The Industrialization of Additive Manufacturing During COVID-19
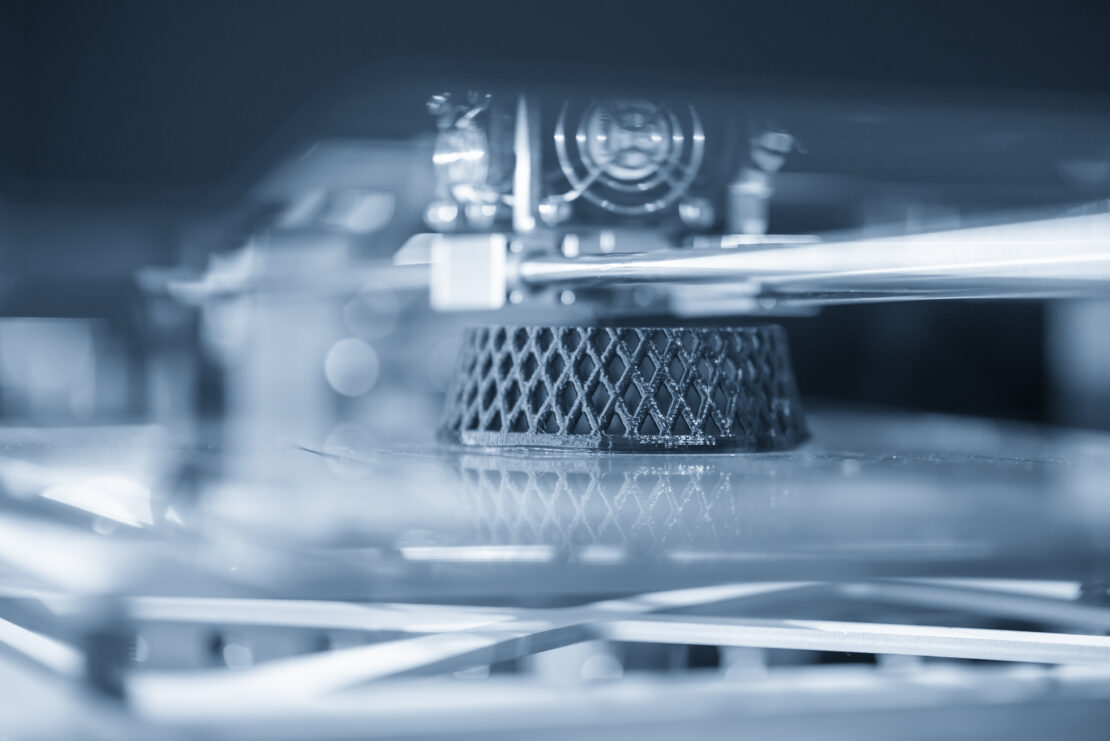
What has COVID-19 meant for additive manufacturing? Has this crisis helped push it into the industrialization stage? Additive manufacturing has been primed to move out from the strictly prototyping technology area, to a more industrialized position to revolutionize design engineering and manufacturing for quite some time. The industry was set up and ready to respond to help our world get through this global COVID-19 challenge, to quickly help with personal protection equipment for instance. This was possible because unlike other manufacturing processes, there is no need for a large upfront investment in new tools such as molds, and users are able to print in a large variety of different materials.
On this Episode
On this episode of The Next Generation Design Podcast guests Tod Parrella, Boris Lauber, and Tom Van’t Erve sit down with host Jennifer Piper to discuss industrialized additive manufacturing: the challenges it has overcome and the opportunities that lay ahead for those industries that have begun to apply it in their processes.
What is Additive Manufacturing?
What is additive manufacturing? Is it the same as 3D Printing? While the guests on this episode have their opinions, they say it is very much open for interpretation. Consensus says, while some use the terms interchangeably, 3D Printing is more applicable for in-home desktop applications where as additive manufacturing is better suited for industrialized processes. Additive manufacturing simplistically refers to the adding up of material to a design; whether it be powdered metal or welding rod, until you reach your part. This is a break from the traditional subtractive manufacturing which is machining from a big piece of material down until you arrive at your desired part.
Additive Manufacturing in Design
When we think about the possibilities of additive manufacturing from a design standpoint, what should be considered? Some of the questions that may come to mind include: How would we reimagine this deign to make sure of the benefits of additive manufacturing? Could we take this multi component assembly and condense it down into one, more complex, 3D printed part? How would we do that, what are the design considerations? These are the questions we explore in this episode of The Next Generation Design podcast.
AI, Machine Learning, and Additive Manufacturing
If recent forays into industrialized additive manufacturing are any indication, many more companies and industries will begin to apply this technology as a routine part of their manufacturing processes. As it evolves the possibilities of AI and Machine learning integration, and closed loop monitoring and control systems are just the start of where this technology could go in the future.
Jennifer Piper: Welcome back to another episode of Next Generation Design. I’m your host, Jennifer Piper. Today, we’re talking about industrial additive manufacturing. We have three guests joining us from the Siemens Software team, and they’ll be giving us some insight into the design, simulation, and building preparation that goes into additive manufacturing at the industrial level. Tod Parrella joins us from the NX design team. Tell us about what you do with Siemens, Tod.
Tod Parrella: Hi, Jen. Yes, my name is Tod Parrella. I work in the NX Design Product Management organization. I’m the Manager of the Industry and Design Product Management team within the product engineering software. My background – many years as an applications engineer in the software industry; prior to that, also a design engineer at a number of consumer products goods companies. My current role as a manager and leader of design is setting the vision strategy and direction for NX CAD in terms of what we deliver to market. Specifically, for me, I’ve been very focused working with this additive manufacturing team within Siemens in the tools and technologies and the workflows on the design side – so, what it takes to design a part that’s suitable for additive manufacturing.
Jennifer Piper: I asked Tod how additive manufacturing has demonstrated potential during COVID-19. Has this crisis helped push it into the industrialization stage?
Tod Parrella: Well, there’s been a lot going on, quite frankly. We’ve been talking for quite a while about how this industry has been primed to really move into the industrial phase of manufacturing process out from the sort of a purely prototyping type of technology. Companies have been seeing, for the last few years, some real opportunities to revolutionize the way that they design, engineer, and manufacture products, because of the possibilities that additive manufacturing provides. And many of them have been on this track to realize additive manufacturing as a truly industrialized manufacturing process, which means a lot of different things that we’ll get into in more detail. But I’ll just say that that had been happening for a number of years. Companies had been seeing the opportunities to use additive manufacturing. Because of that, I think the industry was really set up and ready to go to respond to a situation like we have today, where they could actually turn this technology around and start using it towards the application of solving some of the problems that we’re having and helping to protect our first responders and also helping to protect the people who have been diagnosed with COVID-19. So, it was really appropriate timing from this technology’s perspective to help out and help our communities and our world get through these challenges.
Jennifer Piper: Tom van ‘t Erve works in NX Additive Manufacturing, build preparation. Tell us about your role, Tom.
Tom van ‘t Erve: Okay, thank you, Jen! I’m Tom, I’m Dutch. I’ve been working for Siemens for 25 plus years. I’m a mechanical engineer. For the first 20 to 25 years of my career, I’ve been doing CNC machining in the software development area. And for the last five years, I’m responsible for all our software development on the manufacturing side on build preparation for additive manufacturing.
Jennifer Piper: Can you give us some examples of additive manufacturing production during this health crisis?
Tom van ‘t Erve: A key thing in my mind is that a significant number of companies have started to move towards the industrialization of additive manufacturing. And these front runners have moved from producing just prototypes to producing production parts. They’ve moved from small batch sizes to larger batch sizes. They’ve moved from testing and validating a fairly new and exotic manufacturing technology into a productive use of additive manufacturing, as just another manufacturing process. Basically, just another tool in the toolbox. This trend together with some of the key strengths of additive manufacturing, such as geometrical complexity comes for free, or you don’t need a large upfront investment in tools such as molds, and you can print a large variety of different materials, makes this a unique technology to quickly help, for instance, in this case, with the industrial manufacturing of personal protection equipment.
Jennifer Piper: Before we dig any deeper today, let’s define what additive manufacturing actually is. A lot of people might say it’s 3D printing. But what do the experts say?
Tom van ‘t Erve: I think 3D printing really came up as a terminology more for the home use, the desktop use. I think additive manufacturing is a better-suited term for the industrial processes that Siemens is focusing on. But that’s just my opinion. I’m sure there are better answers.
Tod Parrella: I’ll just add one thing. In the manufacturing world, that word often had a concept of subtractive manufacturing – machining from a bill of material, a big piece of material, and machining that down until you’ve arrived at the product. Additive manufacturing was the terminology which was the exact opposite – starting from nothing, starting from powdered metal or welding rod, and building up additively adding material to the design until you arrived at the part. In a sense, they are interchangeable, absolutely – and it may be more technical depending on which direction you come from.
Jennifer Piper: Before any manufacturing can take place, there’s an important process that needs to happen. Testing, gathering data, and learning how a new product will behave is not only cost-effective, but it saves time and materials. That’s where the simulation comes in. Boris Lauber, from the NX additive manufacturing simulation team also joins us today.
Boris Lauber: My name is Boris Lauber. I’m part of the product management team for simulation, so I’m mainly responsible for our tools for simulating the additive manufacturing process. I’m about 12 years in the company now I was working mainly in simulation as a pre-sales and application engineer. And now, I moved to the product management team, and I’m working on additive and also on generative design.
Jennifer Piper: Boris, tell us how simulation works and why communication is so important.
Boris Lauber: We see simulation techniques used a lot along the process chain of additive manufacturing. When I started 20 years ago, with topology optimization, we used the technique to lightweight designs – to get design ideas – but nobody really thought about manufacturing those parts. Now, we have manufacturing techniques that allow us to directly take what we simulate and put it on a printer and get a physical part out of it. So, the importance of all the simulation gets inside the whole process and it gets really very tightly tied inside. And I think all the different disciplines get more and more connected. So, it’s not having a CAE engineer and a design engineer separately, but they’re closely communicating. In many processes, it’s one and the same person. It gets really quite challenging and more and more simulation techniques are, of course, used all across the process for assessment and also for prediction.
Jennifer Piper: The process of additive manufacturing comes with a lot of benefits. In order for these benefits to be applied, we have to first create a digital twin. Tod tells us what that means from the product side.
Tod Parrella: So, the product digital twin is about a lot more than just the geometry or the form of the product, but it’s about how it functions. It’s about its performance. So, the digital twin of the product needs to consider the material usage of that product, its weight, its strength characteristics. All of the functional characteristics have to be captured within that product digital twin. If it’s a product that has airflow or acoustics or vibration, all of this is captured in that digital twin. So, it contains everything that you can see and feel and test on a physical component or an assembly, but in the digital world.
Jennifer Piper: For an example, let’s turn to Tom and see how the production team adapts as they process information provided by the digital twin.
Tom van ‘t Erve: If your designer has good reason to put a certain surface finish and dimension accuracy on his design because it has to fit into an assembly and otherwise it won’t function, he puts that product manufacturing information – PMI – on his design, and then he asks the manufacturing team to then go produce that part. So maybe the first thing we do is we use some of the manufacturability checks and simulation to see, can we actually produce that? So, we go back to additive manufacturing. Maybe we orient the part, we do a thermal simulation, and we see how the part, under its manufacturing process, under additive manufacturing, for instance, powder-based fusion, how it would distort? If that distortion is bigger than the tolerances that the designer has specified, then we can throw our hands up in the air and say, “Well, we can’t produce it.” Or we can say, “Well, we can print it, but if we really need to meet those design specifications, we need to print it a little bit bigger, so that we have enough stock to then subsequently in the next step, go CNC machine some of the critical surfaces and then meet the requirements.”
Jennifer Piper: From the simulation perspective, Boris’s team really has to think from all sides of the product equation and consider every possible outcome before moving towards the production phase.
Boris Lauber: For example, if we build something up, maybe it is extremely interesting to see what is the acoustic performance of the part. But, at the same time, we need to know about the thermal behavior and the strength – and all these kinds of different disciplines can be just added as properties to this kind of virtual representation; and then, also to do some optimization steps upfront to really be able to be fast during the development and to get quick feedback and enhancing the capabilities and strengths of the product.
Jennifer Piper: Connecting all of this information between teams is critical. Tod explains.
Tod Parrella: So, the connections between design, simulation, and manufacturing are more important than ever to realize a truly industrialized additive manufacturing process. They’ve always been there in traditional processes, but more so, with additive manufacturing, the interdependencies are so much more critical to get right, in order to realize this as a truly industrialized process.
Jennifer Piper: With any growing industry, there are inevitably challenges that have to be met in order to move forward. Tom shares some of those earlier trials and development in quality control.
Tom van ‘t Erve: Five years ago, you could try and print a part today and get a certain quality. If you would print it two weeks later, you would maybe get a different result. And that’s really not what you can expect and can accept in an industrialized manufacturing process. So, you need to be able to have a repeatable quality process that will give you the part characteristics, the material properties, and you’ve got to certify that. Because let’s assume for a minute that you’re printing a part that goes up in an airplane. That needs to last for 30 years, it is not allowed to fail, we don’t want to hear about planes dropping out of the sky. So, you need to do a lot of material research, you need to do a lot of material certification, process certification, because if you take the exact same material, but you vary your process slightly – for instance, different layer thickness, different laser powers, different scan speeds – you may end up with different material properties, different microstructures, and your part may behave differently. It may look geometrically the same, but it may be prone to failures, more than not. And that’s really what you need to prove. You need to prove that to the authorities, you need to prove that to yourself, and you need to make sure that you have your process under control, that it is repeatable, and that is reliable. And that is still a challenge.
Jennifer Piper: Once changes from the simulation side have proven successful, I asked Tod what they have to think about in terms of design.
Tod Parrella: How would we reimagine this design to make use of the benefits that additive manufacturing can provide? One simple example is, “Could we take this multi-component assembly, and could we actually condense it down into one more complex, one 3D printed or additively manufactured part? And how would we do that? What are the designs considerations we need to take into account in order to do that successfully?”
Jennifer Piper: I asked Boris about a recent additive manufacturing success story where they were asked to redesign a part for Hewlett Packard.
Boris Lauber: There was a part selected that was an intake cooling duct. And the challenge, in that case, was not only to have a good design – a lightweight design, or a low-stress design – but the requirement here was mainly on the flow side. So, to have an increased airflow at the end increased the performance of the machine itself. So, in that case, a different kind of generative design technology was used. It was not, I would say, the standard long-year experience topology optimization generative design capabilities that it’s existing for quite some time, that is mainly doing structural analysis and structural optimization. In that case, it was an optimization based on the fluid flow. So, the channel flow was simulated, and an optimum channel flow was generated with minimum pressure drop and constant pressure profile to really optimize that kind of structure. And you can imagine these structures are really quite bionic designs that can only be manufactured by the additive manufacturing process.
Jennifer Piper: Sometimes, there can be additional benefits that we didn’t expect. Tom explains how being meticulous and going through the entire process created an added benefit.
Tom van ‘t Erve: This technology allowed HP to increase the airflow by 22% just by going through this topology optimization, multidisciplinary multi-objective, and not just looking at the weight or the structure. But a 22% increase in airflow allowed the machine to run 15% faster and reduced the part count of the whole assembly by 10%. So, part consolidation is another key advantage of additive manufacturing. With our tools, we were able to do that innovation process in just 25% of the time it would normally take to do such a significant innovation. So, significant benefits that were worked out, were proven by using these technologies.
Jennifer Piper: Which industries are starting to see the benefits of this type of technology?
Tom van ‘t Erve: I have been exposed more and more to the medical industry where additive manufacturing has been growing quite significantly. For two reasons: people have been able to manufacture parts, standard parts – for instance, complex lattice structures that allowed bone ingrowth that couldn’t be manufactured any other way. But the trend there is really going to patient-specific implants.
Tod Parrella: Manufacturing flexibility is very attractive. Additive manufacturing is very attractive to the opportunity to be much more flexible in your manufacturing. For example, going back to where we are today with some of the challenges around the world, the ability to bring production anywhere needed in the world to address, serve printing products for our medical responders, that’s an unbelievably big benefit that they’ll get from that – to bring manufacturing to where the challenges exist. And that’s true today with the current challenges. That’s also true when you’re an oil and gas company and you are at remote locations around the world and you have a part that breaks, you would like to maybe possibly use additive manufacturing, print something locally, so you could get that power generator up much more quickly than the traditional processes.
Jennifer Piper: Tod shares his predictions for the future of additive manufacturing.
Tod Parrella: I believe you’re going to see the use of artificial intelligence across our digital solutions, which is going to be implemented very pervasively across the product – and additive manufacturing will be a beneficiary of the implementation of artificial intelligence and machine learning inside of our technologies.
Jennifer Piper: There’s also an opportunity for simulation to play a greater role in the future. Boris explains.
Boris Lauber: The simulation in the future will give more feedback to the manufacturing side. So, for example, if we want to build the part and we see there’s a problem, how should the supports be changed? What can be done to remove that problem? And all this in the virtual world before building the parts on the printer.
Jennifer Piper: For the manufacturing process, the future is all about identifying potential problems before they happen. It requires tight communication on multiple fronts.
Tom van ‘t Erve: That’s where simulation, artificial intelligence, machine learning, close-loop monitoring, and control systems all play a role and help us move forward.
Jennifer Piper: Thanks for joining us today on this podcast! I’m your host, Jennifer Piper, and this has been another episode of Next Generation Design.
Jennifer Piper: Siemens Digital Industries Software is driving transformation to enable a digital enterprise where engineering, manufacturing, and electronics design meet tomorrow. Our Xcelerator Portfolio helps companies of all sizes create and leverage digital twins which provide organizations with new insights, opportunities, and levels of automation to drive innovation. For more information on Siemens Digital Industries Software products and services, visit www.sw.siemens.com or you can also follow us on LinkedIn Twitter, Facebook, and Instagram. Siemens Digital Industries Software – where today meets tomorrow!
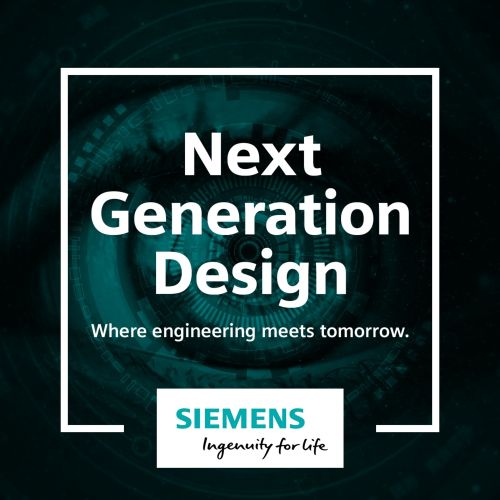
Next Generation Design
As product engineering tools continue to morph and expand at speeds human expertise may not be able to endure, Revolutionary design technologies that span beyond industry borders, will prove their necessity for companies looking to take over their markets in the future. What will the future of design technologies and machinery look like? What will your digitalization story be? Where engineering meets tomorrow.
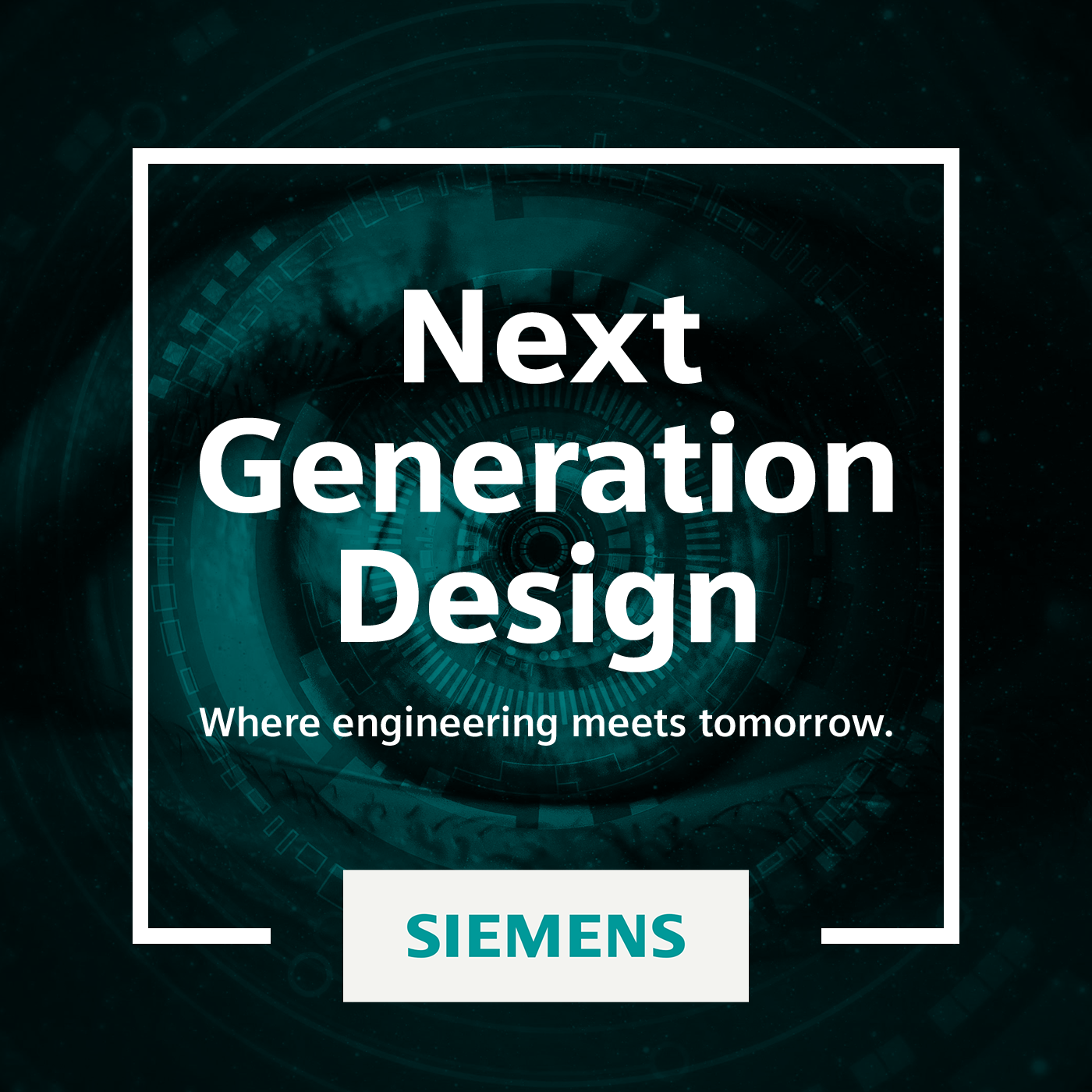
Next Generation Design Podcast
As product engineering tools continue to morph and expand at speeds human expertise may not be able to endure, Revolutionary design technologies that span beyond industry borders, will prove their necessity for companies looking to take over their markets in the future. What will the future of design technologies and machinery look like? What will your digitalization story be? Where engineering meets tomorrow.