Reimagine innovations in quality management for smart operations

In an age when quality-first culture can drive huge profits and increase market share, using data to achieve continuous quality improvements has become fundamental. Organizations are striving to embed a culture of quality, into their DNA by continuously improving processes and analyzing data to drive their own success.
Yet while manufacturers are surrounded by data, many are starved for insights. This technological challenge with next generation quality management processes is critical for manufacturers to overcome. As organizations look towards embracing smart manufacturing, they must have the right tools for correcting, distributing and analyzing shop floor data in order to benefit from these technological innovations.
Next Generation QMS
The Digital Transformation for Quality Management is a 5-episode podcast series, part of Where Today Meets Tomorrow, which focuses on the value of quality management in the digital era and the future of next generation QMS.
Benefits of leveraging innovative solutions for Quality Management System
In this last episode Bettina Pruemper is joined by Subba Rao, former Director for Innovation to Market at Siemens Digital Industries Software and now Director Industry Marketing, Manufacturing Industries Cloud at Mendix, a Siemens business. Subba will explain how manufacturers can reimagine innovations in quality for smart operations and introduce the process for shaping the future of quality management and its value by leveraging innovative solutions. He will also discuss how new innovations are helping organizations with quality-first culture thrive in an environment filled with complexity. Finally, Subba will explain the role that data plays in helping companies continuously improve their processes and products, and the impact of extending the traditional quality lifecycle and breaking down information silos.

In this episode, you will learn:
- How organizations with a quality culture utilize their data (03:28)
- Why culture is important in the adoption of new technologies (06:02)
- The role of data in continuous improvement across the quality process (09:28)
- The impact of technological advancements on quality life cycle (13:00)
- The benefits of extending traditional quality life cycles (20:42)
Connect with Subba Rao:
Connect with Bettina Pruemper:
[00:11] Bettina Pruemper: Welcome to Where Today Meets Tomorrow. I’m Bettina Pruemper, and I’m your host with Siemens Global Marketing. I will present a special podcast miniseries as part of Where Today Meets Tomorrow where we talk about how to realize innovation and digital transformation in the context of the digital age. You’re going to listen to five episodes dedicated to Digital transformation for Quality Management.
[00:34] Bettina Pruemper: In our previous episodes about Quality Management, we talked about the value and the business drivers for Quality in the context of digital age. So, today it’s already the fifth episode and we will focus on innovations in quality management. So, in particular we will talk about reimagined innovations in quality for smart operations. And for that, we will discuss how to further enhance that vision. And we would like to introduce a possible future for quality, and not talking about a visionary future. Amongst other things, we are talking about shaping the future of quality management and its value by leveraging on innovative solutions. So, let’s get started.
[01:18] Bettina Pruemper: For having this deep dive, I’m pleased to introduce today’s special guest, Subba Rao. He is the Director of Innovation to Market at Siemens Digital Industries Software. Welcome, Subba. Thanks for taking the time to join us today.
[01:31] Subba Rao: Thanks for inviting me and having me in this podcast series.
[01:34] Bettina Pruemper: Before we dive in, could you please share a little bit about your background and role at Siemens?
[01:38] Subba Rao: I have over 24 years of industry experience in Digital Manufacturing and Manufacturing Operations domain. Predominantly, in the discrete manufacturing space, supporting aerospace and automotive customers or manufacturers of these industries. Even though they’re pretty diverse, they’re kind of related as many of our listeners can attest to it. I’ve been with Siemens for the last 14 years, currently, with the Manufacturing Operations Management Portfolio domain. Me and my team, we advocate our portfolio innovations and strategy, the branding, to the market. And we bring the thought leadership themes and customer industry-centric value messages and customer experiences that we learn from our customers in terms of their journey of smart manufacturing and how they adopted the new technologies and also Siemens solutions to bring value into their business processes that they have been striving to be creating a competitive edge for themselves. Along with that I work with the analysts’ community so that we understand what’s happening in the industry from the analysts’ viewpoint and aligned with our strategies and give a broader perspective of our portfolio updates to the analyst community, and also, like, work on the new product launches, and bringing new products to the market in the right way. And one of them is a quality domain that we recently launched, Teamcenter Quality. And that’s been one of the core elements that our team has been coordinating. So, I’m excited to talk about the innovations in quality and bring what we learn from our customer engagements to light, and also get feedback as part of this whole podcast series.
[03:27] Bettina Pruemper: All right. So, as part of digital transformation, there’s a big push to transitioning the manufacturing landscape towards smart manufacturing or Industry 4.0. So, what is the role of quality on this road? And what is transpiring in the industry that is shaping the future of quality management? Why is it critical for digital transformation?
[03:48] Subba Rao: Yeah, Bettina, that’s a pretty long question. But let’s start in a simplistic fashion in terms of what’s happening in the industry. As we know, the organizations or manufacturers who are looking at quality-as-first, they have the quality culture, or the culture of quality embedded into their DNA. They look at continuously improving their processes, and they look at the data, and they are more like data-driven organizations that drive their success. So, what I mean by that is the data has been inherent in all the continuous improvement measures that these organizations have been striving and working towards. Because the culture of quality is embedded within their DNA, everybody within the organization is driving towards those continuous improvements. Traditionally, this has been done on a paper-based or on different silos but still connected, because it’s embedded within the DNA of the organization. But with technological advancements, both on the IT (Information Technology) side or you can consider the engineering technology side and operational side, because we are talking about manufacturing, there is a lot of automation and products that are getting built. So, there are a lot of technological advancements that happened, that includes automated quality methodologies, and then acceleration or the need to transform towards the digital technologies by the manufacturers. It’s not only to meet the current demands, but also the recent pandemic has accelerated that needs to transform digitally and quality is becoming one of the core elements. This technological usage into the next generation quality management processes and quality management thinking is becoming key for the manufacturers towards their goal of becoming a smart manufacturing or Industry 4.0 trends that they want to get to, and also realize the benefits from these technological innovations.
[06:01] Bettina Pruemper: This sounds very exciting. So, you’re saying that the increased complexity in the manufacturing landscape is also shaping the next generation of the culture of quality, right?
[06:13] Subba Rao: That is true. Culture is one of the core elements. If one group within the organization is more tuned to certain technological advancements adoption, but the other group is not, then there is always kind of a gap. And this is where it’s kind of the holistic view into how you adopt the technologies and how it is embedded into the culture of the people and processes adopting those will become the key for the success of the organization. And that’s what we see in our customers as well as they went into this journey. Because it’s not a single switch like you use new technologies and then everything changes, it’s a journey that you’ll be adopting because there are several technologies that give value into this quality life cycle that stretches from all the way from the very early stages of requirements and all the way till the services of the product that end-users are using.
[07:13] Bettina Pruemper: All right. So, let’s extend on that. What technologies are heavily influencing the future of quality management? And why do you think they are critical for manufacturers’ quality-first mindset?
[07:26] Subba Rao: So, here, there are a couple of things, Bettina, that I want to highlight and bring to surface some of the things that we have seen from our customers as well. It’s not that technologies are not there before, it’s more than some of the technologies have become more primetime, and the adoption has become easier, and then kind of like implementing them into the manufacturer’s landscape is also becoming smoother as well. So, just to name a few. The first one is like there are automated and non-destructive inspection methods which have been traditionally used in some industries, they have been kind of like pioneers and kind of using these non-destructive inspections, and that’s been in their industry for several years. But the wider usage of these across industries is becoming much easier now, and that’s attributed to the technological advancements. So, let’s take a couple of examples like robotics, or drones, or other advancements in the laser technologies, ultrasonic, and machine vision systems, or acoustic methodologies – all these technologies that have been used in the instrumentation that’s used to measure the quality aspects has paved the way for the future of the quality, so that the historical, the manual processes are replaced with these new technological advancements. Depending on the process, not every one of these is like. In some of the products, maybe ultrasonic way of inspection is leading to good results, and that is the key technology that you want to adopt. In some other cases, maybe the very machine vision is one of the key elements or technological lever that fits into the manufacturing process. But the key point here is that our technology is predominantly helping in the quality control aspect within the shop floor, that’s taking the manual aspects out and more into automated.
[09:28] Bettina: Automated inspection is great, but what about data? It seems to be key for continuous improvement initiatives.
[09:37] Subba: Data is one of the key ingredients for continuous improvement across the quality process, and this has been there historically, whether the data has been collected and analyzed manually or with advancements with advanced analytics and we are hearing more about artificial intelligence, the machine learning, all these are making the traditional analysis much more sophisticated. It’s not just giving the traditional analysis more on the preventive side, because they’re after the fact reports. Now, with this advanced artificial intelligence or machine learning algorithms that you can apply to the data that you collect, you’re getting more towards the predictive and prescriptive aspects of the continuous improvement. So, just as an example, if you look at quality improvement methodologies that industry has been using all these years, like Kaizen, or Zero-Defect programs, or Lean Manufacturing initiatives, or Six Sigma, or even like Taguchi methods – all these are depending on the industry, these have been embraced and use for several years. All of them are dependent on data, the consistency of the data, the reliability of the data, and how you are using that data further is key to get into the predictivity or prescriptivity, or even some kind of measured actions. That’s one aspect on data. But another technological advancement that’s kind of helping this whole advanced analytics is the cloud technologies. Before I was talking about automated technologies for the inspection processes, then there is the advancement in the edge technologies. The edge devices that are closer to your automation and shop floor devices, where the data has been collected and use localized analytics that can help further, that’s just as an example. And the Internet of Things combined with low-code, no-code, and multi-experience technologies, or even augmented reality. All these are paving the way for sharing the data across the disciplines, that is key for the quality processes. As I said, quality is spreading from requirements, engineering, all the way to the product build and services. So, all these needs to be connected. And these technologies are helping to bridge those gaps and also look forward into adopting those innovations in the right way. And lastly, the technologies are not just for the “technologies” aspect from the automated inspection or cloud technologies or analytics, there is a digital twin technology that like we are hearing. And Siemens is one of the pioneers in talking about that and helping our customers to build the digital twins of their product and processes. And these are bridging the traditional gaps across the quality processes as well. So, the more you embed the quality processes into the digital twins, that will create more value in terms of adopting these technologies, and also going through the change management in a very seamless way. And also collaborating across the stakeholders, whether it be customer, or vendor, or supplier, or engineering, sales or manufacturing, right. All of them can be streamlined.
[12:58] Bettina Pruemper: Impressive. So, talking about these technological advancements, what makes these advancements so unique and beneficial to manufacturers so that they bring added advantage to quality life cycle?
[13:12] Subba Rao: Well, Bettina, I will not say they are unique. Rather, they have reached the level of maturity, it’s like they’re more prime time, I was telling before. Some of these technologies have reached the level of maturity that combined with the sense of necessity or the need that this current pandemic has put a lot of manufacturers to rethink their strategies. So, the adoption has gone at a faster pace. And irrespective of the manufacturing style or process, this adoption has been growing in a positive direction, let me put it that way. As I said, it’s not just one industry, all the industries are seeing this trend, several factors like technology advancements, their readiness, their maturity, and the pandemic era. It’s like all the lessons learned from the pandemic and the urgency is helping them. So, let’s take a deep dive into a few of you of the technologies that I was talking about earlier. Let’s start with the standard technologies. When I say standard technologies, we have taken a lot of technologies for granted. And especially in this last one and a half year when we’re hit with COVID, a lot of us started working from home. Even the manufacturers, their IT groups and the supporting systems, maintenance of the systems and all those personnel, they also started working remotely. And they started using technology tools like video conferencing for their day-to-day activities. So, taking that further into the quality processes. So, some of the manufacturers took that leap forward and started looking at “Okay, how can we adopt these existing technologies that we are using for our meetings today?”. And get into the supporting the remote inspections and integrate that into the workflows and processes, so that the remote collaboration can be enabled with remote inspection, for the example on the virtual audits or checks on some of the quality processes that can happen remotely through collaboration between the person on the shop floor and also the inspector doing remote remotely, validating the stuff. So, the video conferencing helped a lot but by integrating that into the workflow of the quality processes. Stretching that further into the virtual audits, like it’s not only the inspection process, the whole audit process, which is key for the quality and compliance aspect. So, those are also adopting these standard technologies that we have seen. And then the other one, the number two is automated inspections. I talked about automated technologies as one of the key elements with sensors, cameras, and advanced instrumentation. The traditional manual inspections are getting replaced with automated processes. So, as an example, in the automotive industry there’s a moving line with the visual inspection by an operator. There is definitely a probability of human errors and time that’s required to identify the defects or root cause analysis is definitely time-consuming, and the cost of it is also dependent on the processes and how many times these things reoccur. So, with automation, say, replace a manual process with the machine vision system capturing the images of that visual inspection process of the product, and analyzing automatically using your advanced machine learning and artificial intelligence algorithms. So, recognize the patterns, the defects are not only identified, but a clear indication of potential root causes can also be done because you’re learning from those patterns with these advanced algorithms. And that helps in identifying the defects, potential root causes, and also process degradation possibility. So, you’re getting more into predictivity – where things could go wrong? Also, drive towards what as a technician or operator or inspector you need to do as a resolution? So, these are all the possibilities with automated processes. Now, taking that further, all this requires data, and I was talking about data as one of the key elements. So, historically, there is a saying, “Data is the new oil.” So much data is being captured, and with automation that brings some additional data, the frequency of data that gets captured is much higher. So, timely analytics and ability to interpret them, correlate that with the rest of the processes, and resources that have been used at that particular moment when that information is captured – all those are critical elements that are much needed for the productivity or prescriptivity or any improvement within the quality lifecycle. So, these are the multi-dimensional information that gets captured. As part of the quality process, this multidimensional information is key for advanced analytics to apply the algorithms in the right way to get the right level of insights, and also drive continuous improvement. This rich data set is very, very critical. So, today the data is available probably in some cases. In some cases, it’s not even available depending upon the industry, their maturity, and their processes and standards they’re adopting. But more streamline you make it in terms of how you collect the data, and how you make the data structured, and then how you apply the pattern recognition and machine learning algorithms to the data, and how you take it to the next step or applying artificial intelligence to drive the predictivity and prescriptivity into those processes.
[19:10] Subba Rao: So, those are the key levers for continuous improvement and also helps the manufacturers in terms of containing the cost of quality and increasing the brand reputation, providing transparency across the stakeholders. So, these are a couple of them, and I already talked about the digital twins, I mentioned briefly. So, digital twin is helping manufacturers validate the impact of the changes. So, what I mean by that is there are several changes that happen. You collect this data, you apply some advanced algorithms, you get some prescriptivity, and some predictivity. But you need to validate those before applying those changes further down into your processes or especially on to the automation. So, this is where the digital twins will help further in terms of validating down all those needed changes virtually before applying them physically. So, this is becoming a recipe for competitive advantage for the manufacturer of the systems, processes, and speed to innovation perspective. So, overall adoption of innovation technologies tools, I’ll go back to my statement earlier in terms of the quality culture, as good as people that are using them. Yes, technologies are there, technologies can help in certain way, but adoption and the quality culture need to be embedded within the organizational processes and people.
[20:42] Bettina Pruemper: All right. So, you’re saying that the future of quality is heavily reliant on automation, data availability, and organization adoption of artificial intelligence and machine learning tools. So, does it mean the application of these tools is limited to quality control and quality assurance processes in the shop floor? What about the technological advancements in upfront quality requirements, engineering and planning, and also supplier collaboration?
[21:12] Subba Rao: That’s a very good question, Bettina. Yes, I’ve been talking about all this; automated inspection process, or data collection on the shop floor, or the manufacturing process when things are happening right. But these advancements are especially on the data front, are applicable on the rest of the processes of quality lifecycle as well. As our listeners would have listened to the previous episodes of this podcast series, some of my colleagues or experts talked about extending traditional quality lifecycle -the “Plan-Do-Check-Act” steps of quality lifecycle to engineering and across supply chain processes. Advantage of this extension is definitely coming from taking advantage of or leveraging all the 3D data, the model information with design intent. You’re taking the traditional “Plan-Do-Check-Act” quality life cycle, extending that into the engineering and supply chain. So, that’s one of the key elements with our Teamcenter Quality, where we are taking that backbone of Teamcenter, and also using all the change objects and design information in a streamlined way, bringing that further into all the quality processes of your design FMEA, and then get into the process FMEA and driving that information with the product manufacturing information content for creating your control plans, inspection plans, and further down into your execution of those inspection plans for collecting that data. So, traditionally, it’s been done but not leveraging always the 3D data, the design intent, and PMI, all the characteristics that are defined on the model level. So, we need to bring all those together. And this helps in terms of creating a closed-loop for continuous learning and continuous improvement across those technologies. And lastly, the usage of the more data that we are collecting, there is a big advantage of applying artificial intelligence and machine learning algorithms across these processes. So, we create the digital fabric across these processes and also create a continuous improvement loop.
[23:38] Bettina Pruemper: So, what do you think? Is it possible along the quality processes? Can you give an example maybe on the quality planning side?
[23:49] Subba: So, just to stretch that further, traditionally, the FMEA process – I talked about the FMEA process – which is done by assembling a cross-functional team of experts with diverse knowledge across product, process, or service to document the current knowledge and actions about the risks and failures for use in continuous improvement. And this is a manual knowledge-driven process. Just imagine the power of historical data that we already have, if we collect all this data across the product, or process, and applying artificial intelligence. And most of the knowledge of potential failures risk can be automatically gathered or you can apply the patterns and bring that into FMEA form sheets or even map it into the industry standards that are needed. So, the whole manual process, the knowledge, can be augmented with these advanced technologies. So, it’s like the pool of knowledge can bring into a system of tools and also for taking further into ramping up the new skills that are needed in this smart manufacturing Industry 4.0 era, where the next generation workforce has all the knowledge pool that can be applied based on these traditional ways of doing things and bringing that with the technology in the right way.
[25:15] Bettina Pruemper: Amazing! It is very exciting to hear the possibilities that are only possible, because of the combination you talked about. So, unfortunately, we are already coming close to our podcast time, let me ask one last question that our listeners, and I guess especially manufacturers, are intrigued. So, with such proliferation of digital technologies, manufacturers have challenges on where to start and how to embrace the digital transformation journey with quality processes embedded. What is Siemens’ advice and recommended approach?
[25:51] Subba Rao: Well, Bettina, there is no single perfect answer for such a journey and technological adoption. Because what we have seen with our customers and our broader expertise within different industries, it varies from customer to customer and their current IT landscape of the systems, processes, and their maturity in terms of bringing them together. So, all these are definitely key factors in defining how their journey looks like. And another factor to it is if it is a Brownfield facility with all the existing systems versus the Greenfield where they can start with a new approach and new systems, that also plays another factor. So, the starting point for the customer journey definitely depends on all these factors and maturity. But one thing is for sure, digital transformation for the manufacturer systems and processes, adopting to these new technologies is eminent. Our strong recommendation for our customers or listeners is definitely adopting your partner that has the technology, domain know-how, and strength to support your journey. At the same time, not just on the pilot level, but scale fast at the pace that your organization is envisioning. One key nugget I want to leave is all these technological advancements and the future you can see is not just one technology but it’s a combination of cloud, edge, IoT automation into the quality processes and bringing the PLM and MOM technologies for MES aspects. So, you have to look at this as a holistic way, but define the roadmap, the journey in a very realistic fashion that meets your needs and the pace at which your vision and goals are.
[27:47] Bettina Pruemper: Fantastic. Thank you, Subba, for your time and giving the future perspectives of quality management.
[27:53] Subba Rao: My pleasure, Bettina, anytime. And thank you for having me as one of your guests.
[27:58] Bettina Pruemper: To our listeners, we hope you enjoyed the talk and perspectives from Subba today. If you have not listened to our previous episodes, I encourage you to listen to them. If you’re interested by some of the concepts our experts talked about or any generic question on Siemens Quality Management Portfolio, please visit our website at siemens.com/teamcenterteamcenterquality or just send us an email to mom-marketing.plm@siemens.com. This is our last episode of the “Digital Transformation for Quality Management”; a miniseries part of Where Today Meets Tomorrow. Thanks again for joining us.
In case you missed the previous episodes, check out the following links:
- Ensuring quality excellence across the value chain
- Quality is your Competitive Advantage
- Revitalizing Quality Culture with Best-in-Class Solutions
- Constructing an Agile Quality Ecosystem with Low Code Apps
If you are interested in Quality Management topics, you might also check out:
- A virtual tour: Closed-loop quality from design to manufacturing
- “A broad approach to Quality Management. Closed-loop quality solution leverages Teamcenter backbone” – A CIMdata commentary.
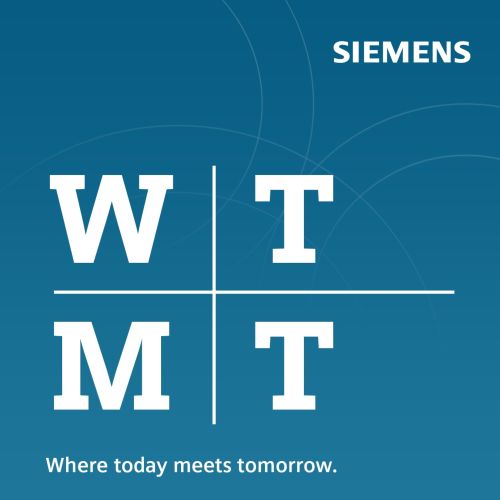
Where Today Meets Tomorrow Podcast
Amid unprecedented change and the rapid pace of innovation, digitalization is no longer tomorrow’s idea. We take what the future promises tomorrow and make it real for our customers today. Welcome to “Where today meets tomorrow.”