Improve Serviceability with integrated Service BOM Management
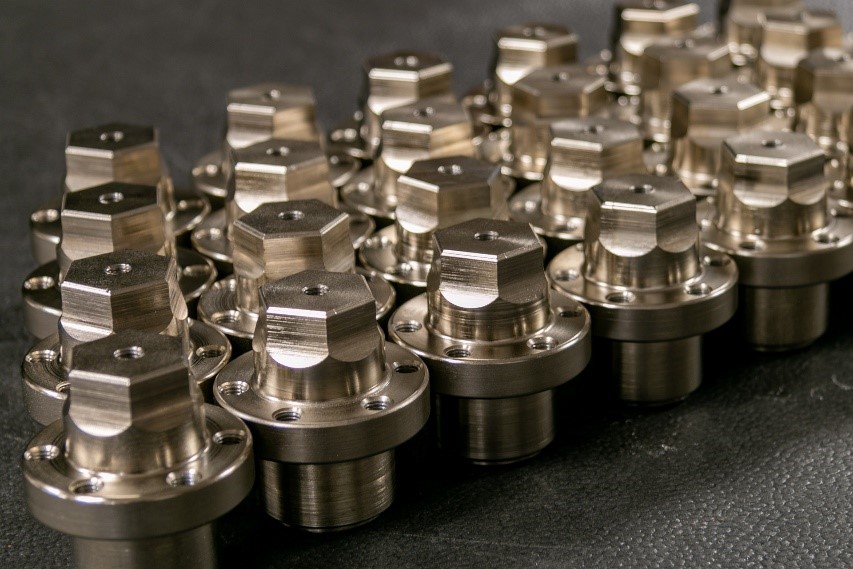
This is the second in a seven-part series where we will discuss our integrated Service Lifecycle Management (SLM) capabilities and the potential benefits that can be realized. If you missed the first part please find it here: Part 1: Digitalization Strategies for Service Lifecycle Management (SLM)
Probably the most critical factor in implementing a service strategy is ensuring that the required parts to support your assets are available in the right place at the right time and in the correct quantities. While in many industries there is a lot of focus on optimizing inventories and logistics from an operational perspective, what seems to be lost in many cases is whether the correct parts are being stocked to begin with. This typically comes from both ends of the lifecycle, in some cases there remains a large delay in implementing changes & upgrades from engineering and at the other end there is likely a gap in managing accurate configuration details for the fielded assets. Both scenarios can drive significant increases in inventory hold costs and scrap rates among other inefficiencies. These challenges are amplified from lacking a managed view of the service material requirements that can bridge the ongoing design requirements to the specific asset configuration requirements. This managed view is what we refer to as the Service Bill-of-Material (sBOM).
For many manufacturers and especially owner operators, an integrated Service BOM likely does not exist. It may be captured as a disconnected parts catalog or as a separate BOM in the ERP system. But in general, there is likely no direct linkage to ongoing change processes or the physical assets, which can result in significant discrepancies over time. Additionally, if these sub-optimal conditions exist then it is also likely that the service impacts are not clearly visible and therefore not fully considered as changes and updates are proposed. As the lifetime of complex assets generally continues to increase, this gap in visibility and traceability will only produce a greater challenge in the future.

Implementing an integrated Service BOM that is directly linked to the engineering definition provides a clear & accurate understanding of what parts are required to be tracked and maintained. Beyond just simply linking to the engineering definition, the Service BOM can be used to:
- Define additional characteristics critical to service
- Expand the definition of purchased assemblies to include required serviceable items
- Define service kits to collect and manage loose parts that will be sold as service offerings
- Create and manage service assemblies to enable more efficient asset serviceability
- Define service specific items that may be required to perform service tasks
- Manage specialized tooling required for service that may be sold as a service offering
- Manage compatible upgrades within the defined configurations
- Derive integrated parts catalogs in various formats including interactive 3D
As manufacturers and owner operators look to improve their service operations this most basic and critical aspect of the Service Lifecycle cannot be undervalued. It establishes the required foundational service data and enables the downstream efficiencies and quality improvements required to develop an optimal services strategy as well as providing a bridge for engineering to understand service impacts, opportunities, and asset performance in the field. Introducing an integrated Service BOM as part of a broader SLM strategy can provide significant value, including…
- Early collaboration of service stakeholders for early identification of material or logistics issues
- Reduced inventory costs through clear visibility to latest part requirements minimizing inventory holds and reducing scrap rates of unneeded parts.
- Improved efficiency of parts catalogs through automated creation and reuse of available data from Service BOM
- Improved traceability and clarity of service impacts across the enterprise
Look for part three in the series coming soon where we will discuss the benefits of managing integrated service plans that leverage and reuse all available data while providing improved quality and traceability.
Learn more about our Service Lifecycle Management offerings here