What’s new: Simcenter Testlab 2021.1
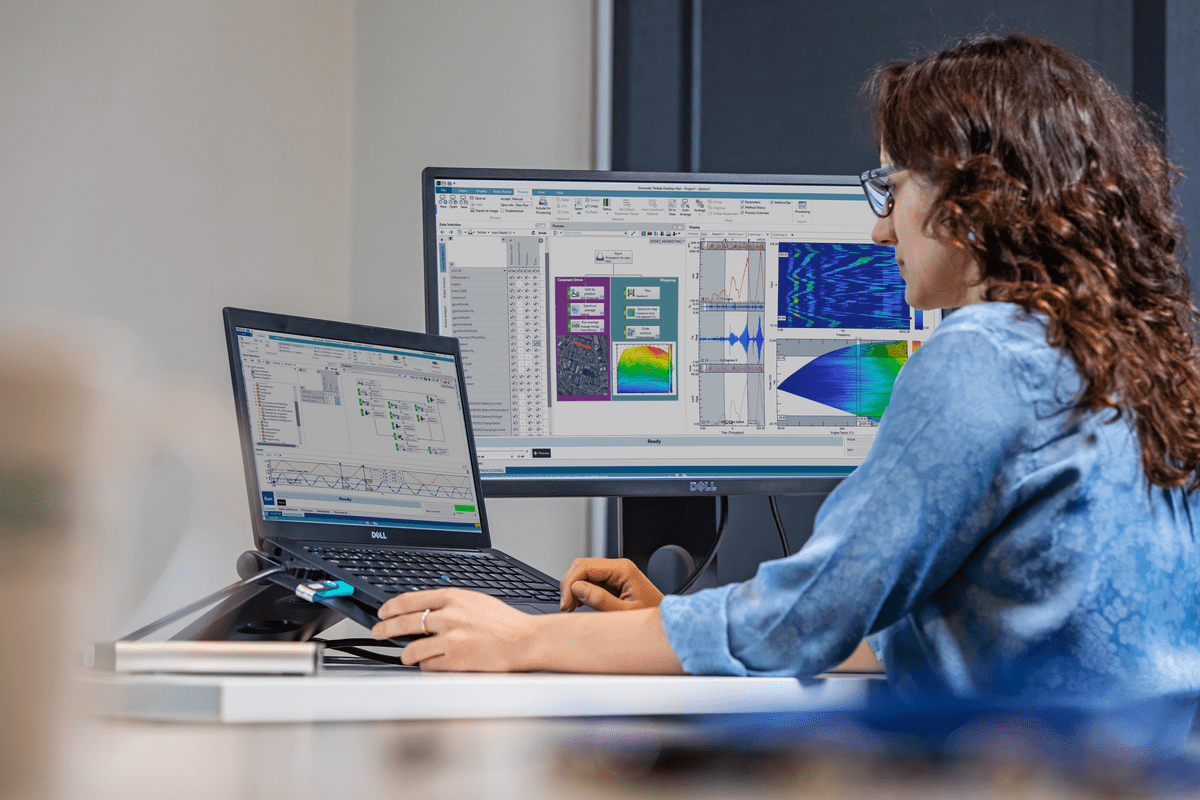
New times bring innovation, but also new demands. There is a need to achieve realistic and predictive results more efficiently than ever before.
Test teams are now working closely together with simulation teams, as the ever-declining number of prototypes available calls for the use of digital twins in the early stages of development. At the same time, there is a strong call to obtain the most information possible from massive amounts of data, collected by testing and generated by simulation.
We at Siemens have gathered years of engineering experience, selected the best methods and carefully designed testing solutions to help tackle these new engineering demands.
Discover the innovative technologies in Simcenter Testlab 2021.1, our new software release for multi-disciplinary test-based performance engineering, carefully designed to help tackle new engineering demands.
Watch the video below:
Simcenter Testlab 2021.1 offers test and simulation teams new capabilities to innovate smart products more productively under tight schedules.
Highlights in this release
Simcenter Testlab Neo
Realize new levels of testing productivity through process and technology innovation in Simcenter Testlab Neo, including completed workbooks for acoustics, durability, signature processing, reporting and data sharing.
Years of engineering experience are integrated into a new environment
that offers greater productivity, more insights, increased confidence and easier collaboration.
The task-driven user experience in Simcenter Testlab Neo is designed for the novice and the expert, with a fully customizable process designer speeds up analysis, multi-disciplinary analytics support, and the capability to embed simulation models as part of any process flow. It also offers display panels, as well as intuitive and interactive graphs accelerate results interpretation.
Model-Based System Testing
Close the loop between test and simulation using faster simulation model validation through integrated model execution and simulation data processing with Model-Based System Testing (MBST).
Model-based system testing accelerates system testing at any development stage of the model-based development process. By integrating test and simulation in a single environment for product performance validation, the risks and costs of testing can be reduced, the productivity increased, and extra system insights can be gained.
MBST maximizes the consistency of used tools and methods while providing a highly agile mechatronic system engineering environment. It also enables attribute-specific evaluation using virtual models, combined virtual-physical models, and physical prototypes.
Digital Image Correlation
Accelerate structural dynamics testing with Digital Image Correlation (DIC), a new technique for measuring full-field 3D displacements, strains and vibrations, bringing a paradigm shift in materials and structures testing
The fast development of digital camera technology in combination with high-performant DIC techniques is currently bringing a paradigm shift in this domain. Thanks to DIC, it is now possible to extract full-field 3D geometry, displacement and strain information, under any load and for almost any type of material, with limited instrumentation.
Based on only a pair of cameras digital image correlation measures full 3D displacement and strain fields at ten thousand of points. Rely on our non-contact structures and material testing solution to reduce high-spatial resolution modal testing from days to a few hours. Increase confidence in your digital twin by providing a modal model with a spatial resolution equivalent to that of an finite element model.
Frontload full NVH synthesis
Frontloads full vehicle NVH analysis with component-based transfer path analysis methodology with improved component characterization methods and predictive NVH synthesis supporting performance evaluation of virtual prototype assemblies.
Predicting the in-vehicle noise contribution of components, such as powertrain, road, HVAC and steering system during early development, is tremendously challenging. To avoid endless design iterations, engineers need modular technologies that leverage measured individual component models into full-vehicle noise predictions.
This is exactly the scope of component-based TPA. The process starts by characterizing the source loads independently, based on acquired free velocities or blocked forces. Next, using sub-structuring techniques, engineers can study the component-level NVH performance without having to physically create the full vehicle in all its variants. Such early predictions help to avoid issues and allow a more realistic design target setting.
More about Simcenter Testlab 2021.1, please!
All in all, the new Simcenter Testlab 2021.1 software release offers test and simulation teams new capabilities to innovate smart products efficiently and optimize testing productivity.
Discover these highlights and other improvements in Simcenter Testlab 2021.1.
Learn about Simcenter Testlab in this free on-demand webinar.
Read more about Simcenter Testlab 2021.1 in this fact sheet.
Visit the website for more information about Simcenter Testlab.
Comments
Comments are closed.