Boost confidence: simulating electric heavy equipment
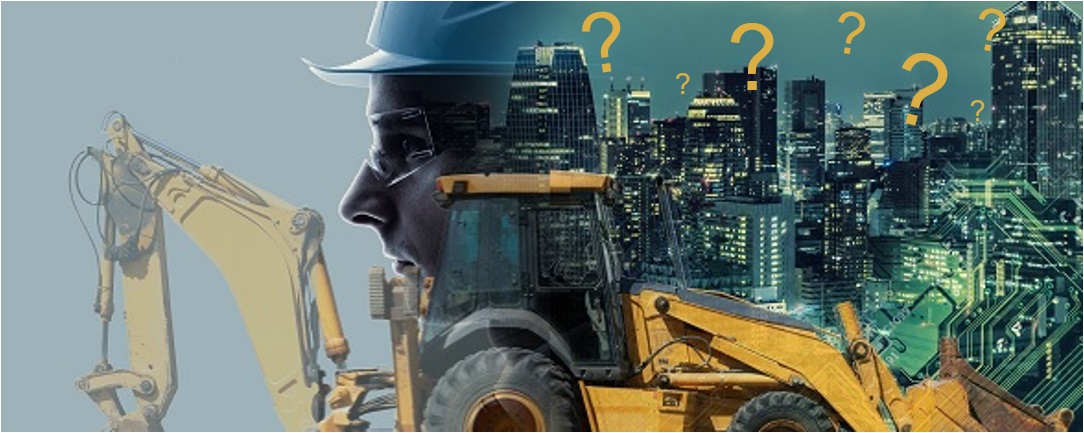
Before a buyer invests in electric heavy equipment, it’s critical the makers prove the efficiency of their machines. One option for OEMs is to use a smart combination of simulation and testing, such as Simcenter. This allows anticipating this efficiency in cost, time, and quality.
Investing with certainty in electric heavy equipment
Some industrial purchases are a high and considerable investment. As mentioned in Durability is a top priority for heavy machine makers, an excavator costs as much as a family home and even a small backhoe matches the cost of a luxury car. Who would buy a product entailing new technologies without being certain of its full efficiency and productivity? Answer: no one.
Any individual consumer and industry end user’s specifically identified concerns they want to address before any purchase.

New technologies to power small heavy equipment machines
Driven by environmental and efficiency concerns, heavy equipment OEMs are rethinking the way to power their machines. Consequently, the offer for electric heavy equipment increases. Indeed, electrified construction machines – and mainly compact equipment – are often ideal in heavily populated urban environments, made of low emission zones. This trend towards electric-powered machine is also due to the technologies becoming more mature and affordable. Of course, this has been aided by their development and use in the on-road segment. Beyond emissions regulations, noise reduction is a factor thanks to electric heavy equipment. Reduced noise is another considerable benefit for operators and for others’ comfort and safety on the job site.
There is an initial focus on smaller equipment because conventional power-engine remains the most appropriate power source for larger equipment.
Whatever the alternatives to fuel are, the new machines must allow operators to keep working in the same, if not better, conditions. As well, operators aim at reaching the same operability and productivity than when using conventional/diesel-engine machine regardless of the technology. Those alternative vary from full-electric with battery-powered, fuel-cell or still hybrid machine.
Legitimate concerns when it comes to heavy equipment electric powertrain as fuel alternatives
Regardless of the OEMs efforts to bring cleaner and quieter machines to the market, the end-user concerns remain present. They can wonder: will my TCO remain stable? If I opt for a battery, what will be the charging times? Will this technology shorten my operation capacities and, if so, make me less productive?
All are very legitimate questions that OEMs must answer with concrete fact and figures. And that is where the use of a smart combination of simulation and testing is a key ally to leading the innovation race towards electrification.
Answering technical issues caused by an electric heavy equipment thanks for simulation and testing
Simulation is the only option to design and analyze new machine architecture efficiency, way before the machine will physically dig, lift or carry. Simulation provides conclusive answers to possible technical concerns issues. While testing enables a machine in operation to capture data and feed the data back to existing models to improve the next machine generation. Getting access to a complete portfolio such as Simcenter is key to move on the following product development steps:
Comparing various architectures and the finding the best electric powertrain technology
As a first step, simulation enables to compare various architectures based on newly defined technology. It helps to determine if a full electric or a hybrid version meets the flexibility needs of the customer.
Once a common direction is defined for the architecture, system simulation can be used to perform component sizing and cascade down requirements for each components. This eases the collaboration with suppliers.
System simulation analysis is a first step in the product development cycle to have a raw view of what should be the global machine architecture. All of it without compromising various attributes performances, and identify what should be the correct technology to invest in.

Finetuning the powertrain and electric actuators design using simulation
Once the architecture is defined and main components are sized at machine level, the next step is to fine tune the powertrain and electric actuators design. This covers battery, fuel cell stack, electric machines, electrical and electronics design. Therefore, it is mandatory for an engineering group to have access to a portfolio of simulation tools that covers in details multi-physics domains and the entire so-called V-cycle.
Additionally, engineering departments are progressively acquiring knowledge on new electric technologies. Therefore, a correct simulation solution should not only rely on domain simulation solutions (like CFD, FEA, 3D or yet 1D) but also on component-oriented solutions: battery, fuel cell, electric motors, and electronics dedicated simulation and testing capabilities. This eases and accelerates engineering group expertise.

Verifying and validating electric component control logic
In parallel with the model development, engineers should verify and validate electric components control. Indeed electrification also implies an increase in software complexity, especially with hybrids. How do you manage the power split between internal combustion engine and electric motor? How to you ensure battery safe operation?
A model-based approach can accelerate and improve the development of advanced control strategies. It supports the set-up of X-in-the-loop virtual or physical test benches bringing an accurate representation of the hardware as a support of the control development.

Optimizing and balancing performance attributes at virtual integration stage of your electric heavy equipment
Last but not least: integration. Once you have validated every component and control design, it is time to integrate them within the machine assembly. This is when a model-based approach would bring back the system simulation in the loop of the development. Details analysis results and outcomes are imported within a system level view via different solutions, from simple data import to weak or strong coupling simulation capabilities.

The final objective of this virtual integration is to optimize performance attributes. It allows to find the correct balance between operability, thermal management, acoustics, NVH or even durability before building the first prototype.
Our key takeaways about using simulation and testing for heavy equipment:
- Boost engineering process from the early stages by making the correct decisions on electric heavy equipment from the start.
- Acquire expertise and deepen the electrified components analysis with integrated ‘métier’ capabilities.
- Deploy a model-based approach to support advanced controls development and validation.
- Optimize performance attributes and find the best comprise to fit both regulations and market requirements.
Related resources: you are eager to learn more about Simcenter for heavy equipment electrification?
- [Webpage] with resources about Simcenter solutions
- [On Demand Webinar] Electrifying the future of the heavy equipment industry: How Simcenter simulation and testing solutions can help define the best alternative to fuel
- [On Demand Webinar] Improve the thermal management of hybrid heavy equipment using Computational Fluid Dynamics (CFD) simulation
- [Success Story – Hyster Yale] How to convert a conventional 120-ton GW lift truck into an electric vehicle?
- [Success Story – Mecalac] French construction machinery manufacturer uses Simcenter Amesim to develop first electric wheeled excavator
- [On Demand Webinar] Go further and discover what DISW has to offer to electrical and electronic (E/E) systems design: Effective design and engineering of E/E systems for heavy equipment and off-highway vehicles