The global pandemic and how digitalization is helping electronics manufacturers produce more at lower costs
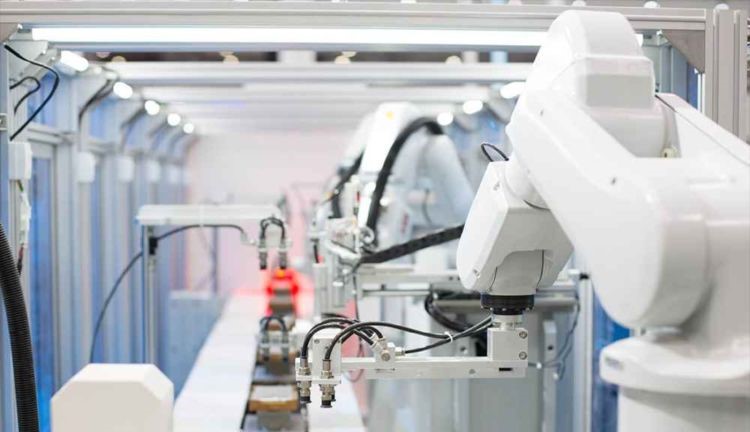
In our fourth episode of The Voice of Smart Manufacturing, we will talk with Oren Manor about the impact COVID-19 had on the electronics industry from manufacturing disruptions from lockdowns to increased supply chain disturbances. We will learn how digitalization is working to alleviate these impacts on electronics manufacturing.
[00:10] Bettina Pruemper: Hello, everyone and welcome to the Voice Of Smart Digital Manufacturing, a cross10-part industry podcast dedicated to the industries of tomorrow and how they can be enablers of fundamental innovation and disruption. A place that brings the promise to allow today’s listeners to meet tomorrow’s innovation. I’m Bettina Pruemper and I’m your host with Siemens Global Marketing. Before we start, let’s shortly recap our last episode where we talked with Silvio Saouaf about technological innovations and Siemens Opcenter execution core family. We also discussed how Siemens digital infrastructure and technological innovations are the keys to unlock advancements and innovations to industries at any level. If you missed that episode, go back and take a listen. Today, in our fourth episode, we will focus on the electronics industry. So, we will talk about the global pandemic and how digitalization is helping electronics manufacturers to produce more at lower costs. So, in particular, we will discuss how digitalization is supporting industry manufacturers to speed up the production and innovation to market while lowering the cost. I’m pleased to introduce today’s special guest, Oren Manor. He is the Director of Business Development for Digital Manufacturing at Siemens Digital Industries Software. Hi, Oren, thanks for joining us today. How are you?
[01:38] Oren Manor: I’m good. How about you?
[01:39] Bettina Pruemper: I’m fine. Thanks for asking. So, today we will talk about how digital infrastructure accelerates growth in the electronics industry of the future. But before we start, could you please share a little bit about your background at Siemens?
[01:54] Oren Manor: Sure. So, I’ve been with Siemens now for about nine years. I had originally joined the value division of Mentor Graphics, and since the acquisition of Mentor by Siemens I have joined the digital manufacturing segment, and am now really responsible for our portfolio for electronics manufacturing. I spent all my career really in business development and sales positions around different types of soft software, a lot of manufacturing software, embedded software. And I’m very passionate about technology and I’m really trying to promote the digitalization and automation of electronics manufacturing. And after living in a number of different cities, today I live in Tel Aviv.
[02:42] Bettina Pruemper: Wow. Thank you, Oren. It’s really nice to have you here today. Hopefully, you’re moving towards the end of the COVID-19 pandemic in Israel. It for sure deeply changed our lives and everyday interactions but it also had a huge impact on the manufacturing industries and the market scenarios. So, Oren, also talking about the electronic industry, could you tell us more about the key changes in manufacturing due to the current global pandemic?
[03:11] Oren Manor: Sure, I’d be happy to. And I think we’ve been talking about digitalization for years. And I think for a number of years people were saying, “Do we really need it? I mean, that sounds all great but why can’t I just physically come to the office and physically go to the production lines, and physically meet everybody? And if needed, get on a plane and fly?”. And then suddenly right about 18 months ago, this global pandemic hits us in the face and suddenly all of this talk about digitalization became a real necessity and had massive impacts on how more customers manufacture products and bring them to the market. One thing that’s very significant is social distancing. I mean, you cannot have everybody on the production lines or in the office when you try to practice social distancing. And things that you don’t necessarily have to do on the production lines—like pre-production, engineering, defining the bill of process, preparing the machine recipes—all of this stuff technically can be done far away from the machines and honestly, even from your home. And suddenly, customers started talking to us, “Well, how do we really do that? How do we do some of this pre-production and new product introduction activities away from the production lines for social distancing?”.
[04:26] Oren Manor: The other thing is, manufacturers needed suddenly much more flexibility where they manufacture the products. They really had to move production between sites. Now, we’ve been talking about this for years but people always said, “Well, shipping might be a little bit more expensive now but moving it is such a hassle. Let’s just keep making it in someplace.”. But now suddenly, when COVID hit China, everybody said, “Okay, we have to get production out of China to Southeast Asia.”. But then the COVID leaped over there, so people said, “Okay, let’s get it to Europe.”. And then COVID hit Europe, so people said “Well, let’s get production back over to China.”. But obviously, these production lines are not really identical, and moving them is not that trivial. And you have to have the digital twin and the machines and the software set up in order to be able to do that, to really allow you to walk around these local lockdowns and the inability to travel. I mean, how do we do a new product introduction? We get on a plane, fly to the production lines, and guide them as they do the new product introduction. Well, for the last 18 months, that’s really not something you can do. We see that still, there is a decrease in lot size. The batch sizes are getting smaller and smaller, up to this magical lot size one, and the mix is getting higher and higher. Still, you have to do this with all of these COVID-19 implications.
[05:49] Oren Manor: And maybe the final one was this global shortage of components in the electronics industry. It started because of COVID-19 and the lockdowns where they actually make all of the ICS and chips. But then the automotive industry initially halted the production because they thought, “Well, everybody’s in lockdown, who wants to drive cars?”. What really we all bought was networking equipment – webcams, routers, more computers. Everybody suddenly needed more bandwidth and needed more computers at home. So, they kind of picked up and consumed all of the available components. Now when they want to make cars again, they just don’t have components available. And this means you have to make changes in the design and changes in your supply chain in order to be able to manufacture. If you just want to wait for this specific capacitor, you might have to wait for two years. So, you have to use a similar capacitor but it’s not identical, which again, is creating challenges for you and you have to do revisions, you have to do new products introduction again. So, I would say COVID has probably been the key influencer in this industry if you look at the last decade for sure.
[07:02] Bettina Pruemper: So, COVID really changed a lot. So, Oren, could you explain a little bit more how you managed to support the industries during the COVID-19 pandemic? And in your opinion, which solutions have been crucial?
[07:15] Oren Manor: Well, first of all, I have to say, we’ve been working all through this crisis with our customers – with existing customers as well as completely new customers – in trying to help them to digitalize their manufacturing operations and their whole factory when it comes to electronics manufacturing. Now, honestly, for us it’s easy. I mean, COVID hit, we took our laptop, we went home, we connected it, and we started working. So, as we don’t have production machines, we don’t have a supply chain, for us, it was very easy to move our operations. But for our customers, it’s much much harder. They have physical assets, they have to get the material on the production lines, somebody has to be there to run the production. But we started to work with them on how to create much more automated and unified PCB assembly engineering. So, really what we try to do there is really try to get them a holistic and unified process of how do we take design data, electronic design data – which is usually CAD files, eCAD files coming either from the Siemens Xpedition tool, or additional tools like Altium, Cadence, Dukane – taking a bill of material file, a bomb file which is using an Excel file with a list of components. And really, how do you take that, merge that, and create all of the assets to manufacture it for the first time? Now you need multiple assets here. You need a program for the pick and place machine, you need inspection programs. We use a lot of inspections in PCB assembly, automated solder paste inspection, optical inspection, X-Ray inspection. We use different types of testing equipment, we have to design a stencil, we have to create work instructions. And we have applications that can really do that in one place for all the different machines, for all the different lines, and even for multiple sites. So, some of our customers did it for the whole line, big ones did it for the whole factory, and the really big ones did it for the whole enterprise creating a competence center which sits somewhere at home, at the location with less let’s say COVID implications, and doing this for all of the production sites globally.
[00:09:25] Oren Manor: And STI is really a great example, we have a very nice success story. It’s a European manufacturer who decided – based in the Benelux – not to stop now and halt everything because “Okay, it’s COVID who knows what’s going to happen.”. But on the contrary, they said “This is the great time to go and digitalize. We know we need it, we also have a little bit of time to breathe now because of the uncertainty and we want to be ready. So, when everybody goes back to the full production we’ll be even better.”. And we implemented this solution there and it really works very nice. The other thing we did, and we have a very nice success story with Scanfill, which is really a tier-one contract manufacturer with global operations. And there, we really spent a big effort to get real-time data collection from the shop floor and then understand what’s happening around material availability, the quality, so we can react faster. When you add batches of let’s say 10,000 products, okay you could take some time to fine-tune your process, you could take 100, 200 of the 10,000 PCBs, you will chuck away. But if the old batches are 100, you can’t dedicate 10 PCBs – which is 10% of the batch – to getting your process under control. You maybe have one or two units, so you really need to get very fast data from the production lines so you can really make fast decisions. And if you started great but suddenly something’s happened and the process has gone out of control, you’ve got to stop it because if you don’t stop it, half of the batch can go bad. So, we really did something very nice there in digitalizing this. And also these are not state of the art machines, these are machines that have been around for maybe a decade but we can still connect to them, get the data, and really digitalize the production lines and give global awareness to what’s happening in real-time on the production floor.
[11:23] Bettina Pruemper: I see. That’s really interesting. Now, I would like to focus more on the supply chain. So, what would you say which of these solutions is a real game-changer in supporting production lines?
[11:37] Oren Manor: I mean, we all know that in electronics the primary cost is the components. If you look at an iPhone, for example, it’s like 85% of the cost of the iPhone is the actual components. The workmanship and the actual building of the iPhone is a very small percentage. Anything we can do to optimize the way the material is used has a very big impact on our profitability and therefore has a very good ROI. And of course, anything we can do to reduce the inventory is great. We all know that having excess inventory looks bad on our reporting books from an accounting perspective. But we also need real estate. And a lot of our customers, they built the factory 30 years ago outside of the city, but now the city is all around them. And real estate is very expensive and they just cannot buy more space in their location. So, they have to do that. And that’s why I think really everything around interplant logistics, about optimizing the way material flows inside the factory from the different storage areas to the consumption areas, whether it’s machines, robots, people – anything you do there to optimize that has a very big effect and is probably one thing that we’re a leader in, and really our customers say that as well. And unfortunately, today ERP doesn’t really have visibility there. I mean, once it’s dispatched from the warehouse, ERP loses connection. The next time it hears about it is when the production is completed and the unit is scanned and put on the truck. It really doesn’t know what’s happening to that component in between. Now, if you know where it is, you know that you shouldn’t order more material because you never used the material you dispatched because there was a stop on the line, the worker was late, there was a production halt because there was an electricity failure. Who knows. We can really bring a lot of visibility to that. And Roy – which is a customer that really implemented this – when you listen to the Roy success story and Roy, again, a leading electronic manufacturer in Biella, in northern Italy, where real estate is expensive and where people are expensive, understood that the number one stoppage of the production line is that the material doesn’t reach the machine at the right time. They really implemented this system in order to make sure that that’s not why they stopped production and lose money. Now we’ve also announced, Siemens has announced about three months ago the acquisition of SupplyFrame. And SupplyFrame is really a global leader in design to source intelligence software. Now, this is a real game-changer. SupplyFrame knows for each component what’s its availability, where can you source it from, what price you’re going to pay, should you buy it, is it close to the end of life, but they lack a lot of the real-time data coming from the production lines regarding quality, regarding availability on the shop floor. We’re now going to take these two data sets and merge them. This is going to be a really unique solution and I think our customers really have things to look forward to because as we bring these two data sets together, it’s going to be a real game-changer.
[14:50] Bettina Pruemper: Looks like Siemens is providing some great promises for the future. As we are near the end of this episode, do you want to share anything with our listeners?
[15:00] Oren Manor: I mean, I really think that one thing we can talk about, especially now is digitalization. And digitalizing the factory sounds very scary, right? It sounds like a very expensive, very ambitious project which is going to take years to implement and has a good chance of failing. But digitalization can also be done one step at a time. You don’t have to think of it only as a megaproject with millions of euros invested in it. You can also think of something that starts very small and scales up slowly but surely. We can start from the pre-production and the engineering, as we spoke now, and digitalize that. We can also decide that we’re in a very high mixed environment, let’s start by digitalizing the planning and scheduling. And Siemens has great solutions for planning and scheduling the electronics factory, including the SMT lines, the box build lines, the full system assembly. We can decide to say, “Let’s leave all of that, let’s go with creating the digital twin of the actual manufacturing. Let’s collect data in real-time and visualize that data.”. You don’t have to start with a MAS to do that. You can keep your MAS on the production lines, you can decide to start collecting a lot of quality data from the machines not only the pass-fail but also the actual measurements. Start building this into a big data warehouse and create reports to understand how are you manufacturing, how are your KPIs, how is your DPMO, how is your first best yield, how is your overall equipment efficiency and start to benchmark between the production lines and between even sites. So, really, I think we’re very flexible in how we can go ahead and do that. And we can really sit together, look at the current challenges, look at the key areas and come together with the best kind of process to do that. And that’s what I suggest we can really kind of tailor the suit for a specific customer and work together. And as we get credibility, and as we show results, take more and more steps into becoming the real digital factory of the future.
[17:16] Bettina Pruemper: Great. Thank you, Oren. Thank you for taking the time to discuss such a fascinating topic on the global pandemic and how digitalization is helping electronic manufacturers to produce more at lower costs. So, we are really looking forward to discussing the electronics trends with you within the next podcast episode. Thank you so much for listening to this episode. If you enjoyed it, click the subscribe button and leave us a review and rating to help us spread the message of these extraordinary visionaries. We have recorded over 10 episodes and we want to bring you more exciting content just like this. In the meantime, we will be working hard and putting together episodes for your auditory pleasure. Also, for further information, you can visit us online at siemens.com and use the contact section to reach out to us. This is the Voice Of Smart Digital Manufacturing, and I hope you will join us again for our next podcast episode.
What you’ll learn in this episode:
- The impact of COVID-19 on electronics manufacturing (02:57)
- The support offered by Siemens to the electronics manufacturing industry during the pandemic (06:57)
- The importance of component tracking in manufacturing (11:22)
- How design-to-source intelligence platform – Supplyframe – works (13:57)
- Different digitalization strategies that Siemens supports (14:53)
Meet the expert
Oren Manor is the Director of Business Development for Digital Manufacturing at Siemens Digital Industries Software. He is responsible for charting the future direction of Siemens’ products and technologies for the electronics manufacturing portfolio. Oren has been working in this role for almost a decade, coming from the Valor division of the Mentor Graphics acquisition. Prior to working at Siemens, he worked for Signature-IT and Jungo in business development and sales positioning.
Oren received a Bachelor of Science in Computer Science and Economics from Tel Aviv University.
Connect with Oren Manor on LinkedIn.

The Voice of Smart Digital Manufacturing Podcast
The Voice of Smart Digital Manufacturing is a podcast dedicated to the industries of tomorrow. Throughout 10 episodes, we will invite industry experts to share their experiences on how Siemens enables industry manufacturers – from Medical to Electronics – to become leaders, by leveraging the digital infrastructure to accelerate growth and innovation to market while lowering the cost. This series will shine a light on the road ahead for industries that are willing to embrace change brought on by digital transformation. Hosted on Acast. See acast.com/privacy for more information.