Inside the Design and Manufacturing Processes at Piper Aircraft
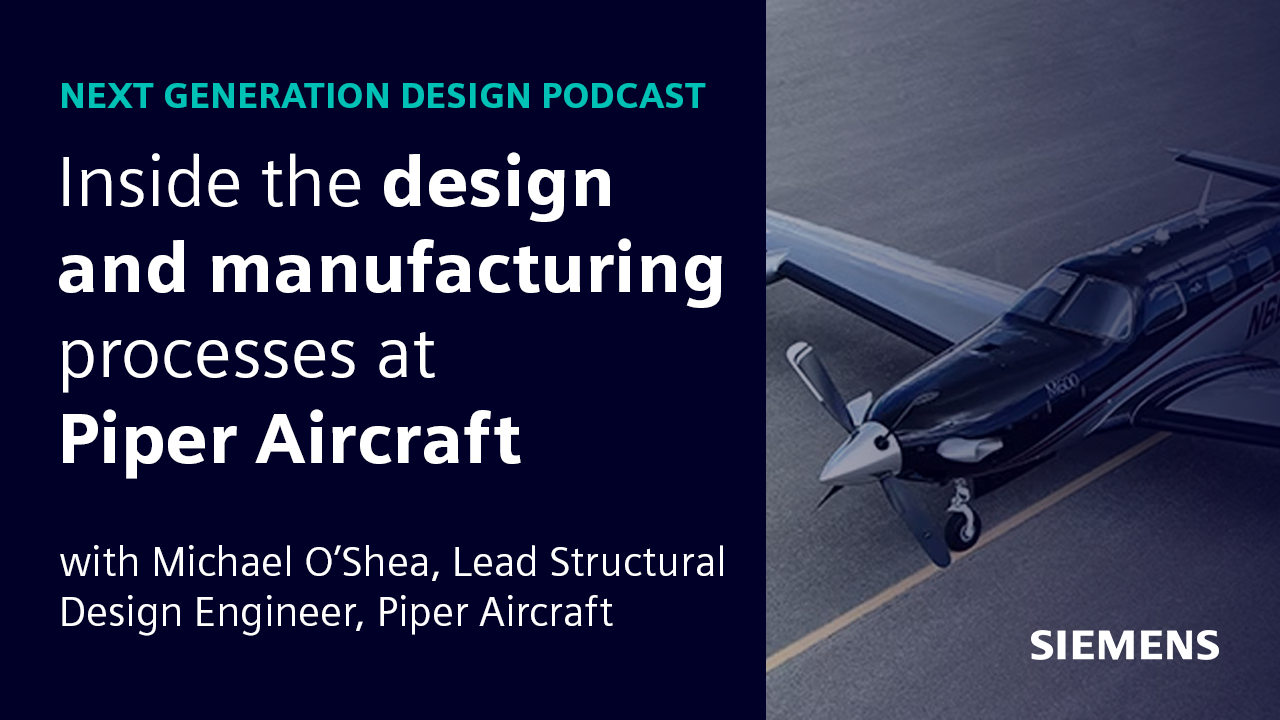
Computer-Aided Design (CAD) systems allow engineers, architects, and other design professionals to deliver numerous drawings quickly and accurately during the planning and design phase. And just like in other industries, the use of CAD in the aerospace industry is vital for the successful creation of innovative airplane designs and functionality.
On this episode of the Next Generation Design Podcast, our host Jennifer Piper is joined by Michael O’Shea, the Lead Structural Design Engineer of the Product Development IPT at Piper Aircraft. He will be talking to us about the design and manufacturing processes at Piper Aircraft.
In this episode, he will help us understand his role as a lead structural design engineer and his day-to-day work, which involves a lot of CAD modeling with Siemens’ NX CAD. You will learn about the design and manufacturing processes at Piper Aircraft and the impact of the COVID-19 pandemic on the aerospace industry and how Piper Aircraft adapted to new demands, including the move towards electric and autonomous aircraft.
What You’ll Learn in this Episode:
- The design process at Piper Aircraft
- How Siemens’ NX helps Piper Aircraft keep up with the increasing product complexities in the industry
- The challenges in aerospace and defense, and how simulation and visualization tools help in the design process
- Piper’s Halo safety system
- The impact of the COVID-19 pandemic on the aerospace industry and how Piper Aircraft adapted to new demands
Today, everything just starts digitally. I mean, every concept, layout, iteration, it’s all in CAD. And CAD really makes it a lot easier and cheaper to do that.
Michael O’Shea, Piper Aircraft
Listen to the Next Generation Design podcast wherever you do podcasts.
Connect with Michael O’Shea:
Connect with Jennifer Piper:
Listen to or read the next episode of the Next Generation Design podcast: How NX CAD Meets the Needs of Small and Medium Businesses (SMB)
Listen to or read the previous episode of the Next Generation Design podcast: Integrating Siemens Software and Tools in Engineering Education
Podcast Transcript
Michael O’Shea: Everything just starts digitally — every concept, layout, and iteration, it’s all in CAD. And CAD really makes it a lot easier and cheaper to do that. I can’t imagine having to go rework an airplane every time I wanted to change something; you can just do it in CAD and say, ‘No, that’s not going to work,’ and then iterate it.
Jennifer Piper: Welcome to another episode of the Next Generation Design podcast. I’m your host, Jennifer Piper. In this episode, I’m talking to Michael O’Shea, Piper Aircraft’s Lead Structural Design Engineer, about the aviation company’s design and manufacturing process and the ways they utilize NX and the digital twin. Before we begin, let’s meet today’s guest. Michael, can you tell us a little bit about the role you play at Piper Aircraft?
Michael O’Shea: I’m a Structural Design Engineer. So I started in 2016, as an entry-level engineer, and I joined a team with just great mentors. I picked up CAD pretty quickly — heavily a CAD designer. After a couple of years, I was promoted to a mid-level engineer where I got to start working on bigger programs and helping to train entry-level engineers and interns. And then last year, Piper created a product development team, like a new separate team, so I took on the lead role there.
Jennifer Piper: And can you give us a bit of an overview on Piper Aircraft as a company?
Michael O’Shea: Piper is a general aviation aircraft manufacturing company. We’re located in Vero Beach, Florida. We’re probably most recognized for our very yellow Cub that we used to make back in the day — everyone always asks us about it, and they ask us to start making them again. Today, we currently manufacture trainer-class aircraft as well as business and personal-class aircraft.
Jennifer Piper: Well, welcome to the show and thank you for joining us today. I’m curious, what got you interested in aerospace engineering? Was this a world you had always seen yourself in?
Michael O’Shea: No, I didn’t plan on being an engineer at all, actually. I was big into music growing up, and I started my first semester of college in music production. And after a semester, it just seemed like it was going to be really difficult to get a job in that industry, so I switched my next semester to architecture because I didn’t know what I wanted to do. Architecture was an interest when I was a kid, but still didn’t really want to do that. And then my parents were having a dinner party one night, and my grandfather was over and he started telling me about his career at Pratt and Whitney as a Propulsion Engineer—I had no idea that he had done that—and he was recommending aerospace engineering. This was like 10 years ago, so the industry was all going private for space, and SpaceX was doing big stuff, so it seemed cool. So, the next day, I jumped online and changed my major.
Jennifer Piper: Wow, it sounds like you owe your grandfather a big thank you for that! What would you say is your favorite model of aircraft that Piper manufactures?
Michael O’Shea: Definitely, the M600. I don’t like flying and I’m afraid of flying. I’m not an aviation enthusiast. But from a product standpoint, it’s our flashiest plane. It’s got a nice interior and awesome avionics. And as I mentioned earlier, it’s got Garmin’s Autoland system in it, which is just really cool.
Jennifer Piper: Can you describe for our listeners what your day-to-day looks like? What tools are you using on a daily basis?
Michael O’Shea: It’s a lot of CAD, a lot of time in NX. At Piper, we’re able to work on just so many different areas of an aircraft. So, being in Structural Design, I’ve worked on the fuselage, wing, empennage, and landing gear. Our interiors are also the responsibility of structure design, too, so there’s a lot that goes into the interiors. And that’s just one aspect of design there that we also have avionics, electrical, and software departments. We have powerplant and mechanical systems departments. There are just so many departments. And we run everything through CAD, so it’s a lot of CAD modeling. For me, our structures are mostly metallic, so it’s a lot of sheet metal design. We do other components like machining; castings; for interiors, we’ll do thermoplastics; 3D printed parts — so many different modeling techniques go into all those different manufacturing styles. Also, we do CAD sub-assembly and large assembly configurations all the way up to our complete aircraft. So, everything is configured through CAD. And all the engineers at Piper are also our drafters — we draft all of our own designs as well, so we have to know all of the drafting functionality as well. So, just a lot of CAD work day to day.
Jennifer Piper: How were you introduced to CAD software and NX? Was that process something you learned in college?
Michael O’Shea: You would think that in college that we would have tons of CAD experience and that’s what they would be heavily teaching us, but I didn’t really get CAD experience until my senior year in senior design. And even then, it was very minor and it was in SolidWorks. So I think my first real introduction was NX at Piper. It was kind of a get-your-feet-wet-and-start-modeling kind of process. The leads helped answer questions and guide you. We had introductory training but I always found the best way to learn how to model was to just start gaining familiarity.
Jennifer Piper: And what advice would you give to someone trying to learn NX?
Michael O’Shea: For someone trying to learn NX, I would say stick with it. It can be very overwhelming at first to just open up a CAD suite, and there are so many tools, and you don’t know any of the names of anything or even what it can do. So, oftentimes, you’ll see entry-level designers struggling really hard to make something, and they’ll throw 50 features at it, and you just tell them, “Hey, you can just do this one thing and it makes it way easier — one feature.” So, you just stick with it, get over the learning curve, and learn how to use it.
Jennifer Piper: It sounds like there’s a lot of trial and error involved in that process.
Michael O’Shea: Right. You read a bunch of manuals on how to do it and you don’t know the names of anything, so it’s kind of useless. You’ve got to start using it to figure out what stuff is.
Jennifer Piper: Michael, I’m wondering if you can give me a little more insight into the design process at Piper Aircraft and what that actually looks like. Where does that process start?
Michael O’Shea: That one is pretty difficult to pin down. I think it’s very heavily dependent on the scale of a program. So you could have a really large program that involves every engineer at Piper or you could have something really small. It’s just revising a single part that takes one engineer. So, I think regardless though, it starts with the concept — so, maybe marketing will ask for something new or manufacturing will request that we revise something to help them build the plane better. Engineering will evaluate it and we’ll start modeling. Everything really just starts with modeling. We’ll kick off and do a modeling effort, and we’ll host design reviews using a TC Vis (Teamcenter Visualization), we’ll showcase the design concept. And sometimes it’ll get approved right away if it’s something simple; something more complex takes many design reviews, many weeks, many iterations to really nail down.
Jennifer Piper: And how many people do you typically see working on one program at a time?
Michael O’Shea: For a large program, we could have the entire engineering team. You could have upwards of 100 people—sometimes more—working on a single program. So, there are a lot of moving parts with something that big. And what’s kind of funny to think about is, back in the day, before I started, it was common to just have all of your CAD files stored natively just in your server, I guess, that you just access it through the file explorer like a Word document, and people could overwrite files, and there wasn’t really a good way to control that. So, since we do use Teamcenter, everything runs through that. I’ve used Teamcenter my entire career, I don’t know any different. So, we run all of our modelings and drafting files through it. You’re able to check files out really easily. It indicates to other users that they’re locked out and that they can’t modify it. And we also run our entire sign-off process and release all of our CAD data through Teamcenter. So, that really helps on a big program like that to collaborate. You don’t have to do so much physical communicating with people; it does it through your data management system.
Jennifer Piper: How much would you say that process has transformed since the beginning of Piper Aircraft? I would think the process from 90 years ago would be pretty unrecognizable today.
Michael O’Shea: As you can imagine, I wasn’t around in the ‘30s when they were doing that, so I can only speculate. But it seems like a lot of design back then, I believe, was building; you would build the plane first, and then you would catch up on the documentation. So you would try a lot of different physical designs, and then once you found out what worked, you document that. And that’s how you would repeat builds in the future. Today, everything just starts digitally — every concept, layout, and iteration, it’s all in CAD. And CAD really makes it a lot easier and cheaper to do that. I can’t imagine having to go rework an airplane every time I wanted to change something; you can just do it in CAD and say, “No, that’s not going to work,” and then iterate it. And it’s really easy and a lot more affordable.
Jennifer Piper: So CAD and NX have created pretty massive advantages in the design process.
Michael O’Shea: NX makes it just really easy to quickly model these concepts. And you can build these CAD models in a way that is effective and easy to use for downstream users. So, you want a fully parameterized CAD model where you can control the design, and a user can come in and see exactly what your intent was and how to make an easy change. You don’t want them to have to rebuild a part every time they open a file. NX is really powerful and allows you to do that. And as I mentioned earlier, being able to do this quickly saves time and money. So, it’s all cost efficiency. Another big aspect is assembly management. You can put all your parts together in a way that makes sense and build sub-assemblies and feed those into assemblies and installations all the way up to the full airplane. There’s a lot of complexity there with these large-scale assemblies and NX helps manage that.
Jennifer Piper: I know the aerospace industry is seeing big trends in customization and increasing product complexities, how does NX help Piper Aircraft keep up with that?
Michael O’Shea: One big tool with the assemblies—just to touch on that a little bit from where we left off—was suppression and assembly arrangements where, especially with us for our interiors, there’s so many different options and configurations. And it can be multiple colors of the same thermoplastic part or 3D printed part. And you have to have a different part number for each color that you have, so you can stock it on the shelf. There are also alternate parts. So you might have an interior panel that has a storage pocket or one that doesn’t and they’re optional. So, in CAD, you wouldn’t want all these different options piled up on top of each other. So being able to store them away in different arrangements, you would suppress one option in one arrangement, suppress another in another arrangement, and it helps in showcasing these different configurations to especially people in marketing so they can see what the customer is going to get. So if the customer wants to toggle on all these different options, you can showcase just one aircraft with all those options instead of just having everything thrown on top of each other. So I think it’s a really powerful way to handle that complexity.
Jennifer Piper: Is Piper Aircraft on the continuous release program with NX software? How has your experience been with the frequent software updates?
Michael O’Shea: It’s definitely cool that they get access to it more frequently. Prior to Teamcenter 13 or continuous-release NX, I think we were on NX 11. And prior to that, we were on 7.5. So, because there were such intrusive updates for us, we have to basically stop what we were doing, roll it all out over a weekend, and then make sure that everything was working — Sunday, with some test users. And then if it doesn’t work, we have to roll it all back. So, doing this continuous release has been a lot easier because they’re smaller updates, but big enough to make improvements but small enough not to shut us down if something goes wrong. So, it’s been really cool.
Jennifer Piper: Well, that’s great to hear. What are some of the challenges in aerospace and defense that Piper comes across on the day-to-day?
Michael O’Shea: That complexity is really hard to deal with. Customers want so much now and it’s hard to do that. Back in the day, you’d buy a car, and you could get a “tan one” or a “black one,” and it just came how it was. Now, there are packages for everything; you have a package for this and that, and the seats can be different colors, and you can go outside of the packages. Really managing that is extremely difficult. It’s not just as simple as offering it to the customer; it has to be managed and you have to make sure it all works together. So, that’s very complicated.
Jennifer Piper: Earlier, you mentioned 3D printing. How is that helping you keep up with the complexity?
Michael O’Shea: We use it a lot for interior components right now. You have to get these parts certified for different levels of aircraft use. Right now, we’re approved for interior use basically. We don’t do any metallics, it’s all plastics. But yeah, it’s a big deal.
Jennifer Piper: What role does simulation and visualization play in the design process?
Michael O’Shea: We use TC Vis here every single day. You walk through engineering, and every engineer has it up on their computer. I personally have three screens, and one of them just has TC Vis constantly. So, again, with that complexity, just being able to see all of your parts, your design concept, you make a layout file, and you can load it into an aircraft on TC Vis and you can see how it interacts with what’s there. Or maybe you didn’t realize somebody in another department was working on that same area and they changed stuff and you didn’t realize that. So you make these layouts, you get into a design review, and you have all these disciplines sitting in a conference room, and you go through your designs for that week. And being able to see that in a lightweight representation and in visualization software just helps everyone provide feedback in a quick and easy way.
Jennifer Piper: And what about the digital twin?
Michael O’Shea: Being able to have access to an entire aircraft, we crank through planes, physical aircraft, so quickly that we don’t have many just laying around for us to go look at. So, there’s oftentimes where you have to investigate clearances and just really understand how parts interact together. We also make a lot of older design planes too that we aren’t familiar with the previous designs. So, being able to see that in CAD when we don’t have access to a physical aircraft is really helpful.
Jennifer Piper: I can imagine that would be a massive game changer in those sorts of projects. One of the things Piper is known for is their HALO Safety System. Can you tell me a little more about that?
Michael O’Shea: Technically, I don’t know what all goes into a big software avionics effort like that. But I can tell you a little bit about how it functions. It can be activated either manually or automatically. Basically, if the pilot experiences some type of health issue, either the pilot himself or herself or a passenger can manually push a button and activate it, or if the system determines some weird flight anomaly, it’ll activate automatically and give you the option to cancel it if it was by mistake. Once it’s activated, it’ll calculate a variety of parameters like fuel, runway size at nearby airports, and weather that’s around you, it’ll create a flight path and it’ll automatically fly around terrain and weather. It’ll also automatically communicate an emergency to air traffic control and update passengers on status and ETA. It’ll eventually land, automatically brake, and shut off its fuel so the engine will power down. And by that point, emergency services should be there on the ramp waiting for you.
Jennifer Piper: And what a huge advancement that system has been for general aviation. Obviously, the COVID-19 pandemic has had major impacts on the way many people do their jobs. How was Piper Aircraft affected by the COVID-19 pandemic? Have you seen any long-term changes?
Michael O’Shea: Surprisingly, I think, long term, not really. At first, we were all really uncertain about what was going to happen, obviously — everybody was. And for engineering, specifically, we were thinking, “Will we remote from home? We don’t have that capability. Are we going to get furloughed? If we can’t design plans or build plans, why would you pay us?” That kind of made sense too. But fortunately, management worked through all of that and set up remote access for us. It was implemented full-time with a lot of employee input and feedback as to how we would do it. And were able to keep working and maintain all of our commitments for those years. We did end up having part shortages like everyone else did, but we just worked through them and we worked closely with our suppliers and kept that supply chain open and made all of our planes.
Jennifer Piper: Did it change any of your processes going forward? Or has everything basically remained intact?
Michael O’Shea: I think one of our big changes or light shined on was our sign-off process. So, prior to the pandemic, we were already digitally releasing all of our CAD data, but we were still physically routing drawing packages that you have to sign. When you’re remoting from home, how do you do that? You print out your drawing package, and it sits around, and then some people would show up at night and sign drawings. It’s not ideal. So, we were already toying with the idea of getting into digital sign-off, that’s one of Teamcenter’s capabilities. And this really highlighted the need for it and being able to work from home if necessary, and to be able to still release type design.
Jennifer Piper: And what about the aerospace industry in general? What effects has the pandemic had there?
Michael O’Shea: I think general aviation seemed to be affected opposite to that of commercial aviation. With commercial aviation, it really tanked and everyone was afraid to fly next to other people; they didn’t want to get sick. They still needed to fly, people wanted to see their families, people needed to travel for work, or they just liked traveling. So, you’d see this boom in people or companies buying general aviation smaller aircraft, so they could keep doing this and they viewed that as safer. So, our demand increased or stayed the same, it didn’t get worse.
Jennifer Piper: So, you could say because people were forgoing commercial aviation, smaller aircrafts grew in popularity. Before we wrap up, I’d like to talk a bit about the next generation of aerospace design. How do you see the industry evolving over the next decade or so, especially for Piper Aircraft in particular?
Michael O’Shea: Everybody seems to be pushing really hard into electric and autonomous aircraft, whether it’s a general aviation aircraft that they just make electric propulsion or you see some of these eVTOL (electric vertical take-off and landing) vehicles for air taxis and stuff. Everybody seems to be really into doing electric aircraft. And with that, there’s been a lot more composites because of their strength-to-weight ratio, and they’re trying to maximize battery life. So, it’s a good option. Every once in a while you hear about companies still trying to pursue supersonic aircraft. There are a lot of startups that have a lot of backing from big investors. And a lot of the time, you need that to push some of these ideas forward.
Jennifer Piper: So it sounds a lot like the trends that are happening with the automotive industry as well. What would you say Piper is doing to adapt to those new demands?
Michael O’Shea: Some of those demands were electric, autonomy, and customization that we discussed. Piper specifically, in July, we announced a partnership with CAE to develop an electric conversion kit for our Archer. CAE is a major aerospace training solutions corporation. Once they certify that kit, they’re going to convert two-thirds of their Archer fleet to electric. And then they plan to market that kit for third-party use. So, anybody with an Archer, theoretically, could convert it to electric. For autonomy, we discussed earlier, Piper was the first to market with Garmin Autoland integration, and there’s more on the horizon with autonomy at Piper. And for customization, interiors are the primary offender and everybody just wants to customize everything, so we try to keep up with those changing demands and be able to give customers what they want so they can feel like their plane is unique.
Jennifer Piper: And what does the future of design look like to you as a lead engineer?
Michael O’Shea: The future of design seems to be going towards rapid prototyping. Even in NX’s latest update, you can see that there are a lot of new tool renovations for rapid prototyping. And this makes sense with the Additive Manufacturing 3D printing part, everything’s quick. So, it’s great for quick conceptual designs and prototypes, you reduce iteration times and mock-up times. There is an important aspect though to not lose sight, I think, of parameterized design. So, rapid prototyping is great for development and getting concepts refined really quickly. But the engineer still needs to maintain control of the design by using like expressions and input parameters and just using parametric design. And NX gives you the capability to do both; you can rapidly prototype and then you can go back and parameterize your designs.
Jennifer Piper: Well, Michael, thank you so much for joining us today, it was great chatting with you.
Michael O’Shea: Thanks for having me. I appreciate it.
Jennifer Piper: Thank you to our listeners for tuning in to today’s episode. Join us next time for more discussions about the latest in design innovation and software applications. I’m your host, Jennifer Piper, and this has been Next Generation Design.
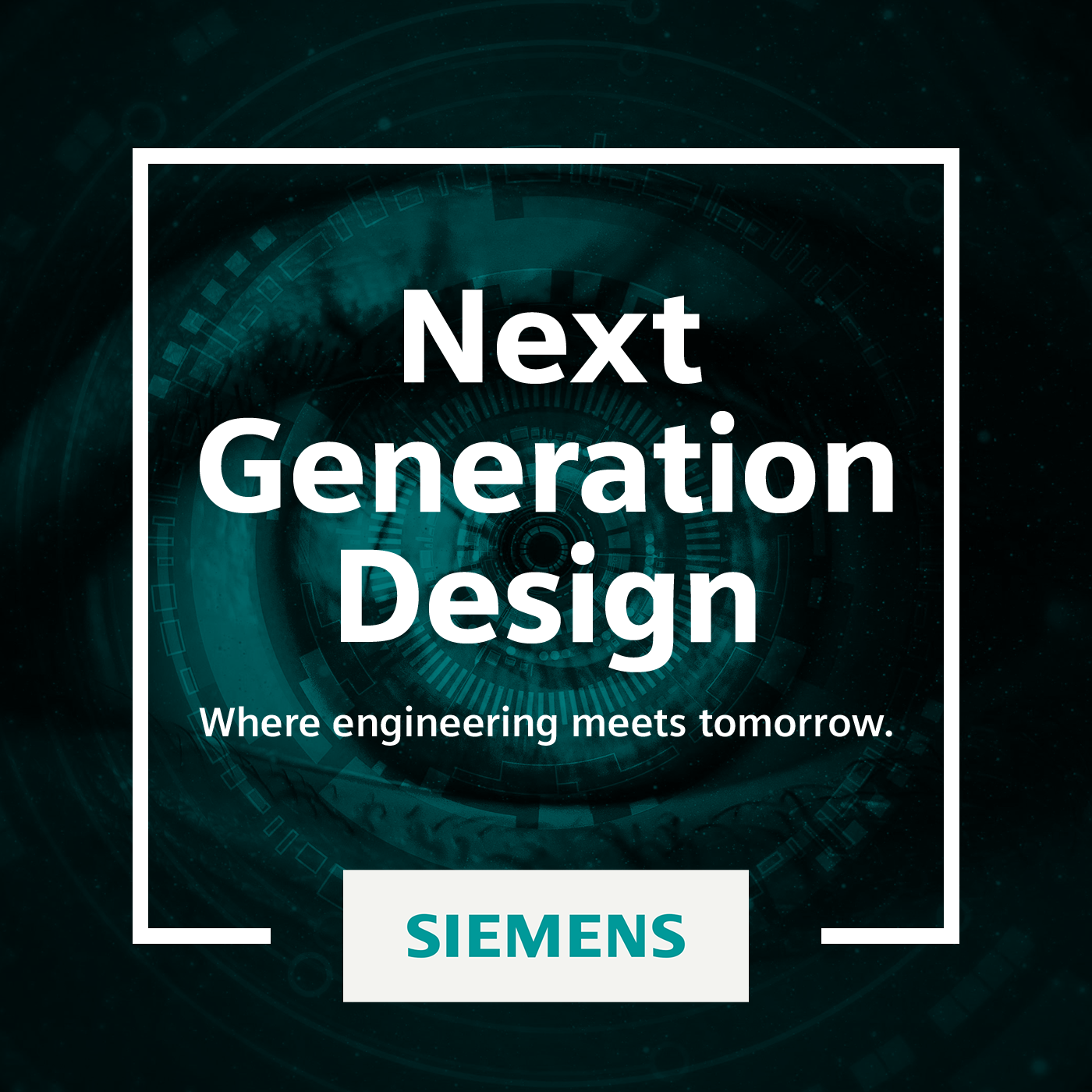
Next Generation Design Podcast
As product engineering tools continue to morph and expand at speeds human expertise may not be able to endure, Revolutionary design technologies that span beyond industry borders, will prove their necessity for companies looking to take over their markets in the future. What will the future of design technologies and machinery look like? What will your digitalization story be? Where engineering meets tomorrow.