Virtual Material Characterization: enabling efficient materials engineering for composites
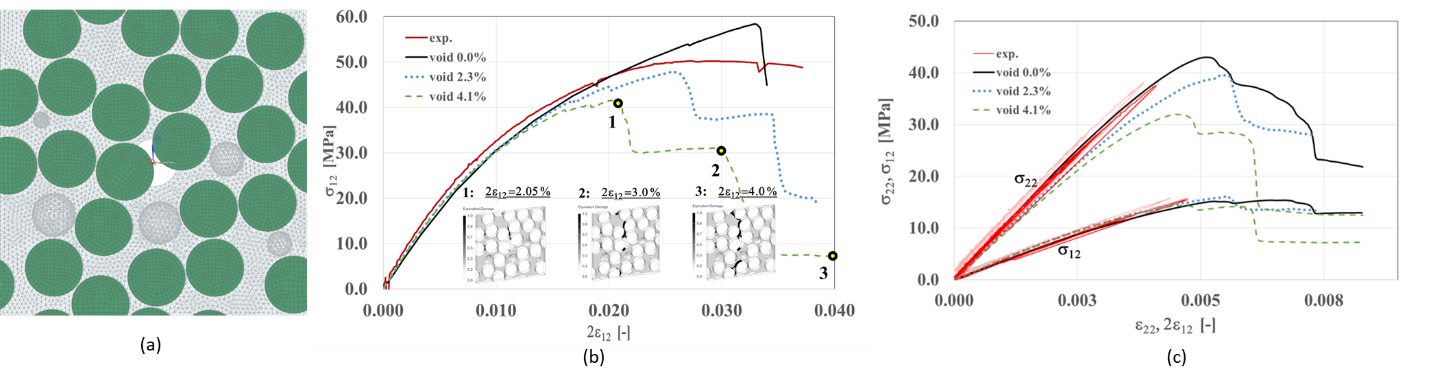
Currently, lightweight materials are increasing their penetration into several transportation industries. For example, in aircraft design, the strict norms on fuel efficiency and emission can only be achieved by increasing the use of fiber-reinforced composites and other lightweight materials into the structural design process. Due to the fact that each combination of material is different (i.e. different type of fiber, resin and mixture of the both), one requires a unique material calibration stage. This process still strongly relies on testing and validation: a large and expensive test campaign is done from material characterization by coupon tests up to system level, so that reference results only become available at a late stage in the design process, when important decisions on part geometry have already been taken, thus limiting the design freedom that is still available in a reduced timeframe.
Siemens PLM Software has designed the Virtual Material Characterization (VMC) ToolKit in Simcenter 3D to allow engineers to perform material exploration and to efficiently translate design requirements into material requirements at all design stages including early design stages. With the VMC ToolKit, the material design process can be completed with fewer tests, and then up-scaled to the component level via homogenization techniques. This enables component optimization based on virtual material models. The VMC functionality has been created on top of Simcenter 3D, a multi-attribute portfolio providing CAD, CAE and multiphysics solutions for predictive engineering analytics. The VMC ToolKit has been created in collaboration with several academic partners in the M3 Program[1] (http://www.sim-flanders.be/research-program/m3) using NX Open © to interface with key third party solutions such as “WiseTex” for fiber-reinforced composites geometry creation (courtesy of KU Leuven) and key methods such as virtual parameter identification schemes required to model composites damage (courtesy of Ghent University).
Figure 1 shows the flowchart of the VMC ToolKit workflow, based on the multi-scale modelling concept automation. Staying at the continuum scales, the VMC relies on the detailed material modelling that goes down to the micro-scale (or fiber/matrix-level = length scale in the order of micrometers) and sequentially builds up knowledge in terms of material mechanical behavior towards the meso- or yarn/bundle- (the order of millimeters) and macro/component application-scales. The workflow begins with the generation of a detailed geometry of the material, covering different scales and a wide range of supported composite types, such as UD plies, 2D/3D woven, non-crimp, weft-knitted, 2D/3D braided fabrics. In the next step, efficient quality meshing is performed. Loading and boundary conditions are automatically defined followed by a detailed Finite Element (FE) analysis. This results in the prediction of equivalent material properties that can be used on a next material scale, and process can be repeated up to the macro-scale. The design engineer can afterwards virtually optimize the component. A more detailed overview of the ToolKit can be found in [1]. Several validation cases to predict elastic properties of different woven composites are demonstrated in [2–3]. The error between the experimental values and predicted Young’s moduli lies in the range of 2-15% in the warp direction.
[1] Belgian R&D Program funded by SIM (Strategic Initiative Materials in Flanders) and VLAIO (Flemish government agency Flanders Innovation & Entrepreneurship), coordinated by Siemens PLM Software.
Figure 1: Flowchart of the Virtual Material Characterization (VMC) approach for composites structural design.
The validity of the VMC approach for dynamics applications has been demonstrated on a case of industrial complexity in reference [4], which originates from an R&D collaboration with the University of Calabria. The case of interest is a hybrid gear design, with the rim and hub in metal and the gear web in composites material, as shown in Figure 2. From the literature, the experimental modal analysis results were available, as well as a not so favorable comparison with FE using isotropic material properties, see also Figure 2. The last column shows that the simulation of the first and second modal frequencies obtained with the VMC multiscale approach are well-correlated with the experiments.
Figure 2: Validation example of VMC: accurate representation of the dynamic modes of a hybrid gear.
To estimate the “as-manufactured” properties of specimens, the VMC ToolKit is extended with a feature of void generation. Voids are modeled explicitly on the fiber scale (Figure 3a) and linked to the ply-scale by a homogenization scheme [5]. First, the Classical Laminate Theory is utilized to obtain a link between applied deformations of a laminate in longitudinal direction and local strain field in each ply. Secondly, the ply is modeled as a unit cell with randomly distributed fibers in a matrix and loaded with pre-calculated strains equivalent to the macro-strain loading. In [6] the effect of intra-ply voids on stiffness and strength of a ply is virtually assessed in multidirectional laminates [±45]2s and [±67.5]2s. Obtained homogenized stress-strain curves with and without presence of voids are depicted in Figure 3.
Figure 3: RP model with 2.2% of spheroidal voids and 1.9% of cylindrical voids (a); Homogenized stress-strain curves in shear direction in ply [-45] from the virtual test on the [±45]2s laminate (b) and in shear and transverse direction in ply [-67.5] from the virtual test on the [±67.5]2s laminate (c)
The VMC ToolKit is developed with the motivation to serve performance engineering by virtually generating material knowledge. This concept will be further extended to also support manufacturing engineering of composites that will be achieved by building on the rich multi-physics CAE platform Simcenter 3D.
Acknowledgement:
The work leading to this publication has been funded by the twin projects SBO & IBO “M3Strength”, which fit in the MacroModelMat (M3) research program, coordinated by Siemens (Siemens PLM software, Belgium) and funded by SIM (Strategic Initiative Materials in Flanders) and VLAIO (Flemish government agency Flanders Innovation & Entrepreneurship).
References:
[1] Farkas L, Vanclooster K, Erdelyi H, Sevenois R D B, Lomov S V, Naito T, Urushiyama Y and Van Paepegem W, 2016 Virtual Material Characterization process for composite materials: an industrial solution, in Proc. of the 17th European. Conf. on Composite Materials, Munich, German
[2] Shishkina O, Matveeva A, Wiedemann S., Hoehne K, Wevers M, Lomov S V and Farkas L 2018 X-Ray Computed Tomograhy-based FE-Homogenization of sheared organo sheets, in Proc. of the 18th European Conf. on Composite Materials, Athens, Greece
[3] Matveeva A, Tabatabaei A, Sevenois R D B, Farkas L, Van Paepegem W and Lomov S V, 2017 Assessement of different meso-modelling techniques for 2D woven composites, in Proc of the NAFEMS conf: Multiscale and Multiphysics Modeling & Simulation – Innovation Enabling Technologies, at Columbus, OH, USA
[4] Catera P G, Gagliardi F, Mundo D, De Napoli L, Matveeva A and Farkas L, 2017 Multi-scale modeling of triaxial braided composites for FE-based modal analysis of hybrid metal-composite gears, Comp. Struct., 182, 116–123
[5] Garoz D, Gilabert F A, Sevenois R D B, Spronk S W F and Van Paepegem W, 2017 Material parameter identification of the elementary ply damage mesomodel using virtual micro-mechanical tests of a carbon fiber epoxy system, Composite Structures, 181, 391–404
[6] Matveeva A, Garoz D, Sevenois R D B, Zhu M, Pyl L, Van Paepegem W and Farkas L, 2018 Effect of intra-ply voids on the homogenized behavior of a ply in multidirectional laminates, in Proc. of the TexComp13, Milan, Italy