Going digital: CIMdata’s Tom Gill and Siemens’ Dale Tutt talk verification and certification through digitalization
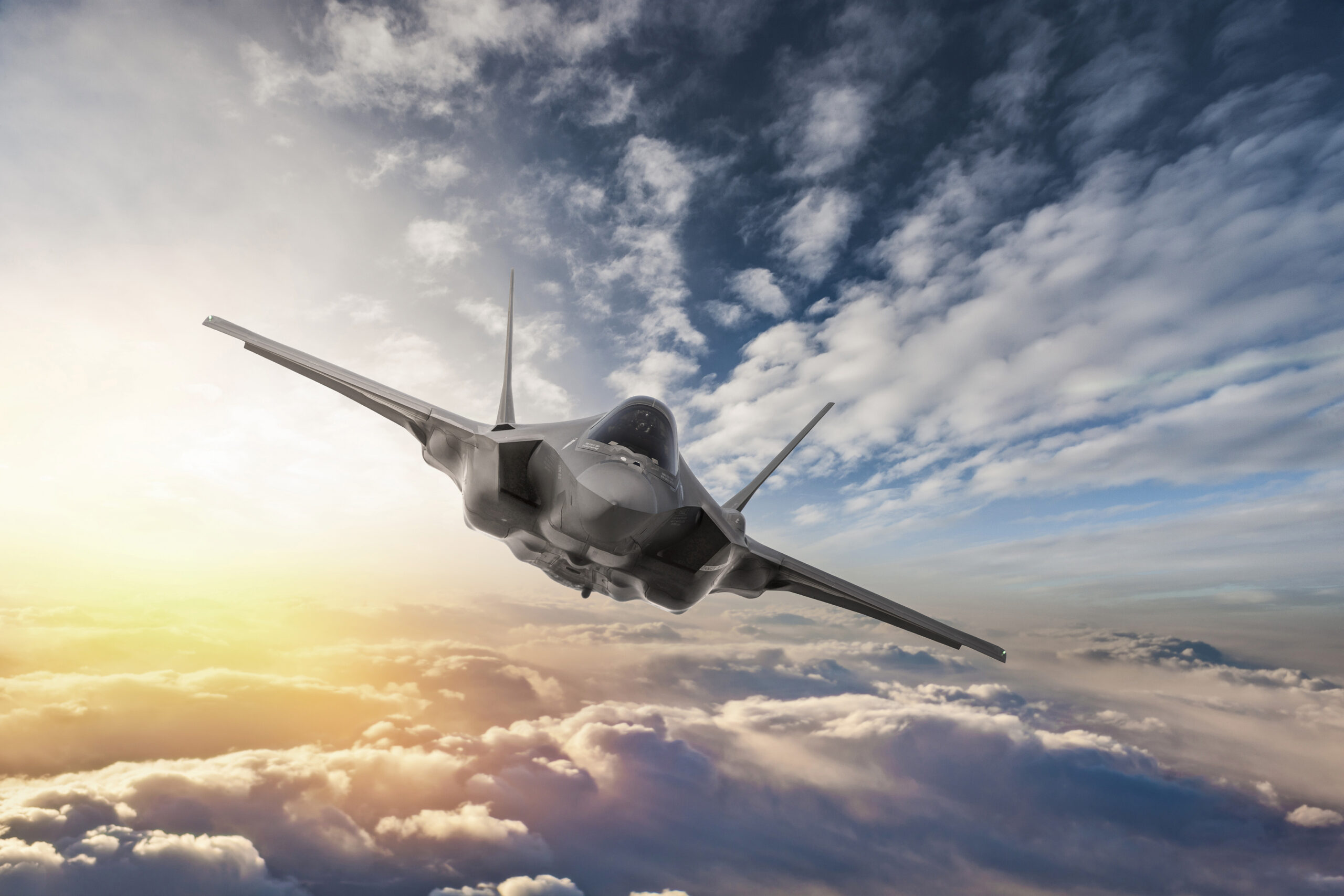
Okay I have some good news, and I have some bad news.
Let’s get the bad news out of the way first. Did you know the cost of aircraft certification is going up? In fact, Rockwell Collins has stated that once upon a time 75 cents out of every dollar spent went into program cost and 25 cents went into certification. Well, with today’s complexity along with other challenges – that ratio has totally flipped!
More costs are going into certifying than developing a system. The problem is exacerbated when you realize most A&D companies are stuck in legacy processes and technologies. As the complexity of product development increases, companies are unable to keep up with the demand.
And the good news?
There are A&D companies out there quickly learning that when they transform into a digitalized enterprise, the cost to verify and certify is dramatically reduced. Established commercial and defense OEMs are verifying multiple systems and subsystems like never before. Things are more electrical. There’s more software. We have new designs. New composites. New types of propulsion. It’s quite obvious old methods and practices must be replaced with a more digitalized approach. We simply can no longer rely on old methods, practices and tools during this time of intense innovation.
Join me as I welcome Tom Gill from CIMdata and Dale Tutt from Siemens Digital Industries Software. We’ll be talking about when companies introduce digitalization into the product development process how they’re able to conduct virtual testing throughout the entire product lifecycle, making certification a whole lot easier, faster and far less expensive in the long run.
It’s an eye-opener, and I hope you’ll join the conversation.
Listen to the podcast now:
“Transforming Certification in the A&D Industry Through Digitalization”
Welcome to Talking Aerospace Today – a podcast for the Aerospace & Defense industry. A place that brings the promise of tomorrow’s technology to the ears of our listeners today.
Building aerospace products is quite a complex endeavor these days as innovative new technologies are introduced, and customer expectations demand ever-more functionality. This presents a big challenge to companies in the A&D industry as they seek to have their products certified by various governing agencies.
But there is some good news…
Companies today are quickly learning that when they introduce digitalization into the product development process they are opening the process up to virtual testing throughout a product’s entire development lifecycle, making certification a whole lot easier, faster and far less expensive.
In this episode of Talking Aerospace Today, we’ll be talking about a digitalized certification process. Joining me is Tom Gill, Senior Consultant at CIMdata and an active member of the PLM A&D Action Group at CIMdata. Tom has over 30 years of experience in engineering design, development and program leadership within the aerospace industry. Also joining me is Dale Tutt, my partner, and Vice President of Aerospace & Defense at Siemens Digital Industries Software.
I’m your host, Scott Salzwedel, and I hope you’ll join us for this highly informative talk on how to improve the certification process among the many obstacles and challenges facing the industry today.
Some questions I ask:
- Could you explain the role that CIMdata plays in the A&D industry? (03:44)
- What can customers expect in terms of certification once they become a more digitalized enterprise? (21:39)
- How does Siemens approach virtual testing? (26:17)
- How does the verification management digital thread work? (29:03)
- What is the role of Xcelerator in A&D? (35:15)
What you’ll learn from this episode:
- Why certification is more difficult for companies still using legacy processes and technology. (06:01)
- The alignment of Siemens digital threads. (07:55)
- The importance of visibility in the supply chain. (12:22)
- Why product certification in the A&D industry is suddenly more challenging. (13:51)
- The benefits of a verification management digital thread. (37:48)
Connect with Tom Gill:
Connect with Dale:
Connect with Scott:
Resources:
Scott Salzwedel: Hello, this is Talking Aerospace Today. A podcast for the aerospace and defense industry. A place that brings the promise of tomorrow’s technology to the ears of our listeners today. And I’m your host, Scott Salzwedel.
Welcome to a special episode of Talking Aerospace Today, where we’ll be talking with our special guest, Tom Gill of CIMdata. Of course, as always, my partner, Dale Tutt, is here too. This promises to be a fascinating discussion with two highly recognized industry experts. I’m excited to have these two join me today.
And what’s the topic of today’s podcast? Well, today’s podcast, “Transforming the A&D Certification Process Through Digitalization” takes a much-needed look into the costly and time-consuming activities around certification. How do we address certification in today’s world when we have more innovation than ever? Urban Air Mobility vehicles are requiring new and faster ways to certify. We’re seeing growing complexity in systems and platforms, which are becoming more integrated. Certification has always been a complex and drawn-out process. And given the challenges of today, how do OEMs and their supply chain even begin to certify?
Well, there is hope. Today, we’re going to discuss the bright light shining down the dark tunnel of aircraft certification. And that bright light is introducing digital transformation into aircraft certification. Now, there’s a lot to discuss here, so let’s begin by first meeting our special guest from CIMdata, Tom Gill.
Hi, Tom, welcome to the show. Could you please tell the listeners a little bit about yourself and what you do at CIMdata?
Tom Gill: Nice to meet you, Scott. As far as my background, I’m a mechanical engineer, and I’ve had a diverse industrial career. I started out working for a couple of machinery companies and used the early Unigraphics CAD software. I get involved in CAD system support, then moved over to the automotive industry where I did CAD support, automation programming using Grip. And then a bit of fun at Element Analysis. And then moved on to Freudenberg-NOK, a tier-one automotive supplier, where I was PLM director and lead the implementation and operation of their PLM solution. And for the past 12 years, I’ve been working at CIMdata as a consultant, where I work both with industrial companies and with solution providers, helping them with PLM strategies and solving tactical issues.
Scott: Wonderful. Thank you. It’s an honor to have you here today. And Dale, could you please share with our listeners what you do at Siemens?
Dale: Hey, Scott, it’s good to be here again with you. What I do at Siemens, is I am the Vice President of the Aerospace and Defense Industry Strategy team. I lead the development for all of the industry activities for the aerospace and defense industry here at Siemens. I work with our customers to help define where we need to invest in new solutions, and where do we need to invest in helping to bring new products and solutions to market for all of our customers. And sometimes, I tell everybody that I represent the voice of the customer here at the company. My background – I joined Siemens from I’d previously been out at The Spaceship Company and part of Virgin Galactic as a Vice President Engineering and then Program Management. And before that, I had about an 18-year career at Cessna Aircraft Company working on a number of different programs. So, I’ve seen a lot of certification activities and a lot of flight test and ground testing activities throughout my career.
Scott: Great. Well, it’s wonderful to have you, Dale. Thanks for being here. let’s start with you. For listeners not familiar with CIMdata, could you explain the role CIMdata plays in the A&D industry?
Tom: CIMdata is a strategic management consulting firm and we’ve got three elements to our business. We perform research, both technical and market-oriented. All the major PLM solution providers use our market numbers to do their business and product planning. We provide education, we have a PLM certification class: we offer both publicly and privately. But the biggest part of our business is consulting. We help industrial companies sort out digital transformation and PLM strategies, select software, and plan their implementations. We also help solution providers better understand the market and get their messages out. We don’t sell or implement software so we can maintain our market independence. And we’ve been operating this way for almost 40 years now. As far as A&D-specific, we’ve really done consulting work with A&D companies since our inception, and continue to consult individually with companies. But since 2014, we’ve been putting a lot of effort into a group that we administer, known as the A&D PLM Action Group – started in 2014 with Boeing, Embraer, Airbus, and Gulfstream, and now includes most of the major airframe and engine suppliers. The mission of the group is to enable the industry to speak with one voice on important PLM-related topics to solution providers, standards bodies, and other interested parties. Within the group, they fund research and CIMdata provides subject matter experts to administer projects and also execute some of the research. We’ve published a lot of papers and have presentations available, and you can get them for no charge on our website. Some of the interesting topics are PLM solution obsolescence – a big problem in aerospace, multi-BOM collaboration and model-based systems engineering (MBSE).
Scott: So Tom, I’m curious when it comes to the state of A&D certification, what are you seeing out there?
Tom: The problem in the enterprise software world today is companies are falling behind because they’re stuck on legacy processes and technology. And as the complexity of the product and processes increase, the demand increases, and they’re not able to satisfy it with their current methods and tools. So, if you look at the requirements involved for both product and for certification, there can be tens of thousands of requirements, and they do change over time. So, keeping the configuration of requirements and how they impact the downstream designs all in sync is really complicated. Currently, they use a lot of manual processes. So, there’s manual transfer data, emails, and things like that to keep things coordinated. It’s easy to have data get out of sync. Also, like all products today, there are more and more electronics and software getting incorporated – aerospace products are no different. And keeping track of the requirements across the integrated systems and the interfaces gets extra hard if you have to do it manually. And if there’s a change, making sure that the proper testing is done to make sure you’re validating all the right data and instances of the data or the physical product, gets ever more complicated. What happens when they get out of sync, something changes in the design or in the plan? Since design planning, testing or validation tends to run in silos, you can really get cascading scheduling impacts with all the complexity involved in the schedule when something goes wrong.
Scott: It’s clear aerospace and defense manufacturers are under continuous pressure to evolve and also just improve how they operate, and this definitely includes new methods for certification. Especially now, we see the emergence of space travel and tourism, the quickly emerging UAM segment, zero-carbon flight. Domains across the entire product lifecycle from acquisition to engineering, design, production, and even into service – they all must improve. Now, Dale, I know Siemens has a lot to say when it comes to the digital transformation.
Dale: Yes, Scott, we do. When we think about all the challenges that our customers face, whether it’s design, development, systems engineering, verification, manufacturing, product support, program management – all of these areas have challenges. So, we’ve organized all of the different products that we have, we’ve organized these solutions into what we call digital threads. And these are really geared towards addressing the difficult business challenges that our customers are facing with an overarching goal of improving the technical performance of their programs, helping them reduce program costs and program schedule, all while managing their program risks. So our digital threads, we’ve aligned these along with the five major functional areas for most programs: engineering, program management, supply chain, production and product support. We’ve identified these digital threads that address the needs of those functional areas within the context of a larger program. And these digital threads stretch across the entire product development lifecycle from the conception of a new product, all the way to the end of life when you’ve delivered product to the customer, and they’ve flown it out for years. These five functional areas probably account for 95 percent of the people that are working in these programs. And so what we really have done with these threads in addressing these is we’ve created these configurable solutions that really tie together and integrate all of the solutions that we have into a stronger digital thread that’s traceable from beginning to end. We’re able to automate some of the workflows within these digital threads so that you’re eliminating all these manual activities, these manual data translations, as well as even things like just keeping track of when work is completed. We’re able to automate some of those tasks and update the program schedule. So when you finish a test, that program schedule automatically updates because of how we’ve automated these solutions. And so, really geared towards focusing on these customer challenges, the business challenges that our customers have, and helping them go faster.
Tom: We see these pressures on all businesses, and especially in A&D. I do want to focus on the supply chain thread that Dale mentioned. As far as verification and validation A&D supply chains have really grown significantly in their size and the complexity and the responsibility that they take on. And so getting that thread under better control is a big win for OEMs and the whole industry. Components get manufactured in sub-tiers, but the higher tier suppliers end up developing systems and subsystems, and those require verification and certification. And then that certification needs to roll up to the OEM. And so making sure that the schedule communication happens with integrated program planning is critical to keep programs on track and certification happening when it needs to happen. Ultimately, the OEMs are responsible for the certification, so it’s up to them to coordinate. That’s been a big change we’ve seen in working with aerospace companies as the amount of collaboration that they’re bringing in with their supply chain. The OEMs, the suppliers as well, the whole supply chain needs clear visibility into production and certification processes so that when things go wrong and schedules change, everyone can update with as minimal impact as possible. By bringing this technology upfront, you’ve got to also address the issue that each company does make its own choice in solutions and tools, and making sure that standards are supported so that data can be exchanged is really a huge challenge that we see and it’s part of what the A&D Action Group tries to address with some of the research.
Scott: You mentioned clear visibility, it’s so critical. Sure, we can talk about digitalization throughout the product lifecycle and how it can seriously help the certification process, but equally important is the visibility into the supply chain.
Dale: Absolutely. To ensure that a program runs on time and within budget, it’s very critical for the OEM to have access to, and really an understanding of, and the ability to respond to the supplier status and the feedback. So, as you’re going through these verification programs, and Tom mentioned standards, how do you help the flow of information? And if customers and companies can work to standards, then that helps them share the information more effectively. But when you think about what these companies are dealing with, the data from all the supplier tests and the certification reports, these are very important artifacts that OEMs have to use to assess the issues, and maybe any issues that are raised by suppliers, they can be used to validate the quality of the design, the product, the supplier performance, and as often is used in certification. So, the OEMs have to be confident in the quality of the supplier data in order to achieve product certification in a fast and efficient manner. So, as you’re passing data back and forth, the OEM is flowing requirements to the supplier, the supplier is oftentimes validating or verifying that those requirements have been satisfied, and then passing that data back in a secure configuration-controlled manner. And so you need to be able to help with that within the processes.
Scott: Let’s go a little deeper now into how the digital transformation impacts product certification. Dale, can we start by first discussing the challenges?
Dale: Within our aerospace and defense, as in many other heavily regulated industries, product certification can be very challenging. And there are different flavors for certification, whether you’re talking about a civil certification for an airliner, if it’s a military aircraft that’s going through airworthiness, or even if you’re a space launch vehicle going through a certification or a verification with NASA – you have to be able to make sure that you’re meeting those standards and that you’re ensuring that the flight and the human safety requirements are met. So, the products must be certified over and over again sometimes. Sometimes we talk about it for, basically, the original design of the product, then your production process has to be certified to verify that you are actually producing what you said you would produce when you designed and tested the product, and then maintaining continued airworthiness throughout the life of the product through maintenance practices, and through how you keep your records. And so each certification process comes with unique challenges, so kind of the bottom line on this. Certifying A&D products is very expensive, and oftentimes, it’s on the critical path to delivery. Oftentimes, by the time you’ve started your certification activities, the aerospace and defense customers have already invested huge amounts of money in building prototypes and pre-production units, and so the certification process really starts from the beginning. But if it fails, if the product fails certification testing, you can’t deliver it, you can’t get certified, you can’t start delivering or operating it until you’ve resolved that problem. And you can’t collect revenue. So, it takes time to resolve these issues, and it can result in huge cost and schedule overruns for a lot of these OEMs.
Tom: From a PLM viewpoint on that process, once you have your certification plan defined, it needs to be executed and the data captured – the test data associated with the appropriate product configurations. And you need to be able to demonstrate traceability, end to end, from the initial requirements through virtual and physical testing to ensure that the product’s verified. So, that’s where the big part of where PLM can help; keeping all that data linked together. The other thing is change control. Within any large program, there are always many, many changes in process and sometimes those changes impact test plans or certification-related issues; could be anything from a design fix, a new requirement for manufacturing, or new materials, that happen during the long development life cycles in A&D. So, you really need to be able to coordinate that all, so that when you get into that certification process, you don’t get big surprises that disrupt things. The other thing Dale mentioned, the different certification types. It’s not just the verification, it’s not just the initial compliance; but it’s that over the lifespan, making sure that they maintain airworthiness, especially in the commercial world because planes are expensive and they generate a lot of revenue, and if it falls out of compliance, it can’t fly, so that’s a huge impact on the business, and there’s many, many things that need to be followed over a very long period of time, decades. So, keeping track of all that documentation is really a serious endeavor to make sure that planes maintain their airworthiness.
Scott: Historically, certification has been a parallel independent process, often done long after the design. But that simply doesn’t work today. It’s just too expensive and costly, and it’s just more complicated than ever. I read in a piece from Rockwell Collins that said, “In past years, 75 cents of each dollar spent would go into the program cost and 25 cents would go into certification.” Well, today, that’s totally flipped! More costs are going into certifying rather than developing the system.
Dale: I’ve watched that, I’ve witnessed that, or maybe I’ve lived through that my entire career, where early on this certification effort was an activity that we did towards the end of the program. But two things really come to mind. I think that as we look at the amount of complexity in these systems, the level of integration between all the different systems now that you have on an aircraft, you no longer have just individual mechanical systems on the airplane, but these are all interconnected electromechanical systems. And there’s really just a lot more electronics and software on all these airplanes, and you’ve seen that growth over the last few decades. And so that’s driven the cost increase for verification, and all that complexity. And then the other thing that we see a lot is that the legacy test and verification processes have been very manual. They’ve been document-driven, or at least document-centric. And even though they maybe have gone to electronic methods, it sometimes feels like digitized paper using spreadsheets and Word documents. And those processes just don’t scale to meet the complexity of the products that we have today. And really, they’re not going to meet the complexity of the products that are going to be coming out in the future with everything, with all the new exciting developments on the horizon. So, you have to move from these document-centric systems and processes. You need digital transformation to really help keep your costs under control, but also to ensure that the products are properly and completely verified and certified. And that’s a key part of also ensuring the safety of the product for our customers.
Tom: So, you mentioned the legacy processes. We still see a lot of those out there in our consulting. And what historically has happened – and is still happening in many cases – is validation is really treated as an after-the-fact process, the proverbial throwing things over the wall. And then the validation team or certification team needs to dig through documents and data to pull together a package to submit to the regulatory authority. Often, it’s done outside of configuration control, so there are always questions about “Did we test the right configuration against the right data?” causing additional loops of verifying the data before you send it in. When you’re doing physical testing, it’s time-consuming and it’s expensive, with complex setups that you often need the schedule a long time in advance. So, if the testing teams are in a silo and don’t have access, or updated access to project plans and the change process, they can get surprised. So, if they get surprised, you end up impacting schedules, and the certification process adding additional waste. And you can understand why that cost metric flipped that you’d mentioned Scott, from 75/25 to 25/75. But with a lot of activities being pushed down the supply chain, it’s even more critical to get a good communication strategy set up with a supply chain, so they’re totally integrated into the program and project management, helping you to ensure that your certification deliverables all come in automatically and are properly configuration controlled and can adapt as the plan changes.
Scott: Wow Tom, so many obstacles. It’s just crazy. When it comes to certification, what can customers expect once they become a more digitalized enterprise?
Dale: Well, within a modern product lifecycle management platform, and with modern solutions, and all the applications, and the digital threads, the digital twin that’s available to us now you’re able to bring various digital or virtual analysis solutions to enable verification and certification to be done more regularly during the design. When you think about this, that as you’re developing the product, that you’re doing virtual testing of it, you’re doing your analysis of it; that helps reduce the chances of finding a problem once you get into your physical test or your flight test program. So, it really significantly reduces the cost and the timelines by identifying these potential flaws or design issues early in the process. When the cost of change is still pretty low, you haven’t built parts yet, you haven’t built any products. And so you don’t have to do as much rework, you’re able to modify the design before you start building airplane components. By converting to a digital paradigm, you also speed up your processes, everything’s a lot more traceable. The artifacts that are necessary for certification are captured as really a byproduct of the daily work. And so no longer when you started going through the auditing process for certification, you have to start running off to different shared drives, different filing cabinets – the data is all contained there. And so the digitalized approach lowers cost, it helps shorten your timelines, and it minimizes the risk of changes, and it really minimizes the risk of all these scrambles that typically happen when you’re trying to find and gather all the certification documentation, or even if you’re just trying to respond to something that happened in the middle of your flight test program, you need to respond quickly so you can get back into your certification process. So, helps eliminate a lot of those risks, versus using conventional legacy approaches.
Scott: What Dale just described, the digitalization of process, opens the door to virtual testing. So Tom, what’s CIMdata’s take on this?
Tom: We’ve got a lot to say. Certainly, A&D products push design and materials to the limits of physics and the logic that are encoded within the products: the software, electronics, and things. In some ways, A&D is behind other industries. Automotive has done more virtual validation, or we see more of a virtual validation there. But the extreme safety considerations of aerospace products, we believe, have driven that somewhat conservative nature, and I think that’s a good thing. Virtual testing’s value is obvious; saves time and money by enabling routine tests to be done in software. It frees up resources, but also the test, virtually, can be done early and often, earlier in the design process before you have the physical product to test. And you can also perform studies that might be difficult to physically test; have virtual sensors to reach into areas that would be hard to physically instrument. Often what we’re seeing is the physical sensors can’t be installed because of space limitations or operating constraints. And if you’re running a simulation using data from physical tests, you can actually predict, for example, in the case of an engine test, if you’ve got the inlet temperature and the outlet temperature, the simulation can model that, and then you have a lot more confidence that the intermediate temperatures within the engine are accurate, and where it’s difficult to install a sensor. So, that really helps a lot, especially in the development side of the product. The other thing with virtual testing is you can run more tests more easily. By adding additional compute resources, you can run tests in parallel, and run many more iterations than you can realistically run physically. You can run a lot more operating conditions that you might not be able to get in the physical world. Also, you can run things closer to the edge of destruction, let’s say, without risking damage to expensive physical prototypes.
Scott: And Dale, how does Siemens approach virtual testing?
Dale: I’m glad you asked. This is a very big deal for us. And I think this is an area where we have a lot of opportunity with the comprehensive digital twin. When I hear the phrase “virtual testing”, I immediately think about “flying it before you build it.” What we’re really saying is with the comprehensive digital twin, our customers are able to build a virtual integrated aircraft, or even a virtual integrated iron bird, which helps to minimize the developmental flight testing. And so you’re able to do your physical test and your flight testing to really just demonstrate compliance and really reduce that period of discovery that often occurs in the developmental flight testing. So, there’s a lot of real advantages here using the power of the digital twin and the digital thread. You’re able to identify these technical issues and the risks as the design is being developed so that you’re fixing problems earlier – as we said earlier – when the cost is still low. And then you’re able to start to minimize your physical testing to only the most critical test cases. Oftentimes in a flight test program, you’ll see flight test conditions really just spread across the entire flight envelope, both through the virtual testing. And as Tom was mentioning, with the addition of using the virtual sensors, you’re able to get a lot more insight into how the product, your aircraft, your platform is going to perform once it’s in flight test. And so instead of just spreading points across the entire envelope and just testing everything, you’re now able to validate the digital twin, how it represents your models, and how it represents the performance of your product, and then really focus on only the critical flight test cases so you’re able to run a much more efficient and effective flight test program. And then finally, you’re able to de-risk your certification because you’re doing this early integration in the virtual world, and then you’re making your iron bird and your simulators more effective. And then that, again, also leads to your overall aircraft program is much more effective from the flight test perspective. So, in recent years, companies have really turned to the digital twin to start ensuring that their configurations are accurate and usable to meet the validation operational requirements for their aircraft platform, for example. So by creating a digital thread, and then using the digital twin to manage all of your verification and validation programs, it really speeds up the design process because you eliminate mistakes, you have fewer changes in your design. And then as your solution improves over time, as you get confidence as you’ve used this on one program and in the next program, both your internal staff and the regulatory agencies, their confidence in virtual testing will continue to improve. And so we’ll continue to see more and more growth of virtual testing as we go forward.
Scott: Well, we’ve talked about verification management as it relates to product validation. But I would imagine there’s much more behind the verification management digital thread.
Dale: Our verification management solution leverages the Teamcenter capabilities to manage large amounts of data in a very robust manner, and we’ve tailored these processes to the aerospace and defense industry. And so these capabilities really range from tracking from your requirements, all the way through your design, analysis, your manufacturing, your testing, and then even into service. And they’re all maintained under configuration control within Teamcenter. And so you’re really easing one of the major issues that’s associated with certification is being able to keep this data properly organized, and then to be able to reference it as you’re going through your certification process and collecting up your compliance artifacts. And so how does this work? Well, with Teamcenter, with the collaboration capabilities, you’re able to support data sharing and communication fully within your team and also within your supply chain, and also with the regulatories for both the initial airworthiness discussions as well as your continuous airworthiness certifications once your products are out in the field. And by leveraging this integrated verification management solution, you’re able to assess your change impact analysis a lot more easily, and how do changes affect different certification artifacts that need to be reviewed throughout the entire process. So, when you do have a change, you’re able to ensure that you have accurate information that can be distributed across the entire enterprise, including your supply chain of those changes. And this traceability that’s enabled by Teamcenter gives the extended enterprise complete visibility to the source data that’s required for certification artifacts, and really improves confidence in both the digital and physical versions of the product. And then, finally, Teamcenter acts as the backbone for multiple digital threads and manages the data representing the digital twin, so that, as I mentioned earlier when as you start to automate these workflows, as you complete verification activities, it’s automatically updating your program schedules because these artifacts are interconnected within the process.
Scott: Yes, and talking about that digital transformation, Siemens has made a bunch of announcements involving major industry wins, which include the likes of the US Air Force and Northrop Grumman. In fact, listeners, if you want details on digital transformation wins at Siemens from the past year, I suggest you Google “Lockheed Martin selects Siemens,” and look for the Siemens blog by Dale. It has all kinds of details and wonderful links.
So, we’ve talked about the verification management digital thread. Dale, is there another digital thread we should be talking about?
Dale: I’ve hinted at this a little bit already, but it’s the integrated program planning and execution digital thread. So, this is much more than just keeping track of the schedule. It really starts at the beginning when you’re developing your initial program plan, you’re starting to create some artifacts, and you’re using historical information to build your initial product proposal and your product plan. And then that connects that plan throughout your program execution processes to really help improve the visibility. So, it brings many of the aspects of a traditional program management system forward by providing visibility to this information on how you’re doing on your project and your schedule, and how you’re doing on costs. And by connecting these deliverables with the project tasks throughout the entire program, whether it’s design release or completion of a test, or even completion of manufacturing process steps, you’re able to create a holistic view of the data that’s being captured in the context that’s much easier for non-engineering staff to be able to consume as you’re talking about the verification process. So, rather than navigating large bill-of-material structures or searching for inconsistent item names, team members are now able to navigate via the work breakdown structure that the program plan is built around, and to really define the appropriate deliverables that they need to do as they do their work. So, while the data in the process management that’s enabled by Teamcenter provides the data authors with these robust capabilities, the integrated program planning and execution solution coordinates these activities across the entire extended enterprise and down into your supply chain. And so you’re ensuring that the engineers and technicians, all the people that are needing access to the data, they’re able to ensure that they complete their tasks on time and within budget. So, the basis of all this is the IPP&E, our Integrated Program Planning and Execution solution uses a common work breakdown structure to really organize all of the planning and all the execution activities so that you create these work packages that help integrate your cost, your schedule, requirements, process inputs and outputs throughout the entire process. And because it’s all connected with the digital thread, this is where the workflow automation starts to come in. As you complete tasks, it’s automatically updating your schedule, so your teams aren’t having to spend a lot of time doing their work and then going in and updating the schedule after the fact.
Tom: At CIMdata, we’re a big believer in that integrated program management approach. Enabling that alternative way to navigate product data is really a time saver within organizations. The engineers and designers understand how to navigate from a BOM, but they’re often the only ones that do. So, it gives an opportunity for others to get much easier access to data. The PLM implementation I did at Freudenberg, that was one of the key things we delivered was program management tied to product data. So, as an engineer released some product data, it would automatically complete the task and the other people would be able to navigate to the data, and it was a huge win for the company. So, we see interest in A&D and taking advantage of that capability.
Scott: What I’d like to do now is change directions a bit. The Siemens Xcelerator portfolio of software and services has been in the news lately because it’s available now as a Software-as-a-Service cloud solution. Now, we could do an entire podcast on that alone. But when it comes to the A&D industry and the digital threads we’ve been discussing Dale, what is the role of Xcelerator?
Dale: The Xcelerator portfolio from Siemens Digital Industries Software contains out-of-the-box solutions that support our aerospace and defense customer’s products across their entire lifecycle, from concept through verification, certification, and manufacturing, and into service. And so we’re talking about a very highly adaptable and open, modern ecosystem that the platform is built on. It’s flexible and open, it’s very adaptable. There are a variety of integrated solutions within Xcelerator that help address the challenges that our A&D customers face, ranging all the way from requirements management to model-based systems engineering (MBSE) all the way into simulation, design, and manufacturing and into service. And so the Integrated Program Planning and Execution and Verification Management that we’ve talked about here today are really two of these digital threads that help leverage the Xcelerator portfolio in solving some of these business challenges for our customers.
Scott: Well, gentlemen, unfortunately, we are nearing the end of this podcast. In closing, Tom, what would you like to leave with our listeners?
Tom: I think the big takeaway is certification is a critical, expensive process in bringing A&D products to market, and that’s right for digital transformation. As Dale said, it needs to evolve from a scavenger hunt to something that gets executed in the course of your daily work, that the artifacts are automatically captured and organized when the work is managed by a proper program planning solution. The extreme and growing complexity of aircraft and related products is making physical testing more costly and time-consuming. And in some cases, impossible. There aren’t enough hours in the day to get all the physical testing done. So, the industry is moving and will continue to move to virtual testing, and the Integrated Program Planning to keep things all organized and under proper control is the path forward. If you haven’t bought into that yet, I would suggest you start investigating it, moving forward with it.
Scott: Good advice. And Dale, any parting shots from you?
Dale: Yeah, at Siemens Digital Industries Software we’ve been enabling digitalization for decades. As we continue to work with our customers on their business transformations, we recognize that in order to achieve your business transformation, you have to have digital transformation. And so part of the solution that we’ve talked about here today, our digital threads are really bolstered by the digital twin, which enables incorporating all the verification management activities within an integrated program management methodology. And so again, your verification management digital thread, as part of these solutions, offers complete traceability from requirements through your verification planning into design and test, really provides easy communication, a verification status through real-time visual reporting throughout the entire process. And most importantly, it gives teams visibility to assess design changes that are inevitably going to occur as you go through a program and really understand the impact of those design changes as you analyze those. And so all of this leads to improved program performance in a faster, more efficient certification process for our customers.
Scott: One of the takeaways for me is verification management is so much more than just product certification. By incorporating the certification digital twin throughout the enterprise and supply chain, aircraft OEMs gain more effective program execution which includes simulation and physical test coordination. So, this in turn reduces physical test costs and improves confidence in virtual testing and certification.
Dale: Exactly… Our certification digital twin ties certification into the overall product development process. So when you start with your planning, customers are able to build in their entire verification and certification plan into the overall program plan. As you start to execute and move into the execution phase for various certifications, customers are going through their developmental testing and analysis, and they’re being able to track the live status of verification and certification activities throughout the entire process. As you move into the audit phase, as you’re going through your final certification phases, customers are able to leverage the digital thread to navigate through all the verification and certification plans and to gather all the compliance artifacts in your means of certification. And then finally, as you go into the maintain phase for your airworthiness, the aircraft certification is not just a one-time activity; you go through that as you design and deliver the aircraft, but you have to build and maintain it throughout the entire life of the aircraft. And so, by using this certification digital twin, users are able to really leverage all of this certification information to accelerate their product evolutions, as well as in-service updates. So, there’s no question that collaboration plays a key role in managing the execution across the entire enterprise, but also with the regulatory authorities, and this is all built on the certification digital twin with a strong digital thread.
Scott: Well said… Thank you, Dale. Alright Tom, Dale, it was a pleasure having you on the podcast. Thank you for your time today.
Tom: Thanks to Scott and Dale’s great discussion. I really enjoyed it.
Dale: Yeah, hey thanks, Scott. And thanks, Tom. It was a great discussion. And Tom, thank you for joining us today.
Scott: If you enjoyed this episode and don’t want to miss any of our upcoming episodes, please subscribe to Talking Aerospace Today on Apple iTunes, Spotify, or wherever you go to get your favorite podcast. We are currently in Season 5 with one more episode planned around zero-emissions aircraft. My name is Scott Salzwedel, and this is Siemens Talking Aerospace Today. I hope you’ll join us again for our next podcast. Until then, bye for now.
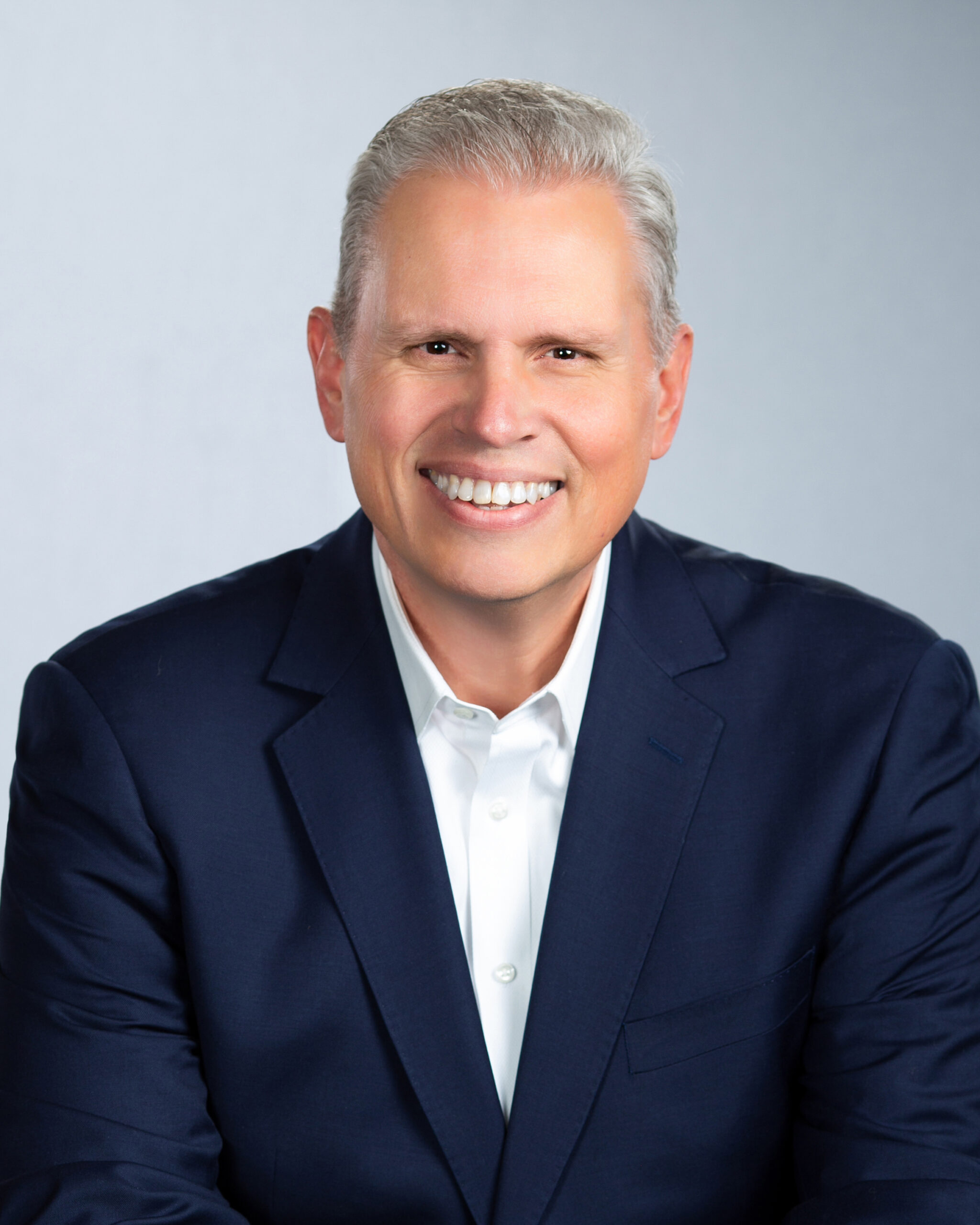
Dale Tutt – Vice President of Industry Strategy at Siemens Digital Industries Software
Dale Tutt is Vice President of Industry Strategy at Siemens Digital Industries Software. Dale leads a team of experts to develop and execute industry-specific product and marketing strategies in collaboration with the global product, sales, and business development teams. With over 5 years of experience in this role combined with extensive experience in the aerospace and defense industry, Dale has a deep understanding of the challenges and opportunities facing companies as they embark on their digital transformation journeys.
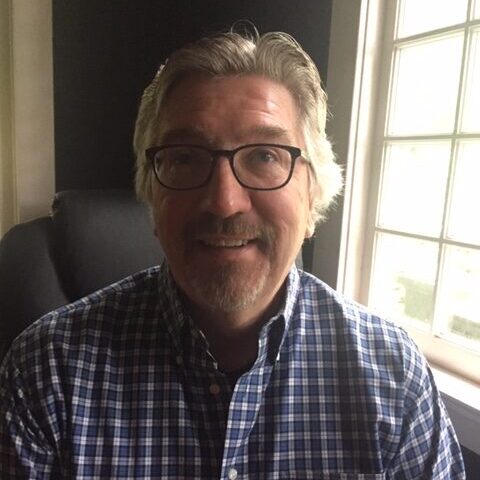
Scott Salzwedel – Host
Scott Salzwedel is senior technical writer and corporate communications writer involved in the Siemens Aerospace & Defense Industry and Siemens Capital. In addition to writer/host of Talking Aerospace Today, Scott is the writer of white papers, articles, blogs, videos and websites at Siemens.
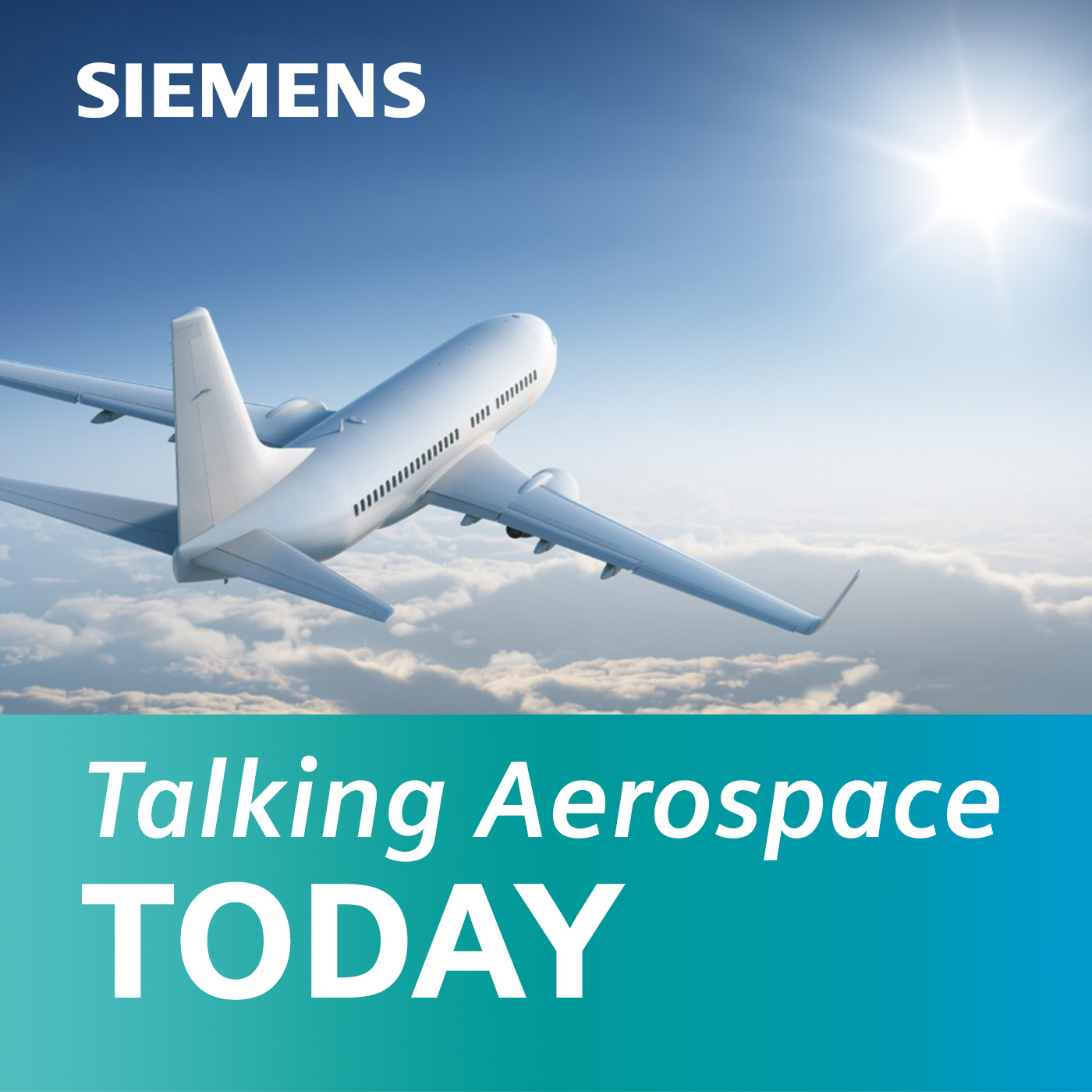
Talking Aerospace Today Podcast
The A&D Industry is at a serious inflection point. Transformation to the digital enterprise has opened up a new era in innovation and technological breakthroughs. However, complexity and compliance continue to hamper the best of efforts.
Join us as we explore how Siemens is turning complexity into a competitive advantage for many of our customers – today and well into tomorrow.