Podcast: The birth of Simcenter (Episode 4)
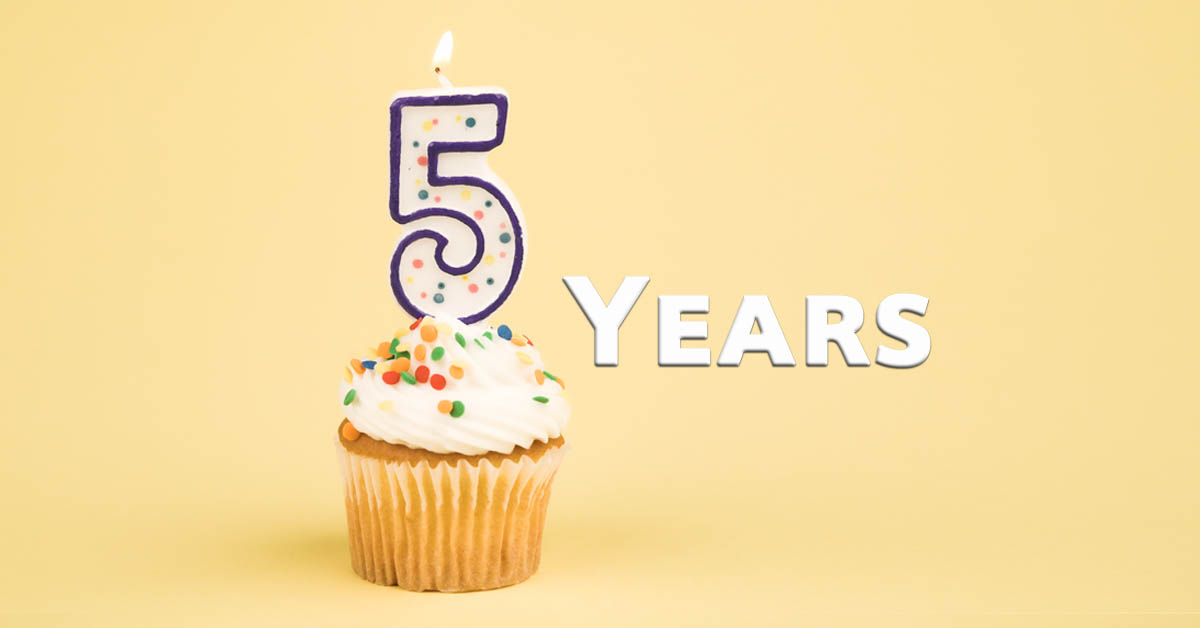
5 Years on ….
When it comes to measuring the passage of time, five years doesn’t seem like a huge amount of time. Unlike decades, which seem to pass very slowly, things that happened “five years ago” seem so close that you can almost touch them.
In this edition of the Engineer Innovation podcast, we step back five years to the birth of Simcenter and explore all of the reasons why the last five years have been some of the most tumultuous in the history of our species.
I’m joined by Jean-Claude Ercolanelli, Siemens’ new Senior Vice President of Simulation and Test. Although Jean-Claude wasn’t quite present at the conception of Simcenter, he was there for the birth, and is now charged with guiding it into the world of adulthood.
Together we explore how Simcenter has helped to solve some of the biggest issues that our species has faced in the past five years. We also discuss the core principles behind the development of Simcenter, which Jean-Claude confidently predicts will allow us to tackle whatever challenges the next five years throws our way.
- The role played by Simcenter in the Tokyo Olympics (06:22)
- How Siemens helps the medical industry in optimizing production (08:21)
- The role that Simcenter will play in the future of the digital twin (12:16)
- How Simcenter is leveraging machine learning and AI to improve the user experience (17:31)
- How Simcenter is helping in the development of autonomous vehicles (22:30)
- Simcenter’s biggest accomplishments in the last five years (24:05)
- A prediction of what the next 5 years hold for Simcenter (29:41)
[00:00] Stephen Ferguson: Today, I’m joined by Jean-Claude Ercolanelli, who’s Siemens’ new Senior Vice President of Simulation and Test. So, this podcast is sort of a birthday party for Simcenter, which has recently celebrated its fifth anniversary. Now, this is kind of a very intimate party, one to which only Jean-Claude and I have been invited. Or perhaps it’s one of those awkward conversations you sometimes have in the kitchen of bad parties only with several hundred podcast listeners eavesdropping on our chat. So, as I understand, Jean-Claude, Simcenter’s official birthday was June 14th, 2016. What do you remember from that time?
[00:33] Jean-Claude Ercolanelli: Well, there’s a lot of things that did happen in 2016. First of all, I think that you may remind yourself that it was a special year for us. It’s when CD-adapco was acquired by Siemens Digital Industries. Well, what I do recall is also a bit of what I was told at the time is that actually the Simcenter was initially meant to be the combination of NX CAE and LMS products. But with the acquisition of CD-adapco by Siemens Digital Industries Software, that quickly expanded into “Hey, let’s make Simcenter the portfolio for all the simulation and test solutions that Siemens is investing in and bringing in.” The team at that time did really a sound and smart decision. I wish, to be honest with you, that I was part of that team, we’ve met it, because I really believe they did an excellent job at creating that brand.
[01:25] Stephen Ferguson: So, you weren’t there at the conception or the birth really. But like five years later, you find yourself in charge of kind of bringing the whole of the Simcenter portfolio of products, Simcenter itself, to maturity. And that seems like a massive challenge, doesn’t it?
[01:39] Jean-Claude Ercolanelli: Yes, you’re right. But you know what? I feel so excited and confident at the same time. But first, I need to acknowledge or recognize that I’ve been extremely lucky in my career because I worked and learned from the greatest visionaries and pioneers in the simulation and test industry we’re in: Steve MacDonald, David Gosman, Jan Leuridan, Alain du Vauvray, McNeil, John Swanson. No one can wish for better mentors to work and learn from. But secondly, I’m also fully supported by a reliable team of talented and creative engineers. That team has been built upon and has created a solid foundation that resulted from the success of Siemens acquisitions. With the team, we’re sharing the same passion for contributing at creating a sustainable industrial innovation for the world we really want to live into today but also tomorrow. That’s where the confidence comes from, also from the team and the background, and also by the intimacy in the connections that we have with our customers and their grand challenges. At the end of the day, my responsibility is to make sure that the Siemens Simulation and Test Solution team is developing the best-in-class solutions to help our customers realize their engineering objectives, that is to design, optimize, test more effectively, better products and faster. So, at the end, they can also themselves create value and sustain their competitive advantage.
[03:04] Stephen Ferguson: So, we talked about the challenges of today, I wanted to frame this episode of the podcast in terms of the five years. Because for most people, five years doesn’t seem like a huge amount of time, especially for middle-aged men like us. But if you think back five years, there are so many huge things that have changed in the world. And I want to just maybe think about some of those things, and talk about the role that Simcenter has played. So, for me, the biggest thing that’s happening in the moment is obviously climate change. Now, obviously, climate change is already happening five years ago, it’s been happening more or less since the Industrial Revolution, but for a lot of that time was quietly creeping up on us. But since 2016, there’s been a real change in urgency. And perhaps I give it too much credence but I think in 2018 when Greta Thunberg addressed the Climate Change Conference and started talking about her “ruin my childhood” speech. Since then, almost everybody has been talking about climate emergencies, and there’s like a real sense of urgency. And if you think about this is the biggest challenge our species has probably ever faced, since the Industrial Revolution. Like our entire civilization, our entire standard of living is based on burning these hydrocarbons, and we can’t do it anymore. So, in the next 10 to 30 years, we’re going to have to stop burning hydrocarbons. We still got to maintain the standard of living for 8 billion people. And obviously, I mean simulation and test, and digital twins are going to play a huge role now. Aren’t they?
[04:28] Jean-Claude Ercolanelli: Yes, and luckily the investment being made in those fields to address that major challenge – or probably the most important challenge – that we’re facing for a long time isn’t starting just today or it hasn’t started even five years ago when Simcenter was created. Siemens teams have been working on the sustainability and environmental problems for actually several decades from now already. And we can actually really stay that this is putting us into an unrivaled position to really fully support our customers to reduce those CO2 emissions from the products but also the processes as part of that transition to the net-zero carbon economy. And here our role is crucial because we enable them to achieve those technological innovations that contribute to better living. As an example, in the field of power generation, did you know that the Tokyo Olympic Games have used energy produced by hydrogen-burning gas turbines?
[05:27] Stephen Ferguson: Amazing. No, I didn’t know that.
[05:29] Jean-Claude Ercolanelli: And did you know that these were designed with the Simcenter?
[05:32] Stephen Ferguson: No, that’s incredible.
[05:34] Jean-Claude Ercolanelli: If that was possible, it’s because the investment of making it possible started a few decades ago. What we see here is that the readiness of our solution to help enterprises tackle those challenges. And it’s not the only one, so we have plenty of customers involved in many ambitious projects from carbon capture usage and storage units, but also in the global subsea power grids to address the challenge of exists today in complementing the green electricity sources that we have. If you look into also in the field of automotive transportation, we are engaged for more than 30 years at improving the efficiency of the internal combustion engines, and developing cost and usability competitive alternatives with a safe, hybrid, and electrical power trains. But we also investigate for actually 12 years now in new battery cell technologies and in the fuel cells application domains as well. So, you see, we’re not just passive, and we’re already ready to help our customers to really embrace that challenge and address it.
[06:36] Stephen Ferguson: You’ve really got to be ahead of the curve, though, haven’t you? Because the development time for some of these things is so long, you have to be looking to the future all the time, which is part of the challenge that you face in your new role, I guess.
[06:46] Jean-Claude Ercolanelli: That’s correct. You actually absolutely phrased it right. We’re here to anticipate what the problems of tomorrow may be. And we would not do that on our own. We’ve created that Customer Advisory Council where, with the key players, we meet a few times a year, discuss about the grand challenges and where the simulation and the test solutions can help them, addressing their grand challenges. So, that’s the way we build the future and the capabilities that are being used by our customers.
[07:17] Stephen Ferguson: So, the second big challenge I came up with, which is also a rather obvious one, is the whole Coronavirus thing. So, if we’d talked in 2016 and predicted that within five years most of us would have been locked in our homes for 17 months hiding from a virus, it might have seemed like science fiction. But of course, that’s a reality we’ve all lived with. And we’ve lived through a pandemic which has demonstrated that keeping well and being healthy is not just about our personal lives but the whole economy of the whole planet depends on it because everything stopped because of this virus. And when I’d spoken to you before, you said, since the 1970s computer edge engineering has had a massive impact on how we live, how we travel, how we communicate and connect with one another, and increasingly how we can be cured. And that “how we can be cured” and live happier and healthier lives, that’s something else which Simcenter is going to play a big role in in the future, isn’t it?
[08:12] Jean-Claude Ercolanelli: Just a moment on the Coronavirus, I think that’s absolutely right. The world has never before needed to implement that type of mass immunization for its entire adult population. And that represented the biggest manufacturing and logistics effort since the end of the Second World War. The reason is that because vaccine manufacturers need to scale up those processes from a small quantity that you work into a lab of a working vaccine into an industrial scale in multiple production facilities that are spread around the world in order to manufacture those billions of doses. And there is where the challenge lies because biological processes don’t scale linearly with the geometric size of the bioreactor. And it’s also unfortunate, but it’s also one of the main reasons behind the production delays that have been extensively reported in the press and were the cause of quite considerable international political tensions. So here, the use of a Simcenter digital twin model helped bioreactor manufacturers to tackle that challenge and allow them to double the production of vaccine per unit floor space, and therefore, respond to the time constraint. It has one side of the question, I think. But while Siemens has a strong presence in the pharmaceutical domain for optimizing also the energy efficiency of the drug manufacturing processes, I mean minimizing also the energy consumption as well as the waste of the raw materials while improving the throughput, we expect to see also an increased use of the engineering simulation disciplines in the field of drug discovery, precision medicine, in simulation of body organs subject to protein ingestion, for instance, and to anticipate on the responses of individual patients. And what we see ahead of us – and it’s kind also an objective that we have – is the ability to create in the future a digital twin of a full human body.
[10:05] Stephen Ferguson: And I noticed that on the Hype Cycle, which they publish once a year, with kind of emerging technologies. This year’s one is about to come out now, but last year’s one had digital twin of the person as one of those kinds of emerging technologies. So, that’s an exciting thing for the future. It’s going to take a while before we get to that stage. But again, that’s the way we have to have the foresight now to be looking for these trends and developing the simulation and test technology that will allow us to help them come to maturity, I guess.
[10:32] Jean-Claude Ercolanelli: You’re right. The digital twin is that visual representation of a physical asset or even a process. But you’re absolutely right. So, in the future, it’s going to be also the virtual representation of a human body, and that’s where we are working on. It’s not for tomorrow, to be honest with you, it’s going to take a few years before we get there. But we start seeing the first digital twin models of individual organs that can already be used, like heart, liver, that type of organs that for which we can already model the behavior subject to protein ingestion, or a drug, or any other type of molecules.
[11:12] Stephen Ferguson: So, that brings us nicely on to the third thing which I think has changed in the last five years, which is the emergence of the comprehensive digital twin. So, you mentioned that we’re acquired by Siemens in 2016. And up until that stage, I’m fairly sure I’d never heard the word “digital twin” until we started meeting with Siemens people. But since then, it’s been everywhere. Now, that might be my ignorance as well. But I look back at the Gartner Hype Cycle, it didn’t appear. The word “digital twin” appeared for the first time in 2017. And they were talking about a kind of maturity time of five to 10 years. So, it’s four years since digital twins have appeared on the Hype Cycle. And I think we’re starting to get to a stage now where we’re starting to see real-life examples of digital twins in action. And again, that’s going to be a huge thing for Simcenter and simulation. So, Jean-Claude, what role do you think that Simcenter will play in the future of digital twin?
[12:09] Jean-Claude Ercolanelli: So, as I said just before, a digital twin is the virtual representation of a physical asset or a process. When you consider Simcenter, our entering simulation and test solution, we do predict the performance and the behavior of these assets and processes even before cutting any steel. So, we can really consider Simcenter as being the beating heart of the Siemens comprehensive digital twin. And you mentioned as a comment before, you know that I do believe in the value that simulation and analysis tools bring, whether they are software, hardware or services, and the value that they bring to the world since they exist. The use of the digital twin models has a direct and positive impact on the way we live, the way we travel from a place to another, the way we get connected, and more importantly, how we can be cured. If you look into the investment that Siemens made in the last 10 years, the fidelity and the accuracy of our digital twin, its comprehensiveness as well, is a knowledge in the marketplace to be the most advanced and thorough. We’re used widely across many industries to design, to build products that range from the largest chemical processes plants to the smallest mobile devices, and everything in between, whether it’s aircraft, ships, cars, engines, medical devices, home appliances, batteries, and so forth. You see that all types of companies, from the startups to the largest and iconic ones, are using Simcenter to remain competitive because we help them discovering better designs faster, and help them predicting and validating how the next products will actually behave. So, our solution spans from materials to full systems. And the entire products including electronics, mechanical, electrical design, manufacturing safety, and reliability aspects. Indeed, my goal is to continue expanding that relevance and making sure that our technologies serve the purpose we have mentioned before. So, what we do is we keep working at lowering the barriers for using these models even more widely and seamlessly than before, in order to see them used by every engineer running on any edge device and so forth. So, as an example, we released last year, what we call the executable digital twin. Those are smart models, don’t require an engineer sitting in front of his desk to operate them. They’re just being fed with IoT and sensors data, and can accurately predict product performance based on real operational conditions, meaning that they provide today valuable information to the design engineering teams, so they can use that for the next generation of products or even improve the current product line. But it can also be used by the maintenance and operation teams to optimize the service time of these products and help in diagnosing possible corrective actions in order to anticipate also the maintenance operations. So, you see that the usage of the Simcenter digital twin models is today close to be limitless. And we keep expanding it as scope and value every day.
[15:12] Stephen Ferguson: So, one of the predictions you’ve made last time I interviewed you was that computer-aided simulation technology will be used by every engineer and installed on every piece of hardware equipment. That’s a huge vision. It’s a huge potential for our industry as well.
[15:27] Jean-Claude Ercolanelli: That’s happening today. It’s actually effective and we have that on the edge devices already available. Thanks to our executable digital twins. It’s just the start of, I guess, that spread that I was mentioning before, and desire to see it used more and more because it brings real value to the enterprises.
[15:49] Stephen Ferguson: And for guys like us who’ve been around for 30 years, it’s amazing, the progress that’s been made. Because when we first started, this was kind of a geeky, niche technology that people were only starting to take seriously. We had to really convince people what we were doing was simulating reality. And now we’ve come to a stage where it is part of literally everything. So, it’s a really exciting time.
[16:11] Jean-Claude Ercolanelli: There has been a real shift in people’s minds about simulation solutions and tools. From being just a troubleshooting type of technology to now really driving the innovation into these enterprises.
[16:27] Stephen Ferguson: So, that brings me on to the fourth trend as well, that the whole idea of democratization is about to get even more turbocharged by the emergence of artificial intelligence and machine learning. So, back in 2016, maybe I owned an Amazon Alexa, but these days those kinds of personal assistants are everywhere. But they’re not just for consumer goods, they’re going to start influencing the simulation and test games in ways that people haven’t even really imagined yet.
[16:56] Jean-Claude Ercolanelli: Right. There’s been a lot of research and actually achievements that have been made in the field of artificial intelligence. We’ve been exploring ourselves also the possibilities of artificial intelligence, machine learning, deep learning in the way they could add value to our users, helping them in one way or another. So, if you pay attention to Simcenter today, we already feature a number of those capabilities across its solutions. We have not finished, we’re still working on, we’re still expanding the usability and the scope of AI within our solutions. But customers can already benefit from it today at different levels. First, on the user experience. If you look into Simcenter 3D, we have the user interface exposing the next command that you’re likely to need based on your past actions. So, the UI will adapt and adjust based on what the system is anticipating you will need to use as a common, making the UI much more clean and giving more room for your graphic window where you are operating on your design. The second is on accelerating design predictions. Today, we’ve demonstrated that you can train your neural network with advanced physics results. We’ve been actually also publishing examples on combustion results within the piston chamber. And also showing predictions coming from both the artificial intelligence solution platform as well as the combustion analysis. The solutions were within less than 10% difference. So, we’re not saying that AI can help you validating yet your designs, but they capture the trends, and they can help you accelerating your selection of designs. So you remain when you get into the validation stage, which is just a few designs rather than having a large number. So, you can focus your time, and the harder time, and the analysis time just on a few of them.
[18:57] Stephen Ferguson: That’s an important point because it basically allows people to spend more of their time doing what engineers should be doing, which is interpreting the data and making decisions, and less time doing manual arduous tasks, which is, again, what it was like when we first started as well. So, that’s a big step forward for engineers as a profession, I think.
[19:14] Jean-Claude Ercolanelli: Right. So, we used to spend 90% of the time in the past when I started to work myself in the early ‘90s, 90% of my time was to create a mesh and then to set up the solver. And the last 10% on understanding the results and grow conclusions to improve my design. Now, it’s the opposite. I mean, people, what happens with our solution, spend maybe 10% to 15% of their time setting up the problem but the rest is on “Let me analyze all my different analyses here and find out what is my best set of designs or trade-off analysis I can get out of it.” So, it really has the engineers doing their engineer role. I was mentioning about accelerating and the design predictions, but we can also use that to AI to create reduced-order models, and then use those surrogate models to continue accelerating that design predictions even faster. We can even embed those into edge devices to create those executable digital twins. See, this is also the link with the previous question that you had; what do you see the Simcenter going in the future? And it’s not only there, I mean, today, we also use AI in Simcenter for Additive Manufacturing process simulation and performance on the fatigue aspect. We can actually take into account the macro porosities of the different mythological faces that have been created during that building process, and assess the durability and the fatigue of such a product, thanks to AI, it’s impossible otherwise. In the field of advanced driving systems and autonomous driving, here too, AI is instrumental in identifying the critical scenarios to validate. There are so many of those that are possibilities that we need smart ways to actually limit our effort or the simulation effort on those that are actually critical. And AI is here to help us identify them. The number of applications is endless. With just scratching of a surface and covering the possibilities, on this front, you may need to stay tuned because there’s a lot of to come in the coming months and years from Simcenter.
[21:26] Stephen Ferguson: That whole automated driving system’s progress has been much faster than most people expected as well. So, once again, if we’d said five years ago, “You’d be able to go to Arizona and hail a completely autonomous Google taxi cab,” people wouldn’t have believed that at all. But now I’m looking at it like, so I’ve got two kids who are eight or nine. Normally, when you get to 18, the big rite of passage is getting your driver’s license for the first time. But for my kids, that’s not going to be a thing, I think it’s going to be almost a redundant skill, such as the pace of development in automated driving. And again, that’s something else which has been being driven by Simcenter and Simcenter Prescan, it’s a huge thing for the world.
[22:07] Jean-Claude Ercolanelli: It’s a huge thing. I agree with you. We really, with our solution, help engineers to really design, test, and optimize autonomous systems by using physics-based simulation, so they can today prove the safety and reliability of those systems from really the early research and development stages until the final stages of validation, but also certification and prepare for the homologation of autonomous vehicles. We have a large scope of capabilities that are available within our solutions today for them to easily perform that self-driving studies in order to optimally configure the sensors, but also develop that robust driving assistance systems. Evaluating the performance of the perception, the fusion, the planning, the control algorithms together, and therefore, get ready to the certification of those autonomous vehicle systems.
[23:02] Stephen Ferguson: And eventually end up with autonomous drivers who are safer than human drivers. I think that’s going to happen quite rapidly. So, looking back across the whole of the first five years of Simcenter, what do you think Simcenter’s biggest accomplishments have been?
[23:02] Jean-Claude Ercolanelli: I think that we, first of all, can be really proud of what Siemens has been delivering with the Simcenter because it’s been on its promises. First, if you look into the field of integrated and comprehensive, multidisciplinary and multi-physics simulation and test solutions, we have brought together, under one umbrella, technologies and products coming from various key players, whether it was UGS, LMS, CD-adapco, Mentor, TASS, SAAB MEDAV, Multimech, Culgi , and more recently, Nextflow Software, that’s quite an achievement; being able to rely on that integration. The second is, I think that we are the first to offer a system simulation capability for model-based design. If you look into the industry, the product innovation and differentiation is increasingly happening through that combination of mechanical, electrical, but also electronics, and software disciplines together. What I’m saying is that the corresponding product complexity is drastically higher than it used to be. You don’t find an industrial company today, optimizing a product for just one single discipline and one single attribute. And what we do is that with a Simcenter system simulation, we lead the way and provide deep insight into the underlying physics by shifting to the left the management of that complexity and very early into the enduring cycle. The third is in the field of generative engineering. I think that everybody appreciates that exploring the space of the possible configurations of a design of a product is a multi-faceted approach and this encompasses multiple technologies. If you look into it, we feature today AI and machine learning within Simcenter to search intelligently for suitable system and product architectures. No one else can do this. Then we have also, within the Simcenter, the ability to perform what we call topological optimization. But we can do so for different disciplines for structural, fluidic, thermal disciplines as well in order to propose new designs that offer higher performance and often can be manufactured with Additive Manufacturing processes. Then we use AI again for anthropological and parametric exploration together to fine-tune those design analyses and offer the users for him to actually select what is the most robust design you can find and perform these trade-off analysis and make the right decision at the end of the day. I mentioned just before the structural integrity and the fatigue performance of 3D printed components. So, here we’re connecting today the manufacturing process with a structural performance through that modeling our this microstructure that is being built during the Additive Manufacturing process. And we can leverage, really, our true multiscale approach with AI to enhance the simulation of that lattice structures, take into account the effect of the porosity in the microstructure as well as the other attributes to assess, accurately, what the fatigue performance and durability of such parts are. On the fourth, I think I want to come back on these advanced driver assistance systems and autonomous driving. I think that, here, our solution is today capable of helping engineers designing, testing, and optimizing those systems by using physics-based simulation. They can already prove the safety and the reliability of their autonomous systems, and perform easily those self-driving studies, and prepare for the validation and certification of their autonomous vehicle systems.
[27:04] Stephen Ferguson: The whole rapid prototyping and 3D printing because that means now we can use the AI things in machine learning to generate more optimized, better-performing designs. And now we can also, for the first time, manufacture them before. Because that was always a huge constraint is you could design things you couldn’t build. But 3D printing, rapid prototyping help us to build things as we design them for the first time.
[27:31] Jean-Claude Ercolanelli: It was very virtual, that’s right. It was a real digital twin in the past. So, now, with another Siemens solution, we can also manufacture those products and they are fully optimized. And there, you get shapes that no one can actually imagine with a traditional parametric-based geometric tool.
[27:49] Stephen Ferguson: You can only do that using multidisciplinary simulation and test, because like you were saying, all the simple single discipline problems have already been solved. And in order for us to solve these huge challenges we’ve talked about, we have to use all the weapons, all the tools that are available for us, and that means optimizing across multiple domains. So, that’s a massive challenge once again.
[28:12] Jean-Claude Ercolanelli: I agree. I think the industry has exhausted optimization, thanks to simple approaches. Now, in order to get further, you need to embrace that complexity. And that’s exactly what we aim at. We want them to actually understand and acknowledge that, yes, what they’re doing is very complex. So, they need a tool that has the ability to manage that complexity.
[28:37] Stephen Ferguson: As a final question, which is probably slightly absurd considering all the massive unpredicted changes we’ve talked about already. But do you have any predictions about what the next five years are going to hold for engineering simulation Simcenter?
[28:52] Jean-Claude Ercolanelli: Well, I can tell you one thing is, for us, we shall continue contributing to creating that sustainable industrial innovation for the world we want to live in today and tomorrow. To me, having a purpose in what we do every day is of primary importance. And we will do so by expanding the Simcenter portfolio to support our customers in their digital journey. I’m not going to unveil features and so forth, but I can tell you that the way we were up today, we actually are building our solution on four pillars, which we consider being imperative requirements in order to help our customers in their digital journey and digital transformation of their engineering and simulation processes. I mentioned just earlier, the first of these pillars, and I think it should not be a surprise, is the ability to model the complexity. I’m talking here, really, the ability to predict, to measure the behavior and the performance in the best possible way. Meaning, I want us to capture all the complexity – be it from the geometry, the physics, the interaction of the physics together, or the operating environment as well, in order to be able to deliver that and create a value. The second pillar of our foundation here of a strategy is to explore the possibilities. I mentioned several times about trade-off analysis exploration. Yes, as the complexity increases, the degrees of freedom available for making decisions also increases. And it’s through a systematic and intelligent exploration of the design space that our users will gain a tremendous value from our models. And they will be able to discover new designs, they will be able to optimize for the performance, they will be able to improve the robustness. The third of our pillars is going faster. Well, if you increase the complexity of your modernization, whether it’s from the geometry or whether from the physics, if you now add also another dimension that you want to explore multiple scenarios – multiple configurations – well, that pressure of time, the cost and quality still apply. So, our imperative here to our development team is to ensure that while our customers are modeling with higher fidelity, their products and systems, and while exploring multiple variants and configurations, the execution of our solutions must stay within their expected timeline within their constraint. So, for us, it spans across multiple areas. It could be on the licensing that needs to be adapted and flexible. It spans through the support of the latest hardware technologies. It means also making sure that our solution is available on the cloud. There are a lot of implications of going faster. It’s not just from the solver time, it’s from also the engineering, it’s from the access, it’s from the flexibility that we offer to our customers. I just mentioned three, if we talk about the fourth, well, the fourth pillar is to stay integrated. As the product development has become more complex, there also are more opportunities for misalignment between the teams working on those products. So, we consider traceability as a key enabler for visibility, and additional continuous process that connects all the relevant stakeholders, processes, models, data, suppliers, and so forth, is actually highly critical. So, that’s for us, the fourth pillar is to ensure that integration and interoperability between the different disciplines but also between the different steps within the design lifecycle. You’ll see a lot of progress in the multiple disciplines, but we continue expanding the disciplines in the scope of a Simcenter.
[32:52] Stephen Ferguson: That’s a really interesting insight. Because when you think about how we’re going to solve problems we don’t know even exist yet, and it is by sticking to those kinds of core principles, you call them pillars. But by sticking to those principles, we end up developing software and test systems which will help us deal with any problems we face in the future. I think we’ve demonstrated across the last five years that that approach is the right approach.
[33:15] Jean-Claude Ercolanelli: So, that approach gives us the agility to actually adapt to the grand challenges of our customers. I mentioned the Customer Advisory Council that we have, this is where those are being discussed as well – the challenges. And that approach, that strategy based on these four pillars helps us adapt and be nimble on the needs and helps us anticipate what the future holds.
[33:39] Stephen Ferguson: So, Jean-Claude, I want to finish this podcast off with an invitation. I want you to open your calendar now, book in a slot for June 16th, 2026, so we can get together for the 10th-anniversary podcast, and we can reminisce about how quaint the world was back in 2021, and all the other fantastic problems we will have solved by then. So, I’m sure if you open your calendar, you’ve probably already got a booking for that day for something else. But if you can find a slot for us in five years’ time, we’d really loved to hear how’d the next five years go. So, are you up for that, Jean-Claude?
[24:11] Jean-Claude Ercolanelli: Sure thing. Actually, I’m just opening it now. Done. You better be there.
[34:16] Stephen Ferguson: Yeah, I will. Thank you very much, Jean-Claude, that was brilliant. Thank you.
[34:19] Jean-Claude Ercolanelli: Thank you.
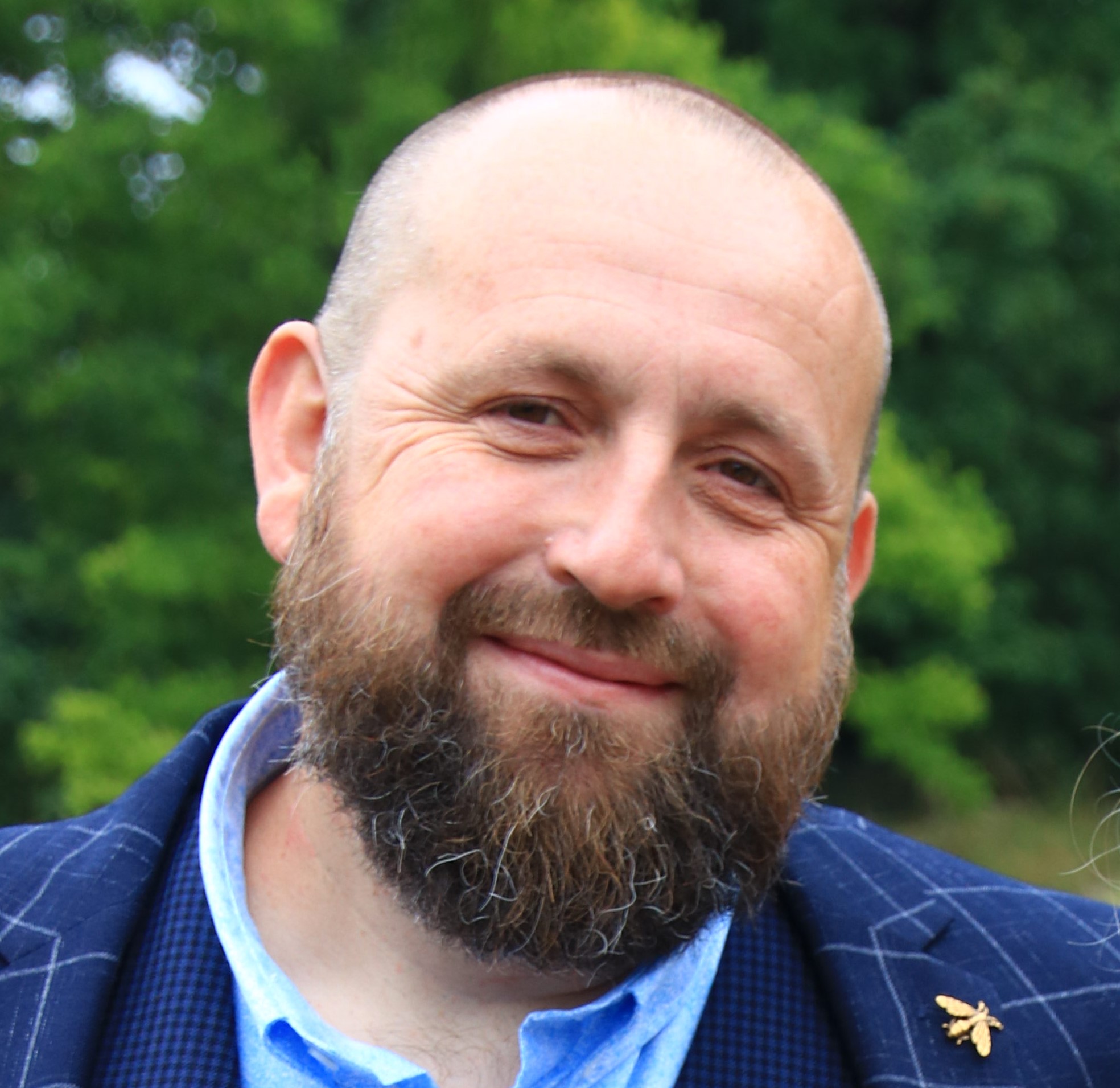
Stephen Ferguson, your host
Stephen Ferguson is a fluid-dynamicist with more than 25 years of experience in applying advanced simulation to the most challenging problems that engineering has to offer for companies such as WS Atkins, BMW and CD-adapco and Siemens.
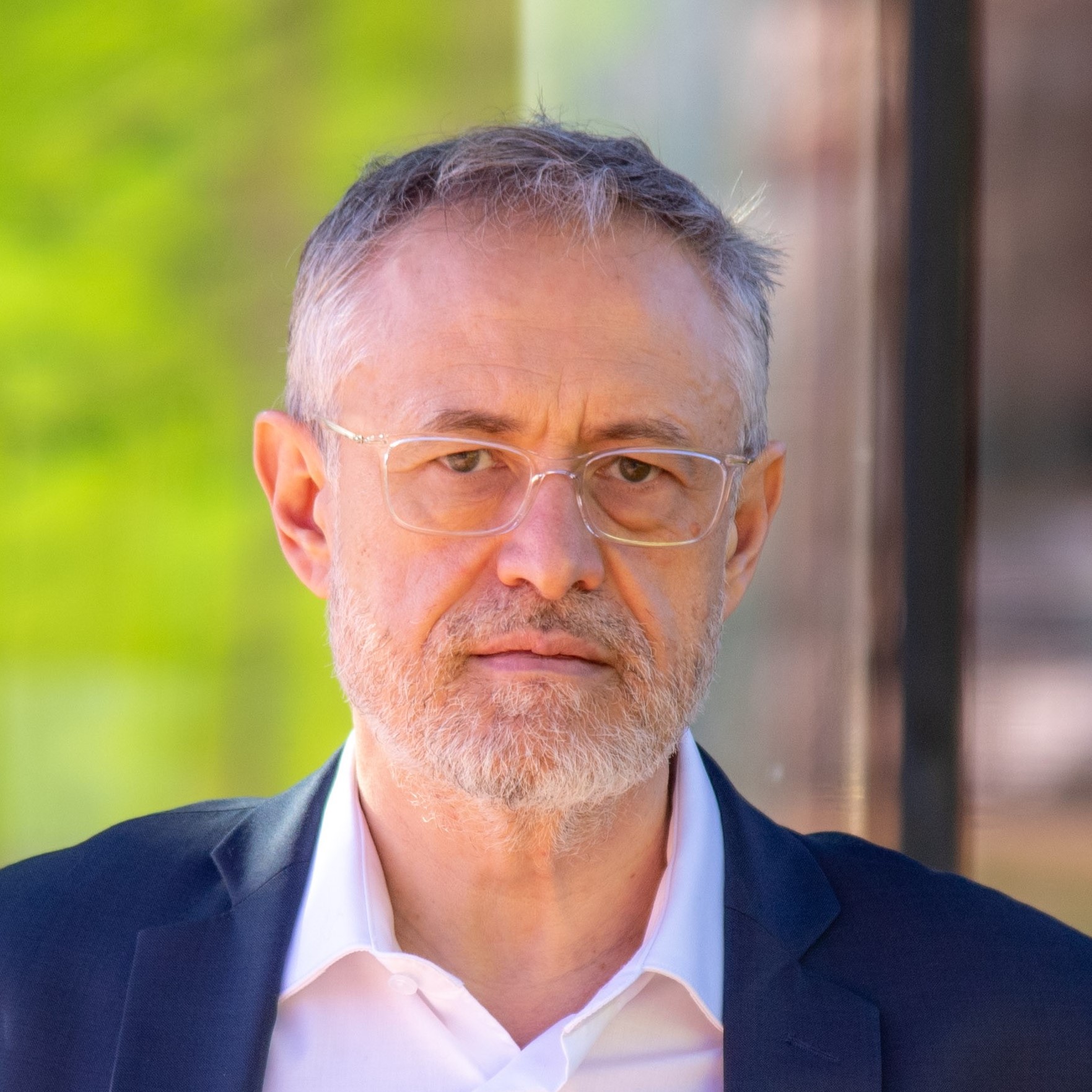
Jean-Claude Ercolanelli, our guest
Jean-Claude Ercolanelli is Senior Vice President Simulation and Tests Solutions. and leads the Siemens Digital Industries Software Simulation and Test business segment, including serving as CEO for Siemens Industry Software NV.
Stuff to watch:
- Ride the digital wave with CFD simulation
- Podcast: What are digital twins made from?
- Engineer of the future
Good reads:
- Keeping the lights on in a Climate Emergency
- Engineers caused the Climate Emergency. Only engineering simulation can save us from it.
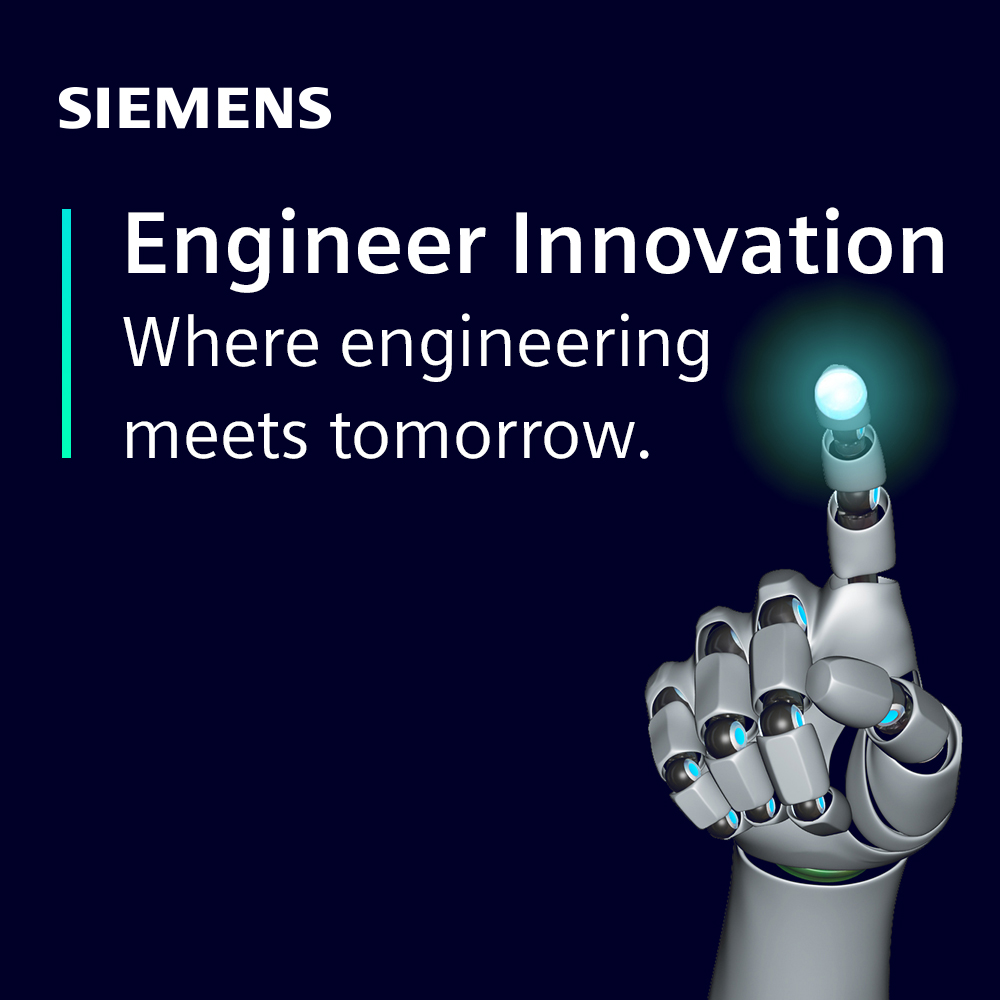
Engineer Innovation
A podcast series for engineers by engineers, Engineer Innovation focuses on how simulation and testing can help you drive innovation into your products and deliver the products of tomorrow, today.
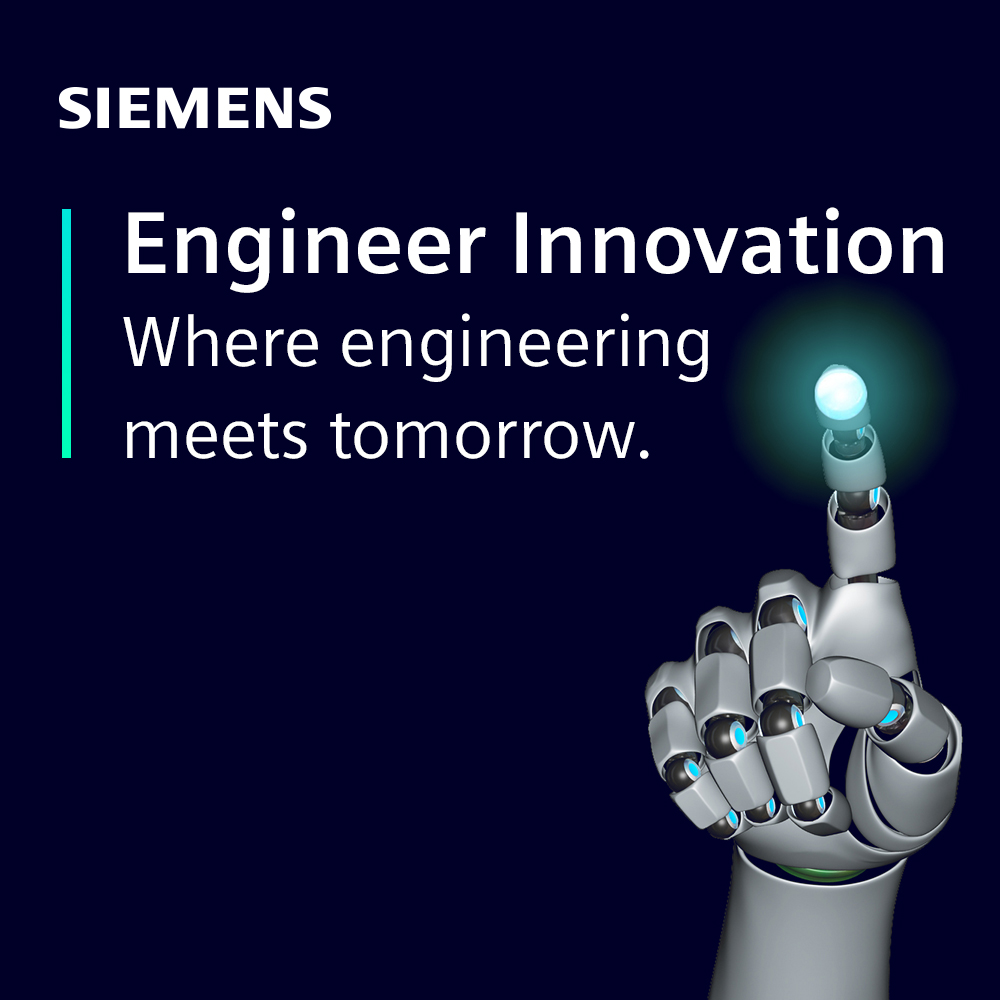
Engineer Innovation Podcast
A podcast series for engineers by engineers, Engineer Innovation focuses on how simulation and testing can help you drive innovation into your products and deliver the products of tomorrow, today.