MBST: the marriage of Test and Simulation – part 2
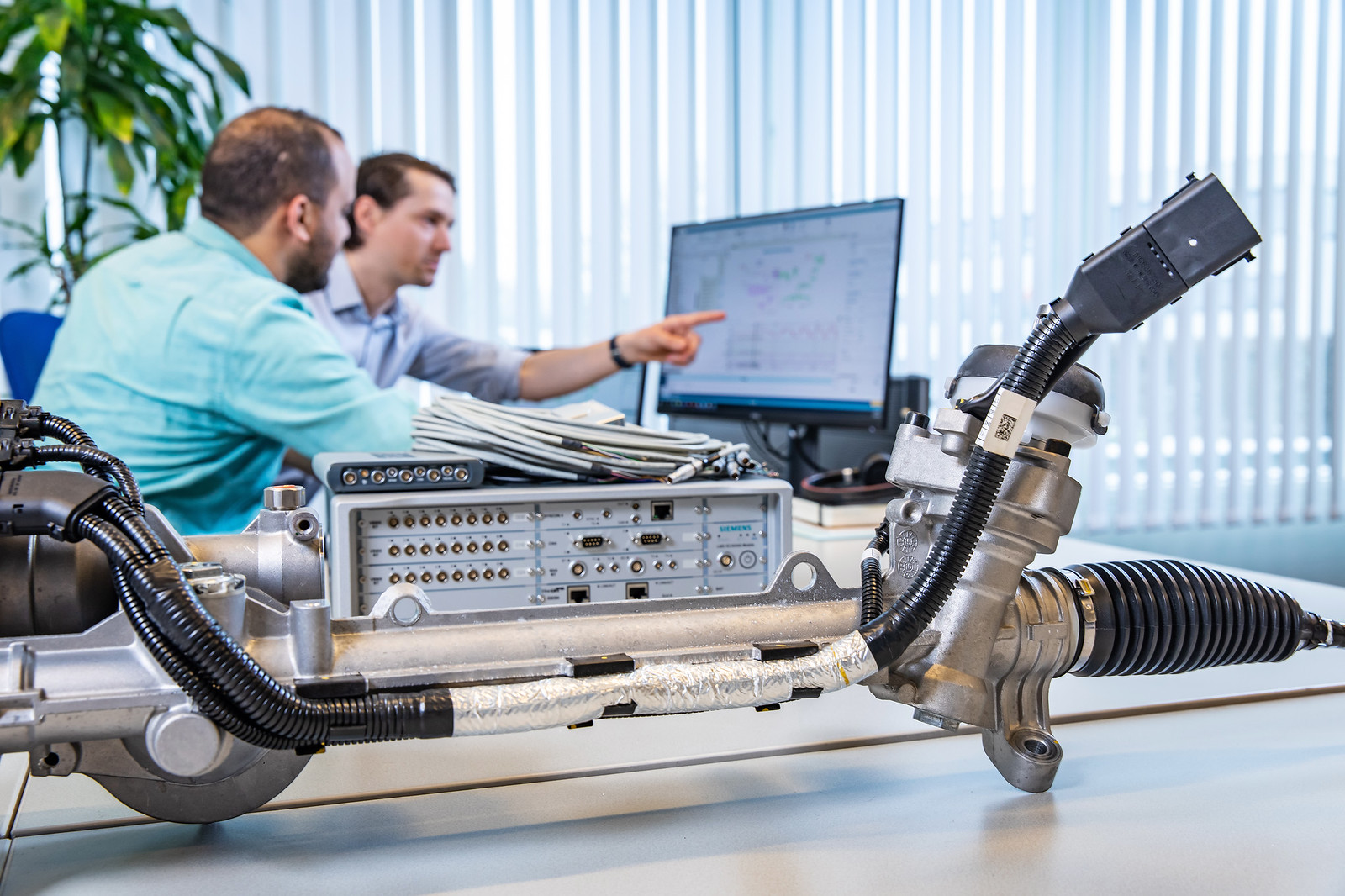
What is the first thing that you consider when buying a car?
I will be honest, and maybe I am biased because of my job, but the first thing that I check is its vehicle performance — especially the right balance between handling and comfort.
From a “development” point of view, finding the right balance between different attributes in an efficient way can sometimes cause a headache.

I spent years testing cars, linking the subjective feeling of a driver with objective data, getting insights into vehicle performance, and helping OEMs find the right balance for different attributes. For me to be able to do so, innovative technologies were developed by Simcenter Engineering.
How?
If we test the vehicle and we get the info only at the center of gravity, we might be able to see differences between vehicle variants.
However, sometimes this is not enough! Especially if the main interest is to understand why a certain configuration is better than another one and where to focus if we need to improve vehicle performance. In that case, we need to test more: more quantities and at subsystem levels (e.g. axle, wheel or suspensions).
This extra information will give us more understanding of the vehicle performance as an extension to the response at the center of gravity.
To do so, we need to use very expensive instrumentation (and sometimes even this is not enough). Another option it’s to consider advanced technologies to overcome this problem.
Let’s discuss the third pillar of Model Based System Testing (MBST): Simulation for Test.

Simulation for Test: apply simulation to define, improve and augment testing

The solution to objectively quantify design changes and full vehicle performance is using model-driven test solutions.
Simulation models are deployed to maximize testing capabilities: we are able to test more efficiently, increasing the precision and the quality of the measurements. This approach can be used at all stages of the development cycles, especially at the subsystem level.
Using vehicle dynamics models in combination with test data, we are able to collect extra data which cannot be measured directly during the testing campaign. This is what we call a virtual sensor.
There are multiple benefits: increased efficiency due to a reduction of instrumentation, lower processing time and cost, and at the same time, increased data accuracy.
Imagine how powerful it is to be able to estimate wheel or axle motion without the usage of wheel force transducers. Or being able to estimate the slip angle or wheel motion without optical sensors.
For example, in the picture below, you can see a vehicle instrumented for some handling tests, equipped with a Simcenter SCADAS for data acquisition.
As extra, there is a vehicle dynamics model made with Simcenter Amesim.
Thanks to the combination of test and simulation, wheel forces are estimated and correlated with physical sensors. No debate on the quality of the results!

The level of complexity of the models depends on the application and it can go from a multi-body simulation (e.g. using Simcenter 3D Motion) to a simplified system model (e.g. using Simcenter Amesim).
The testing acquisition is done with Simcenter Testlab and Simcenter SCADAS, which support vehicle dynamics hardware and sensors.
Thanks to the accuracy of the MBST methodology and the experience gained in the past years, the technology described can also be used in critical conditions when the excitation level is very low. In this specific case, it’s difficult to have stable test data for specific signals, such as slip angle. On-center performance (or a low lateral acceleration maneuver) is a typical critical scenario where the simulation model can support the testing, allowing meaningful information that enables the comparison of vehicle configurations.
If not enough, the state estimation of the so-called virtual sensors can be done directly in Simcenter Testlab Neo, thanks to the FMI support: multiple FMUs can be run directly in the test software.

To summarize: using models and integrating them in testing solution, we can get more data out of our test, without increasing or while even reducing instrumentation. As such, we gain insights while increasing efficiency and reducing cost.
Do you want to know more about MBST?
Check out the white paper, the article in the vehicle dynamics magazine, or read the previous blog on Test for Simulation.
And don’t miss the upcoming part 3 of the series!