Save Time and Money with Accurate Maintenance Forecasting
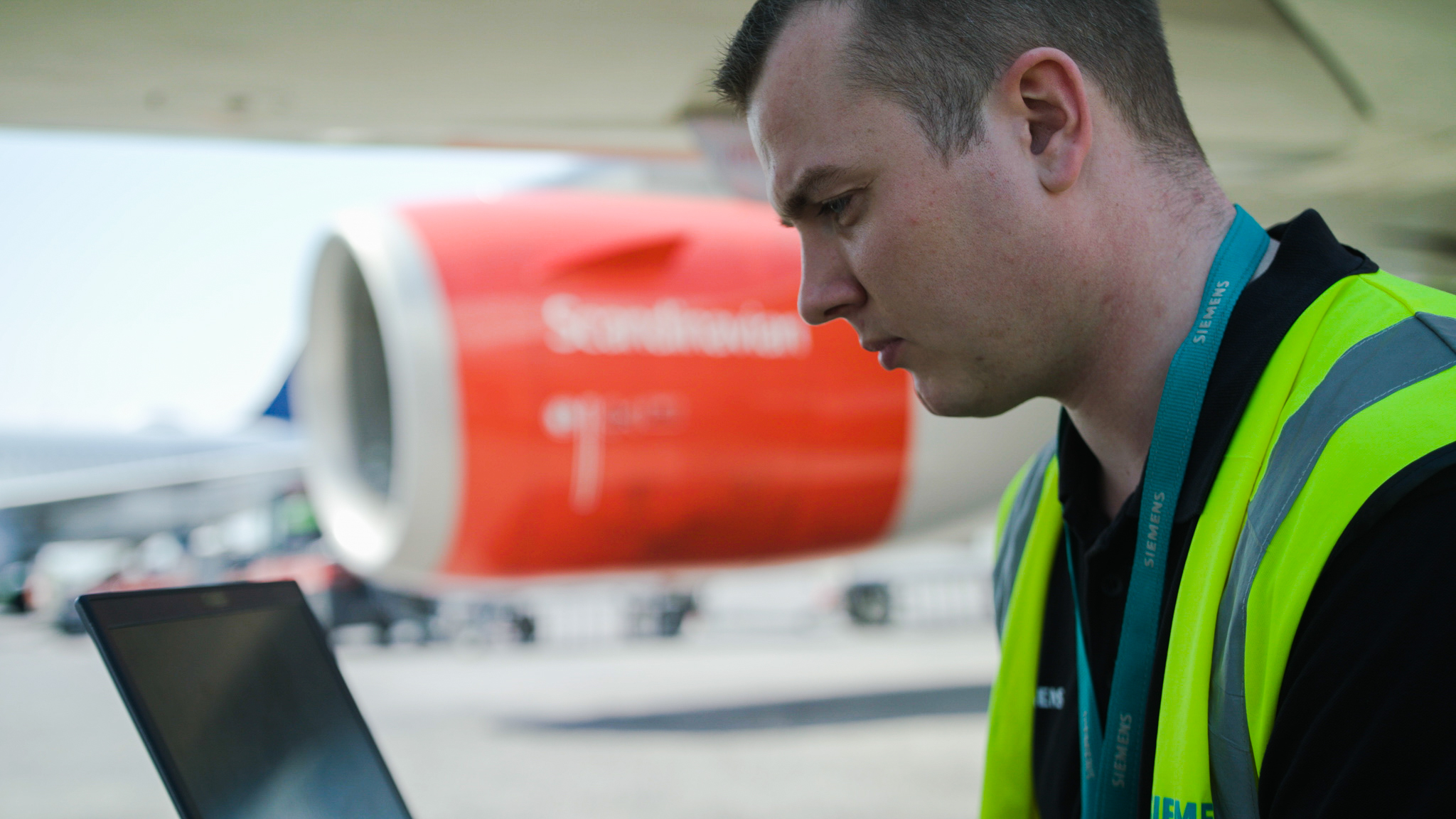
Effective and accurate maintenance forecasting leads to improved asset service, ultimately saving you time and money. Read on to learn more.

Challenges to Achieving Accurate Maintenance Forecasting
For increasingly complex products, creating accurate maintenance forecasts for fielded assets, and managing the associated spare parts inventory, presents a considerable challenge for Owners-Operators. Without having the right maintenance forecasting tools in place, you could be at risk of increased asset downtime, and increased costs.
Accurate service planning is especially challenging when pertinent service information is not readily available, and scattered between different data silos. Efficient maintenance forecasting requires visibility and access to data across the entire product and service lifecycle to avoid excessive time spent searching for information, and the risk of working on the wrong data. Leveraging product lifecycle management (PLM) capabilities such as intuitive search, BOM management, and visualization helps you eliminate data silos, and ensure efficient service planning, with a tight connection between product design, manufacturing, and service activities.
Interested in learning more about Service Planning and how it can help you reduce risks?

For a complete list of Service Lifecycle Management virtual seminars and dates, go here.
Benefits of Effective Maintenance Forecasting
With effective maintenance forecasting, you have a clear understanding of the serialized physical asset, its service requirements, and required resources to maintain it. This helps you ensure proactive service planning, and increases your potential of service profitability. For example, visibility into the current physical asset configuration of your products increases the quality of service and decreases unplanned failures, removing costs of asset downtime. Knowing exactly what parts will need to be maintained and the skill set required to maintain them will streamline your maintenance planning.
The easy to use and web-based Teamcenter Service Lifecycle Management (SLM) solution for maintenance forecasting provides capabilities to effectively plan for maintenance.
Teamcenter Service Lifecycle Management
Using the intuitive Teamcenter web browser, you benefit from complete visibility into your asset maintenance initiatives – current and future. For example, a maintenance supervisor can open a representation of a physical part in Teamcenter and view its maintenance due dates, frequency, and status. With Teamcenter, information related to the service planning, service requirements, and execution of service is available in a single environment. This helps you to be more proactive in maintenance capacity planning, and reduces your risk of errors.

Another benefit you get from Teamcenter, is flexibility in how you view your service information. Service requirements, for example, can be viewed for a selected part, or all levels of a part. In the above physical structure of the Power Generator, if the Battery Management System part is selected with a default Scope as Selected Part, then the requirements associated only with the Battery Management System will be visible. If the Scope is set to Selected Part and its Child, then requirements associated with the Battery Management System and its immediate children (i.e. Battery and its sibling) will be visible. If the Scope is set to All Level, then requirements associated with Battery Management System and its children at every level (i.e. Primary Battery and Secondary Battery) will be visible. Once selected, these views provide the associated service requirements of the part, its frequency, and the status of the service.
Service scheduling and execution assignments are supported through external systems, such as IBM Maximo, as part of the Service Lifecycle Management solution. For example, a supervisor can generate the Maintenance action. The Maintenance Action provides the right input into the Service Work Order by identifying the Asset, Service Requirement, and suggested due date.
Reduce Maintenance Related Downtime
Accurate maintenance forecasting will help increase operational availability and reduce maintenance-related downtime. To learn more about this topic, go here.
Try Teamcenter Service Lifecycle Management now for free with a 30-day trial. No setup or configuration required.
Be sure to catch the virtual Service Lifecycle Management seminar series to learn how to turn product complexity into a competitive advantage. In this multi-part series, we will focus on challenges you may be facing in the service lifecycle domain, and how Siemens software can help.