Chengdu: VEM lab to boost vehicle performance
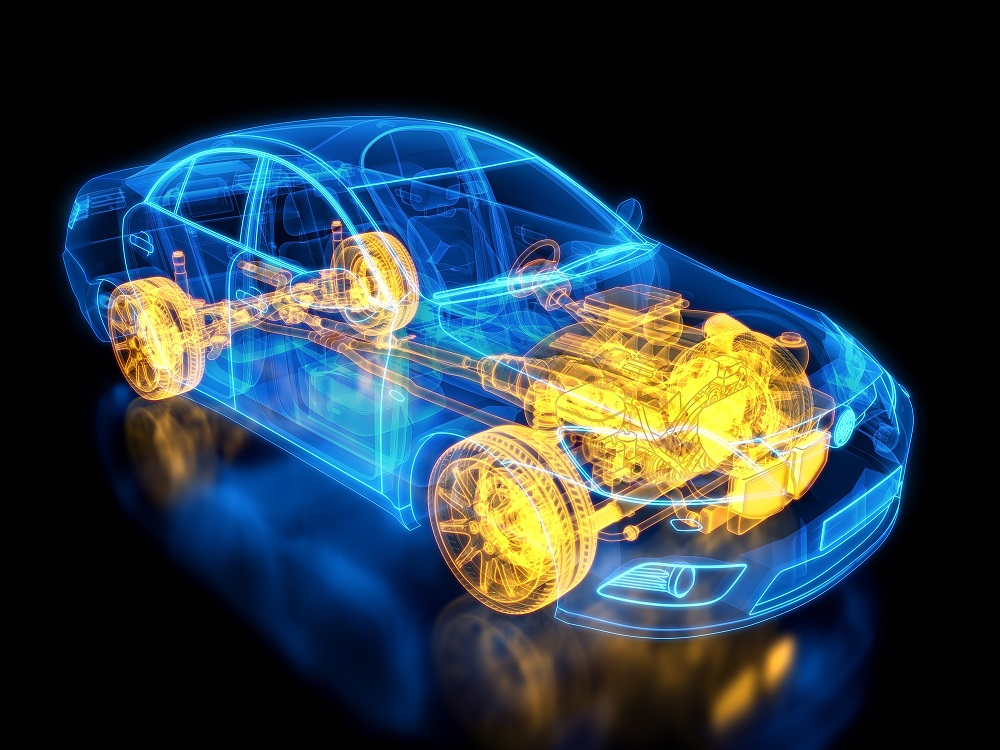
In the first blog of this series, Chengdu to build China’s Auto Silicon Valley, we discussed the new engineering center in Chengdu, China. Additional blogs have explored various services and capabilities at the center, including the ADAS, hardware-in-the-loop and battery labs as well as the multi-attribute balancing lab located at this facility. In this post, we will focus on the vehicle energy management (VEM) lab and how it can help automakers test the energy performance of their vehicles early in the development process to save time and costs down the line.
The idea for the Chengdu VEM lab comes from a similar lab we built in France. The lab has proven so beneficial that many car makers around the globe rely on it, especially companies from China. Given the popularity of vehicle electrification, VEM was selected as a key discipline for the AV/EV Engineering Center.
Climate change is creating intense interest in electrification. Meeting increasingly more stringent vehicle requirements necessitates evaluating everything down to the component level to ensure regulations regarding safety and the environment are met. It’s also important to address these concerns early in the design process, when issues are easier and less costly to resolve.
The vast majority of automakers currently set energy targets in their development cycle but typically do not take a controlled approach to the process. The VEM lab on the other hand offers a complete solution and workflow that delivers repeatability.
The Chengdu VEM lab
The state-of-the-art VEM lab offers next-generation testing-based capability to analyze the fuel efficiency and performance of vehicles. The test facility enables a car to be placed under very specific conditions that are well-conditioned to test each of its individual components, either inside the car or outside on small component benches. Developed by Simcenter Engineering Services, this process typically requires putting the car on a test bench and instrumenting it with hundreds of sensors. The sensor output can then be used to decompose the vehicle into the different subsystem targets to analyze where the biggest performance losses occur.
Another major capability of the VEM lab stems from a structured workflow that intelligently takes the testing data and turns it into a model or several models. These modeling capabilities can then be used to analyze the car with respect to a myriad of different metrics. Perhaps the design team will want to compare the current design to a competitor’s. Or the team might want to examine the current model against an older version of the same vehicle to help the team set targets for the next iteration.
In the video hereunder, Senior Vice President of Simcenter, Jan Leuridan, explains how Simcenter Engineering and Consulting services couples advanced testing solutions on a full vehicle level with in-depth physics simulation to take fuel efficiency to the next level.
Testing the performance of electric vehicles
The lab can also help improve vehicle energy performance of hybrid and electric vehicles.
Until now, testing solutions required tediously cobbling together an environment that often involves human drivers in scenarios that were difficult to reproduce. In contrast, the VEM lab enables repeatable measurements by using a spindle dyno approach. It also relies on a robot driver to ensure repeatability and puts the vehicle in a temperature-controlled climate chamber. Then the car can be instrumented with over 200 sensors—without any impact on the vehicle’s operation.

A major benefit to users of the center is gaining access to our experienced engineering staff who help with the set-up and process the data in a synchronized way. Information can then be fed automatically into models that analyze the impact of an improvement, for example, of one percent to the fuel economy or driving range. A fractional gain like this sounds modest but is significant if a car maker can realize it.
Many vehicle companies are highly compartmentalized, with the different groups working largely independently of each other. Within these organizations, there are people just purely responsible for testing, or for making a component model, or for assembling that model with another model and so on. However, the lab is unique because it’s not just a test bench. It offers a complete solution and workflow. As a result, the lab helps break down the silos that often hinder a company’s ability to develop a vehicle faster.
The Chengdu VEM lab solution brings together all those groups and promotes collaboration between all the stakeholders, which is needed to achieve success faster.
Looking forward in Chengdu
As China continues to gain momentum and prestige for its EV automotive capabilities, the Chengdu VEM lab will provide the advanced digital tools and solutions needed to improve crucial energy efficiency. This in turn, will encourage more startup companies to view Chengdu as an automotive center that addresses the needs of where today meets tomorrow, so we expect a continuing influx of engineering talent.
Established automotive OEMs will take advantage of this lab too for their testing campaigns; for example, to gain a competitive edge in upscale, global EV markets. Even suppliers could use the test bench or component bench to improve efficiency in their subsystems to entice automakers to buy their products.
Thus, Siemens Digital Industries Software helps provide the state-of-the-art testing that the Chinese EV market will need to flourish.
Conclusion
The Chengdu VEM lab is designed to help every company, from established OEMs to new start-ups, to compete globally and to pave the way towards vehicle electrification and autonomy.
With the success of the Chengdu AV/EV Engineering Center, there is likely to be similar labs in other emerging countries like India and Brazil where there is a growing community of automotive engineering and innovation.
To put it simply: the focus of the VEM engineering lab is continuing to help automakers to succeed.
A special thanks to the experts Peter Mas and Nicolas Sabatier for their insight and input for writing this post. This concludes our blog series introducing the Siemens’ new innovative engineering center based in Chengdu, China. If you haven’t had the opportunity to read about our other labs, check them out:
Comments
Comments are closed.