How does cold crucible induction melting ensure titanium purity?
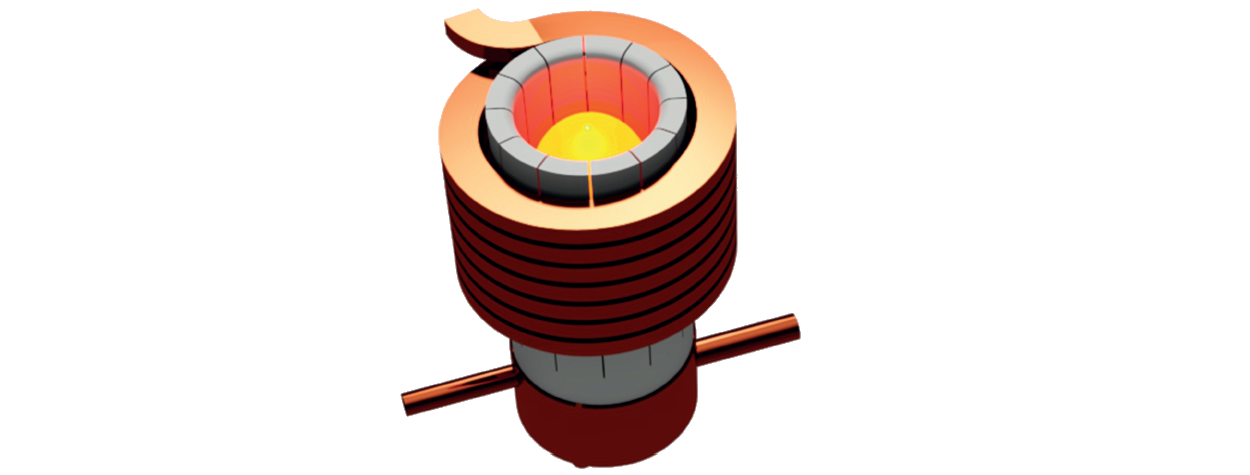
Levitation melting of metals
Metal refining employing magnetic levitation melting in cold-crucible induction furnaces is widely used in the melting of reactive and pure metals. Metals are refined by heating ores at extremely high temperatures, that is, smelting. In electric induction furnaces, electrical energy provides the heat required to smelt the metal. Compared to other forms of smelting, electric smelting is a cleaner, efficient, and well-controlled process. Electrical resistivity is at the heart of an electric furnace operation, which is either DC or AC. In submerged-electrode DC furnaces, resistive joule heating melts the ore (charge or load). In inductive AC furnaces, the changing electromagnetic field induces eddy-current joule heating on the charge.
Some applications, such as medical implants, aerospace and defense, chemical, oil and gas, high-performance automotive parts, and sports equipment like titanium golf club heads, demand a higher level of purity. To effectively eliminate contamination, the contact between the molten metal with the electrode, crucible walls, and ash, has to be eliminated. Using magnetic levitation melting in cold-crucible induction furnaces (CCIF) one can meet these strict requirements. They virtually eliminate contamination and the need for electrodes. When the molten metal contacts the cold-crucible walls, it solidifies protecting the melt from impurities, and the crucible walls from the hot melt. Siemens und Halske Company, Germany patented this innovative idea in 1931.
An integrated electromagnetic, thermal, fluid, and electrodynamic solution
In CCIFs, the electrical energy transforms the solid charge into a “floating droplet”, as illustrated in Figure 1. The induction coils transfer this energy via the electromagnetic field. Before transformation into a droplet, the molten metal forms a meniscus, which in complete magnetic levitation equates to the full load. Therefore, by controlling the molten load meniscus, the melting process is controlled; ensuring purity.

Designing such a furnace is challenging. The furnace has to simultaneously melt and magnetically levitate the molten load in a process where the load phase, shape, and properties transform from a solid to a solid-molten, and finally to a molten state. This fundamentally changes the furnace parameters, and to satisfy both conditions requires an integrated electromagnetic, thermal, fluid, and electrodynamic solution.
Is there a simpler way? We reached out to Dr. Vitaly Peysakhovic, the president of Elmag Corporation. Elmag is an electromagnetic equipment engineering design and manufacturing company. Elmag confronts such multiphysics challenges for every new specification of induction furnace from its customers.
In this technical document, Dr. Vitaly explains the step-by-step multiphysics approach of designing a cold crucible induction melting furnace for refining pure titanium and its alloys. This blog summarises the key points to consider in the design of a CCIF.
The three main design criteria of a CCIF with induction melting and levitation are:
- Maximize the induction furnace efficiency
- Control the levitation melting process, hence the melt purity
- Optimize the load utilization
1. Maximizing the electrical efficiency
Minimizing the joule losses in the coils and in the copper cold-crucible maximizes the electrical efficiency of the furnace. Sizing of the hollow coils, their placement relative to each other, and active shielding minimize the coil losses. The number of crucible sections has a strong influence on the crucible losses and its performance. Hence, Simcenter MAGNET enables the optimization of these variables, yielding a CCIF with conical induction coils and 24 sections as seen in Figure 1.
2. Ensuring the melt purity (minimizing contamination)
Controlling the melting process ensures melt purity. As mentioned before, the design of a CCIF is a multiphysics problem. Hence, Elmag Corporation proposed the iterative multi-physics approach shown in Figure 2.

The melting process is split into steps from the start to the end, in order to account for the load changes (phase, shape, and properties). The melting energy has to be controlled to control the melt purity. This is achieved by controlling the eddy-current fields, which are visualized as current-density. Figure 3 (a) shows the initial steps, where melting starts from the top to the bottom of the load. As the top load area melts, electromagnetic pressure disperses the melt; transferring the melting energy to the solid zones as seen in Figure 3 (b).
To prevent the molten load from contacting the cold-crucible walls requires the control of the molten load meniscus. An optimal molten load front ensures the coincidence of the electromagnetic and fluid pressures, energy conservation in the system, the stability of the meniscus, and efficient power source utilization. The same technical document shows how this was achieved at Elmag Corporation.

3. Load utilization
The load utilization is a key differentiator in a cold-crucible induction furnace design. This is because of the extremely high cost of super-pure metals and their alloys. It is a mass ratio of the molten load output over the furnace charge. It is an output of the magnetic levitation melting process, as seen in Figure 4. Hence, a design search for an efficient CCIF furnace in terms of the utilization ratio is arrived at.

Summary
Elmag corporation leveraged the openness of Simcenter MAGNET to generate the electromagnetic quantities needed to primarily ensure the melt purity, and maximize the load utilization. In addition, their iterative multi-physics CCIF furnace design approach improves electrical efficiency.
We have briefly shown how Elmag Corporation leveraged simulations to design a titanium cold-crucible induction furnace (CCIF), which effectively eliminates charge contamination.
For further step-by-step detail on this iterative multi-physics design approach of cold-crucible induction furnaces (CCIF), see this whitepaper.