Asset Maintenance with Teamcenter and Maximo
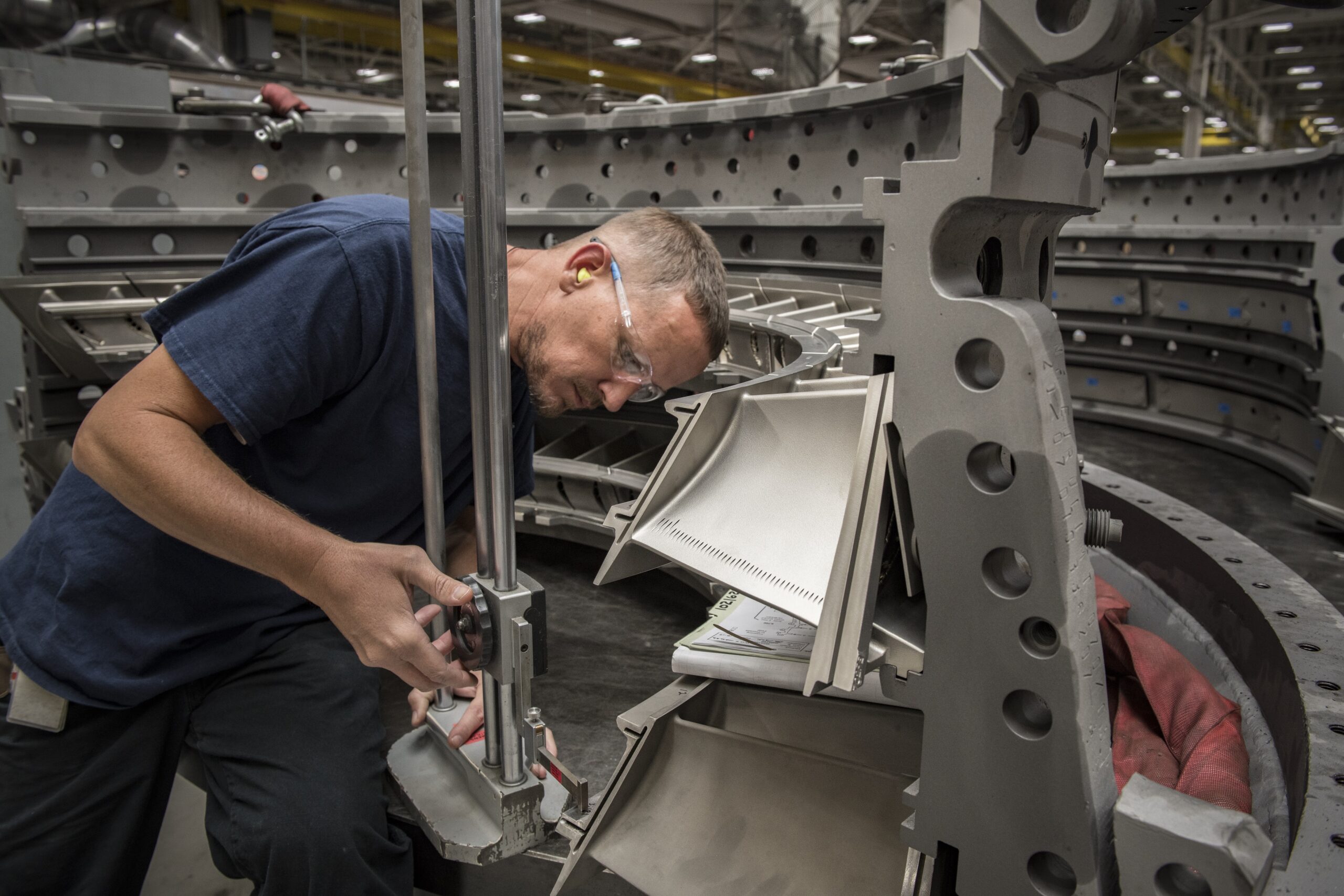
Efficiently manage asset maintenance throughout an asset’s service life, bridging together the Service BOM and Execution.

Siemens and IBM have entered into an alliance that delivers uniform and centralized BOM management across the enterprise, supporting a holistic asset maintenance process. This blog highlights solutions from Teamcenter Service Lifecycle Management and Maximo, and how they are integrated to provide a complete solution for maintaining physical assets throughout their service life.
Closed-loop Asset Maintenance
To achieve a closed-loop Asset Maintenance process, service engineering should occur in parallel with design and configuration work. This is possible using Teamcenter and Maximo integrated solutions, where the data (asset information) flows from Teamcenter to Maximo, and back from Maximo to Teamcenter.
The Service BOM (sBOM), managed in Teamcenter, will contain the design of the product with serviceability information such as, whether a design in the sBOM is a lot, or whether it’s serialized, etc. The Service Plan details the steps for servicing the components from the sBOM. The Service Plan, defined and managed in Teamcenter, has three main components which are Service Requirements, Work Cards, and Activities. Each Service Requirement represents the maintenance that needs to be performed on the asset. This Service Plan definition is used by Maximo to create Work Orders.

In Figure 1, the Service Plan of a Landing Gear is defined in Teamcenter. It has six (6) Service Requirements highlighted in green. There can be a Frequency defined on the Service Requirement, indicating how often the maintenance needs to be carried out on the asset.

As seen in Figure 2, there is a Frequency defined as “ReplaceTireFrequency” on the Service Requirement “ReplaceTire”. It indicates that the “ReplaceTire” has to be performed every six months. The Planner can also define that a Service Requirement resolves a specific Fault Code.

The Work Card details how the Service Requirement is to be completed. The Planner can specify the Skills, Tools, and Resources on the Work Card. In Figure 3, the “ReplaceExistingTire”, Work Card is defined on the Service Requirement “ReplaceTire”. If more detailing is required on a Service Requirement, additional Work Cards can be added to it.

Similarly, in the Service Requirement, “InspectOilLeakageHydUnit,” “Inspect Oil Leakage,” there is a related Work Card, as seen in Figure 4. The Service Requirement/Work Card also has information regarding the tools and resources required to perform the maintenance. The skills and qualifications required by the Technician to perform the Service Requirement are also defined in Teamcenter. In this example, the Work Card “InspectOilLeakage,” has the defined resources and necessary skill sets required to carry out the maintenance work.
Furthermore, activities are defined on the Work Card, as granular steps. There can be multiple Activities described on the Work Card. Activities sequencing is defined in Teamcenter, along with the duration required to perform each Activity. The sub-assembly can also be assigned to the Activity, along with the equipment used to perform it. All of the Activities that need to be performed in order to “Replace the Tire” are also defined in Teamcenter. The Work Time required for completing the “Replace Existing Tire” activity is the sum of the Work Time required for all activities under it.
As you can see, the Service Plan, Frequency, Service Requirement, and Work Card – all critical components to an execution process, are created and managed in Teamcenter, but the execution information is stored in Maximo. With execution data flowing between Teamcenter and Maximo, the product design can be enhanced based on operational information such as failure code, parts affected, replacement part life, etc.
Accessing Teamcenter data from Maximo
To import the sBOM structure of the asset, Maximo queries Teamcenter using a tracking number such as an Item ID, Serial Number, or Part Number of the Physical Part (Fielded Asset). Once the import is triggered, the entire configured sBOM present in Teamcenter is used to create an equivalent asset hierarchy in Maximo. This results in the mapping of Teamcenter Parts to Maximo Assets or Items.
The movie below shows Teamcenter asset information imported to Maximo.
In the movie below, you can see the asset hierarchy imported from Teamcenter to Maximo.
In the movie below, you see the asset hierarchy in Teamcenter.
In the movies above, you can see that the asset hierarchy imported in Maximo is the same as the hierarchy defined in Teamcenter. Service Plans associated with the sBOM in Teamcenter are also imported to Maximo . The Work Card is used to generate a Job Plan in Maximo, and the Activities that have child Activities are also imported. Activities having no children get imported as Job Tasks.
Once the data is imported into Maximo, all the respective objects are created – Assets, Spares, Job Plan, and Job Tasks.
Maximo to Teamcenter
Work Orders in Maximo are created using the Job Plans imported from Teamcenter. The Work Orders are then assigned to the technicians and are executed based on the requirement and schedule.
Teamcenter users have visibility into the history of all the Work Orders executed on a specific Asset from Maximo. Work Order information includes values such as Action Start and End date, Problem Code (Fault Code), Named Technician, observations recorded by Technician, etc.
The movie below shows importing Work Order history to Teamcenter from Maximo.
Updating data in Maximo
If there is a modification in Teamcenter on the sBOM or Service Plan it can be imported into Maximo by using the same process defined in Accessing Teamcenter Data from Maximo. This is achieved leveraging the digital thread which spans across these two systems – PLM (Teamcenter) and EAM (IBM Maximo).
Summary
As you can see, using the Teamcenter Maximo integration, you can efficiently manage assets and maintain them throughout an asset’s service life, bridging together the Service BOM and Execution – effectively closing the service loop. With execution data flowing in Teamcenter from Maximo the product design can be enhanced based on operational information improving quality and profitability.
This is the sixth in a seven-part series where we will discuss our integrated Service Lifecycle Management (SLM) capabilities and the potential benefits that can be realized.
If you missed the previous parts, please find them here:
Part 1: Digitalization Strategies for Service Lifecycle Management (SLM)
Part 2: Improve Serviceability with integrated Service BOM Management
Part 3: Reduce Downtime through Accurate Service Planning
Part 4: Leveraging Service Data to Drive Technical Documentation
Part 5: Improve Service Efficiency with Accurate Visibility of Your Physical Asset Configuration