Simcenter at Realize LIVE 2020 – round-up
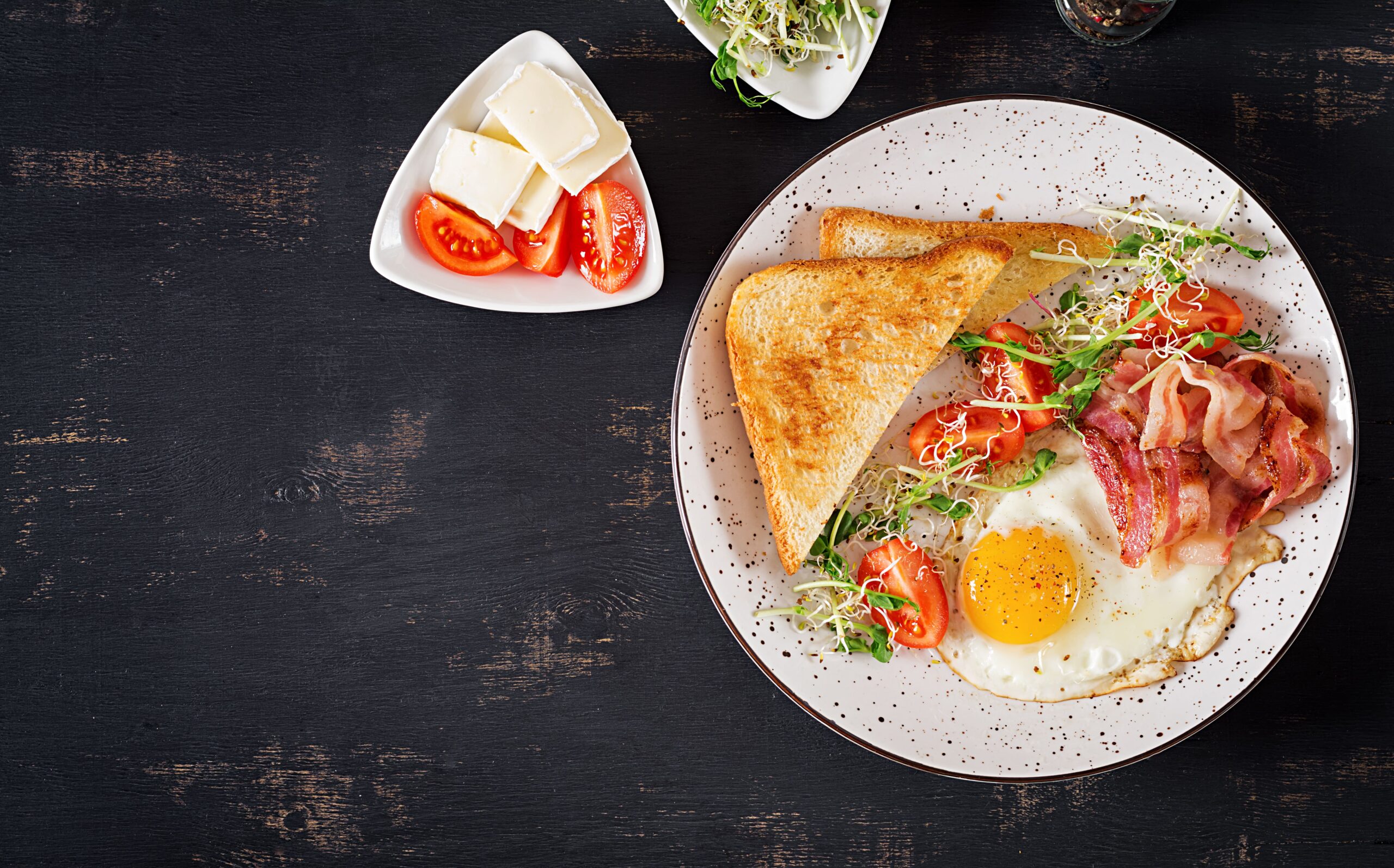
Realize LIVE Europe 2020 is done and if you missed the live broadcasts then you can catch-up now. Our moderators talk about some highlights of day two.
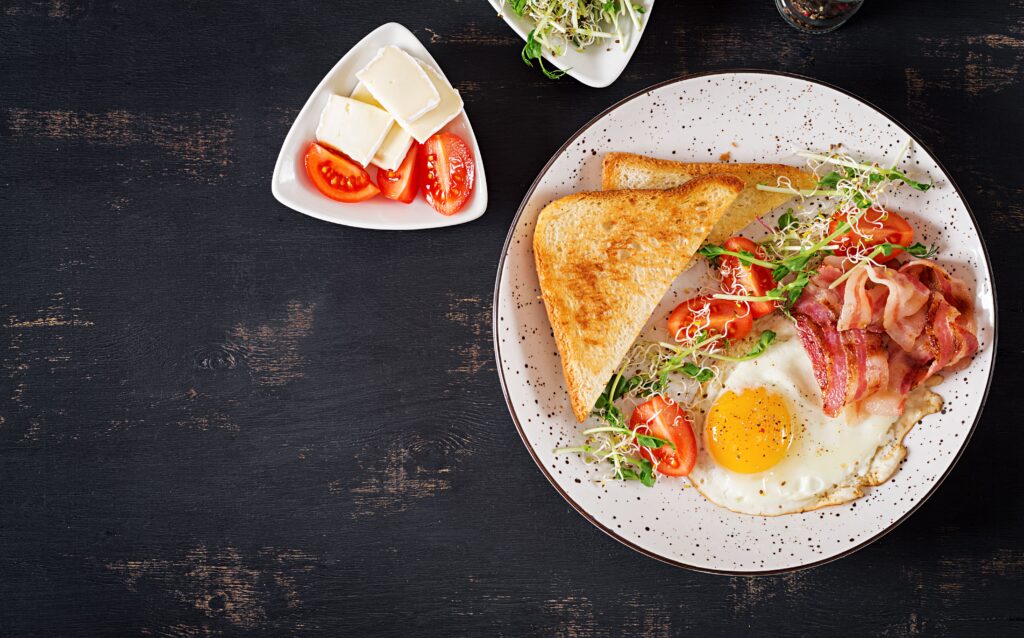
Stephen: Day two’s customer presentations got off to a cracking start while I was still eating my breakfast, which is lucky because the first presentation was about all the engineering simulation that goes into the design and manufacture of a milk or juice carton. This is truly a multi-physics endeavor and we saw examples of rheology (for the extrusion of the carton walls), discrete element modelling, multi-phase flow and fluid-structure interaction. I love to see manufacturing presentations, because I think that we often forget that we can make digital twins of processes as much as things.
Jane: I had a slightly later start than you but it didn’t take long for the digital twin to be front and center and it reminded me of your recent article ‘digital twin’ in Engineer Innovation. Ansaldo Energia and MAYA HTT have a very pragmatic approach and were able to demonstrate the effectiveness of their digital twin against virtual sensors. I say pragmatic, because they had some key learnings and takeaways but you had to be there to see those!
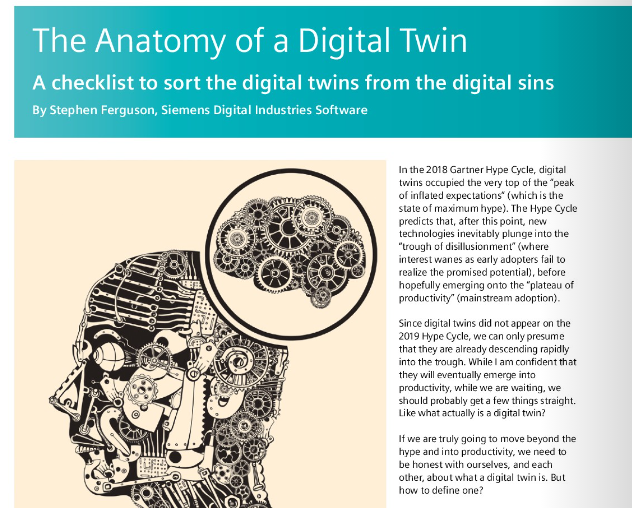
Stephen: The next presentation was about simulating the the startup process in steam turbines. This is an interesting consequence of the shift towards renewable energy sources such as solar and wind, which are intermittent in nature. Steam turbines (which produce electricity in more conventional power plants) are increasing. lt required to switch on and off, and turn up and down, in order to even out the intermittent supply from renewables. Most of the turbines currently in operation were only designed to operate at full load, so using them in partial load conditions can cause thermal stresses that can damage the turbine or reduce its expected lifetime. We saw some excellent fully detailed simulations of the ramp up process, that can be used to understand and mitigate the additional thermal stresses.
Jane: Hyundai’s Dr Jae Sung Bang working in EVs and HEVs reminded me as a marketeer just how pragmatic you need to be in engineering, failure is ok and a genuine opportunity for improvement. Dr Bang examined model-based calibration and picked up on both the limitations and advantages of this approach.
Stephen: Yes I’m all about pragmatic engineering, it’s about influencing the design process rather than chasing an “exact answer”. EVs are everywhere on this year’s agenda, I noted in the news this week that EVs are about to outsell Diesel cars for the first time in history. That’s a huge moment in our collective journey to a zero carbon future. I watched an excellent presentation about the thermal management of electric motors from InDesA, where they coupled various Simcenter tools to make a prototype digital twin of the motor.
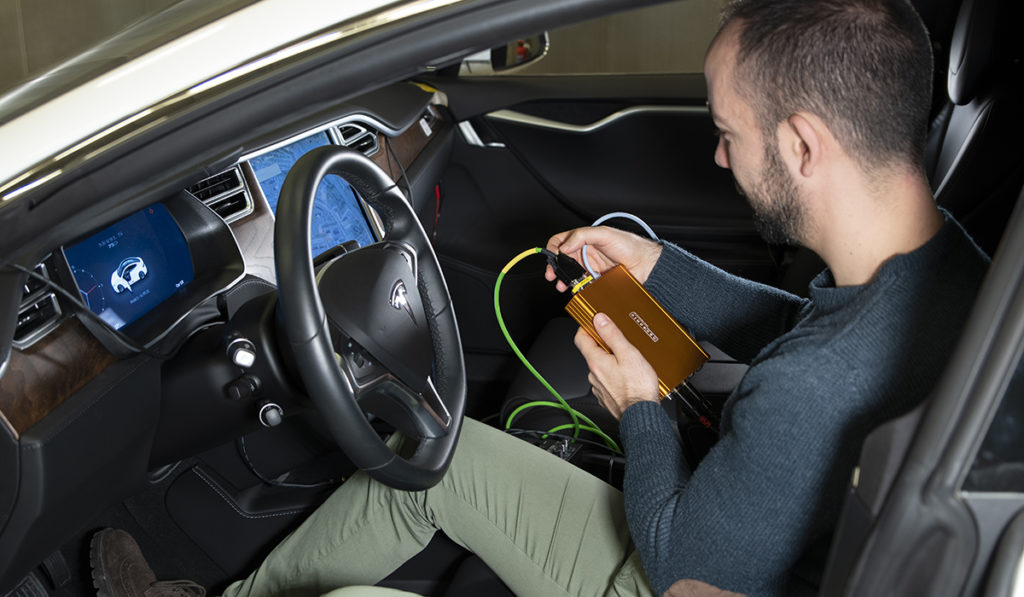
Stephen: Back to more traditional topics with an excellent presentation from Wärtsilä on “how to convey business value from complex simulations”, which make the point that people that are merely competent in their craft (in this case engineering) often over-complicate the presentation of outcomes (simulation results) in a subconscious effort to demonstrate their own competence. It’s only the true experts that can explain complex topics in a simple way (so that non-experts can understand them). Norbert went onto to demonstrate his own expertise by explaining how Wärtsilä are building fully functioning self-propelled digital twins of ships, which include one-dimensional models of engines, as well as all of the hydrodynamics.
Jane: It didn’t stay traditional in my track, Dr Schneider challenged the CFD capacity issues in many R&D facilities. He took the process apart piece-by-piece to understand where greater capacity can be found within existing structures. It was a real-life example of how bottlenecks can be overcome with technology, without sacrificing simulation reliability.
Stephen: As a simulation engineer for over 25 years, I’ve come accustomed to simply accepting material properties as a “given”, extracted from an experiment in someone else’s lab. I was completely transfixed by the presentation about crack propagation in composites, in which engineers were actually simulating the material properties and optimizing them to minimize crack propagation.
Jane: The DTU Wind Energy presentation really opened my eyes, it isn’t any surprise that offshore turbines need to be super-reliable since maintenance on them is both expensive and challenging, but their use of digital twins is helping to mitigate that. They provide every individual blade with its own digital twin! Having built in possible defects into the process, it is much easier to understand virtually the impact of any damage to a blade. This opens the opportunity to move from fixed scheduled interval with reactive maintenance to predictive maintenance, surely the quest for many heavy manufactures. I cannot possibly do justice to this presentation here so urge you to take a look.
Stephen: Yes, that is the bit that almost everyone in the simulation industry forgets, there isn’t a single digital twin but one per real life asset. It’s a bit like object oriented programming, where you define a template for an object that is used to generate many real life instances.
Jane: The future of CFD-Simulations presentation sewed together so many of the subjects that other presenters picked up on today, skill bottlenecks, new challenges in industry (think COVID-19), the move to electrification and improving data flow. Not entirely sure how they packed it all in to just 16 minutes but they definitely shone a spotlight on the potential future here.
Stephen: The great thing about Realize Live is that year on year you see the evolution of engineering as a topic, I can sense a real change in the way that simulation and test are becoming embedded in products and processes and we start to make digital twins a reality, rather than just a buzz word. Exciting times.
Jane: And that is a wrap! Just one parting thought, if you want to understand the FANTASTIC method then you will need to watch this technology update.
A huge thanks to all of the presenters and contributors who made this event such a success, until next time #staysafe.