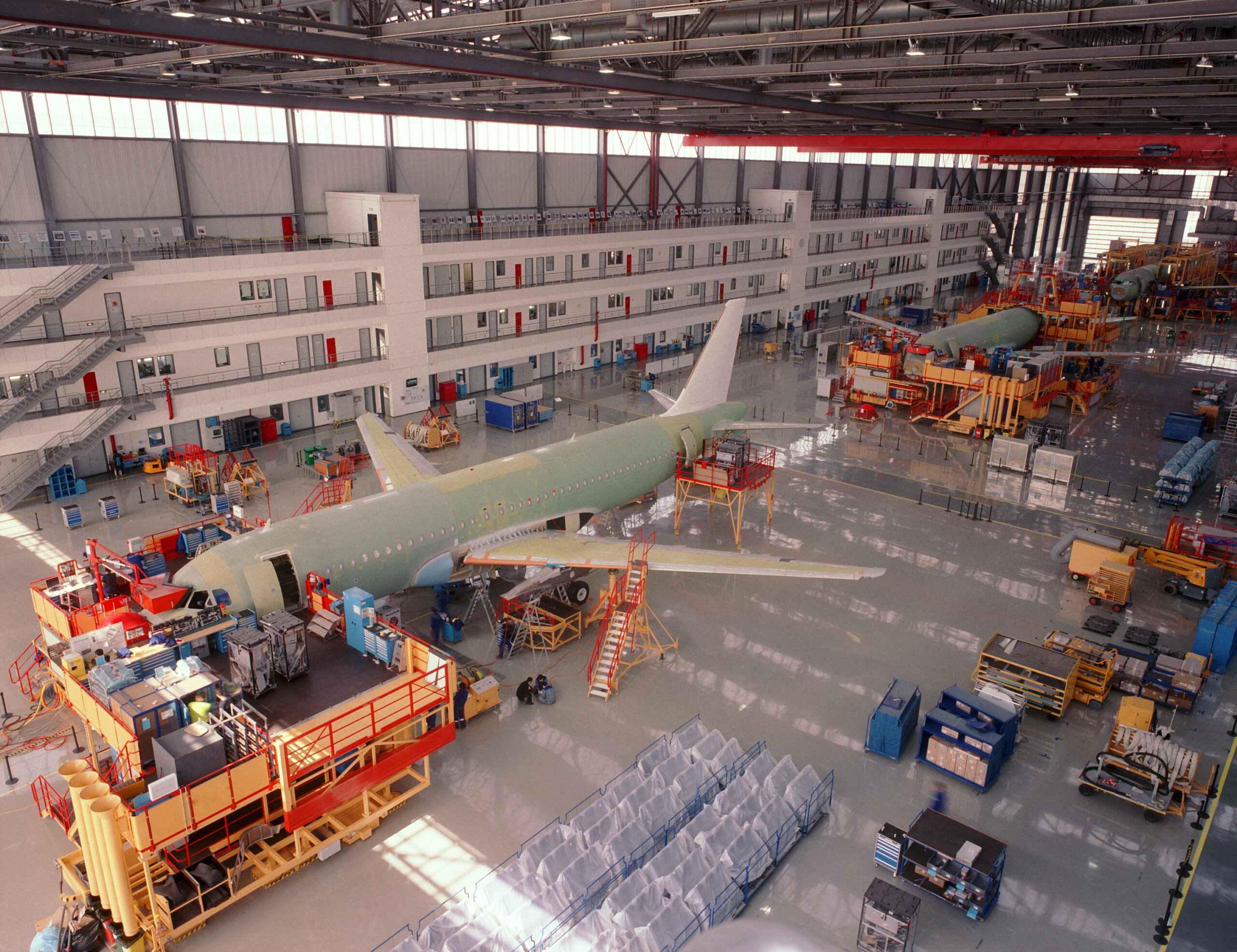
Aerospace wire harness manufacturing is under intense pressure these days.
…Profitability constraints are everywhere.
To make matters worse, increased electrification of a platform has taken harness complexity to perplexing new heights. There’s the constant demand to rapidly transition design changes into production. And let’s not forget customers who expect lower cost assemblies delivered faster, just in time.
This episode, “Increasing Wire Harness Manufacturing and Profitability” discusses what it takes in today’s environment to design, build and install a modern-day wire harness assembly. The podcast addresses the trends impacting manufacturing and how a digitalized process offers multiple advantages across the entire platform development lifecycle.
Listen to this episode now.
This is episode #5 of a five-part series.
Welcome to Talking Aerospace Today – a podcast for the Aerospace & Defense industry. The place that brings the promise of tomorrow’s technology to the ears of our listeners today.
Whether you’re talking OEM or independent supplier, aerospace wire harness manufacturing is under unprecedented pressure these days. Profitability constraints are everywhere. To make matters worse, increased electrification of a platform has taken harness complexity to perplexing new heights. From the need to rapidly transition design changes into production, to serving demanding customers who expect lower cost assemblies delivered faster just in time, when it comes to wire harness manufacturing the list goes on and on.
I’m your host, Scott Salzwedel, and in our final episode “Increasing wire harness manufacturing and profitability” of the electrical systems podcast series, I’ll be joined by Anthony Nicoli, the Aerospace & Defense Director of Integrated Electrical Systems for Siemens Digital Industries Software. We’ll be discussing what goes into designing, building and installing a wire harness assembly, as well as the trends impacting manufacturing and how a digitalized process offers multiple advantages.
Tune in to learn more about the complexities behind wire harness manufacturing and how to stay profitable during this time of great innovation and intense industry challenges.
In this episode, you will learn:
- Why relying on electrical systems has substantially increased the pressure on OEMs and their suppliers (02:14)
- The increasing need to change traditional manufacturing tools (03:32)
- How OEMs can reduce wire harness manufacturing cost and risk (04:08)
- What it means to have a digitalized process (05:36)
- How a model-based approach is used to address today’s harness manufacturing challenges (06:42)
- The importance of electrical and mechanical co-design (07:34)
- The role digitalization plays in wire harness manufacturing (08:15)
- The benefits of being a Capital customer (09:36)
Connect with Tony:
Resources:
Scott Salzwedel: Hello and welcome! This is Talking Aerospace Today – the podcast for the Aerospace & Defense industry, and the trends that drive the digital enterprise, a place that brings the promise of tomorrow’s technology to the ears of our listeners today.
I’m your host Scott Salzwedel. Welcome to the final episode of our five-part series. In this episode “Increasing Wire Harness Manufacturing and Profitability” we’ll be discussing what goes into designing, building, and installing a wire harness assembly. In this episode, we’ll talk about the trends impacting manufacturing and how a digitalized process offers multiple advantages.
Before we dive into this episode, a reminder that our previous episode covered the challenges of how increased complexity and more integration within an aircraft platform has impacted aircraft compliance and certification. Extremely important stuff. I urge you to give that episode a listen. You’ll find our podcast on iTunes, Spotify, Stitcher, Google, or wherever you go to listen to your favorite podcast. I’m excited to get started!
Whether we’re talking OEM or independent supplier, aerospace harness manufacturing is under more stress than ever. Businesses are suffering from profitability constraints on all sides, from increased harness complexity driven by more electric platforms to the need to rapidly transition design changes into production, to serving demanding customers who expect ever lower cost assemblies delivered just in time, the list goes on and on. So in this episode, I’ll be talking with Tony Nicoli, who is the Aerospace & Defense Director of Integrated Electrical Systems for Siemens Digital Industries Software. Welcome, Tony. Thanks for stopping by!
Tony Nicoli: Hi, Scott. Thanks for having me today!
Scott: The pleasure is all mine, Tony. It’s always great to have you on the podcast. It’s always a lot of fun. Let’s talk about the complexities behind wire harness manufacturing, and how to stay profitable. Tony, I would imagine OEMs and their suppliers are under tremendous pressure to deliver a high-quality product on time and on budget. Why all of a sudden is there so much pressure?
Tony: Well, Scott, you touched on a few of the reasons in your intro, but I’ll go a step further. There is more pressure on manufacturing because things are more electrical these days. This relatively new reliance on electrical systems has substantially increased the risk our programs face, especially as they transition to production. Current processes were developed for a world where most of the functionality was implemented mechanically, including pneumatics and hydraulics. As an industry, we know how to work around late-breaking problems in these disciplines without major program iterations. Now, with electrical front and center and new capability implementation – and this includes networks and software – there was a lot more at stake. A problem discovered in first-article integration or transition to production can mean a major development cycle, potentially costing billions of unexpected dollars. This not only puts the program at risk, its cost and schedule, but also the reputations of the program team, the reputation of the business unit, and in the worst case, the viability of the company itself.
Scott: So, is it safe to say because of increased electrification, some of the more commonly used tools are now obsolete?
Tony: The current tools don’t make things easier, that’s for sure. Generally, state of the art for manufacturing engineering employs manual processes with slow and disconnected toolsets. These processes are time-consuming and expensive. Teams often miss or even introduce errors into manufacturing tooling and work instructions, leaving issues to be found late in the game, even after the manufacturing cycle has begun. This forces expensive design iterations and process changes.
Scott: However, the more sophisticated members of the manufacturing community recognize the need to change.
Tony: Yes, that’s the good news. They are applying digital technologies to transform their business processes. They are already adopting model-based development techniques from concept development through design and into manufacturing. Through a digitalized process, they are able to reduce costs and schedule risk, accelerate production ramp, and improve productivity.
Scott: I was surprised to see in the United States the Department of Defense is totally into the digital enterprise.
Tony: Yes, Scott. Leaders in the United States DoD endorsed the shift to digitally connected design manufacturing. And in the commercial sector, we’re also seeing adoption with very clear benefits. Take the case of the Boeing/Saab T-7A trainer program; it was recently named as the first US Air Force E Series aircraft. By using model-based development techniques, they were able to go from platform concept to first flight in under three years. As Boeing’s Chief Engineer, Paul Niewald said, “We are competing against proven in-production aircraft, so we had to do things differently.” The result? By applying model-based development techniques, the Boeing/Saab team was able to build their confidence to the point where they could bid $10 billion below the US Air Force’s expected lifecycle program cost. They won the program.
Scott: So, you mentioned the digitalized process. Could you give our listeners a description of what you mean by that?
Tony: Sure. Using Capital, design teams build a configuration control digital twin or model of the platform’s electrical system. The manufacturing engineering team uses this electrical digital twin to develop its own digital twin of harness production. They use this to design, plan, and optimize the overall production process. Capital is architected to ensure digital data continuity is maintained as the program moves from phase to phase. It does this using an underlying digital thread. This ensures that information added to the electrical system and harness production models is prevented to the manufacturing engineering and design teams respectively. In this way, both teams work from an authoritative description of the electrical system and are informed of relevant improvements and corrections made by the other. That’s an example of the Siemens digital twin and digital thread when using Capital.
Scott: How do we use a model-based approach to address harness manufacturing challenges?
Tony: Well, Capital has always been a model-based approach to electrical distribution system development. It has recently expanded to support electrical system modeling, electrical system architecture design and optimization, and software network development. We call this new approach the Siemens Capital E/E Systems development environment. It’s been architected to ensure digital data continuity as the program proceeds from phase to phase across different domains. This is accomplished by using an underlying digital thread as I mentioned earlier. The digital thread ensures that information added to the electrical system and harness production models is accurately and contemporaneously presented to the manufacturing engineering teams.
Scott: Yeah, I know electrical and mechanical co-design is extremely important these days.
Tony: Oh yeah, because Capital is part of the Siemens Xcelerator portfolio, it not only connects to related electrical disciplines, but it also extends to the mechanical discipline and to the platform’s product lifecycle and application lifecycle management environments. This allows electrical and mechanical co-design, platform level configuration control and revision control, and the capability to configure the platform across domains and up and down the product development lifecycle.
Scott: We’re getting close to the end of this episode and before we go, can you explain to our listeners the role digitalization plays in wire harness manufacturing? I know there are numerous answers but what comes to mind first?
Tony: As I mentioned earlier, teams can directly access the Capital electrical system digital twin to enable an automated harness manufacturing engineering flow. This requires zero manual data re-entry. Consequently, generating accurate manufacturing aids, tooling, and even cost estimates are second nature. This is important because getting these right enables the manufacturing ramp to go as planned. In a low margin business like harness manufacturing, predictably ramping to high yield is critical to achieving profitability. I’ve known a number of our customers who for some reason or other, missed their yield and efficiency number by as little as 15%, and completely consumed the profit for their entire production run as they recovered. Deriving the manufacturing tooling, work instructions, and other infrastructure directly from known good versions of the harness design, versions that keep up with design changes in real-time is one way to reduce the risk of missing those ramp satisfaction metrics.
Scott: Okay, great! Thanks, Tony. Are there any success stories out there?
Tony: You know, Scott, I can’t really name names because of the nature of our business, but Capital customers are realizing quantitative business and operational benefits by the day. I will say, by fully applying Capital to their electrical design and manufacturing processes, one of our customers was able to reduce harness manufacturing time by 100 hours per bundle. That alone represented a cost savings of nearly 3.5% of the platform’s retail price – a clear example of the power of model-based development that favorably impacts harness manufacturing.
Scott: Well, Tony, our time is just about up. Man, where does the time go? Before we end the show, what snippets of goodness do you want to leave with our listeners?
Tony: Well, it’s a real bummer, Scott, made worse by the fact that it’s the final episode. So, a few points that I’d like to make. A model-based harness manufacturing engineering solution can contribute to retaining and even re-improving a company’s reputation for predictable harness manufacture. Using a comprehensive Electrical and Electronic (E/E) Systems development portfolio from Siemens provides harness manufacturing engineers direct access to a configuration controlled digital twin of the platform’s electrical system. This type of solution accelerates manufacturing engineering, reduces errors, and enables manufacturers to respond dexterously in the face of change. The result? Higher productivity, less scrap, and ultimately, more time for our customers to spend with their families.
Scott: Ah, families… I knew you’re a family man, Tony. All right. That pretty much does it for this show. Thank you so much for spending time with us.
Tony: Thanks, Scott. It was really fun. I really enjoyed our time together.
Scott: And of course, I’d like to extend my deepest thanks to our listeners. Thank you, listeners! I’m glad you tuned into this podcast. Now at the top of the show, I mentioned we’ll be doing a five-part series on the evolution of electrical system design in aerospace. If you enjoyed this episode, our final episode of the series, and want to listen to previous episodes, please check out the links in the podcast description. Be sure to subscribe to Talking Aerospace Today on iTunes, Spotify, or wherever you’re listening right now. That way you won’t miss a single upcoming episode. Our next season is already in production, a five-part series on aerospace innovation in the digital age. So, sign up now.
My name is Scott Salzwedel, and this is Siemens Talking Aerospace Today. I hope you’ll join us again for our next podcast.
Until then, bye for now.
Listen to previous episodes from the electrical systems podcast series “The Evolution of Electrical Design in Aerospace.”
Episode #1 – “The Evolution of Electrical Design in Aerospace”
Episode #2 – “Design Tools and Practices – Past, Present and into the Future”
Episode #3 – “Change Management and the Digital Thread”
Episode #4 – “Addressing Electrical Design Compliance and Certification”
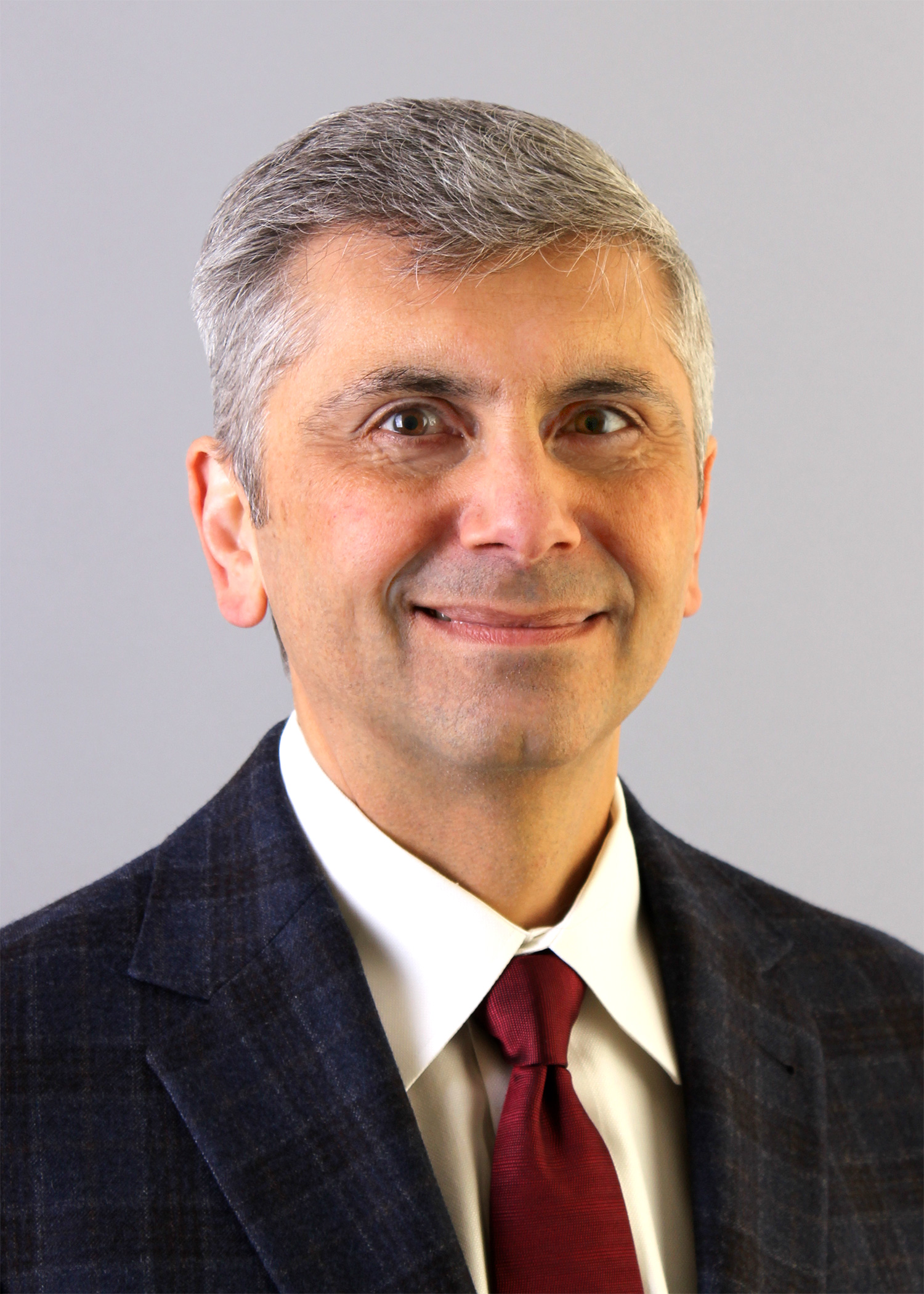
Tony Nicoli – Guest
Anthony Nicoli is the Aerospace and Defense Director for the Integrated Electrical Systems (IES) segment of Siemens Digital Industries Software. He has spent nearly twenty years in the defense industry, developing electro-optic and electro-acoustic systems and businesses, primarily in the tactical missile countermeasure and underwater imaging domains.
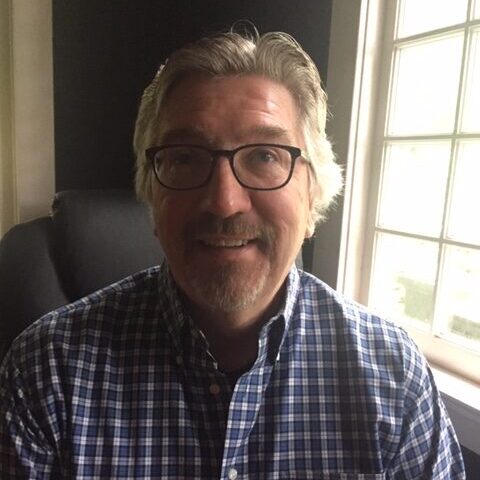
Scott Salzwedel – Host
Scott Salzwedel is senior technical writer and corporate communications writer involved in the Siemens Aerospace & Defense Industry and Siemens Capital. In addition to writer/host of Talking Aerospace Today, Scott is the writer of white papers, articles, blogs, videos and websites at Siemens.
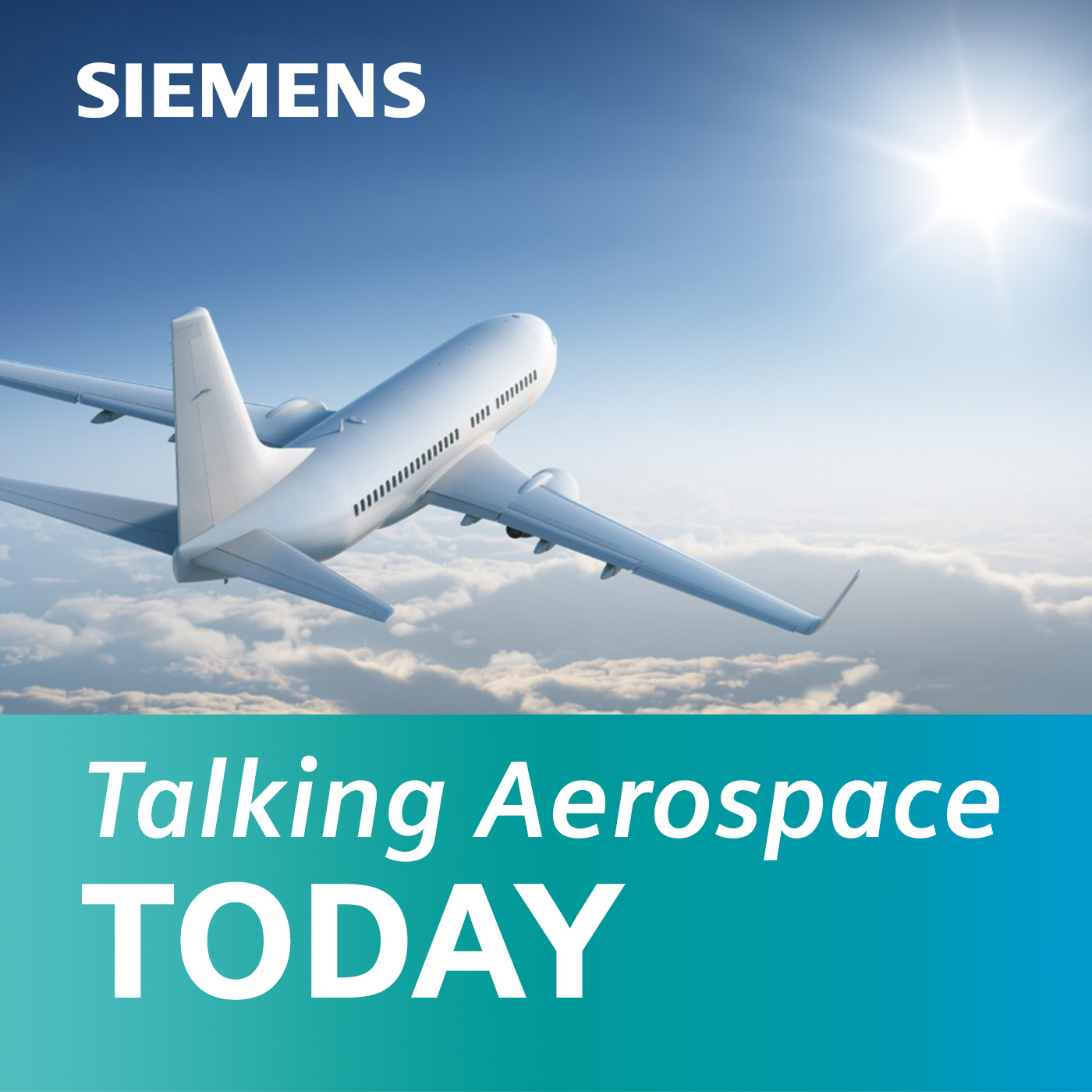
Talking Aerospace Today Podcast
The A&D Industry is at a serious inflection point. Transformation to the digital enterprise has opened up a new era in innovation and technological breakthroughs. However, complexity and compliance continue to hamper the best of efforts.
Join us as we explore how Siemens is turning complexity into a competitive advantage for many of our customers – today and well into tomorrow.