“Zero-emissions aircraft” series (Ep. #4): Production and Product Sustainment
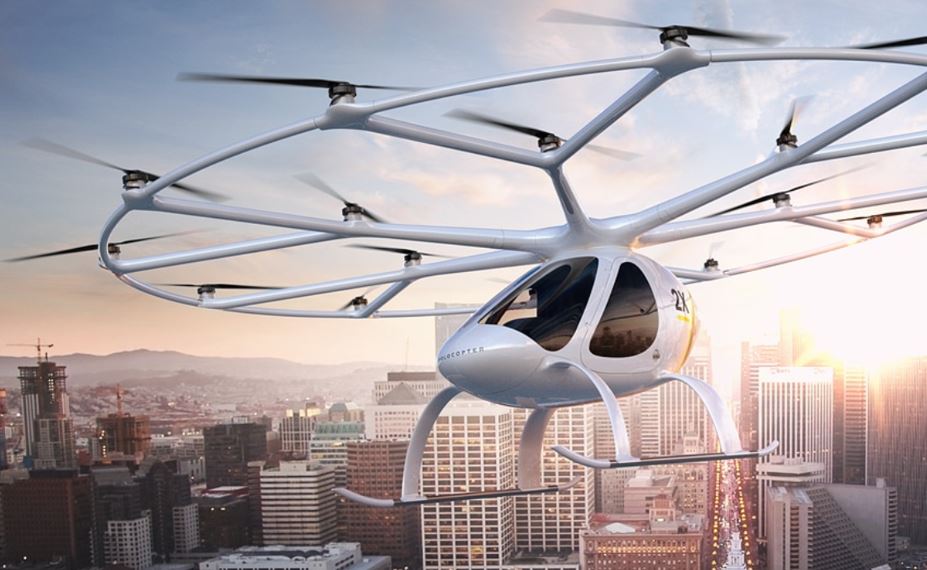
We’re at the stage now where the rotor – or blade – meets the sky.
So far, we’ve gone through conception, design, optimization and certification. Now it’s time to actually manufacture a zero-emissions aircraft. And how does one mass-produce 1,000 eVTOL aircraft per month anyway?
The answer is intelligent manufacturing. And that’s the topic of this latest podcast. Intelligent manufacturing does a lot of things exceedingly well from bringing together engineering and manufacturing disciplines in a closed-loop process to introducing augmented and virtual realities to the factory floor.
Of course, all of this is made possible via the comprehensive digital twin and numerous digital threads.
Intelligent manufacturing and the digital transformation. Two extremely important topics affecting the A&D industry today. I urge you to take a listen.
Listen to the podcast now:
This is episode #4 in a five-part series.
Welcome to Talking Aerospace Today – a podcast for the Aerospace & Defense industry. A place that brings the promise of tomorrow’s technology to the ears of our listeners today.
This is an exciting episode because we’re discussing the actual manufacturing of an eVTOL aircraft. This is the episode where the blade – or rotor – meets the sky. How do you build a great product and stay within cost and schedule? And how do you mass produce these things anyway? To build a high-quality, innovative UAM vehicle within cost requires total optimization of the product as well as the production process.
In today’s episode, “The Zero Emissions Aircraft: Production and Product Sustainment” we’ll be discussing the importance of intelligent manufacturing and its many activities from conception and design, to manufacturing and even into product sustainment. I’m pleased once again to be joined by my partner Dale Tutt, who is vice president of aerospace and defense at Siemens Digital Industries Software. Dale brings a lot of experience and insight to this particular topic.
I’m your host, Scott Salzwedel, and I welcome you to today’s show. In addition to intelligent manufacturing, we’ll also be touching on the importance of the production digital twin and the many digital threads involved in this critical stage of development.
Some really breakthrough stuff here.
In this episode, you will learn:
- How digital threads come together before the start of production. (03:01)
- The role of the digital twin in the production phase. (07:06)
- The difference between the product digital twin and the production digital twin. (10:20)
- How Siemens Xcelerator propels digital transformation. (12:57)
- How additive manufacturing can be used in eVTOL aircraft manufacturing (17:27)
Connect with Dale Tutt:
Connect with Scott Salzwedel:
Resources:
Scott Salzwedel: Hello, this is Talking Aerospace Today – a podcast for the Aerospace & Defense industry, a place that brings the promise of tomorrow’s technology to the ears of our listeners today. And I’m your host, Scott Salzwedel. Welcome to our new five-part series “The Future of Air Mobility: Zero Emissions Aircraft.” In our previous episode, episode three, Dale and I discussed product design and certification of an eVTOL aircraft. We explored how the digital twin and various digital threads are used to develop and certify a zero-emissions aircraft.
In this episode, we’re excited because this is where the blade — or rotor — meets the sky. It’s time to actually manufacture our eVTOL. We have a digital twin prototype and for the most part, it’s been certified. Now it’s time to build. But how can you possibly crank out 1,000 eVTOLs a month? The industry is just not accustomed to high-volume output. What technology or processes need to be in place in order to build as designed? Equally important is sustainment and maintenance once the vehicle is out in the field. These are just some of the topics we’ll be covering in this episode – “The Zero Emissions Aircraft: Production and Product Sustainment.” I’m pleased to introduce my special guest and partner Dale Tutt, who is Vice President of Aerospace & Defense at Siemens Digital Industries Software. Welcome, Dale. Thanks for stopping by.
Dale Tutt: Oh, Scott, it’s really nice to be with you today. And again, thanks for having me. And so, today we’re going to go into production, huh?
Scott: Yeah, it’s that time. As I said earlier, it’s where the blade hits the sky, where the rotor meets the air. So yeah, we’re finally at that point. But before we ramp things up, it might be a good idea to review our progress to date, some of the technology we’ve used so far. So, if you could briefly go back and cover those episodes and hit some of the key points before we go into production, that would be helpful.
Dale: In episode two, we talked about the conceptual design phase, and many of the challenges that are really surrounding the development of a modern-day eVTOL or air taxi — as we’ve been sometimes calling it — and some of the challenges that companies go through as they look at all the different options to decide what vehicle they’re going to build and how does it fit into their business case. And then, in the following episode, which is really the next phase of development into detailed design and into your verification certification phase – during this phase, we solidified our product design, we got into designing all the detailed components and really understanding what the final vehicle is going to look like. And then, we sent it out for certification as we started our testing and certification program.
Scott: Okay, great. And just to be clear, none of this would be possible if we didn’t have these digital threads. And we’ve touched on these digital threads. I think it might be important if you just took a moment and touched on some of the digital threads that are integral to this process.
Dale: When you think about just the complexity of some of these new vehicles, these air taxis, the amount of innovation that’s going on, it’s just amazing what some of these companies are doing. And so, just to provide some context to our listeners, especially those that have joined us for the first time, so far what we’ve discussed is one of our digital threads around Integrated Program Planning and Execution, and how we’ve used that to develop first a business proposal for the program. And then we used that business proposal as the foundation of the product plan as we wrapped up our concept and preliminary design phase, and then transitioned into the later detailed design phase into certification. And you were able to do this because you had a strong basis of estimates from past performance, and you have the systems integrated together so that you can use this strong foundation from your business proposal into your program plan. We used this solution to manage the execution of the program itself. And so, while we didn’t cover it necessarily in detail, but by having an integrated plan, we were able to identify program issues earlier and when we needed to respond to a change, we were able to use the digital thread to really understand the impact of that change and make a much more informed decision on that program change.
We then also talked a lot about Model Based Systems Engineering (MBSE) digital thread. And this is really about managing from a strong set of product requirements. As you move through the different program phases, you then start with that product architecture, you develop your system and your subsystem requirements, and architectures, and all the component-level requirements. And so, it’s really this flow down of the engineering process of requirements and product architectures and systems architectures. And we also used the model-based system safety processes to really drive safety requirements into the product and the systems, to make sure not only that we were evaluating that we could meet those safety requirements for the system. But we also then used those requirements to help drive our product design or verification plan. As we think about, then, the Product Design and Engineering digital thread, this is really getting into designing the product and this is where you can implement some of your agile product engineering processes, with a lot of the activities around optimizing a product using simulation analysis, using generative designs to look at hundreds or maybe even thousands of options quickly to find insights about your product and your solutions that you might not have found with traditional processes where you might have only been able to evaluate, say, 10 or 20 options. And so, you have a lot more power with digital thread and with the digital twin to really look at the most options possible.
And another thing that we used is, where you have this simulation, so we’re basically able to use a virtual integrated aircraft to evaluate the vehicle performance, to “fly it before you build it.” And then, finally, when we started talking about certification, we talked a little bit more about the Verification Management digital thread. Now, we didn’t just start talking about verification management once we got into certification; we started talking about it back in the earliest design phases in concept design, where we started developing verification plans for all of the requirements from the components, the systems in the product level, or the vehicle level. These verification plans, they might include tests, analysis, maybe even design inspections. And we used the digital thread to manage all of the configurations of our analysis models in our test articles. It’s so important to keep all of this in sync with the current status of the design. And then, to be able to link up all of the data that you collect in support of compliance. And so, being able to collect all those compliance artifacts and then report on them to, say, a certification authority such as the FAA, so you can certify your product. And so, that’s how the digital threads between IPP&E and Model Based Systems Engineering, and our Product Design and Verification Management digital threads really have come together through all of these phases to help us get to the point where we’re ready to enter into production.
Scott: We also tapped into the product digital twin, at key moments. Can you explain to our listeners some key points in time when that digital twin really came in handy?
Dale: The comprehensive digital twin itself is at the core of these capabilities and the product digital twin that we might think about — that’s the virtual representation of the physical product — we used that to really drive the optimization using simulation analysis tools on the digital twin. And we used it to do virtual verification, not just through the virtual of integrated aircraft, but through other individual simulations and analysis to really ensure that the product itself was performing as intended to help us identify issues before we built and started testing, doing a rig test or even before we started testing the vehicle to make sure that we effectively addressed all of the risks earlier in the program that we weren’t waiting to physical test to start finding these things. And then finally, another element of the digital twin that we’ll talk about more here is really moving into virtual manufacturing. Because you have the digital twin, you’re able to now start to validate that you can build the product before you start building up your production line and be able to use virtual commissioning — and so, before you start committing a lot of dollars to tooling and building parts and assemblies; the digital twin is really at the heart of being able to more effectively manage and develop new products.
Scott: One point that I would like to emphasize is how manufacturing was present in our previous two episodes. I mean, manufacturing was talked about during concepting. The Verification Management digital thread was already preparing for production way back when. To achieve airworthiness, the verification digital thread is there to verify the as-designed to make sure it’s the same as as-built. The Verification Management digital thread was there. I mean, a key to a lot of this is that verification digital thread.
Dale: As you said, I mean, manufacturing is present throughout the entire process to help drive requirements in your design. But even verification management, you know, we mentioned how that starts at the beginning of the process, not at the end where it’s time to start certifying. And you start using verification planning at the beginning and you use the digital thread to help automatically manage the configurations and the requirements and all of the information. But as you say, it’s not really just engineering. You also have manufacturing requirements that need to be met throughout your program as well, so that as you’re starting to design your aircraft, you need to understand what manufacturing requirements you have. And as you design even your manufacturing line, you have requirements that you need to satisfy, and the verification management thread can help collect up the information to show compliance with those regulations, whether maybe they’re sustainability requirements that you have or safety requirements that you’re trying to meet. You’re able to use a verification process and manage that data collectively, as you stand up your production line; and then, as you start to build your product, you can use these same threads to help verify that the as-built matches the as-designed. So, it’s the same solutions in a little different context, but you’re using a digital thread and the concept of a digital thread to automate these processes across all of your processes.
Scott: When it comes to manufacturing, we use the production digital twin. There’s a huge difference between the product and production digital twin, and I know it’s all part of the comprehensive digital twin that we talk about all the time. But, for our listeners that are just joining us for the first time, could you please explain the difference between the product digital twin and the production digital twin?
Dale: So the product digital twin itself is really focused on the virtual representation of the physical product. So, it’s the 3D CAD models, the simulation models, analysis models, the requirements — basically all the information that’s required to represent your product, your aircraft. The production digital twin, on the other hand, is the virtual representation of the physical production facility. So, in this case, maybe it’s the designs, the simulations, the requirements, the tooling designs — again, all of the information that’s required to represent the factory and how you’re going to build a product, how the parts are going to flow through your product, how the assemblies are going to come together, where you’re going to have people located; all of this information is done virtually to represent the physical production facility. And so, while they’re different, while the product digital twin is really more focused on the product and the production is more on the production line, they come together, they go hand in hand for the virtual verification of your overall business process, that you know you have a product that you’re going to be able to build successfully.
Scott: So, when it comes to that production digital twin, you use it then for virtual commissioning?
Dale: Yeah, absolutely. So, because it represents your production facility, you really get multiple benefits out of your production digital twin. First, you’re able to use it to do the virtual manufacturing. As you’re looking at new concepts, as you’re looking at the design of your product, you’re able to evaluate whether or not you can build it and what it’s going to cost. And so, the production digital twin is a great way to really validate that you don’t have manufacturing issues with your product so that you can still make design changes when you aren’t affecting a process — you know, the production process. But then, when we refer to virtual commissioning, you know, that’s really kind of the final checkout of your factory. I sometimes think about it as you’re effectively doing your first article build virtually to prove out all of your production processes before you start investing in tooling and facilities. And so, this can be done throughout the entire design process as you start to release designs and configurations. But at the end, you still want to make sure that you have everything working as intended — and this is really where the commissioning mindset can come in; you’re verifying that you can actually meet the requirements of your production process.
Scott: I would think, at this time, it makes sense to mention Xcelerator, Siemens portfolio software and services and the nifty application development platform. Xcelerator is what makes all these digital threads come to life and it creates this open and flexible ecosystem where companies can truly embrace their own digital transformation. And they can do it at their own pace. Dale, what’s your take on Xcelerator?
Dale: You’ve captured it pretty well. And I always think about it as, simply stated, you know, Xcelerator is our portfolio of all of our services and solutions, including cloud and SaaS, and managed services. It brings the comprehensive digital twin across the entire product lifecycle. So, from concept design through all of your design, your manufacturing, your testing activities, and even in the product support, you have the digital twin that gives you a rich, robust understanding of how your product is going to perform, how you’re going to build it, and then how you’re going to maintain it. We have the personalized and adaptable solutions that really focus more on configurable solutions and not heavily customized solutions. And doing it in a flexible and open ecosystem, which I think is massively critical. With all the technology that’s out there today, you need to be able to bring in the best technology that you need. In some cases, you have legacy solutions that you’ve used already. And so, by being able to do this in a flexible and open ecosystem, you’re able to operate much more efficiently through all your business processes, and you’re able to bring the best solutions forward to help you solve your business problems. And I think finally, we can partner with companies of any size and scale with their digital transformation with the Xcelerator portfolio because it’s not a one-size-fits-all solution. And so, there’s so much flexibility with it, it’s pretty incredible what we’re able to do.
Scott: I’m just thinking about what we’ve been talking about in the last five to ten minutes. It’s really just been a review of episodes two and three and we haven’t really touched on production. That’s this episode. Let’s get into manufacturing. So, let’s jump into this final phase of development. And so, Dale, what do you want our listeners to understand most about manufacturing?
Dale: First, I would say, remind everybody — we’ve said it before — that manufacturing doesn’t start when the designs are done. The intelligent manufacturing activities really start when you first start conceiving of your product design. And so, as you’re going through your program pursuit and you’re planning your business, or you’re doing your business plans, you’re going through this phase where you’re developing your build concepts – your concept of build phases. And then, as you move into your design phases, you’re designing to build, you’re starting your engineering and manufacturing development processes. And then, you go into your manufacturing planning and, as you start to build, you want to start executing your manufacturing system, so maybe there’s a closed-loop manufacturing, closed-loop quality systems that say, basically, here were our plans and we’ve executed the plans and been able to build what we said we were going to build. And then finally, there’s a learning process — these insights from production. So, as you start to bring the internet of things together with the digital twin, now you’re able to optimize your production processes using continuous improvement. And so, even the intelligent manufacturing is a bit of a closed-loop process, starting with this concept design phase all the way through into sustained production, where you’re still going through continuous improvement.
Scott: We’ve touched on this already, but it really needs further explanation. It’s worth repeating again, but when it comes to manufacturing, especially in Aerospace & Defense, how do you even begin to build 1,000 eVTOLs a month? I mean, the industry isn’t set up for that kind of volume.
Dale: We’re often used to dealing with much smaller quantities. Many companies look at 10 or 20 aircraft a month as a pretty busy month. Some of the larger Boeings and Airbuses, they maybe get up to 40 or 50 per month of some of their production lines. But it’s a much bigger task to go build, say 1,000 a month. And so, there are some lessons that we can learn from the higher-rate industries such as the automotive industry. And the good news is they’re using the same digital tools that we’re talking about here for aerospace. So, there really is an opportunity to reuse that knowledge, the same concepts that we’re talking about here, to build 10, 20 a month more efficiently, are being used by higher-rate manufacturers to produce thousands per month. And so, that’s the good news. And virtual manufacturing commissioning is going to be critical to standing up these production lines as you start to look at how you’re going to build it, how you’re going to get the cycle time down to the point where you need it so that you can build 1,000 a month, you’re going to do it with the same tools that we’ve been talking about throughout this entire episode.
Scott: Yeah. And the other thing is additive manufacturing is quite popular these days. How do you see additive manufacturing applied to this situation?
Dale: I think it’s a great opportunity. I think any discussion with additive starts with the excitement of what you can do and the types and shapes of parts that you can produce much easier than you used to be able to with, say, a machined part or even with some of the composite layups. But it goes without saying that there’s still some regulatory challenges, you know, such as what the industry dealt with when first moving to composites. And so, additive itself is another process-intensive industry that’s going to have to go through some of those same building blocks to demonstrate that you can produce the parts that you say you’re going to be able to produce. And it always comes down to that and it uses a true digital thread from design all the way into manufacturing and into inspection. So you’re able to really maintain that digital environment all the way through the entire process. It will drive different design approaches. I mean, I think that’s what’s really cool and exciting about it, is as you work through some of these other challenges, and start to leverage it, that you can really rethink how you design products. Instead of an assembly of a lot of different parts, maybe you just print a lot of these parts together. And so, it has the opportunity to change how you’re going to build these aircraft and you might be able to get by with less tooling in the shop floor because you don’t need assembly tooling. I mean, if you can start printing these large structures, that’s going to be pretty amazing. But it’s also going to change how you support them. So, can you imagine? Now you’re building thousands of aircraft a day. Can you imagine instead of having a warehouse full of spare parts, that you just have a printer, and you start printing those parts, instead of having the big warehouse? And I think the opportunity for this is just absolutely amazing and it’s going to give a lot more flexibility and I think better operational costs in the long run, both for manufacturing and for product support.
Scott: Yeah… And I like the idea of printing these parts on-premise, just because of a lack of waste; things are designed specifically for that purpose and so, there’s less waste which is very important these days when you think about what’s going on around us.
Dale: A lot of times, when you think about some of these machine parts and how much material it takes to produce a part, you start with 100 pounds of metal and you machine it down to ten or 15 pounds. And now, you can be much more selective in how you apply that and it’s a much more efficient use of material. So it really does offer a lot of possibilities.
Scott: So, one thing we really need to touch on that we haven’t really talked about is that supply chain. By the time we’re ready to manufacture, all the pieces have to be in place. I would imagine, given the struggles we see today with the supply chain, this is something that, in order for it to work, we have to start very early in the process.
Dale: Yeah, so true. The rhetorical question in aerospace is, you know, how many parts do you need to produce the airplane? And the answer is all of them. And that’s why the supply chain is so critical. And so, I think there’s a few things, a few elements. You know, we talked a lot about the flexible and open ecosystem, which I think can provide a lot more visibility into your supply chain without driving a lot of cost into your supply chain. A lot of times, if you’re a supplier and you have to have ten different systems, it’s kind of hard for the supplier to manage. And these are small companies. And so, being able to have the visibility you need without driving a lot of cost in your supply chain is pretty critical. But visibility is very critical in the supply chain. And I think what we learned, like, with the pandemic, is that a lot of companies didn’t necessarily have the transparency in their supply chain, they didn’t have the visibility. So, when they started having hiccups in their supply chain, they were kind of at the receiving end of all of the disruptions. And so, you need this transparency to really understand what are the leading indicators that you’re going to have a supply chain problem. The current indicator today is kind of a lagging indicator, is when your parts don’t show up — and that’s a bad situation to be in. And so, you need the visibility of things that are actually going to indicate that you have a problem coming and you need better mapping of the supply chain, just even to understand your risks and to think about your risk management. I mean, sometimes companies don’t really think about it but, say, you have an engine that’s reliant on a certain bearing, that a supplier has an earthquake or a flood or, you know, some sort of a disaster and they just go out of business. Now, you can’t produce your engines and you can’t produce your airplanes. And so, having an understanding of what their supply chain actually looks like, then when something happens and you have, say, you know, some sort of a natural disaster or something that you can better predict the risks in your supply chain. So, having the digital thread in place with a good supplier collaboration solution is really critical for a lot of these companies.
Scott: Yeah, so very important these days. But more so than ever really, everything we see around us, the importance of the supply chain is so very, very important.
So finally, another integral part of the process that we’ve alluded to is product sustainment and maintenance. So, granted, your typical eVTOL probably has a lot fewer movable parts compared to your traditional aircraft. But still, this is an extremely important topic.
Dale: It’s very critical because you have a lot of new technology out there and the business model for, say, an air taxi is going to be dependent on the fact that the air taxis are actually flying. And so, you have to have a really solid product sustainment plan in place, a good logistics plan with where your parts are going to be, and you’ve got to train technicians, you’ve got to think about how are they going to quickly maintain it wherever they’re at? So, really, I think, the most important part of these business models is going to be how are you going to effectively keep the whole system up and running. And so, you’ve got to be able to support the customer entry into service, the operations that they have during that time — when you just have a few air taxis out there, to when you have thousands out there. You’ve got to be able to track your product reliability and actually be proactive in identifying service issues, so you can identify product improvement, whether it’s maybe improved reliability of the components, but also improved maintenance methods. And so, over the long run, there’ll be changes and modifications, so you have to be able to support those maintenance activities with modification kits and being able to deliver those into the field and to have them be able to be quickly implemented. And so, understanding the as-maintained configuration, we talked about as-built and as-designed, but understanding the as-maintained configuration of each article makes it a lot easier to develop those modification kits so that you can make sure that they can quickly be implemented on your air taxis once they’re out in the field.
Scott: So very important. And I’m sure it’s something that gets overlooked really easily. But yeah, I like our proposed four-passenger eVTOL. I think it’s an excellent zero-emissions alternative. We may have to work on the name a little bit, but at least we have an aircraft. So, this has been a fascinating discussion. It’s been a wonderful digital journey. Dale, any parting shots?
Dale: This is so exciting. I’ve had so much fun talking about this topic along our entire journey from, really, the start to finish of the options of different types of zero-emission aircraft. And then, as we zeroed in on the eVTOL or the air taxi, going through the concept all the way through to design and certification and manufacturing phases. It’s been a fun time and this is very exciting with all the innovations out there. And, at the end of the day, the digital transformation that companies need to undertake in this super innovative environment to be able to accelerate their product development, go faster with the right product, and get it out to the field on time, with these innovative products, there’s going to be new requirements around certification — so, being able to certify reliably and then being able to move into manufacturing quickly, produce thousands a month, and then finally being able to support it. We’re in an era where the digital transformation is going to be able to enable this maybe in a time 20 or 30 years ago would have been a lot harder to do. So, pretty exciting times that we’re in.
Scott: Definitely. Okay, well, we have one more episode left. And, in our fifth and final episode of the series, we’ll be talking about an aerospace company that has experienced its own digital transformation. Now, I can’t say who that is at this time — listeners will just have to check back — but it should be a really great talk, our final episode five. Dale, this concludes another great discussion. Thanks for joining me today.
Dale: Awesome, Scott. And really, it’s always a pleasure to talk with you and have this time with our listeners. And so, I’m looking forward to that final episode. It is going to be a good one and I’m already looking forward to it. So, we’ll be talking to you soon.
Scott: Yeah, yeah I can’t wait. Again, thanks, Dale. Very much appreciated. Okay, so at the top of the show, I mentioned this is a five-part series on Zero Emissions Aircraft. If you’ve enjoyed this episode and you’d like to listen to any back or future episodes, please subscribe to Talking Aerospace Today on Apple iTunes, Spotify, or wherever you go to get your favorite podcast. You can also check out the links in this podcast description.
My name is Scott Salzwedel, and this has been Siemens Talking Aerospace Today. I hope you enjoyed the show and that you’ll join us again for our next podcast. Until then, bye for now.
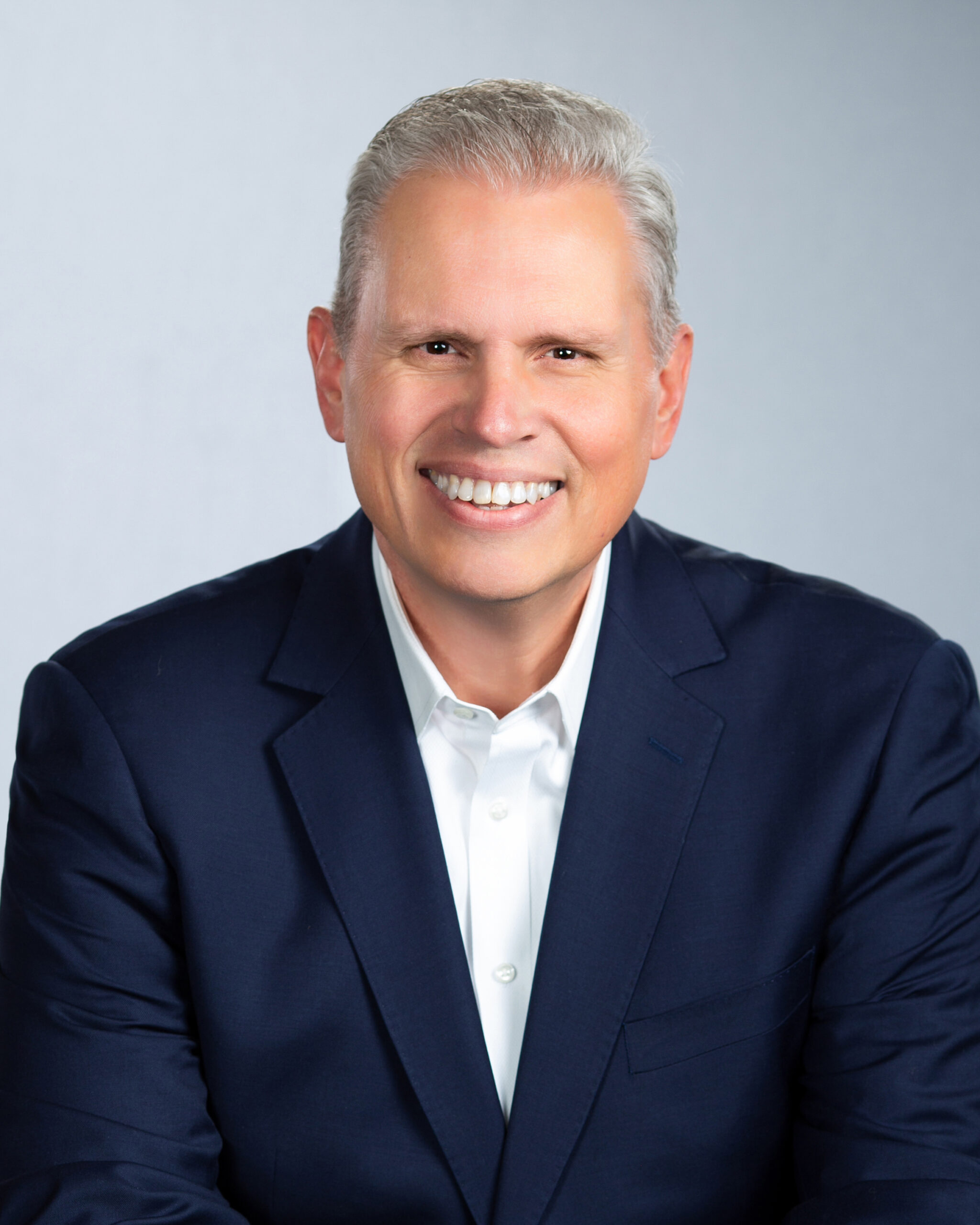
Dale Tutt – Vice President of Industry Strategy at Siemens Digital Industries Software
Dale Tutt is Vice President of Industry Strategy at Siemens Digital Industries Software. Dale leads a team of experts to develop and execute industry-specific product and marketing strategies in collaboration with the global product, sales, and business development teams. With over 5 years of experience in this role combined with extensive experience in the aerospace and defense industry, Dale has a deep understanding of the challenges and opportunities facing companies as they embark on their digital transformation journeys.
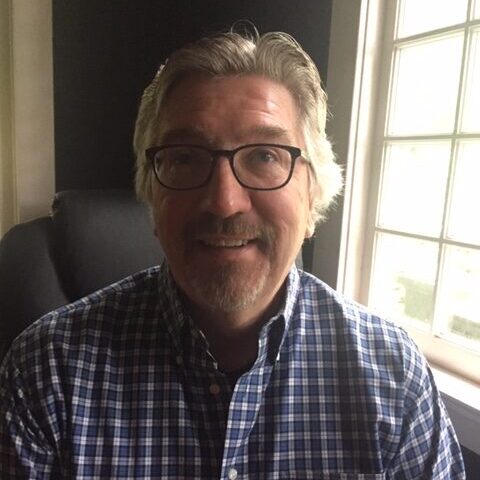
Scott Salzwedel – Host
Scott Salzwedel is senior technical writer and corporate communications writer involved in the Siemens Aerospace & Defense Industry and Siemens Capital. In addition to writer/host of Talking Aerospace Today, Scott is the writer of white papers, articles, blogs, videos and websites at Siemens.
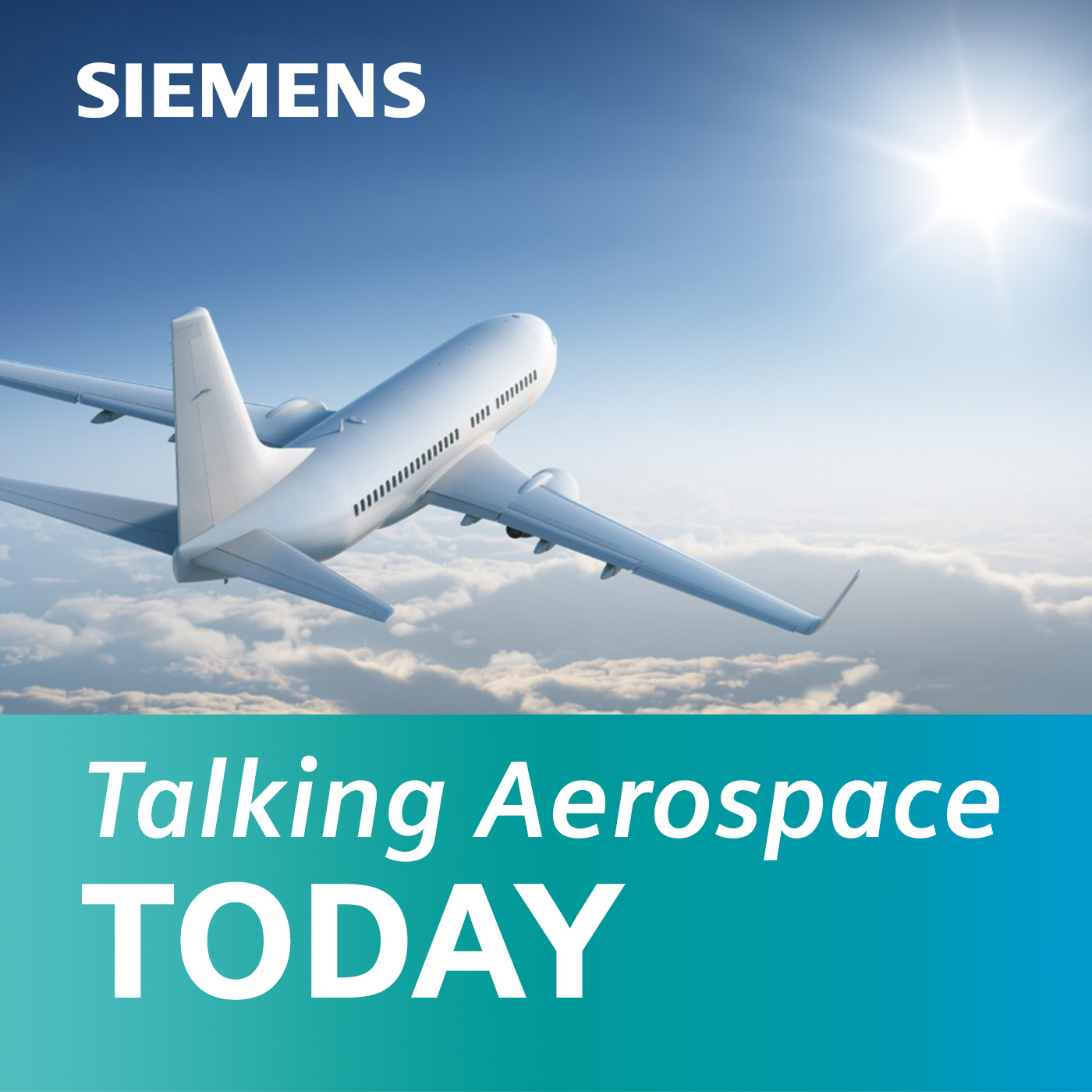
Talking Aerospace Today Podcast
The A&D Industry is at a serious inflection point. Transformation to the digital enterprise has opened up a new era in innovation and technological breakthroughs. However, complexity and compliance continue to hamper the best of efforts.
Join us as we explore how Siemens is turning complexity into a competitive advantage for many of our customers – today and well into tomorrow.