Bridging PLM-EAM Gaps
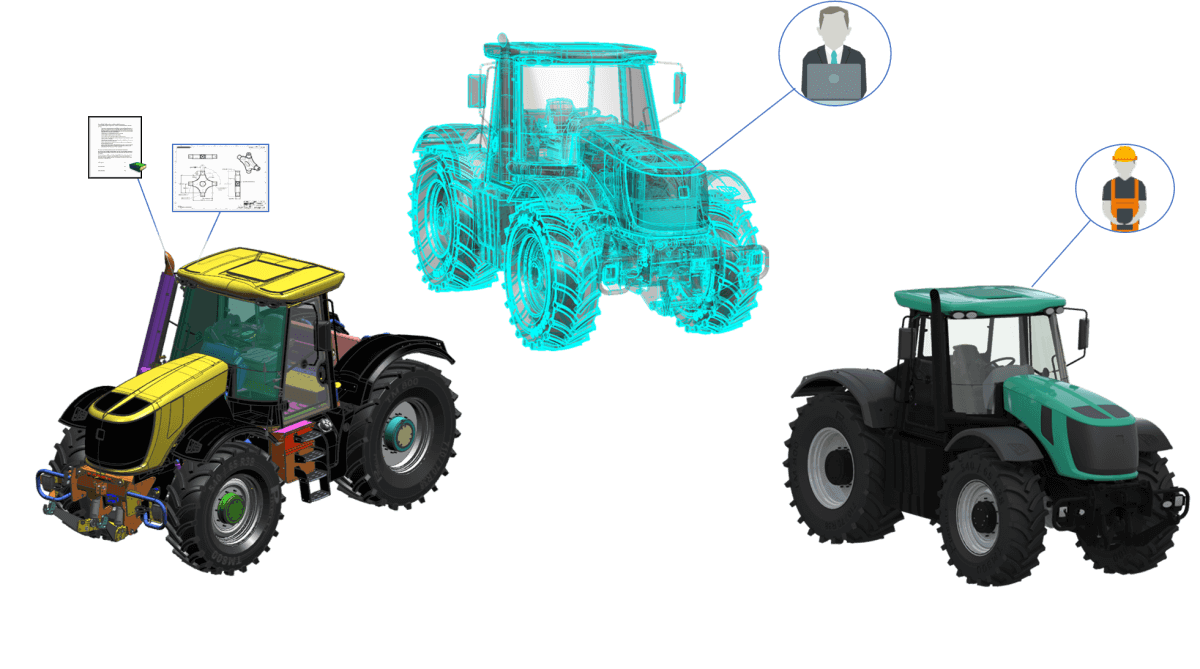
In many cases when maintenance activity is being performed, the technician makes use of the set of tools & replacement parts which are defined by the manufacturer as part of product service plan. This is normally contained in a Product Lifecycle Management (PLM) system. In reality, this information could be out of synchronization in the Enterprise Asset Management (EAM) system. For example, original part could have been replaced in the past which might require a different set of tools and spare parts. Technician comes to know about it only after a visit. Re-visit is required with the correct set of tools, spares or even skills to properly perform the job. This inadvertently increases the down time of the asset. What could be the root cause of lack of latest information? This is a result of the gap between PLM & EAM systems. This gap can be minimized with an integrated digital thread solution.

Siemens Teamcenter Service Lifecycle Management (SLM) has a Design & Service Engineering solution to support service plan definition including service requirements, frequencies, activities, technical publications, etc. On other hand, a typical EAM system would have service operations such as work order management, scheduling, costing, dispatching etc. Conveying updated information of Service Plans & sBOMs is major concern in connecting PLM to EAM systems. The EAM systems which performs service operations may have missing important updates available from PLM systems. This could bring down the effectiveness of the asset’s maintenance.
sBOM & Service Plan in Teamcenter SLM
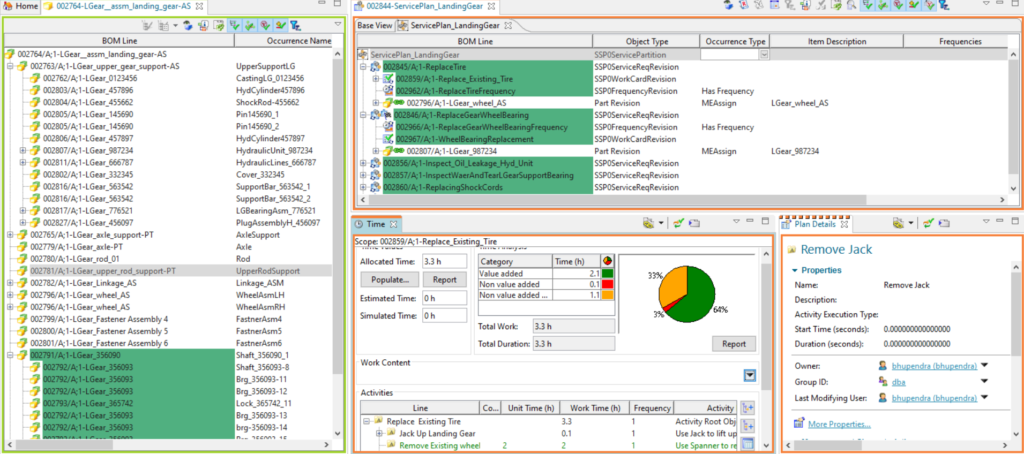
Above image shows sBOM with occurrence specific details. Service Plan will have information about how the product needs to be serviced. It contains information about frequency, work cards, time & activity details.
Imported data from Teamcenter SLM to IBM Maximo
The IBM Maximo user can pull latest & configured sBOM & Service Plan information from Teamcenter SLM. The resulting data in IBM Maximo can be seen in below images.
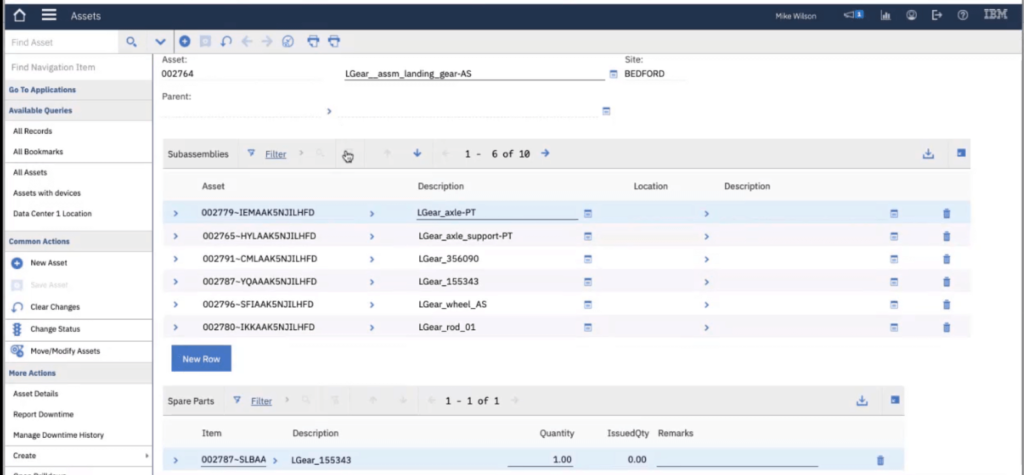
The Assets, Items, Spares are created in IBM Maximo by referring Teamcenter sBOM.
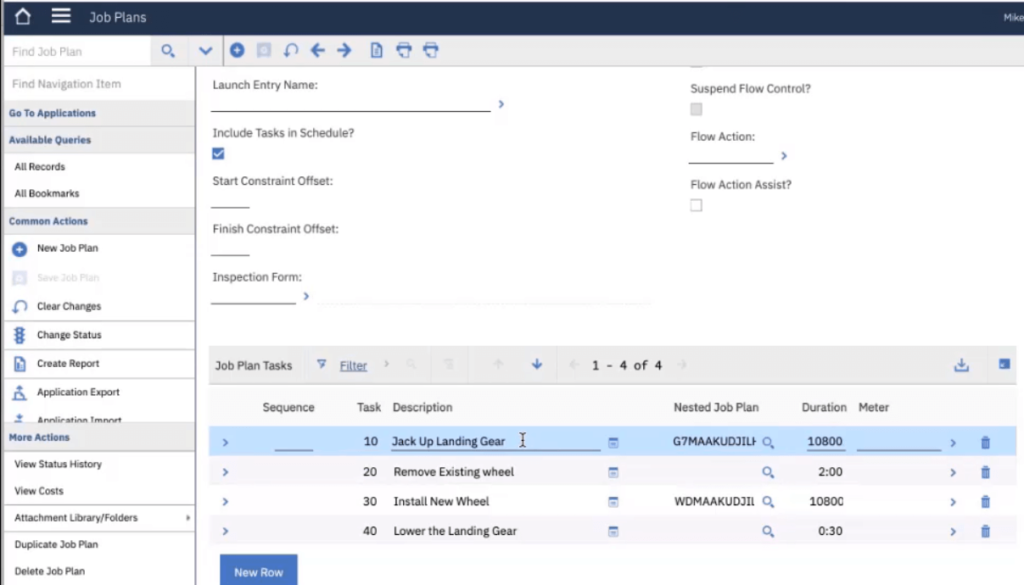
The Job Plans & Job Plan Tasks are created in IBM Maximo by referring Work Cards & Activities from Teamcenter.
Work Order History Gap:
Another gap that can be addressed through an integrated digital thread solution is lack of visibility of performance. The part movements, usage, fault codes & failures would be captured after execution of Work Orders in IBM Maximo. This information will be transferred to Teamcenter As-Maintained structures. This information from the field can be useful input for the designer to perform design improvement analysis . Such workflow of getting feedback from real assets, closes the loop between PLM & EAM systems. It is done by leveraging the Digital Thread of assets from design to service engineering, from service engineering to service operations and vice versa.
For a given asset the Work Order history is created in IBM Maximo in a standard way as shown in below image.

Import of Work Order History from Maximo to Teamcenter SLM:
For a given sBOM in Teamcenter SLM, Designer/Service Engineer can pull the Work Order history of the associated assets from IBM Maximo as shown in below images. This Work Order history provides vital information of fielded assets to the designer which helps in improving the design.

This image shows Active Workspace (AW) which is web version of Teamcenter. Teamcenter Service Engineer can pull the Work Order history from IBM Maximo by providing date range & associated Fault Code in AW.
Summary:
The above solution is an attempt to minimize the gap between PLM & EAM systems and to close the loop of Design, Manufacturing and Service Operations in order to improve quality of product based on feedback of failures, reduce commissioning time, avoid repeating technician visits and increase asset’s availability.